Blog
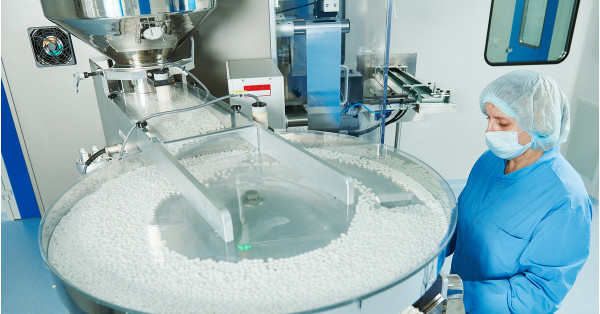
Automation of the Batch Changeover Process – Saving the Time Between Batches You Don’t Have
Batch changeovers are an essential part of many manufacturing facilities. They also represent a loss of productivity, however. After all, when you are changing batches, you are not producing products.
This is amplified further in pharmaceutical manufacturing facilities where the batch changeover and batch control processes are subject to regulations.
So, how do you reduce batch changeover time? Let’s first define what it is.
What is Batch Changeover Time?
Batch changeover time is the period of time between the manufacture of the last good part in the current batch to the first good part in the new batch.
In other words, it is the time it takes you to physically make the batch change on each machine before visually checking the machine and making a manual record.
The Traditional Manufacturing Approach to Improving Batch Changeover Times
Improving batch changeovers times has been an objective of manufacturing facilities for decades. Often it involves initiatives such as:
- Ensuring everyone on the production line understands their role and is accountable
- Applying efficient processes and practices such as getting parts/materials ready for the new batch before the changeover process begins, i.e. during the current batch
- Optimising the process so there is as little physical movement or waiting as possible
- Implementing technical improvements such as installing quick release mechanisms on equipment, modularising equipment, and ensuring as few adjustments are required as possible.
Much of the above is captured in a lean production method called Single-Minute Exchange of Die (SMED). It was developed by Shigeo Shingo, a former employee of Toyota who was involved in a production system aimed at reducing the car company’s batch changeover process.
Single-Minute Exchange of Die refers to achieving a batch changeover process counted in single digits, i.e. nine minutes or less. The method involves taking seven steps which incorporate many of the above techniques.
This was in the 80s, however, when the technologies we have today didn’t exist. Primarily, technologies that make automation not only possible but viable and, in many cases (such as pharmaceuticals manufacturing), essential.
The Way Forward is Automation
Automating batch changeovers delivers significant returns on investment. Not only that, automated batch changeovers are the future of modern manufacturing, particularly in high-quality, high-precision, and highly regulated industries.
The pharmaceutical industry is an ideal example. It is a highly competitive industry as well as being subject to strict regulations. Compliance with those regulations involves accurate record-keeping to give you full batch traceability.
Therefore, a manual/SMED approach to reducing batch changeover times will only take you so far. In fact, because of data logging and traceability requirements, it is unlikely to be possible to achieve anything close single-digit batch changeover times without automation.
So, while automation can improve batch changeover times in all sectors and industries, the benefits for regulated industries like pharmaceutical manufacturing are substantial.
In fact, improvements of over an hour to a few minutes are common.
Benefits of Reducing Batch Changeover Times Through Automation
- Production lines become more productive
- Improves OEE (Overall Equipment Effectiveness)
- Can also improve TEEP (Total Effective Equipment Performance) and OOE (Overall Operations Effectiveness)
- Makes compliance more efficient and effective
- Reduces traceability errors
- Improves quality as you will have fewer defects caused by incorrect adjustments
- Gives you more flexibility to, for example, reduce batch sizes
- You also have the flexibility to make other decisions that help the business overall such as reducing inventory levels
- Helps sales team as they can often offer reduced lead times
- Improves customer satisfaction
To stay competitive, you no longer have the time it takes to go through a manual batch changeover process. The solution is automation.
