Blog
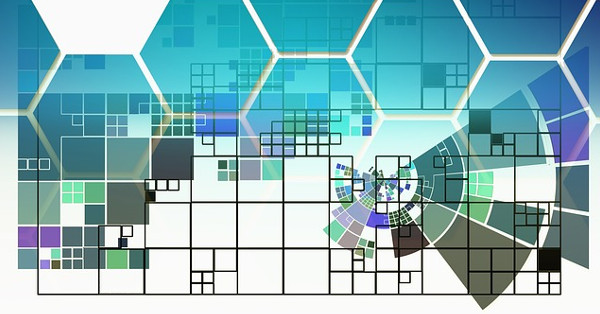
Data Integrity in the Manufacturing Process
Data is essential in modern manufacturing. Without data, you must make decisions based on guesswork and hunches. It is also harder to identify risks and opportunities without data. In addition, modern regulatory systems are data dependent. It is not enough to have data, however, as you must also have data integrity.
After all, the value and quality of data are not always the same, plus data processes, from collection to transmission to storing to reporting, are prone to errors.
In other words, you don’t just need data to make informed business decisions or meet the requirements of a regulator. Instead, you need the right data. This is why it is important to have a focus on data integrity.
What is Data Integrity?
Data integrity is a term that refers to the completeness, accuracy, and consistency of data, i.e. the quality of data. To achieve data integrity, data must have a complete structure with data values standardised according to data type.
In manufacturing, you need systems with structures that give you data integrity at the outset. Those systems must also include validation and error-checking elements to ensure the ongoing integrity of your data.
Why is Data Integrity a Challenge?
Even small inconsistencies or inaccuracies in data can cause significant problems with your use of that data. Unfortunately, those inconsistencies and inaccuracies are all too common in manufacturing facilities. You can lose data during a process or in transmission, for example, or elements of the data you store can be inaccurate.
These problems have the potential of occurring because most production lines feature multiple machines, pieces of equipment, and technology platforms. Those various elements perform different functions and often come from a range of different vendors.
All those vendors will have their own views on structuring data and standardising values. In other words, there are no common standards.
Problems with data also occur when you use systems for data management, processing, and reporting that are poorly designed and implemented.
To put this right and to give you data integrity in the manufacturing process, you need a third-party solution such as TOTALdata or TOTALbatch.
TOTALdata and TOTALbatch are part of a suite of products from SL Controls that automate key parts of the production process, including data management and reporting as well as batch control.
We built these products using our vast experience in creating bespoke integrated data systems for our clients.
Whatever solution you choose, it must standardise data values and structure, it must be vendor neutral, it must have processes that continuously validate the data you collect and hold, and it must be scalable for the future.
Benefits of Investing in Systems that Deliver Data Integrity
- Better decision making – you will have better information on which to base critical business decisions, such as whether or not to implement a project that aims to make your production line more efficient, but which requires a significant investment.
- Verify decisions – you can also use data to check previously taken decisions to verify and learn from them.
- Meet regulatory requirements and requests – for example, by proving your medical device or drug product continues to be compliant.
- Improves efficiencies – data integrity enables you to implement systems that automate processes that make your production lines more efficient. An example is batch control, a process that is very data dependent.
Industry 4.0 and the smart factories of the future will use more data, and in more ways, than we do now. Data integrity is a central component of the manufacturing process today and in the future.
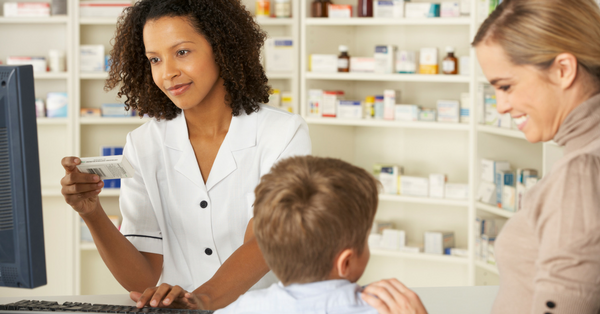
Falsified Medicines Directive – Potential Challenges You Should be Aware Of
The deadline for the implementation of solutions to meet the new Falsified Medicines Directive (FMD) is fast approaching – the new regulations go live on 9 February 2019. You can find out more about the regulations, including how the new systems will work, on our blog Falsified Medicines Directive – Are You Ready? What about the challenges you may face with the FMD?
