Blog
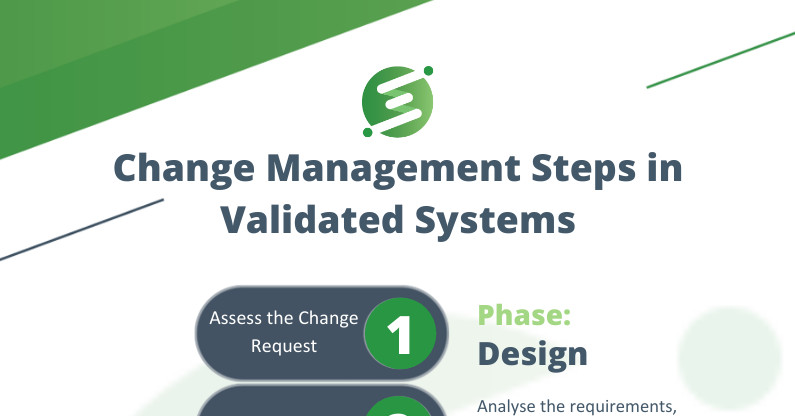
Infographic: Change Management Steps in Validated Systems
Phase: Design
Analyse the requirements, objectives, and impact of the change in addition to assessing the expected outcomes during the project’s design stage.
- Step 1: Assess the Change Request
- Step 2: Assess the Impact
- Step 3: Document the Expected Outcomes
Phase: Implementation
Implement the change in a sandbox or similar safe environment and then test before updating validation documents with new specs, processes, etc.
- Step 4: Implement in a Safe Environment
- Step 5: Test the Charges
- Step 6: Update Validation Documentation
Phase: Testing
Now move to the live environment to implement the change, test, and re-validate ensuring full record keeping of tests and test results. Finally, train users as required.
- Step 7: Implement in a Live Environment
- Step 8: Testing and Re-Validation
- Step 9: Train Users
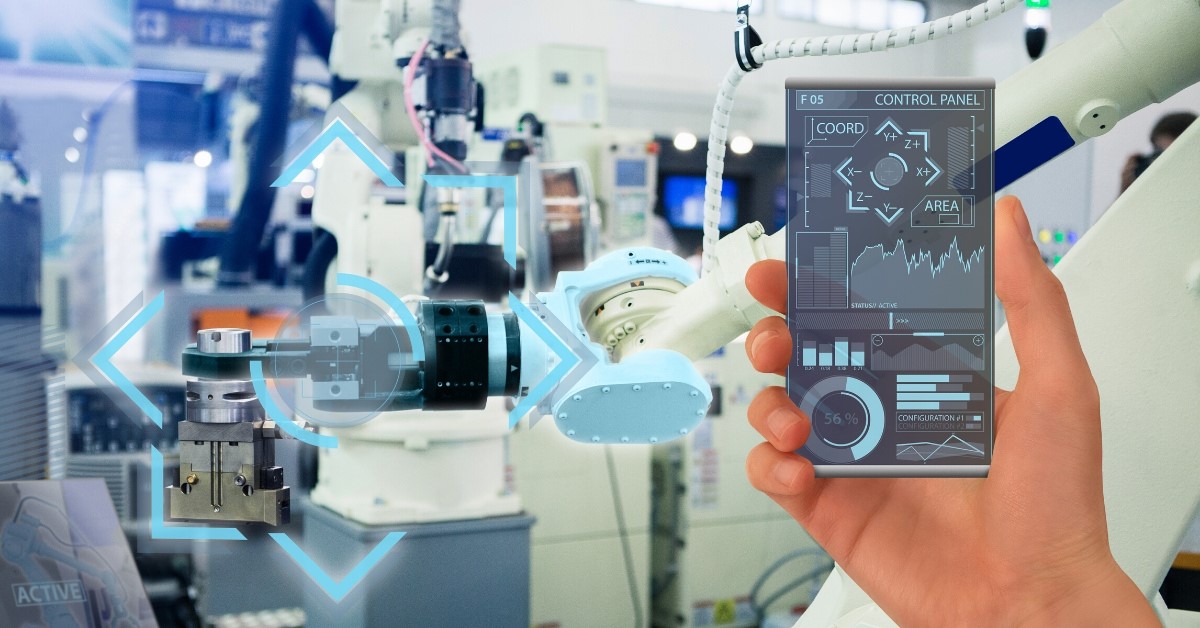
How Smart Factory Solutions Improve OEE in Modern Manufacturing Facilities
OEE – Overall Equipment Effectiveness – has long been a performance measurement used in factories to reduce costs, improve quality, increase capacity, and more. The objective is always to optimise OEE. How can Smart Factory technologies help with this optimisation?
Let’s first quickly define the Smart Factory. It’s a complex picture but, at its simplest, smart factory solutions turn production lines into data-driven production lines. This use of data improves performance, enhances decision-making processes, and makes it possible to increase levels of automation.
Production line controls are also enhanced, factories become more flexible and adaptable, and customer service levels are improved.
Why OEE is Important
OEE typically looks at three key main factors: availability, performance, and quality.
