Blog
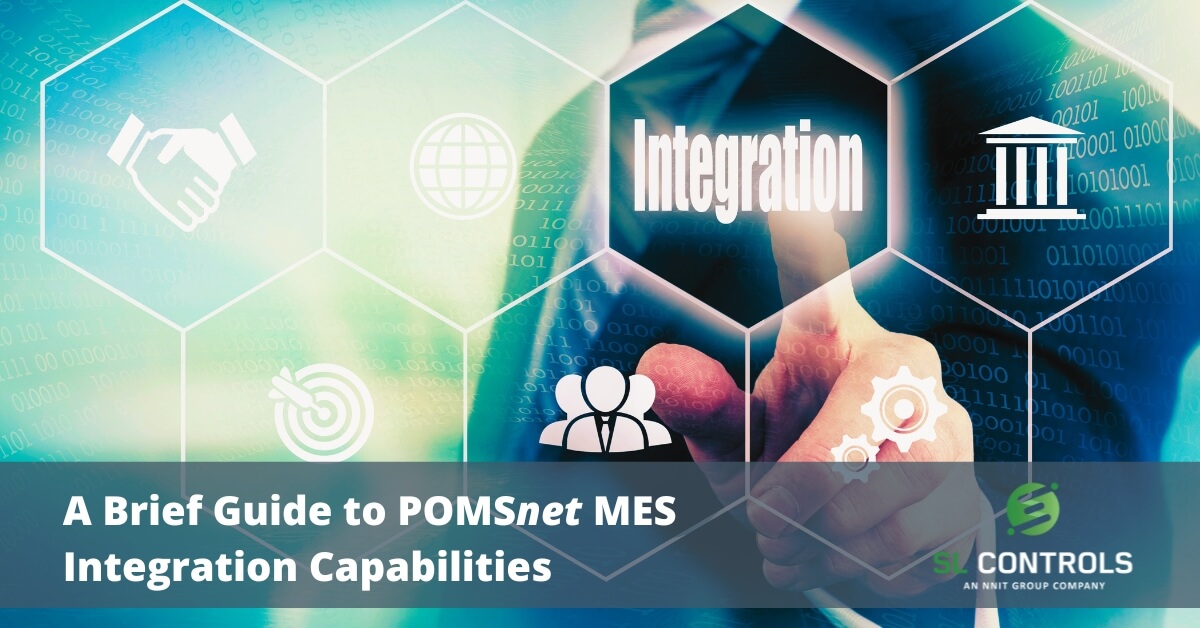
POMSnet MES Integration Capabilities – A Brief Guide
Integration is one of the primary considerations when choosing a Manufacturing Execution System (MES) for your pharmaceutical or medical device manufacturing facility. Not only does the MES platform need to have integration capabilities, but the nature of those integration capabilities is also important.
For example, an MES solution might have integration potential, but a huge amount of engineering hours could be required to create a complex and difficult-to-scale solution to make integration possible.
Integration capabilities are one of the key features of POMSnet Aquila MES (also known as POMSnet MES). POMSnet MES is integration-ready.
In other words, POMSnet is an MES platform that comes with out-of-the-box tools that enable integration across your manufacturing software stack and beyond, including legacy equipment and siloed systems.
Information Flow Bridge
One of the best ways to describe POMSnet MES is as a bridge – a bridge between manufacturing processes on the factory floor and enterprise resource planning. This bridge optimizes processes, drives OEE improvements, and facilitates a seamless flow of data across the organization, from previously siloed legacy equipment to the most advanced ERP platforms.
Examples of the systems, platforms, and equipment that can be integrated with POMSnet MES include:
- ERP – enterprise resource planning platforms
- SCM – supply chain management systems
- PLM – product lifecycle management systems
- LIMS – laboratory information management systems
- QMS – quality management systems
- CAPA – systems that manage corrective and preventative action processes
- Training management systems
- Document management systems
- Asset management platforms
Integration Features of POMSnet MES
Integration capabilities are built into POMSnet MES, making integration possible even with legacy platforms, systems, and equipment. The flexibility of the platform is the most crucial aspect. Because of this flexibility, legacy systems and equipment can be integrated with POMSnet MES via workarounds rather than making complex changes to code or replacing equipment.
This reduces both capital expenditure costs and the engineering hours required to develop solutions. It also simplifies the integration process, speeding up project delivery timescales.
For the most common manufacturing systems and platforms, templates are available within POMSnet MES as standard. The templates use industry-standard technology that streamlines implementation and reduces the complexities that can introduce risks. The standard templates that are available further reduce the engineering hours required for integration.
POMSnet MES also features direct device and process control system connectors that facilitate equipment integration with the platform. Examples of the equipment that can be integrated include barcode readers, local workstations, scales, etc
The Flexibility of POMSnet MES
The flexibility of POMSnet MES is important as the system can be set up according to business needs and the priorities and realities of your production lines and processes. For example, the order management feature of POMSnet MES that initiates work orders can operate independently, or it can be integrated with your ERP system.
SL Controls – Your POMSnet MES Integration Partner
At SL Controls, we have experience working as a POMSnet MES integration partner for companies in the life sciences sector. This experience includes implementing POMSnet MES in existing manufacturing facilities while delivering on key objectives such as retaining existing equipment and ensuring operator buy-in throughout the development and installation process.
To find out more about POMSnet MES, its integration capabilities, and the benefits to your production lines, get in touch with us at SL Controls today.
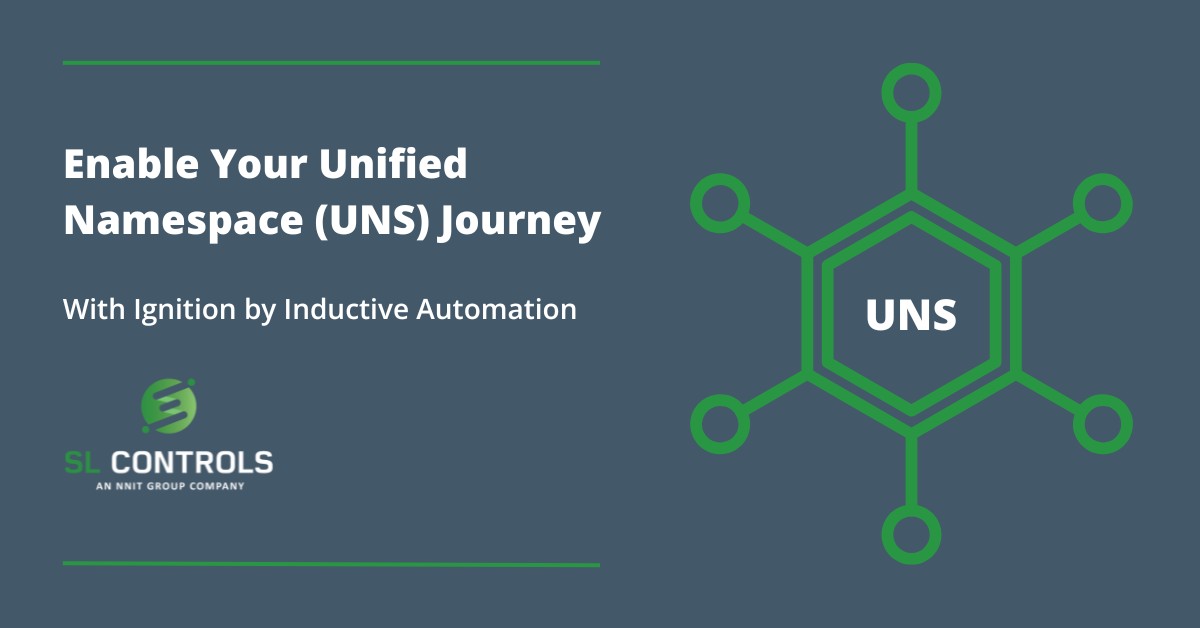
How Ignition Can Enable Your Manufacturing Facility’s Unified Namespace (UNS) Journey
The benefits of a UNS structure are hard to ignore (for an explanation of UNS and how it works, read our previous blog What is the Unified Namespace). This includes immediate benefits such as access to real-time data. A UNS structure also creates an environment that facilitates digital transformation as a UNS structure makes it less complex to implement modernization projects and initiatives.