As with most new regulations, there are challenges when preparing for new rules, initially implementing the rules, and then in their operation. Here are the potential challenges you should be aware of regarding the FMD.
The Scale of Serialisation Required
You must add a unique identifier (UI) to each product at the unit of sale (dispensing) level. In other words, there must be a serial number on the box or bottle of the product that eventually gets into the patient’s/customer’s hand.
This is likely to significantly increase the volume of products you need to serialise as part of your manufacturing process.
Randomisation Requirement
Another of the major differences between the FMD and other serialisation regulations around the world, including previous regulations in Europe, is the requirement for the randomisation of serial numbers. You need a solution that can handle this randomisation of UIs seamlessly.
Data Handling of Products that Enter the Market Before the FMD Goes Live
This challenge applies to products that have UIs but where that data does not go fully through the system. An example is where you are connected to the European Medicines Verification System before the date the FMD becomes active. The European Medicines Verification System is the EU hub you need to send UI data to.
There may be some products, however, that enter the market before the destination country of those products has its National Medicines Verification System up and running. This may result in the EU hub being unable to send information on your products to the national hub. While this will be a temporary challenge, it is one that you need to be aware of and plan for.
Verifying and Decommissioning Issues Before the FMD Goes Live
Another issue you might face with products entering the market before the FMD go-live date relates to verification and decommissioning. This is because it is unlikely that all dispensers and wholesalers will start verifying and decommissioning products until 9 February 2019.
This means, for example, you could have product serial numbers that are uploaded to the EU hub, transferred to the national hub, and then dispensed, but not verified or decommissioned by the dispenser. In other words, the serial numbers remain active in the system, leaving them open to fraud.
Dealing with Mistakenly Decommissioned Products
This is a challenge that is likely to be ongoing. It will potentially arise as your partners in the supply chain, such as dispensers and wholesalers, are responsible for decommissioning serial numbers.
Mistakes in this process are inevitable. To deal with this, those partners can re-commission serial numbers to correct the mistake. However, if they don’t, you could be in a situation of having products in the market but that cannot be sold/dispensed because of an administrative error.
Free Samples
This may be a challenge if you are used to other markets where free samples don’t need serial numbers. Under the FMD, however, they do. In addition, when a product is marked as a free sample, the serial number must be decommissioned.
None of these challenges are insurmountable, but your transition to operating under the new FMD will be smoother when you understand them and plan for them.
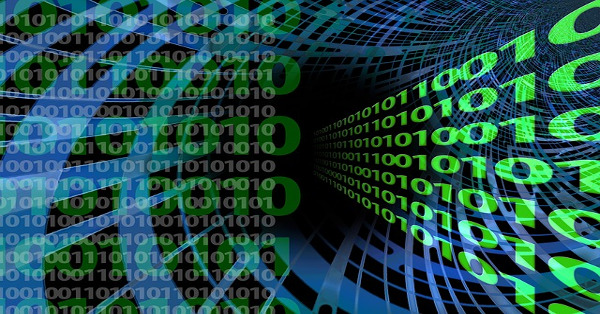
Digitisation and Digitalisation – You Need to Know the Difference
If you run a manufacturing facility, you need to know the difference between digitisation and digitalisation (or digitization and digitalization if you are reading this in the US). The difference is crucial to understanding Industry 4.0, plus it will help you develop strategies to transition your facilities into smart factories.
The difference between the two terms is often misunderstood. In fact, the two terms are usually used interchangeably. At the time of writing, for example, clicking on a link for digitalisation on Wikipedia redirects you to the page for digitisation.