- Availability – the time a line or machine is available for production
- Performance – the speed at which the machine or line is performing compared to its optimum speed
- Quality – taking into account defective products and their impact on performance
All three together give an OEE result. Perfect conditions would give an OEE result of 100 percent. This would be a situation where the line and all machines are always available, everything runs as fast as it possibly can, and every product produced is perfect.
Of course, these perfect conditions don’t exist in the real world. After all, components fail, machines need to be serviced, machines can break down, and multiple factors can impact product quality.
The aim, therefore, is to optimise OEE and continuously make improvements.
How to Optimise OEE
Sometimes there are obvious improvements that can be made to optimise OEE. Generally, however, decisions on actions to improve OEE need to be based on data from the line itself.
In other words, collecting data from the production line and from individual machines, processing that data, analysing the data, and then making a decision on where the best OEE improvements can be made.
This is where Smart Factory technologies become so important as a central component of most Smart Factory solutions is the sensor.
In relation to OEE, sensors on machines collect data and transmit it to a central location where it is processed and analysed. That analysis can be manual but smart factory technologies also make it possible for automated data analysis and automated decision-making.
This makes OEE optimisation a real-time process as well as a process that responds to situations that have already occurred. Overall, it speeds up the time it takes to deal with problems that impact OEE.
In addition, smart factory solutions are capable of effectively processing far greater amounts of data than manual systems. This makes it possible to identify problems and patterns that only become obvious when analysed using a large dataset over time.
Practical Examples of Smart Factory Technologies Improving OEE
- Availability – sensors monitoring equipment alongside machine learning algorithms can predict equipment and component failure before it occurs. This enables the scheduling of maintenance at the most efficient time while also helping to eliminate the worst influencing factor on availability: unplanned downtime.
- Performance – the predictive maintenance example above applies to performance also as predictive maintenance ensures machines and lines not only run but are optimised for performance. Digital twin and other modelling solutions can also be beneficial. These technologies allow engineers, with the help of artificial intelligence and machine learning, to test different scenarios and how they would impact OEE without any risk to real-time production.
- Quality – in addition to identifying actual and potential faults, sensors on machines and equipment can also identify variations in production lines that impact quality. This includes things like temperature, dimensions, tolerance levels, etc. Remedial or corrective actions can then be taken.
Smart Factory Benefits
Improving OEE is only one of the benefits that Smart Factory technologies offer. That said, given the importance of OEE to overall performance and business profitability, the benefits in relation to OEE optimisation are significant.
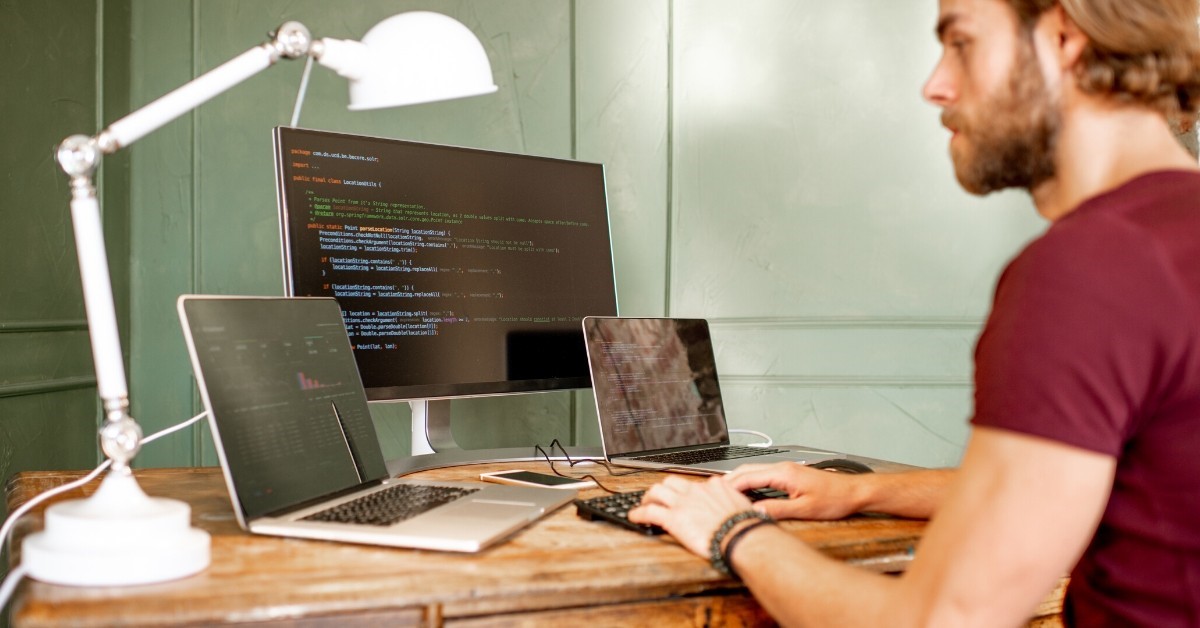
Tips for Working from Home
For many of us, the work experience has become very different over the last week or two.
While the coronavirus situation is temporary, we are all having to adapt to new ways of working as part of the national and international effort to slow the spread of the disease while keeping businesses and the economy functioning.
For companies that work in sectors like pharmaceuticals and medical devices, as we do at SL Controls, the importance of adapting to this temporary change is even more acute.