The digital transformation foundation that UNS establishes is also less costly than alternative options as only one communication interface is needed across the entire IT and OT (operational technology) environment. Integrating new devices and nodes is easier too, and it is much more straightforward to scale.
Where do you start with UNS, though? What are the main steps and what elements are required?
Developing a UNS Strategy
Implementing a UNS structure involves redesigning existing technology architectures, especially those in the OT category. This is a significant undertaking. It is an undertaking that will yield substantial operational benefits and return on investment, but it is a significant undertaking, nonetheless.
Therefore, it is important to get your strategy and planning right as there are a number of approaches you can take when implementing a UNS structure. For example, as UNS is a technology architecture, it can be built from scratch. You can also utilize existing tools and platforms to accelerate development and expand functionality.
What is the best approach to take?
UNS Implementation Using Ignition
From our experience implementing digital transformation solutions in manufacturing organizations, especially those in the life sciences sector, basing a UNS structure on the Ignition platform is often the most effective strategy.
The Ignition platform by Inductive Automation simplifies and accelerates the process of establishing a UNS structure. Crucially, it also creates a robust foundation for future modernization and digital transformation projects where Ignition’s vast range of capabilities can be further deployed.
An alternative strategy that many organizations adopt is to implement a UNS structure as part of a wider digital transformation project, such as implementing a combined MES and SCADA solution. Whether you choose to concentrate on establishing a UNS structure or implement it as part of a wider project, Ignition brings a range of benefits.
The Main Steps for Implementing a UNS Structure
There are three main steps involved in implementing a UNS structure:
Planning
This stage involves defining your objectives as well as identifying all IT and OT systems and stakeholders. It is also important to identify potential challenges to the implementation of a UNS structure so steps can be taken to resolve or mitigate them.
Data Architecture
Defining the data architecture, including the naming convention, is a crucial phase of UNS development. It is also important to define infrastructure and security requirements.
Data Infrastructure
This is the practical stage where you develop and implement the data infrastructure with a combination of hardware and software solutions. Examples include:
- The Ignition platform to manage the UNS and provide edge data processing.
- Connection and integration of all endpoints, including equipment, PLCs, sensors, etc.
- Database or managed cloud data service.
- MQTT data broker to manage the transfer of data.
A UNS Structure and Digital Transformation Success
Creating a UNS structure is increasingly viewed as an essential step in the digital transformation of manufacturing and industrial facilities. It takes the most important element of any digital transformation project – data – and makes it recordable and available when and where it is needed in a central repository. By deploying Ignition as part of your UNS solution, you will have a robust and well-managed data environment alongside the functionality, flexibility, and scalability of Ignition.
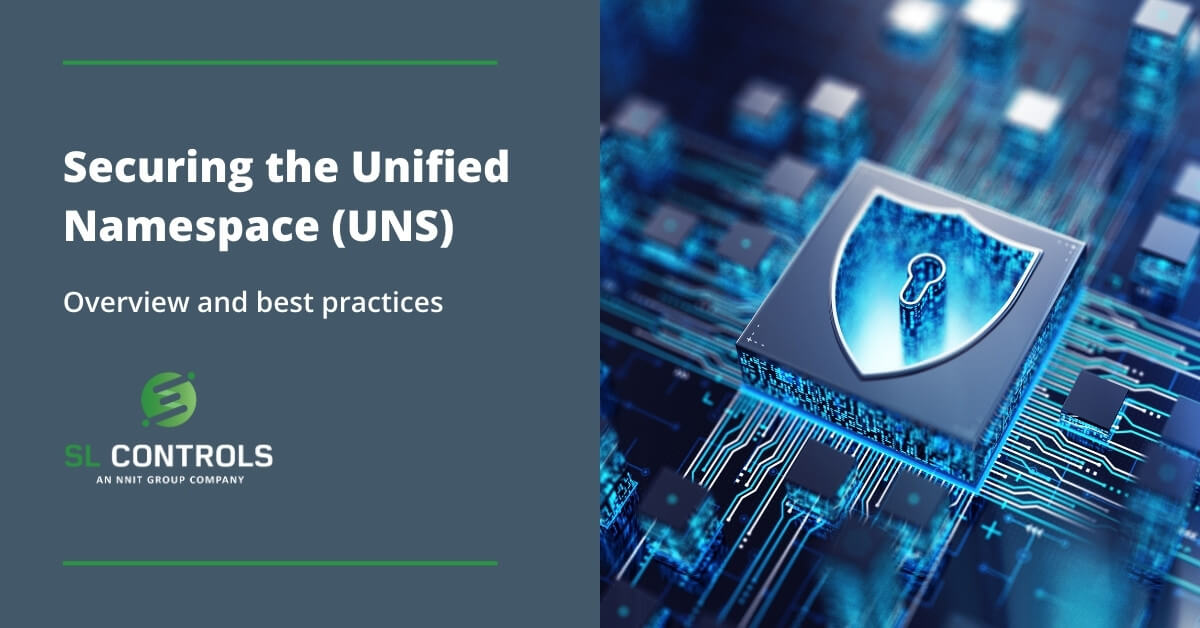
Best Practices for Security in the Unified Namespace (UNS)
The Unified Namespace (UNS) is increasingly viewed as a critical architecture approach in manufacturing environments as it enables effective communication between devices, equipment, platforms, and systems. As with all technology architectures, cybersecurity is an essential consideration.
In this blog, we’ll give an overview of cybersecurity best practices to protect systems, data, and the UNS.
Cybersecurity Challenge
A UNS architecture creates a platform for the modernization of manufacturing where key business objectives can be achieved such as improving quality, productivity, OEE, compliance, and operational competitiveness. As a result, UNS architectures are becoming essential for digital transformation success in manufacturing.
With all new technologies and strategies, there are challenges in addition to advantages and benefits. One of the challenges with a UNS architecture is cybersecurity.
Understanding UNS cybersecurity challenges is, in many respects, a simple equation. A UNS architecture enables the more widespread integration of devices, systems, and platforms to facilitate significantly enhanced communication via an MQTT (message queuing telemetry transport) broker.
More integration and communication combine to increase the potential attack surface in a manufacturing organization, i.e., points at which bad actors and cyber criminals can attempt to intercept or infiltrate. The implementation of an MQTT broker is the best example of this increased attack surface.