The concepts are very different, however, and that difference is more than simple wordplay. Instead, the difference can have a real-world impact on OEE, the performance of your production line, and the overall performance of your business.
What Is Digitisation?
Let’s start with the more commonly used term, digitisation. It involves converting non-digital, analogue material to a digital format. For example, keeping digital records of production line batches rather than paper-based records.
You can also digitise business processes. We can use the above example again to illustrate this.
Digitising batch records is a much more efficient method of record keeping, but it also improves the batch traceability business process. In other words, digitising doesn’t just create digital records of batches. Instead, it creates them in a format that you can then use to make further productivity gains.
What Is Digitalisation?
Digitalisation is about transitioning your business to a digital business. This is why digitalisation is sometimes referred to as digital transformation.
You achieve this using digital technologies, so digitisation is a part of digitalisation. It is only a part of it, though. This is because digitalisation involves changing or adapting your business model, not just digitising your data, processes, and actions.
The result will be a business that is more efficient and productive. In addition, digitalisation can present you with new revenue-generating opportunities.
Digitalisation Example
A good example of digitalisation comes from the movie rental sector. The analogue, non-digital version of this business involved going to your local video/DVD rental store (such as Xtravision) to select a movie to take home and watch.
Movies were then digitised to make it possible to stream or download them online. Trips to the video/DVD rental shop became a thing of the past.
Digitalisation, however, created whole new business models. The digital business Netflix is one of the best-known examples. Digitisation was part of the process that led to the success of Netflix, but it also required a digitalisation approach.
In other words, it was digitalisation that enabled Netflix to develop its subscription-based model and then integrate that model on platforms like the internet, App Store, smart TVs, and more.
Digitalisation and Your Production Facility
Your business can be digitalised in a range of different ways. Moving to a predictive maintenance model for your machines and equipment is just one example:
- Non-digital – you schedule maintenance based on pre-determined time intervals.
- Digitised – sensors monitor key indicators to give you warnings of possible problems ahead of a breakdown. You can then schedule maintenance based on the actual wear and tear of the machine.
- Digitalised – a system constantly monitors the performance of the machine, including the early warning indicators. In addition, AI (Artificial Intelligence) technology enables the system to improve its ability to anticipate breakdowns before they occur. When a sensor triggers an early warning signal, the system automatically analyses the production output of the machine, taking into account anticipated demand in the future. It then automatically schedules the maintenance work so that it occurs before the machine breaks down but also at a time that results in the lowest possible productivity loss for the business.
While the above is a small example, it demonstrates what is possible with digitalisation as well as its potential. It’s time to start the transition.
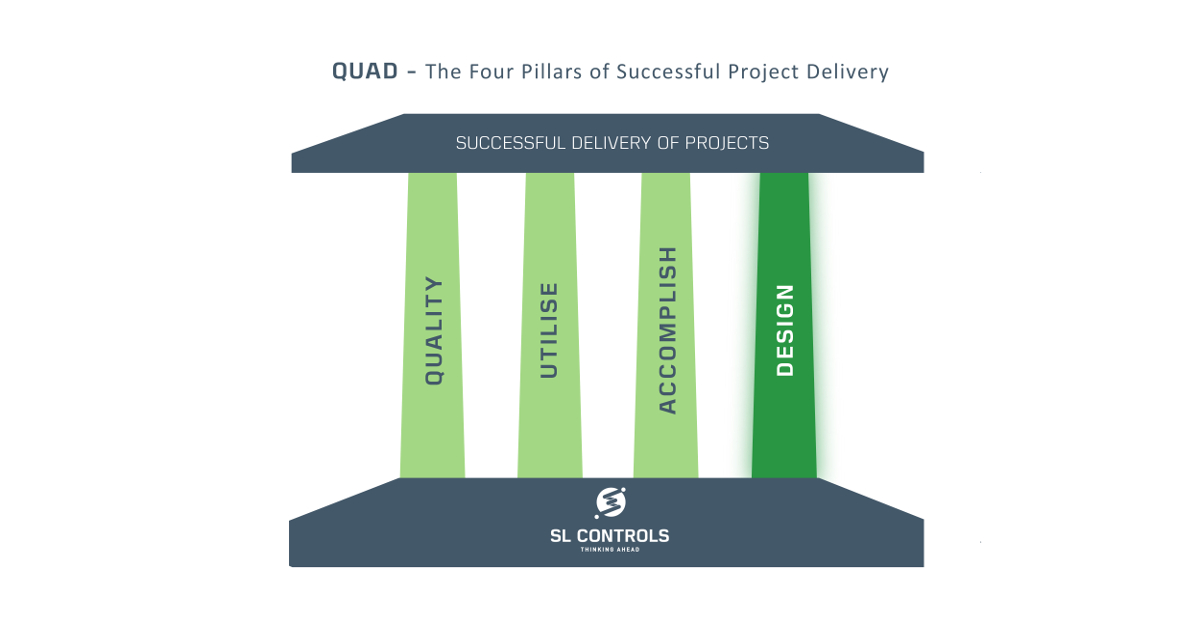
Design – the Prerequisite to a Successful Project
Successful projects don’t happen by accident. Instead, they need carefully developed and well-established structures. At SL Controls, we use the QUAD approach.