At SL Controls, we have many years’ experience in remote working. Some of our engineers work from home, others are based in our offices around the country, while others spend most of their time at client sites.
We’ve learned from these experiences and we’re now using that knowledge to adapt to this all-new situation we currently find ourselves dealing with. This is helping us continue to deliver for our clients.
If your daily work environment has changed, here are our key tips for working from home.
Eliminate the Distractions
Working from home sounds great at first if you haven’t done it much before. The initial novelty soon starts to wear off, however, and is often replaced by frustration. Much of that frustration comes from the distractions that exist in all home environments – children and other people in the house, daily household jobs, etc.
The key is to eliminate these distractions as much as possible. Where possible, work in a location separate from the areas of the house where everyone else is using. A study or home office is ideal.
You then need to follow a schedule to prevent home stuff from intruding on what you have to do for work and vice-versa.
Communicate Regularly with Your Team
If you’re a manager or business owner with staff who are now home working, one of the challenges you have to overcome is the impact of isolation.
In an office, people talk more regularly and hear what is going on. They talk about non-work-related things, of course, but they also stay up to date with everything from new clients the company has won to initiatives and new ideas.
Keeping this connection is vital but it’s more difficult when everyone is separated. So, regular communication is vital.
At SL Controls, we have an employee portal where we post updates and we have a monthly internal newsletter that gets sent to the team.
Take Breaks and Look After Your Physical and Mental Wellbeing
In an office, you take breaks regularly, you socialise, and you may even go for a walk with colleagues during your lunch break. It’s important you continue these routines as much as you can.
While socialising with others isn’t possible with the social distancing requirement that we all must live by at the moment, it is important that you look after your physical and mental health while working from home.
Also, be careful with your work-life balance. It is essential you continue to be productive and deliver on what is required, but don’t go overboard.
Furthermore, remember that it can be harder to switch off when you work from home. When you work in an office, you can use the physical act of leaving and the drive home to switch from work mode to home mode.
This is more difficult when all you have is a walk down the stairs or down the hall. Therefore, you’ll have to make a more conscious effort to switch off.
Managing the Change
There are some people who will thrive in this period of unavoidable home working and there will be others who find it challenging. Whichever category you fall into, the above tips should help.
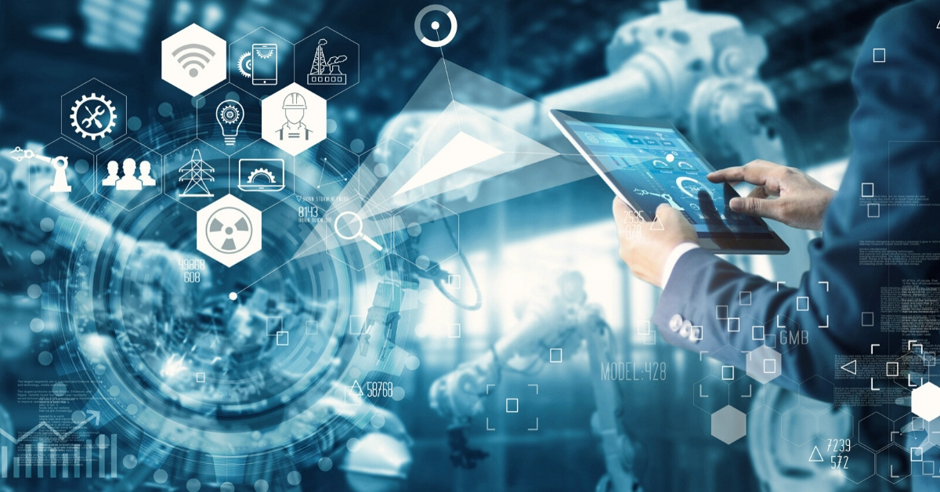
Smart Factory Benefits for Pharmaceutical and Medical Device Manufacturers
How far is your business along the path to becoming a smart factory? Are you increasing your investment in Smart Factory initiatives and projects? Given the competitiveness of the pharmaceutical and medical device industries, and the rapid pace of change, these are important questions to answer. Understanding the scale and nature of the benefits that can be derived from moving to a Smart Factory can help with answering them.
Defining the Smart Factory
Smart Factory solutions are systems comprising both physical and digital components. These systems monitor processes on the factory floor as well as in other areas of the business. They capture data, analyse data, and present data to technicians, engineers, managers, and senior decision-makers in a usable form.
At their most efficient and effective, Smart Factory systems and solutions also automate decision-making as well as automating and supporting controls.
Smart Factory Benefits
Manufacturing operations in all industries can benefit from Smart Factory technologies. The pharmaceutical and medical device industries, however, can realise those benefits faster than most.
Here are the main advantages of moving your manufacturing operations further along the Smart Factory journey.
Compliance
Regulatory requirements have increased in recent years and this is a trend that is likely to continue. Given the financial costs, complexity, and increasingly inherent digital nature of modern regulatory requirements, technology is crucial to maintaining compliance.
Smart Factory technologies can take this a stage further, ensuring compliance while also benefiting your operations in other ways.
Performance Visibility
Data is the lifeblood of the Smart Factory. Therefore, one of the key benefits is the on-demand, real-time visibility of performance information that is available.