A larger potential attack surface is an important consideration for all manufacturing companies, but it arguably has greater significance in the life sciences sector where issues such as patient safety and patient data are top of mind, in addition to valuable intellectual property.
A Balanced Approach
Cybersecurity risks should not prevent or delay the adoption of a UNS architecture approach. After all, the only way to get close to full protection against cybersecurity risks is to eliminate all integration and communication. This is not feasible in the modern world, so a balanced approach is needed, where cybersecurity considerations are at the top of mind when developing and implementing UNS solutions.
A balanced approach involves following best practices with robust cybersecurity protections while ensuring data can flow within the network without delays or restrictions.
UNS Cybersecurity Best Practices
Access Control
Controlling access to data, authorizing clients to publish data, and authorizing clients to subscribe to data are crucial steps to ensure the UNS architecture is secure. Best practices include:
- Implement role-based access control to assign permissions.
- Authenticate users with strong usernames and passwords.
- Define access control rules with access control lists (ACLs) to allow for more nuanced and detailed control.
Encryption
The MQTT messaging protocol doesn’t encrypt data by default, but most MQTT brokers support TLS (transport layer security). Therefore, TLS should be implemented to encrypt data while it is in transit. VPNs and secure WebSockets can be used as alternatives if TLS is not suitable.
Firewall
The UNS infrastructure should be secured with firewalls to block traffic that is either unexpected or unnecessary.
Data Governance
UNS cybersecurity best practices include adopting robust data governance processes. Implementing data standards, policies, and procedures are all essential elements of good data governance.
Training
It is important to train staff on data governance. Training should also be provided on the proper use of systems and the security implications that exist when there is deviation from procedures or a lack of vigilance.
Securing the Unified Namespace
Securing the Unified Namespace is essential and can be achieved with robust cybersecurity strategies that utilize access control protocols, technologies like encryption, and the skills of employees through training. Security in the Unified Namespace is also not a one-time effort. Instead, it should be ongoing, with continuous improvement being a central focus to protect operations and respond to new threats.
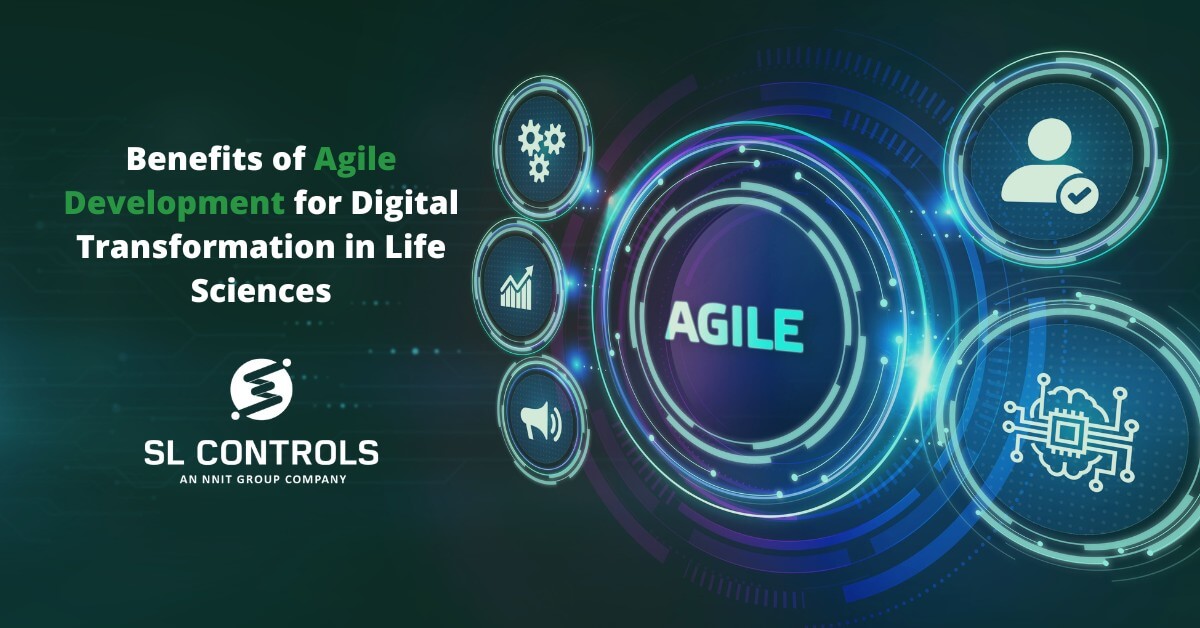
The Benefits of Agile Development for Digital Transformation in Life Sciences
Software applications play a crucial role in digital transformation, modernization, and improvement projects in the life sciences sector. This includes everything from bespoke applications to configured off-the-shelf solutions to customized vendor platforms. In all these situations, agile development processes offer a range of advantages.
Agile development has a long history in the software industry, but it is not widely used in life sciences. This is understandable as the Agile Manifesto favors working software over comprehensive documentation and individuals and interactions over processes and tools. In the highly regulated life sciences sector, documentation and processes cannot be ignored.
That said, the benefits of agile development also can’t be ignored as pharmaceutical and medical device organizations accelerate and widen their digital transformation and modernization strategies. Life sciences sector companies can benefit from digital solutions that are better aligned with business needs by adapting agile development methodologies and ways of working that are suitable for regulated industries.
What is Agile Development?
There are many different ways of developing a software solution, whether creating code from scratch or customizing a vendor’s platform. The approach that has been most commonly used in the life sciences sector is predictive development. This is the common waterfall model where the scope and specifications are set out at the beginning of the project with a big-bang delivery of the full solution at the end.
Agile development is a combination of two other approaches to software development – iterative and incremental.
Iterative is a prototyping-type model, where the exact scope and specification don’t need to be declared at the outset. Instead, developers listen to requirements and then create the code with an “is this what you are looking for” approach.
Incremental development accelerates value and ROI by creating, testing, and demonstrating code in small batch sizes known as sprints. Each sprint is designed to produce usable, valuable code that then becomes part of the final solution.
This iterative and incremental approach is more collaborative and ensures all stakeholders can see and use what is being developed throughout the project rather than only getting sight of the new code/solution at the end.
Benefits of Agile Development
Flexible and Adaptable
The traditional approach to software development required life sciences sector companies to understand and define what they wanted from the project at the outset. This can be incredibly challenging, especially on larger and more complex projects.
With an agile development approach, the scope and requirements can change throughout, so you don’t need to know everything you want or need at the outset.
Fixed Costs and Time
The traditional approach to software development in the life sciences sector involves variable costs and time. However, with an agile development approach, costs and time are fixed, helping with budgeting and planning.
- Traditional approach – the scope is fixed while time and cost are variable.
- Agile approach – the scope is variable while time and cost are fixed.
Competitiveness
Agile development methodologies are about quickly developing working and valuable code. This makes it possible for companies in the life sciences sector to pivot in order to remain competitive and/or meet or adapt to customer demand.
Faster Delivery of Value
You will see and use working code regularly throughout the process, ensuring continuous delivery of value during the project. In fact, it is even possible if required to push code live while the project is ongoing (subject, of course, to verification, UAT, and other testing processes).