The QUAD approach for the successful delivery of projects is built on four pillars – Quality, Utilise, Accomplish, and Design. We are going to focus on the Design pillar in this blog.
The Design Pillar Explained
Robust design is a prerequisite to a successful project. It involves delivering functionality and features according to client expectations. It also involves engineering out problems in the most timely and cost-effective way possible and delivering the project within agreed timescales.
Crucially, design does not take place at a fixed point in the project. Instead, it is continuously part of the process with ongoing reviews and updates. It involves four main elements:
- Scope
- Research
- Create
- Review
A very structured and methodical approach to design is essential. At SL Controls, for example, we have a dedicated design team/group in the business. This team includes our most experienced people in solution design and architecture to ensure the project moves forward successfully.
What about the four main elements?
Scope
Without getting an accurate and agreed scope, the design team, developers, and others will have no firm or clear idea what the project is about. They can guess and make best estimates, but, without a scope, there will always be differences between what the client wants to achieve and what those delivering the project think the client wants to achieve.
So, agreeing the scope is an essential starting point.
The scope will then lead to a URS (User Requirements Specification) that must be agreed by all parties, so everyone understands what is involved.
Given the scope is such an important element, a lot of time goes into its preparation. That said, it is also necessary to make provision for when projects change during development. This requires a process of updating and getting new agreement on the amended scope and, when necessary, the amended URS.
Research
The research element involves researching different aspects of the scope to identify the best solution for the client. At SL Controls, our most experienced people lead on this part of a project and they use a range of techniques to conduct the research.
This includes using the in-house knowledge of our own people as well as our own internal design standards. It also involves referring to industry standards and best practices, plus we often use experiences, results, and lessons from past projects.
Feasibility studies can be part of the process too, depending on the project, plus it is sometimes necessary to bring in subject matter experts. This is beneficial when you have some knowledge and experience of an aspect of the project but believe the overall solution could be enhanced with the in-depth knowledge of a subject-matter expert.
Create
With the scope and all the research elements in place, it is now possible to create the design. The first step is to create a functional design specification. Functional risk assessments take place at this stage too, and actions are put in place to minimise identified risks.
The project then gets broken down further into an SDS (System Design Spec) which is essentially a blueprint of the project that developers can then work from.
Creating these documents is not enough, however, as it is easy to introduce problems at this stage. It is, therefore, beneficial to have a review system in place. At SL Controls, we use a peer review system where a peer in the design group reviews all documents.
In addition, system architects, managers, the quality department, and the client also review and approve the documents.
Review
Design is no good if it is static as this keeps problems in the project until the latter stages. In fact, without a robust and ongoing review system, you might not identify problems with the design until the install and commissioning stages of the project.
The problem with this is the financial and time costs involved in resolving a problem exponentially increases the longer the problem remains in the system.