Deeper Integration
Smart Factory technologies and solutions integrate products and processes from product development to suppliers to production to distribution to the customer – and everything between.
Process Controls
The technologies involved also improve process controls, enhancing productivity and quality.
Flexibility
The Smart Factory is more flexible and adaptable than a standard production facility. This increased flexibility makes it possible for manufacturers to quickly react to (or proactively take action on) a vast range of situations, including market conditions and user demand.
Scalability
The above-mentioned flexibility also improves scalability. Specifically, a Smart Factory can scale up or down faster, with fewer costs, and with minimal complexity compared to a standard production facility.
Improves OEE
Solutions like predictive maintenance reduce machine downtime which delivers improvements in OEE results. Machine learning and digital twin technologies also improve efficiency. These improvements occur at the machine, process, and plant level.
Improves Productivity
Enhanced automation, improved OEE, faster decision-making, greater performance visibility, and more, all results in improved productivity.
Improves Employee Engagement
You will also see improved employee engagement levels and improved morale in the Smart Factory. Employees will be under less pressure to get the minimum done and will be able to work on delivering real improvements, increasing overall satisfaction.
Reduces Costs
For many of the reasons mentioned already, and for other reasons, you will reduce costs as you implement Smart Factory solutions. This applies to both manufacturing and to overall business costs.
There are initial investments required to implement Smart Factory solutions, but those investments will reduce costs in a range of areas including maintenance, material loss, consumption of energy, logistics, and more.
Enhances Quality
Smart Factory technologies enhance product quality in a range of different ways, including through enhanced user feedback, digital simulations to test how various scenarios impact product quality, and improved production processes.
The Smart Factory can also identify and take action on changes in the production environment that can impact product quality.
Increases Knowledge Sharing
With cloud computing, high-speed internet, mobile devices, and other technologies, access to information is no longer restricted by geography. Therefore, the Smart Factory increases knowledge sharing within a plant and between plants whether they are in the same city, country, continent, or not.
Improves the Patient Experience
Many of the benefits above can be viewed from a business perspective – improved productivity, enhanced OEE, reduced costs, lower risks, etc.
However, many of the above Smart Factory benefits also improve the patient, user, and consumer experience. Better product quality, faster new product introductions, more reliable product supply, and increased product customisation are just some of the ways Smart Factory solutions improve the user/patient experience.
Creates New Opportunities
Finally, the Smart Factory will help your business compete in a fast-changing world. The technologies involved enhance innovation opportunities and allow you to move into product and service areas that are currently unavailable.
Moving Forward with the Smart Factory
Transforming your manufacturing operations to become a Smart Factory is an evolutionary process. The benefits outlined above demonstrate the real returns on investment you can achieve by moving forward and ramping up your progress.
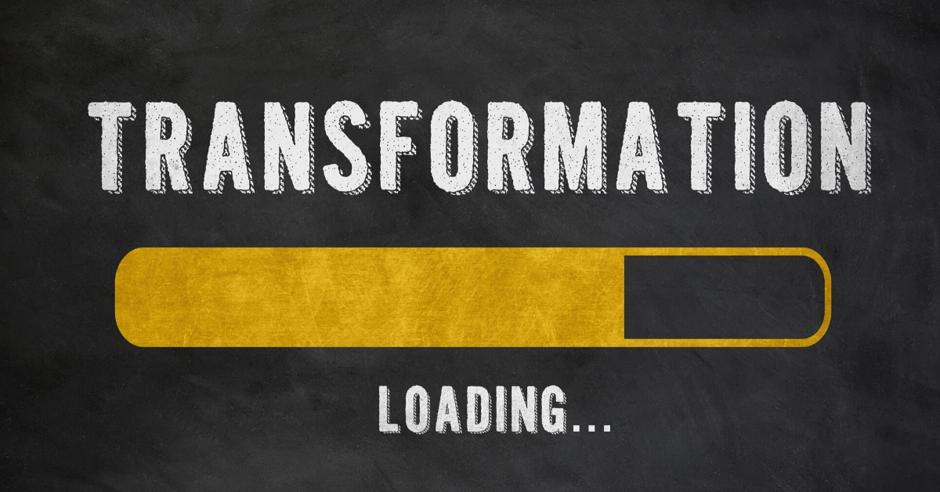
Embracing Digital Transformation in the Pharmaceutical and MedTech Industries
Digital transformation is both an opportunity and a challenge for businesses in all industries. If you are in the pharmaceutical or medical device industries, what does digital transformation mean in the current trading and regulatory environment? What are the next steps you should take?
Digital Transformation – the Goal for Pharmaceutical and MedTech Businesses
Digital transformation involves transforming your business model by taking advantage of the benefits offered by new technologies, particularly in relation to data, communications, automation, machine learning, and predictive analytics.
What does this mean in practice, though? A good description is that digital transformation is about connecting processes, data, and decision-making.
So, at the moment you may have research, engineering, manufacturing, supply chain, distribution, customer service, marketing, and finance all essentially operating separately within your business.
There will be connections, of course. There has to be for your business to function properly. However, the links between these various operations in a typical pharmaceutical or medical device business are usually minimal. In addition, they are almost exclusively manual, i.e. using paper, spreadsheets, emails, etc.