End User Buy-In
One of the biggest challenges in new software projects is getting end-user buy-in. Agile development involves end users throughout the entire process so there are no surprises. End users also feel more ownership of the solution because of that involvement, plus they have hands-on familiarity with the application before it goes live.
Minimises Waste
In the traditional approach to software development, there are high levels of uncertainty as the scope, requirements, and specifications need to be outlined at the outset. Projects inevitably change over time, resulting in code being binned or reworked. This waste is largely eliminated with an agile development approach.
Agile Development in Life Sciences
At SL Controls, we have direct expertise in agile development processes in addition to extensive experience delivering solutions for life sciences sector companies, specifically medical device and pharmaceutical manufacturers. Understanding both – agile development methodologies and the essential compliance requirements and restrictions that exist in the life sciences sector – is crucial to project success.
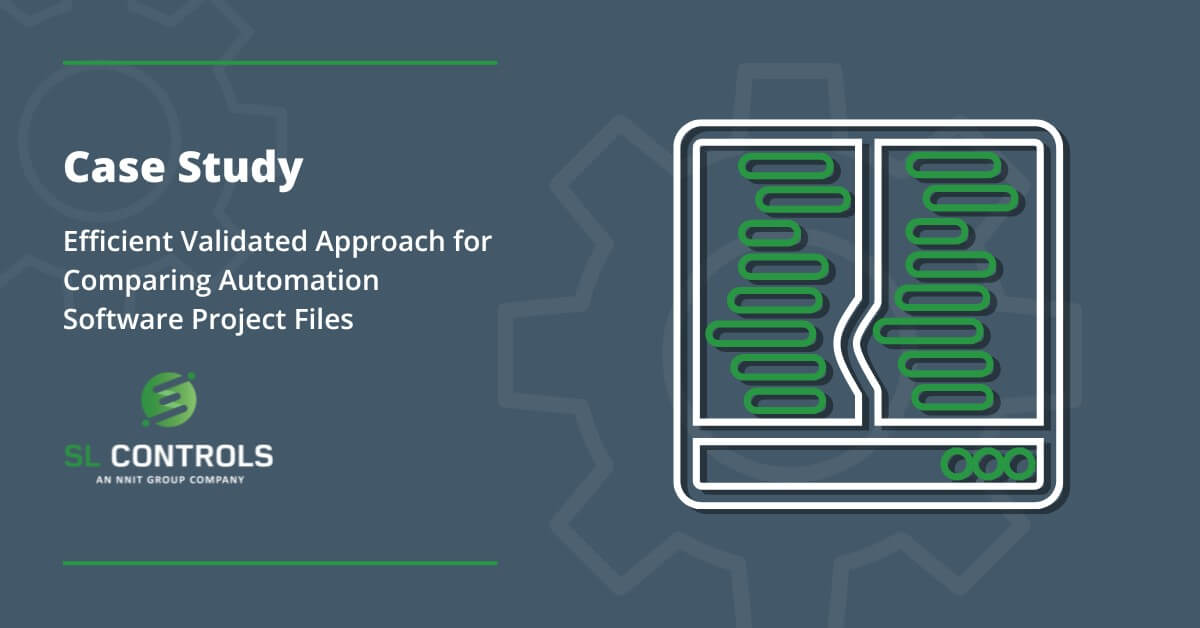
Case Study: Efficient Validated Approach for Comparing Automation Software Project Files
Leading automation applications and platforms continue to transform processes and operational performance in the life sciences sector. They offer an extensive range of features that continue to improve and evolve. That said, even the best automation platforms and applications have limits. They are designed and developed for specific purposes, and, in many cases, they perform very well. However, life science manufacturing facilities require wider capabilities than are often available within single platforms or applications.
This particularly applies when developing a new line or upgrading an existing line, where multiple machines, platforms, and applications are involved, and compliance considerations are as important as engineering and operational factors. In these situations, customized solutions are needed that facilitate the project’s operational, engineering, and compliance requirements.
The Solution
The solution that is the subject of this case study was developed for a multinational company in the life sciences sector. As part of the company’s growth and continuous improvement, new production lines were installed. Improvements were also made to existing lines. Part of the installation and testing process involved comparing automation software project files on several different platforms:
- Allen Bradley PLCs
- Siemens APT PLC (including APT address reporting)
- Cognex
- Generic files (e.g. robot files)
- Generic folders (e.g. robot files)
- Factory Talk View (currently in development at the time of writing)
- Wonderware Intouch (currently in development at the time of writing)
Some of the programs featured a compare tool but using those tools was challenging and time-consuming. The standard compare tools were also generic so didn’t meet the specific needs required by the customer.
In particular, there was no way to produce a validated history of changes using the standard compare tools, which is a compliance requirement. As a result, remaining compliant when using the out-of-the-box compare tools would have involved engineers taking screenshots of the compare tools output and then manually typing the reason for the change. This created significant scope for human error as well as being time-consuming.
The process for applications without a built-in compare tool was even more laborious.
Our client asked us to create a custom compare tool that would compare all the required automation programs using a validated approach.
What We Did
Our team developed a compare solution that met the client’s requirements as well as delivering additional benefits. A key component of the project was to ensure the solution worked with the required software project files. In some cases, different platform firmware versions were used onsite, so the solution had to be tailored accordingly.
The solution compared the automation software project files as required, automatically producing time-stamped history reports without any human intervention in the process. The solution itself was also validated by our team.
The Results
The main initial advantages for the customer included:
- Validated compare approach – the solution enabled a validated compare approach with the compare tool producing the required compliance documentation, including history reports and code review reports.
- Automated the compare process – the solution also streamlined the process of comparing the automation software project files, significantly reducing the engineering hours needed to complete these tasks.
- Reduction in human error – the solution captures all changes within the software project file. This highlights the change to the developer and reviewer of the project file and ensures no unintended changes are made.
The above benefits reduced the time required for SAT (site acceptance testing) so there was less downtime on the line.
This solution has enabled the customer to implement reduced testing strategies for repeat installations. Existing lines were also improved. Following the implementation and validation of the first software program, we streamlined testing and validation processes even further by using the compare solution to check that repeat implementations were the same as the first.
This further reduced installation time, testing time, and the engineering hours required on repeat installations.
In summary, the main benefits of the customized compare solution include:
- Compare automation software project files using a validated approach.
- Validate the code on the second manufacturing line by comparing it to the first using the compare tool.
- Reduced risk of human error by automating data recording and the production of history reports and code reviews.
- 75% reduction in required automation engineering hours for accurate history generation and highlighting all code changes.
- Reduced SAT execution time.
- Reduction in overall line downtime.
- Improved compliance
“Comparing the automation software project files was an essential part of installing and commissioning the new production lines at this life sciences manufacturing facility. Doing it manually would have needed significant automation engineering resources to complete time-consuming and repetitive tasks. Even then, there was no guarantee the histories would be correct as the entire process was open to human error.
“The solution we developed automated the software project file compare process while also ensuring the process was fully compliant. We were then able to utilise this validated compare approach on subsequent lines to speed up installation and testing times even further.
“Investing in custom software solutions can deliver significant ROI for manufacturers in the life sciences industry. In this case, those returns were delivered through a reduction in automation engineering hours, improved compliance, reduced compliance risks, and improved quality.”