Continuous review of the design and other aspects of the project helps prevent this. For example, when developers writing the code uncover issues, the design immediately goes back to the design team to resolve before moving on.
Benefits of the Design Pillar
Reducing the occurrence of errors in the latter stages of the project has several benefits:
- Lowers project costs
- Minimises delays
- Avoids reputational issues, including reputational risks the client faces by manufacturing sub-standard products as a result of errors in the project
In addition, by implementing all elements of the Design pillar in the QUAD approach, you will get a more robust design that delivers on client expectations.
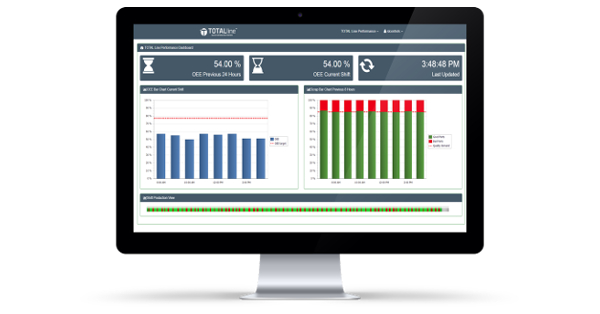
Convincing Management it’s time for Machine Monitoring Software
There are machines, software solutions, processes, and equipment that can and will improve your production line output as well as the profitability of your business. There are also things that will cost money to implement but will deliver negligible improvements. Making a distinction between the two is the conundrum facing managers in today’s manufacturing facilities.
All productions lines can become more efficient and more profitable, but achieving these gains requires investment. How can you be sure the investments you make will help the business while avoiding wasting money on those that don’t?
Machine monitoring software is the solution.
What Is Machine Monitoring Software?
Machine monitoring software collects data from all the machines and processes on your production line. High-quality machine monitoring software, like TOTALdata, achieves this by being vendor neutral.
The data it collects includes both production and non-production events, allowing you to see what is happening on the line and why.
This greatly helps the day-to-day running of your production line, but machine monitoring software also offers additional benefits. Specifically, you can use machine monitoring software to run predictive models.
Making Critical Investment Decisions
All too often, managers in manufacturing facilities must make investment decisions blindly. This happens when machine monitoring software is not in place.
Let’s look at an example of modifying a piece of equipment. The vendor has told you what it thinks the performance benefits will be, plus you will know the costs the vendor will charge.
You won’t, however, know the following with any degree of accuracy:
- Baseline performance data
- Predicted improvement data (rather than general figures from the vendor)
- Actual improvement data post-implementation
As a result, you must use assumed figures and estimations.
Making Informed and Transparent Decisions
Machine monitoring software gives you the data you need to make decisions based on facts. Firstly, the software will give you a performance baseline using real outputs from your production line.
Secondly, you can run simulations on the machine monitoring software. Crucially, you can do this before you make an investment or change anything on your production line, i.e. prior to engaging the vendor.
These simulations use data from your production line and enable your engineering teams to quantify and independently evaluate payback on process changes. They will do this by measuring the results from the simulation against your benchmarking data.
At this point, you will have an estimated return on investment figure based on real data. This enables you to make an informed decision on the investment.
There are also benefits of machine monitoring software post-implementation of the change in your production line. This is because you have the benchmark taken before any modifications. The software can then monitor the performance and profitability of your production line post-implementation, giving you an accurate and tangible return on investment figure.
In other words, you will have the following:
- Evidence the investment is worth pursuing before making a decision
- Proof the investment did pay off, enabling you to justify the decision post-implementation
The above applies to both small and large investment decisions, including decisions like buying a second production line.
Other Benefits of Machine Monitoring Software
Machine monitoring software is not static. Instead, it is flexible and dynamic, scaling and adapting to your business as you make continued improvements. In addition, the software is straightforward and cost-effective to implement when you use a product like TOTALdata.
To remain competitive, you must continually improve the efficiency and productivity of your production line and overall business processes. Machine monitoring software is an essential tool in achieving this.