You probably even have silos within silos. So, the manufacturing part of your business may not be fully integrated with other business units, but you may also have machines on your production lines that are not connected to the others, i.e. silos within silos.
Digital transformation is about breaking down these silos to fully integrate all aspects of your business.
The Benefits of Digital Transformation for Pharmaceutical and Medical Device Companies
The fact that everyone is talking about digital transformation isn’t enough of a reason for you to invest in making changes. Instead, digital transformation needs to improve your business. Here are some of the benefits that digital transformation delivers:
- Save lives and improves quality of life for people around the world. Digital transformation achieves this through things like reducing the cost of manufacturing, improving quality, effectively managing output to meet demand, understanding patient/user/customer needs, and more.
- Builds closer relationships with patients, users, customers, and partners.
- Increases productivity in all aspects of your business, particularly in your production lines. Significant productivity increases can also come from improving the distribution chain.
- Achieves significant efficiency savings not least through automating processes that are currently manual.
- Enhances business oversight by giving decision-makers better, more accurate, and more up to date information they can use to base decisions on.
- More effectively and efficiently meets the requirements of regulators.
- Minimises human errors through increased use of automation.
- Reduces risks in your business in a range of areas. An example includes improving product quality to reduce the financial and reputational risks associated with a recall situation.
- Reduces time to market for new product introductions.
- Improves health and safety in the business, particularly in manufacturing and distribution.
- Enhances knowledge transfer within your organisation. Given the skills shortage challenge that many in the industry are facing, this is a significant benefit.
Challenges of Digital Transformation
As with any change in your business, there are challenges that must be overcome when taking steps on the digital transformation journey. Those challenges include getting agreement to move to cloud computing technologies, data integrity, cybersecurity, legacy systems and the ability to integrate them with other platforms and equipment, attitude to change within the organisation, budgets, etc
All these challenges can be overcome, however, with an approach that recognises the importance of digital transformation, sees the benefits, and embraces the fact that this is the future for the industry.
You also need the right partner to develop the solutions and implement the systems that are required.
Where Should You Go from Here?
Your next steps will depend on your business, its current operations, and the digital transformation progress you have made to date.
That said, an approach that is often effective is to start with an area of the business that could benefit most from the improvements offered by digital transformation. A manufacturing process on a production line, for example. In particular, a manufacturing process that is new or that isn’t running efficiently at the moment.
Integrating legacy equipment and systems could also be a good next step, not least because there isn’t the same requirement for capital investment that there would be if you were commissioning new machines.
In addition, integrating legacy equipment will help provide you with a good foundation for the next stage of your company’s digital transformation journey.
It’s important to stress again that you need to work with the right team – a team that has a track record of success. After all, integrating legacy equipment will enable proper communication, but this can have a knock-on effect in areas like validation and qualification. Understanding and planning for this at the outset is essential.
You will be able to improve your business to take advantage of the opportunities that digital transformation presents with the right strategy and the support of a team that understands digital transformation in the pharmaceutical and medical device sectors.
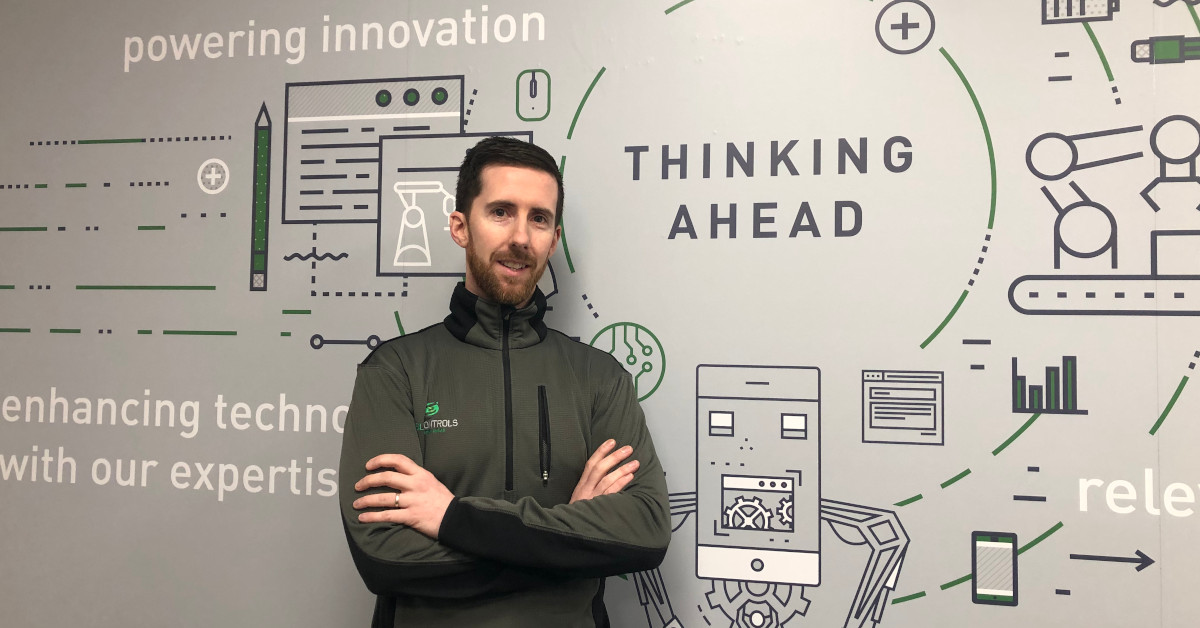
Employee Stories – Moving Back to Ireland After Living and Working as an Engineer in Australia
The start of the last decade was a time of upheaval in Ireland. The global financial crash was practically all that was in the news and, like other countries, Ireland was hit hard. One of the immediate outcomes of this was that people in many industries chose to move abroad for career reasons.