Tom Nolan, SL Controls Program Manager
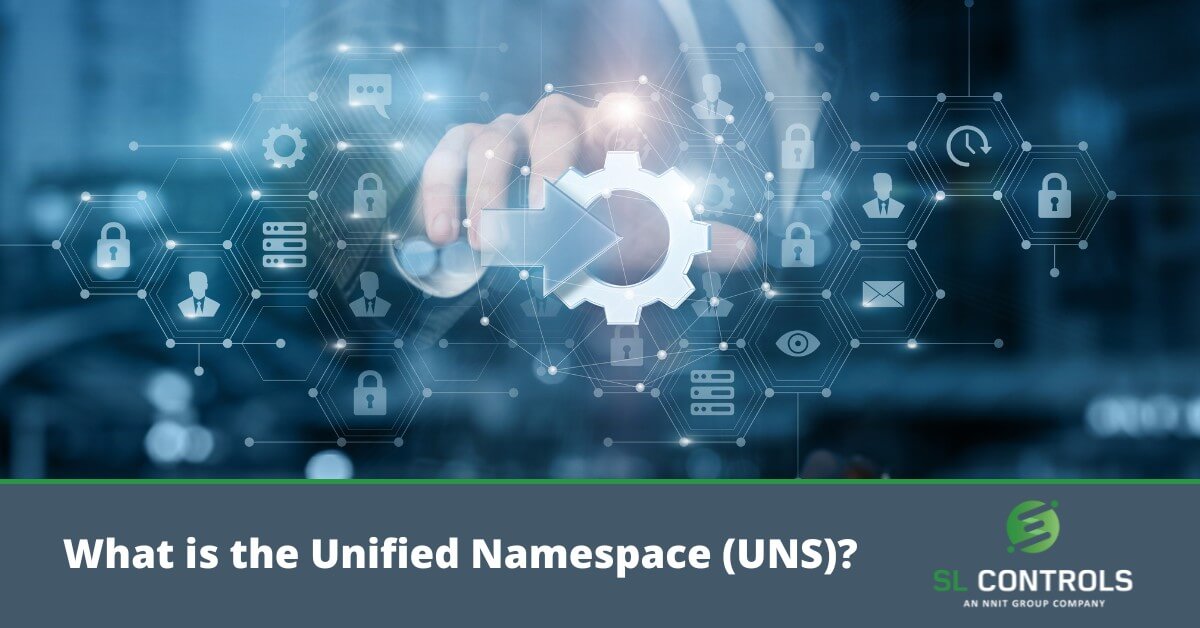
What is the Unified Namespace (UNS)?
The unified namespace (UNS) is a hot topic in manufacturing right now, largely because it is a key component to digital transformation success. We’ll explain what UNS is in this blog and why it is so important. At a high level, it is about data, integration, and communication.
Data, Integration, and Communication
Data is at the center of all digital transformation projects and initiatives. The aim is to make better use of your organization’s data to help achieve operational goals. Some examples include:
- Optimising processes, including digitalizing processes and transitioning from paper to glass.
- Improving data-driven decision-making.
- Facilitating automated decision-making.
- Enhancing the visibility of your operations.
- Enabling predictive analytics and scenario modeling.
Digital transformation success relies on the integration of data. Depending on the project, different machines, devices, endpoints, applications, platforms, and systems must be integrated so data can be exchanged, accessed, and used.
The problem is that integrating data using traditional approaches is not as efficient and effective as it could be. UNS is the solution.
So, what is UNS?
In a sentence, UNS is an industrial architecture approach that simplifies and optimizes the integration of data through two core principles: centralization and standardization.
The Traditional Approach
Let’s start with an overview of the traditional architecture approach. The technology stack in manufacturing organizations has traditionally been based on the ISA-95 model. Here is our version of that model:
This is a model that has served manufacturers well for years, facilitating process improvements and enhancing automation. Technologies have evolved, however, as have business expectations and market conditions.
A data-driven approach to managing operations is today’s reality, and there is one key feature of the traditional model that makes that difficult to achieve. That feature is the hierarchical structure of the traditional model, where data can only move one layer at a time.
To integrate components in the stack using a hierarchical structure requires point-to-point connections and lots of them.
Limitations of the Traditional Model
To fully understand the importance of UNS, it is helpful to first look at the limitations of the traditional model described above. Those limitations include:
- Multiple point-to-point connections require engineering expertise while often adding layers of complexity.
- The creation and maintenance of multiple point-to-point connections is costly.
- It is expensive and difficult to scale using the traditional model.
- Data can be incomplete or inaccurate.
- Data formats differ across the various levels, so data must be converted, multiple times in some situations.
The UNS Architectural Approach Explained
In a UNS architecture, there is a single data environment that can be accessed by all components – systems, machines, applications, endpoints, etc:
In other words, a UNS is a central repository for the information created and used by your manufacturing operations. It can exist anywhere, so long as it is accessible.
One of the key elements of a UNS is a naming convention. The naming convention standardizes the data and creates a single source of truth.
Another key element of a UNS is a communication interface. In manufacturing operations, this is typically an MQTT broker.
What is an MQTT Broker?
MQTT stands for message queuing telemetry transport. It is a messaging protocol designed to be lightweight and flexible, so it works in all types of environments and situations. This includes connections that have low bandwidth, high latency, or an unreliable network.
An MQTT broker is a central hub that allows the various components of the network (devices, SCADA systems, applications, etc) to publish data. Components can also subscribe to receive real-time updates on the data they need from other components.
This publisher/subscriber model of MQTT is beneficial to a UNS architecture as data is only exchanged between components that need it, speeding up the exchange and making the overall solution more flexible.
Benefits of a UNS Architecture
The advantages of using a UNS architecture include:
- Creates a central repository that contains standardized data
- Easy to scale
- Easy to integrate new components
- Reduces costs as only one communication interface is needed
- Improves operational agility as data on all components in the network is available in real-time
- Enhances oversight with real-time data, analytics, and dashboards
A UNS architecture will also enhance your digital transformation projects and initiatives, from paper-to-glass initiatives to process optimization to AI utilization and everything in between. It also helps to flatten the software stack in your organization, reducing digital transformation complexity – read our whitepaper on full stack OT (operational technology) platforms.
This blog is the first in a series we will be publishing on UNS. Upcoming blogs will explore in detail the platforms and technologies (including Ignition by Inductive Automation) that can deliver UNS. For more information on UNS architecture or to discuss your digital transformation requirements or objectives, please get in touch with us at SL Controls today.