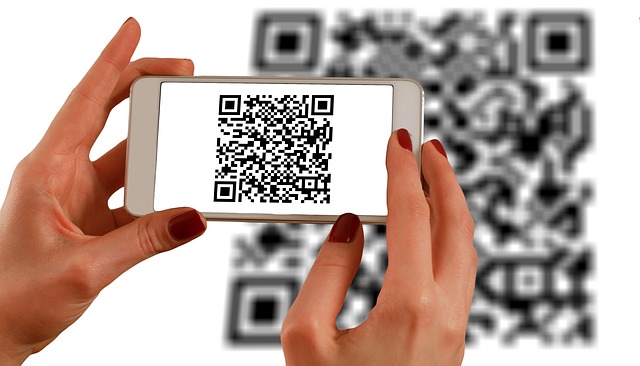
Falsified Medicines Directive – Are You Ready?
The deadline for compliance with the new Falsified Medicines Directive (FMD) is fast approaching. If you haven’t already taken steps to upgrade the systems and processes in your manufacturing facility, you should do so now.
In most situations, this will involve an enterprise serialisation solution and an upgrade to your packaging lines.
Below we answer some common questions about the FMD to help you understand what you need to do.
What is the Objective of the FMD?
The EU wants to protect its citizens from falsified medicines. The FMD also gives added protection to the pharmaceutical industry, helping to protect supply chains, market position, intellectual property, and more.
Where Does It Apply?
The FMD applies to all existing members of the EU, including the UK as it is committed to keeping its regulations in line with the FMD after Brexit.
Other countries outside the EU are also coming into line with the FMD, including Iceland, Norway, Switzerland, and Liechtenstein.
If you sell pharmaceutical products in any of these countries, the FMD applies to you.
When Does the Falsified Medicines Directive Come into Effect?
The FMD goes live on 9 February 2019 so there is less than a year left to get ready.
What Does the FMD Mean for Pharmaceutical Manufacturers?
There are three main requirements you have under the FMD as a pharmaceutical manufacturer. They specifically apply to the individual products that consumers purchase/receive, i.e. serial numbers and other elements must be item-specific, not batch, carton, etc specific.
The three main requirements on manufacturers are:
- Add an anti-tampering device to the packaging of medicines. The exact nature of this device is not specified by the FMD, so it is up to you to decide what to use. Most people interpret this as standard devices that are already widely used such as seals, tape, and glue.
- Add a unique identifier (UI) to all packages. This must be a 2D barcode that contains the product code, a unique serial number, the batch number, and an expiry date.
- Upload the UI code for each product to the European Medicines Verification System. You must also send other data to this system, including the countries the product will be sold in, details of the manufacturer adding the anti-tamper device, details of the wholesalers who will distribute the product, and more.
How Does the FMD Work?
Firstly, the European Medicines Verification System sends the data uploaded by pharmaceutical manufacturers to National Medicines Verification Systems in all participating countries.
There is then a responsibility at multiple points in the supply chain to verify products. Wholesalers, for example, must scan codes to make sure they come from the manufacturer as claimed. Pharmacists must do the same plus they must check the anti-tampering device, ensuring it remains intact.
What Else Do You Need to Know About the UI Code
The UI code that you add to each of your products must be a randomly generated 20-character alphanumeric code. The randomisation element of the code’s generation adds complexity and means you will need a specialised serialisation solution to ensure compliance with the FMD.
What Do You Need to Do Now?
If you haven’t already engaged a vendor to provide the systems and processes you need in your manufacturing facility, you should start looking now.
The solutions provider should have the abilities and resources to provide support at your location, plus the solution should be scalable and future-proof. The latter is important given the evolving nature of regulations relating to the Falsified Medicines Directive as well as pharmaceutical product serialisation in general, product traceability, and more.
SL Controls has experience of the FMD and making manufacturing facilities compliant, so please contact us today.
With support and help from the right solutions provider, implementing systems to comply with the FMD can be a smooth and benefit-producing process.