Roll forward 10 years to today and Ireland is a very different place. The economy is strong again and there are industry-wide success stories across a range of different sectors.
However, part of the hangover from the 2009/10 financial crash remains as there is a pool of Irish talent that is no longer here. They moved away roughly 10 years ago, and many continue to work in their new adoptive countries.
Many, but not all, however, as there are some who are now looking to return to Ireland. They are returning for their careers, to raise a family, and to be back home.
Alan Loughlin is a Validation Consultant. He currently works out of SL Controls’ Sligo office, delivering solutions for pharmaceutical and medical device companies in the North West of Ireland. A short time ago, however, he was doing a similar job in Australia, so his story mirrors the description above.
Becoming an Irish Expat Engineer Down Under
Alan, a NUI Maynooth computer science graduate, worked for SL Controls for almost six years in the mid-2000s. When the Irish economy was hit by the financial crash, he started to look at his options and decided to go travelling.
He travelled around various countries in Asia before ending up in Australia where he lived the standard backpacker’s life – seeing as much of the country as possible while doing various jobs (including fruit picking) to fund the next stage of his travels.
In terms of his career, he was open as to what to do next but then an opportunity came up in Sydney to work in his chosen profession again – validation engineering. He spent a short time in Sydney before moving to Melbourne to do a similar job for a consultancy company that served the Australian pharmaceuticals sector.
Alan’s employer helped him obtain a visa to stay and work in Australia, giving him the opportunity to get further experience, expand his career, and see more of the country in the process.
Ireland Calls
While in Australia, Alan met his wife, Arita, and the couple had a son. Alan said this opened up a whole new chapter in his life.
“Your perspective changes when you have a family,” said Alan. “Your needs change over time.
“I loved Australia. The country, my employer, and the career opportunities I had were all very good to me, but when you have a family you start to miss Ireland a bit more. It’s being away from your extended family and not being able to spend time with your wife and son together with the rest of your family because they are back in Ireland.
“In terms of family, we were on our own in Australia, so we didn’t have that support network that exists when you are back home. This was a big selling point for coming back to Ireland – that support network, plus the fact Ireland is a great place for bringing up children.”
The Move Back
In making his decision, Alan also looked at how Ireland had changed since he left the country eight years previously, noting how it had gone from strength to strength, particularly in relation to the pharmaceuticals sector.
Alan said: “What’s great about Ireland is it’s a real melting pot for multinationals. This provides priceless experience for engineers as there is so much of this industry here.
“When you travel abroad you realise how lucky Ireland is to have this on its doorstep. It’s a great asset to have.”
So, Alan started looking for job opportunities back in Ireland, something which many engineers who left during the late 2000s and early 2010s are also now doing.
For Alan, he chose to take up a position with SL Controls in Sligo.
“When I did start looking back towards Ireland,” Alan said, “I did get a lot of job offers from places like Dublin, Cork etc, but it was great that SL Controls has such a presence on the western seaboard. SL Controls serves so many clients in the West and North West of Ireland that there are opportunities for engineers who want to live and raise a family in this part of the world. It ticked all the boxes for me.
“The company was also a massive help with the relocation and move back to Ireland, making that part of the process go really smoothly for us.
“It’s also really great to see how far SL Controls has come in the period of time I was away. The company has expanded and moved into other areas, including overseas, and I was impressed with the vision and direction the company is heading.
“I was also impressed with SL Control’s focus on innovation as this is a factor when looking for another career step.
“All these things were attractive to me and helped with the decision Arita and I took to move back to Ireland.
“It’s different here, of course. Everyone talks about the weather, but it’s not good to compare the two. For me, I feel lucky to have lived in both countries and I’m looking forward to a future of continuing to advance my career while living and raising a family in Ireland.”