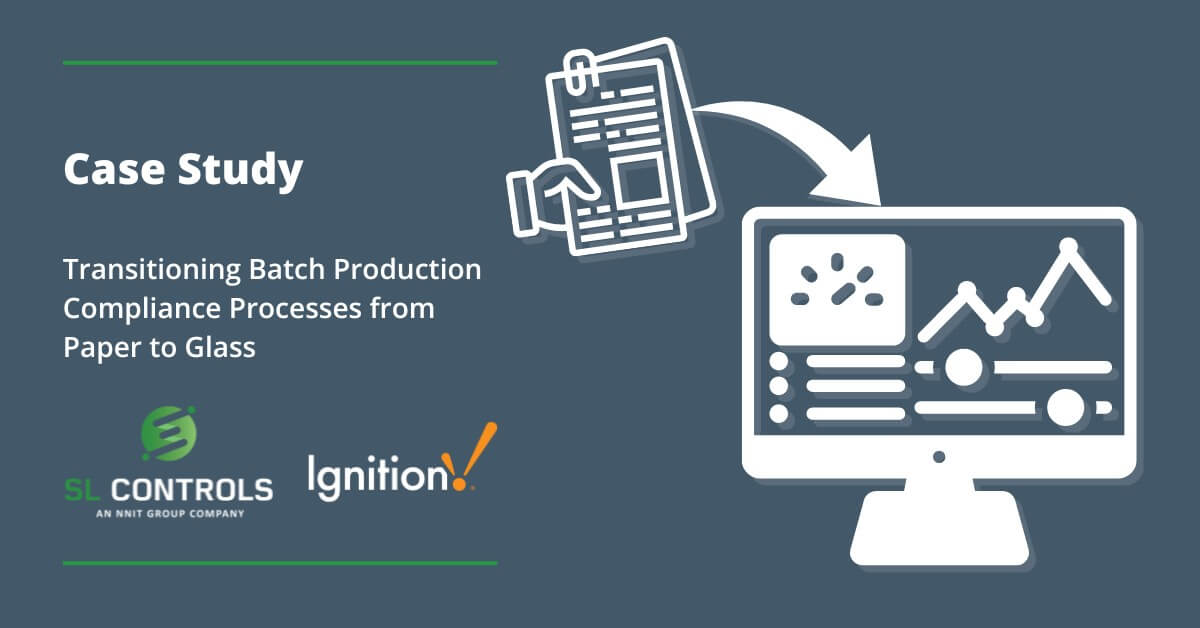
Case Study: Transitioning Batch Production Compliance Processes from Paper to Glass
Digitalization and smart manufacturing projects and initiatives can come under a number of different headings. One of the most common is paper-to-glass, where legacy, paper-based processes are digitalized and, where possible, automated.
Paper-to-glass projects deliver significant improvements measured against a range of KPIs. They can also help establish a foundation for further digital transformation projects and modernization initiatives.
This digital transformation case study outlines how the SL Controls team transitioned essential compliance processes in a life sciences facility from paper to glass. The new digitalized, automated, and semi-automated SOPs (standard operating procedures) transformed operations, eliminated errors, and delivered substantial efficiency savings.
The Project
The client in this case study is a multinational medical device company. We were brought into one of its facilities to digitalize and automate processes to drive efficiencies and improve productivity, compliance, oversight, data-based decision-making, OEE, operational agility, data integrity, and competitiveness.
Our client operates a batch production process on an automated filling and packaging line at the facility that is the subject of this case study. The production element of the line was efficient as filling and packaging processes were automated and largely digitalized.
This was not the case with compliance processes. While there was an element of digital record-keeping, essential compliance and quality workflows and SOPs were paper-based and manual. This included:
- Line clearance
- Changeover verification
- Cleaning execution
- Regular maintenance execution
These paper-based and manual processes meant the manufacturing facility could not operate at its full potential. Daily challenges included:
- Human error – staff were required to manually record data on paper before transferring it to a range of different systems, most of which were not connected or integrated. This exposed the company to the risk of human error and the knock-on impacts on batch release timescales, quality control processes, compliance, and data integrity.
- Data integrity issues – data integrity wasn’t just impacted by human error, as even accurate data could be recorded in different formats. There was also a lack of standardization in the organization’s systems.
- Inefficient use of resources – the paper-based processes in use by the organization meant resources were not used efficiently. Operations teams had to spend time on non-value-adding tasks, such as manually recording data on paper and then entering that data into digital systems. Human errors and data integrity issues led to batches being put on hold, resulting in resources having to spend additional time conducting investigations.
- Lack of oversight – the paper-based and digital data that was available could not be relied on to be complete, up-to-date, and correct, reducing oversight.
- Batch release delays – the overall impact of the company’s paper-based, manual systems resulted in unnecessary batch release delays. This had inevitable consequences for the overall performance, profitability, and competitiveness of the facility.
The last point in the list above is worth expanding on further, as batch release delays did not just occur when problems such as human error arose. To a greater or lesser degree, every batch release process took longer than necessary because of the lack of automation and the use of paper-based systems.
What We Did
The solution we developed for the client utilized the Ignition platform, with its modern and highly customizable SCADA and related features. Ignition also has excellent integration capabilities making it ideal for this project as we were working with existing equipment.
Using Ignition, we automated the legacy SOPs for all quality, cleaning, and maintenance procedures that are part of the batch workflow. This included leveraging the available equipment data on the line to automatically confirm equipment status and readiness. These digitized workflows are executed on mobile tablets running the developed application.
The Results
Accelerated Batch Release
Batch release on the production line was accelerated by an average of one hour per shift through a reduction of non-value-adding tasks, a reduction in human error, and the removal of data integrity risks.
Risk Reduction
The new system removed paper-based risks of completeness and quality control.
21 CFR Part 11 Compliance
The new solution fully complies with 21 CFR Part 11, and the system is fully validated.
Quicker Decision-Making
Operators, supervisors, and managers have access to real-time data, improving oversight, speeding up decision-making, and enabling data-based decision-making.
Improved OEE
Digitalizing 20+ processes accelerated batch release and raised the bar for equipment OEE (overall equipment effectiveness).
Scalability
We implemented the Ignition platform so it could be efficiently and effectively expanded across other systems, processes, equipment, and production lines both within the facility and in other facilities operated by the client.
John Downey, Portfolio Operations Manager at SL Controls, said: “The part of this project that is the focus of this case study concentrates on batch release and related compliance and operational processes on a filling and packaging line in a regulated facility. However, it also clearly demonstrates the power of not only the Ignition platform but also the concept of transitioning legacy processes from paper to glass.
“Our client has advanced technologies in a number of areas, particularly production processes. Compliance and quality processes had fallen behind in the digitalization push, so remained paper-based, manual, resource-intensive, and prone to error.
“The transition from paper to glass was smooth using the Ignition platform and the solution our engineers developed. Ignition is more widely used across the facility, but the benefits of this specific part of the project were significant, immediate, and measurable.”
Don Pearson, Chief Strategy Officer at Ignition by Inductive Automation, said: “We have worked with the SL Controls team on a number of Ignition implementations over recent months and years, and we are delighted they are one of our Premier Integrator partners.
“There are multiple applications for the Ignition platform in the life sciences sector, including in the essential areas of quality control and regulatory compliance. Digitalizing these processes through Ignition is possible even when using legacy equipment, and this project shows the results that can be achieved.
“We are proud this medical device facility now uses Ignition for a range of operational and compliance purposes, and we look forward to further expansion of the Ignition platform in the future. Well done to the SL Controls team for another successful Ignition implementation.”