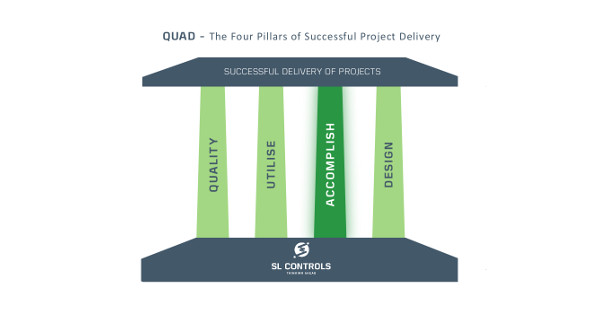
Accomplish – Executing a Successful Project
At SL Controls, we have developed an approach called QUAD for the successful delivery of projects. Each of the letters in QUAD stands for an essential pillar – Quality, Utilise, Accomplish, and Design.
We use the QUAD approach in the delivery of all our projects. This includes automation, controls, serialisation, and validation projects. QUAD has much wider uses than this, however, particularly in the fields of engineering and software development.
In previous blogs, we looked at the Quality and Utilise pillars. This blog will focus on the Accomplish pillar.
The Accomplish Pillar Explained
The Accomplish pillar is concerned with executing a successful project. In other words, it is the doing pillar so includes the practical steps required to deliver the project on the ground.
There are four main elements to this:
- Safety
- Execute
- Validate
- Communicate
Let’s look at each in more detail.
Safety
Safety is the single most important part of any project. It involves taking steps to ensure the safety of employees as well as ensuring their actions are safe.
This all begins at head office and at other regional offices. Specifically, it involves providing a safe working environment for all members of the team. This helps establish the right health and safety culture.
This health and safety culture is then carried through to the client side of the project during, for example, the installation and commissioning stages.
Firstly, all employees should be safety inducted onto every job and every site.
In addition, many companies have their own health and safety group or health and safety officer. It is important on-site teams and project managers ensure there is good communication with these people.
At SL Controls, we specifically focus on ensuring we are on the same wavelength as the client-side health and safety team, as well as ensuring we comply with all safety standards of the client.
Other health and safety best practices include:
- Carrying out risk assessments on all project tasks
- Producing safe plans of action and method statements
- Conducting safety toolbox talks
- Reporting all accidents and near misses both internally and with the client
Execute
The execute element involves project management tasks including scheduling, the creation and management of Gantt charts, and the implementation of agile software development techniques. The objective is to effectively manage the project to ensure it stays within budget and finishes on-time.
The practical steps involve the design group working upfront on the design aspects of the project. This then goes to the developers to complete their work. At SL Controls, we operate a closed loop feedback system between the developers and designers to ensure efficient delivery of the code. In other words, the process of giving feedback is structured and effective, with changes risk assessed and implemented as we go.
In addition to the above, SL Controls also operates a peer review system which we have found to be an effective tool for accomplishing the successful delivery of projects. The peer review system involves one developer creating and checking the code before giving this to another developer to conduct a double-check. This second check ensures nothing in the project requirements is missed as well as ensuring nothing is outside the standard.
In our experience, this peer review system reduces the occurrence of human error.
As well as the in-house phase, you should also plan and implement the installation and commissioning phase. The best approach is to assign a dedicated team, depending on the customer’s requirements. Those requirements might, for example, include evening or weekend work. This needs properly planned and executed.
Validate
The validation element ensures the project is validated against the acceptance criteria. Crucially, you should not only do this during the end stages of the project. Instead, validation should be part of the project from the beginning – at the user requirement stage. It should then continue through to completion.
At SL Controls, we follow the GAMP 5 V-model for validation. These are guidelines for project delivery in a regulated environment and are based on industry best practice.
To ensure we meet requirements for the project, we break it down into essential stages and elements. We then track this breakdown through traceability matrices. The objective is to ensure delivery meets requirements from the beginning through to completion when the customer signs off. At each stage, we get client approval.
Communicate
The way you manage communication in a project is critical to ensuring its successful delivery. The following communication tips will help:
- Only have meetings when they are needed.