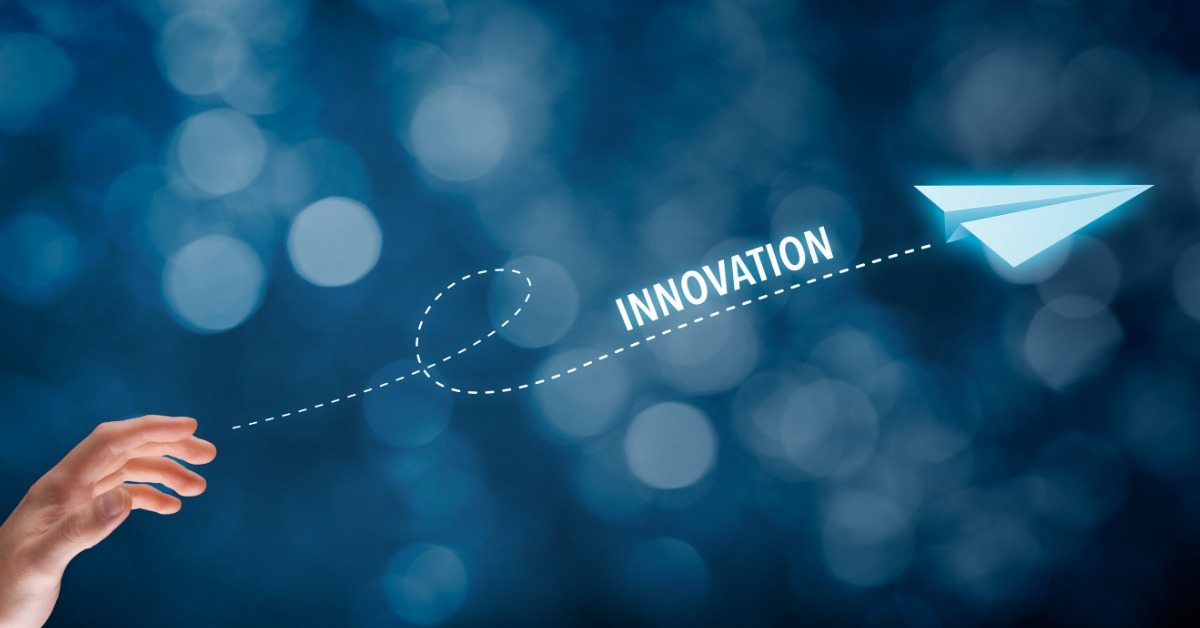
Managing Innovation – Capturing and Driving Good Ideas
The more you work in engineering, and the more engineers you work with, the more you understand there is no shortage of ideas. Coming up with new systems, processes, tools, products, ways of working, templates, and procedures is something that engineers do naturally – it’s in our DNA.
The real challenge for organisations is harnessing and then taking full advantage of those ideas. In other words, managing innovation.
Without a process to manage innovation, great ideas are too often left to wither and die. Even those that are acted on are usually only implemented in a pocket of the organisation, with the majority of business units and teams not even knowing the innovative idea exists let alone how to benefit from it.
So, how can engineering organisations manage innovation to make sure they are benefiting from the ideas being developed by members of their teams?
Taking a Structured Approach
I have personal experience of this issue delivering validation services for SL Controls. The validation engineers on our team are forward-thinking and highly innovative, so great ideas on a broad range of topics come thick and fast. However, we are spread across multiple offices in Ireland, so distance is a factor. Plus, members of the team spend considerable amounts of time at client sites.
Then there are the other departments and teams in the business. The ideas that we develop in Validation Services could be beneficial to those teams. In addition, an innovative idea developed and implemented in another department could benefit us.
It’s a complex situation but, as with most other complex situations, it can be solved with a structured approach. Here are some principles that we adopt at SL Controls to manage innovation throughout the company.
Innovative Ideas Can Come from Anywhere
Senior and experienced members of the team don’t have exclusivity on good ideas. Instead, ideas can come from anywhere, including from engineers looking at a problem with a fresh pair of eyes.
Engineering Organisations Need Systems for Capturing Innovative Ideas
Making the most of innovative ideas is not something that can be left to chance. Instead, you need structures and systems in place to capture the idea, refine it, integrate it with existing processes and ways of working, and then distribute it throughout the organisation with buy-in at all relevant levels.
This is the only way to ensure innovative ideas lead to positive change.
Accept that Ideas Have to Be Prioritised
While you need systems in place to capture innovative ideas, there also needs to be an acceptance throughout the organisation that it will not be possible – or good practice – to implement every idea.
Instead, innovative ideas need to be analysed to assess whether they fit in with the company’s culture and goals. They then need to be prioritised as every organisation has a limit to the number of resources that are available for this process.
Focus on a Company-Wide Approach
The easiest way to manage innovation to capture and drive good ideas is team-by-team or department-by-department. This is not the most effective approach, however.
You will maximise the positive change possibilities of managing innovation if you take a company-wide approach.
After all, a solution in one team may be useful to others. You may also find that a solution to a particular problem someone is trying to solve may already exist.
Managing Innovation
Managing innovation to capture and drive good ideas is about making use of the talent you have available. It makes engineering companies more efficient, it improves customer service, and it enhances quality. It also enhances levels of job satisfaction for engineers to see something they have come up with being implemented and then becoming successful.