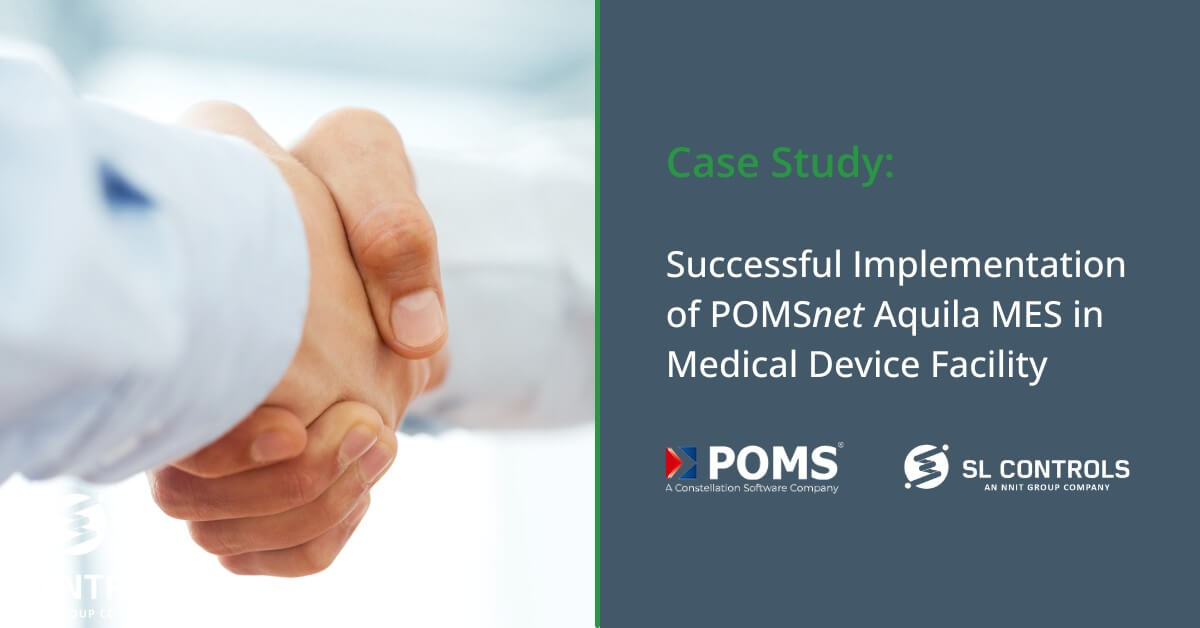
Case Study: Successful Implementation of POMSnet MES in Life Sciences Sector Facility
Digital transformation is a key priority for manufacturers in the life sciences sector. A crucial element of most digital transformation strategies is the implementation of MES (manufacturing execution systems) and/or modern SCADA solutions to digitalize processes and increase automation.
The customer who is the subject of this case study wanted to achieve this objective. They are a large multinational corporation in the life sciences sector with a manufacturing facility in Ireland. The MES platform we were tasked with implementing was POMSnet Aquila MES.
The Project
POMSnet was selected by the customer at a corporate level. To implement the platform, the Irish facility needed a local integration partner.
We were already familiar with POMSnet at SL Controls, and we could see synergies between the platform and the skills of our engineers. In addition, we have a close and long-standing relationship with the customer, plus our engineers are very familiar with the technologies in use at its Irish manufacturing facility. These factors put us in an ideal position to deliver this project.
What We Did
As with many projects of this nature, the implementation of the POMSnet platform would take place in phases. The first phase involved digitalizing two manufacturing processes.
Project Requirements
Our team started by gathering the project requirements, reviewing the paperwork that was being produced manually, and spending time with process owners and other key stakeholders.
Our approach with digital transformation projects like this one is to get a full understanding of the existing workflows and processes. The people closest to those workflows and processes have the most knowledge and experience, so their contribution to the project is vital to success.
User Involvement
Involving process owners and other key stakeholders at the outset of the project is also important to overcome the natural resistance to change that can exist in any organization. By involving team members in the project from the very beginning, they feel involved, consulted, and informed. They also made valuable contributions that enhanced the final solution.
The implementation stage also progressed more smoothly because of the involvement of team members at the earliest stages of the project. A primary reason for this is that less upskilling was required at the implementation point as team members were already familiar with the solution and had experience using it during the development stages.
Also, because of the way POMSnet works, the SL Controls team was able to digitally replicate the manual system, maximizing familiarity levels for those operators transitioning to new processes and ways of working. The fact that POMSnet is very visual in the way it works also helped.
Solution Strategy & Development
Our initial groundwork enabled us to develop a strategy to digitize the existing manual processes using the POMSnet framework. We developed a master batch record within POMSnet to facilitate the implementation of this strategy. Up until then, the master batch record was paper-based.
Following our analysis of the paper-based manual system, we broke the processes down into component parts. We then identified the parts that could be fully automated and presented them to the customer.
The customer selected the elements to automate, leaving us with automated components and components where an operator would have ongoing involvement. Within these parameters, we developed and implemented the POMSnet MES solution, although there were some challenges to overcome along the way.
Collating the Required Documentation
One of the challenges going from a paper-based manual system to a digitalized system in manufacturing environments is collating all the required information and records. This documentation is necessary so our engineers can identify areas of alignment where commonalities exist.
The documentation collation process is difficult because of the various systems, processes, teams, and people involved, but it is important as it reduces development time and improves support. Our engineers worked methodically with the various departments within the customer’s organization to gather the required documentation.
Legacy Systems
The project involved integrating the POMSnet platform with pre-existing equipment. Completing a project like this on a greenfield site is more straightforward as decisions can be made on equipment that ensures compatibility. In an existing facility, as was the case with this project, we didn’t have that luxury.
Instead, we had to leverage the information that was available without making any equipment or code changes. For example, we couldn’t request changes that would standardize a date format or provide us with additional data. We had to work with what we had.
This is one of the strengths of the POMSnet platform, though. The flexibility built into POMSnet meant our engineers were able to develop workarounds for every integration challenge and limitation.
The Results
The implementation of the POMSnet system went smoothly for three main reasons:
- Involvement of the customer’s team throughout the development lifecycle, from senior staff to factory operators.
- The skills and capabilities of our engineers.
- The flexibility of POMSnet and its extensive range of features
As part of the transition to live, we implemented a hyper-care scenario where support was available to the customer’s team on a rapid response, 24/7 basis. There were minimal calls to our support staff during that period, further demonstrating the success of the implementation.
Some of the benefits that have been achieved with the POMSnet MES platform now up and running include:
- Batch release processes on the two manufacturing lines are now 50 percent faster.
- Batch release processes are now automated on a release-by-exception basis, driving additional efficiency savings.
- Quality and material tracking lookups are now instantaneous as all the data is managed on the POMSnet
The success of the first phase of this POMSnet implementation, and the benefits it delivered, led to the second phase getting a green light from the customer. We are working on this second phase at the time of writing. The successful digitalization of manufacturing processes also led to new projects at some of the customer’s other manufacturing facilities.
Eamonn McManus, Director of Technologies at SL Controls, said: “Digital transformation projects like this involve utilizing some of the best technologies currently available. POMSnet is a great example. But the secret to success isn’t the technologies – it’s people.
“In this project, that included the customer’s team who worked with us through every stage. It also included the POMSnet team who provided fantastic support and, of course, our engineers and project managers who led the project throughout, from strategy creation to solution development to implementation and post-implementation support.
“We are delighted this project was a success and we look forward to helping other customers with their POMSnet MES implementations.”
William Shih is VP of the Professional Services Group at POMS Corporation. He welcomed the successful completion of this project.