- Only include people in meetings when they must be there.
- Use a RACI analysis to determine who should be a meeting. This first involves identifying the key stakeholders on your team, on the client side, and any other third party. With the RACI analysis, you then decide if that stakeholder is Responsible, Accountable, should be Consulted with, or should be Informed. This will help you decide who should be at what meeting.
- Once you have determined who you need to communicate with, you should put in place a stakeholder management plan. This should include, for example, who gets daily updates, who gets weekly updates, and who gets monthly updates. Make sure you deliver these updates according to client expectations.
- Collaborative working platforms, such as Trello, can help with project communication.
Benefits of the Accomplish Pillar
- Everyone goes home safe because of the emphasis on safety.
- The project will deliver on customer expectations.
- You will see a reduction in human error which helps you complete the project on-time and on budget. It also helps reduce double work.
- Members of the project management and delivery team, as well as others, don’t waste time in meetings they don’t need to be involved in.
- Generally, helps you bring projects to completion on time and on budget
Successful projects don’t happen by accident. You need all the pillars in the QUAD approach, including the Accomplish pillar.
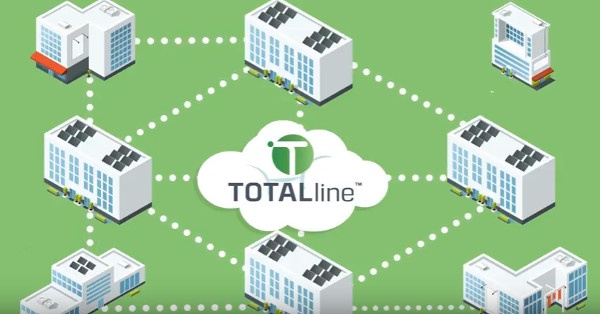
Video – The Smart Way to Make Your Factory Smarter
Turning factories into smart factories is a key consideration for everyone in manufacturing. After all, Industry 4.0 promises significant benefits in terms of efficiency savings, productivity improvements, and enhanced business intelligence. What next step can you take, however, that will help turn your manufacturing facility into a smart factory? TOTALsolution is the answer.
TOTALsolution is part of the TOTALline suite of products. Those products are:
- TOTALbatch – automates batch changeover and traceability processes
- TOTALdata – improves production line data collection and reporting
TOTALsolution features several modules enabling you to choose exactly what you need for your business. We then customise each module to your production line giving you the cost savings of an off-the-shelf product while still getting a solution tailored to your needs.
Watch our short video on TOTALsolution to get an overview of how this unique product works.
To find out more about TOTALsolution, the modules that are included, and how your business can benefit, please contact us today by emailing [email protected]
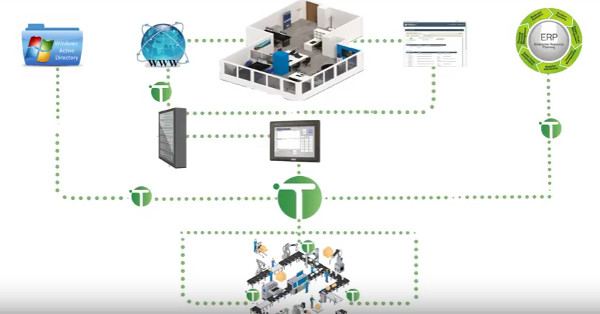
Video – Automating Batch Changeovers and Traceability
How long do batch changeovers take on your production lines? These processes should not take longer than a minute or two.
What about ensuring batch traceability? Are your current batch traceability systems inefficient, open to errors, and time-consuming? You should have an automated process that provides instant and full traceability on every product and batch.
All this is possible with TOTALbatch from SL Controls. TOTALbatch automates both the batch changeover process and your system for batch control, record-keeping and traceability.
This short video explains how TOTALbatch works and how your business can benefit.
Speak to a member of our team today about improving batch control in your business. Email [email protected] and we will get back to you.
« Previous 1 … 14 15 16 17 18 Next »