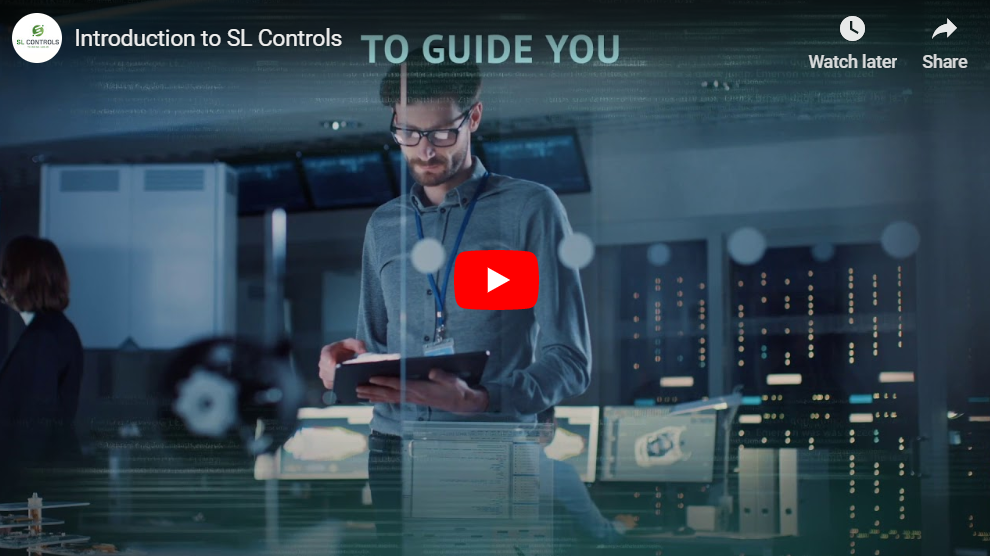
Video: Introduction to SL Controls
Learn more about SL Controls in our new corporate video:
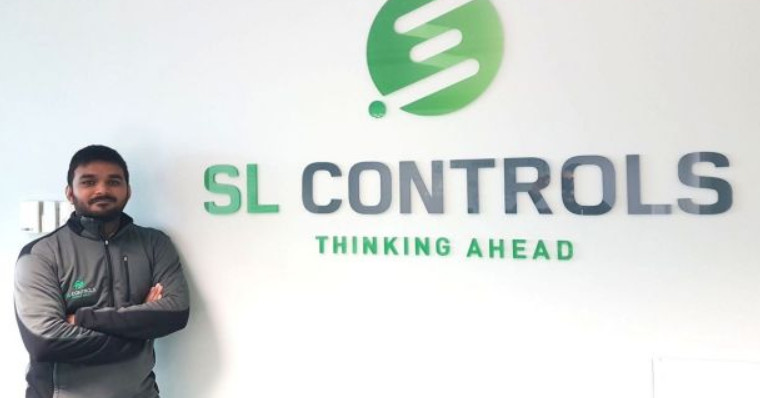
Employee Stories – From India, Via Hong Kong, to SL Controls in Dublin – A Validation Engineer’s Journey
Today, Amit Patel, Senior Validation Engineer at SL Controls, works with some of the world’s largest pharmaceutical and medical device companies from our office in Maynooth, Dublin.
His journey to a career at SL Controls is slightly more unusual, however, than those employees who were born, studied, and/or previously worked here in Ireland. This gives Amit a unique perspective and interesting insights for any non-Irish engineers who are considering moving here to progress their careers.
Early Career
Amit is from Gujarat in India. He qualified with an MSE in Biotechnology at Kadi Sarva Vishwavidyalaya (KSV University) before starting his career locally in Gujarat.
However, he began travelling for work early in his career, getting a job with an Indian company as a Computer System Validation Engineer working on projects across India as well as in Germany, South Africa, and Bangladesh.
Computer System Validation in Hong Kong
In 2013, Amit decided to move to Hong Kong to take up a position with Bright Future before moving to a different company, Fortune Pharma. In both of those companies, he worked as a Computer System Validation Engineer.
After five-and-half-years in Hong Kong, Amit returned to India where he took on a six-month computer system validation contract as a self-employed consultant.
As with other roles and projects Amit worked on over the years, this was successful. It was also during this period of time that Amit learned about the opportunities that existed in Ireland working for SL Controls.
The SL Controls Opportunity
Amit was searching for engineering opportunities outside India in his area of expertise. He said: “Europe was my first preference, which is why I ended up searching for potential opportunities in Ireland.
“I found the SL Controls website during this search. After learning more about the work the company does and the types of clients it works with, I thought it would be a good fit. I then found out more about the job opportunities that existed at SL Controls, and I decided to apply.”
Amit then went through the SL Controls’ recruitment process, although it was a little more unusual than normal because of the distances involved in the initial conversations.
Amit said: “The interview process was remote, but it worked very effectively. I was able to present my skills and abilities, and I could ask questions and find out everything I needed to know.”
Moving to Ireland
Amit was successful in his application and began working for SL Controls on a computer systems validation project remotely from India.
This was for an initial three-month period during which the process of acquiring a visa was started. Amit moved to Ireland with his wife and young son in February 2019.
“I spent my first month in the Sligo office but I now work in the Maynooth office,” said Amit. “I have a lot of experience working in different countries so that wasn’t an issue, and my wife has experience moving with me.
“I suppose the weather here in Ireland was one of the biggest changes to get used to, but everything is settled now. My child is at school and there is a strong Indian community here in Ireland, so it’s been great so far.
“It’s great working for SL Controls too. The nature of the work and the clients are all very interesting, and the culture in the company is very good. Everyone has been very supportive of me in the move from India, both personally and professionally. So, I would have no hesitation recommending SL Controls to other engineers from anywhere in the world with the right skills and experience.”
If you are interested in finding out more about the opportunities that exist at SL Controls, visit our careers page now.
« Previous 1 … 7 8 9 10 11 … 17 Next »