William said: “The entire project ran smoothly from start to finish, from the upskilling of the SL Controls team through all development stages through to the successful implementation. As the makers of POMSnet Aquila MES, we know the power of the platform, so it is fantastic to see it delivering real-world benefits on a high-speed, high-volume production line in the life sciences sector.”
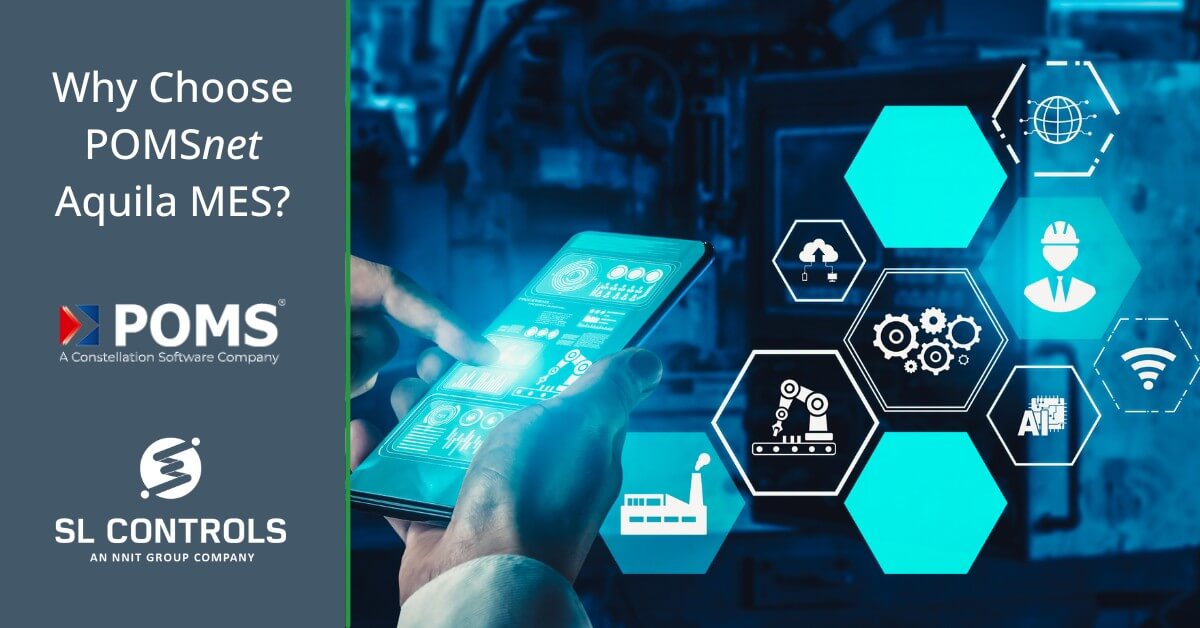
Why Choose POMSnet as Your MES in the Life Sciences Sector
Manufacturing execution systems (MES) are becoming increasingly important as organizations strive to improve productivity, compliance, and control while taking advantage of the opportunities presented by digital transformation technologies. The question is increasingly becoming which MES platform to choose, as there is a variety of options available. One of those options is POMSnet Aquila MES (also known as POMSnet).
At SL Controls, we have experience implementing and integrating the POMSnet platform for companies in the life sciences sector. In this blog, we are going to explore why POMSnet should be considered for your organisation and facility.
What is POMSnet?
POMSnet is an MES platform owned by the Constellation Software Company. In various forms, it has been delivering MES functionality to manufacturing organisations since 1988.
Why Choose POMSnet?
We have identified the 11 main reasons why POMSnet should be on your list of platforms for consideration when choosing an MES platform:
- Well-established solution
- Out-of-the-box flexibility
- Comprehensive range of features
- Highly configurable
- Easy to learn
- Integration capabilities
- Web-based
- Hosting options
- Cost-effective
- Reliable support
- Facilitates paper-to-glass initiatives
We can look at each of these points in more detail.
POMSnet is Well-Established
According to POMS, the platform is used in over 200 validated sites, it is used in some of the world’s largest pharmaceutical companies, the user base continues to grow, and it is one of the most widely used MES solutions in the life sciences sector.
POMSnet Offers Out-the-Box Flexibility
Many MES solutions operate on a customization model where the basic building blocks are provided by the vendor and then you work with an integration partner to customize the platform according to your requirements. POMSnet works differently, as it is both very comprehensive and highly configurable.
What this means is that POMSnet can be adapted to almost any life sciences manufacturing requirement without the need for potentially expensive and complex customisation.
POMSnet Comes with a Comprehensive Range of Features and Modules
As mentioned in the previous point, the out-of-the-box functionality that POMSnet offers covers all MES requirements. Those modules and features include:
- Electronic batch records
- Review by exception and release by exception
- Order management
- Equipment management
- Specification management
- Weigh and dispense for a range of material weighing requirements
- Quality management
- Personnel management
- Worksheets and log books
POMSnet is Highly Configurable
Each of the above feature categories and modules can be configured according to your requirements, ensuring you get an MES solution that is workable and delivers tangible benefits.
POMSnet is Easy to Learn
One of the biggest barriers to digital transformation strategies or the implementation of any new software platform is user buy-in. It is one of the points we address at SL Controls from the beginning of any project, and we continue to work on it throughout. Part of this task is made easier when the software platform is easy to learn and use, and POMSnet ticks both of those boxes.
POMSnet Has Advanced Integration Capabilities
The development team behind the POMSnet platform recognize one of the most powerful benefits of any MES solution is the ability to integrate with other systems in the organisation, especially enterprise-level systems. As a result, POMSnet has been developed to be integration-ready. It comes with tools out-of-the-box that enable integration across your manufacturing software stack, including with ERP, LIMS, and QMS systems.
POMSnet is Web-Based
As POMSnet is web-based, it can be accessed from anywhere and on multiple devices, including phones. The POMSnet solution is also touchscreen enabled.
You Have Multiple Hosting Options
You can host POMSnet on your cloud infrastructure or utilise the POMS SaaS MES Cloud option for comprehensive application and infrastructure delivery and support.
POMSnet is Cost-Effective
Any MES platform you choose should deliver a return on investment and then continue delivering financial benefits in areas like increased productivity, more streamlined compliance, and reduced risks. The pricing model and underlying costs of POMSnet make it a cost-effective MES solution.
You Can Expect Reliable Support
POMSnet is built using common and well-supported technologies that make supporting your implementation of POMSnet easier and more reliable, especially if you work with an experienced integration partner like SL Controls.
POMSnet Facilitates Paper-to-Glass Initiatives
One of the big trends in life sciences is the transition from paper to glass, where current manual processes (that are often paper based) are digitalized and, where possible, automated. POMSnet facilitates your paper-to-glass transition and enables a phased approach with a focus on user buy-in, compliance, process optimization, and long-term success.
Is POMSnet Right for You?
Do the above advantages and features of the POMSnet solution mean it is the best MES option for your facility or organisation? That will depend on your current infrastructure, requirements, and future plans, but POMSnet is likely to be a contender.
The best approach is to work with an integration partner like SL Controls as we have experience across multiple MES platforms. We can analyze your requirements and match them with the best solution for your needs. Get in touch today to arrange a consultation.