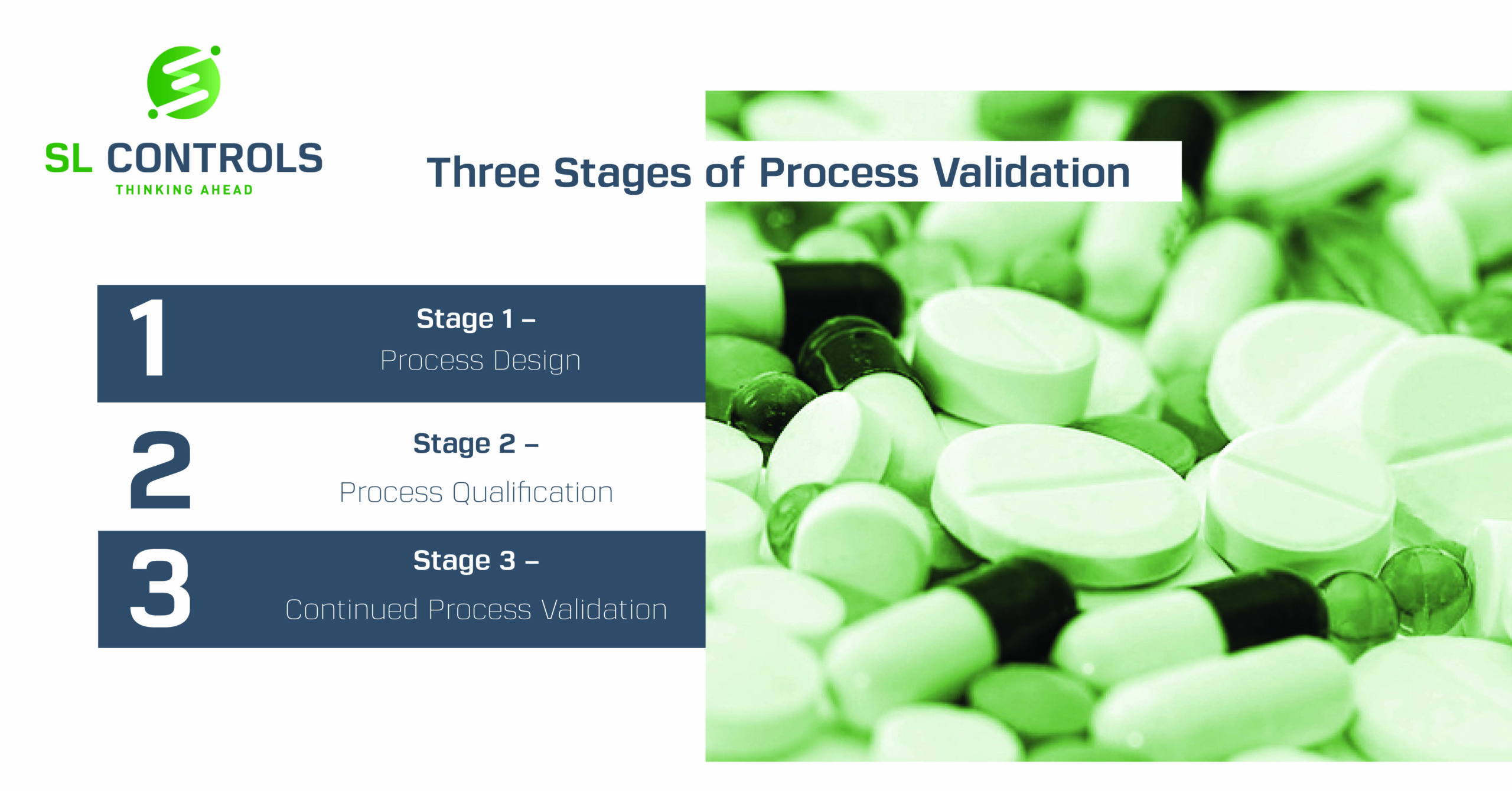
The 3 Stages of Process Validation Explained
The manufacture of safe and high-quality pharmaceutical products requires good manufacturing processes. This is the goal of Process Validation, i.e. ensuring pharmaceutical products consistently meet quality standards and expectations. The way to achieve this is through the Three Stages of Process Validation.
The Three Stages of Process Validation is a protocol published in 2011 by the Food and Drug Administration (FDA) in the US. Guidance from the European Medicines Agency published more recently promotes stages that are very similar.
The protocol applies specifically to pharmaceutical manufacturing and involves an approach to validation that covers the entire lifecycle of a product.
The underlying principle is that you cannot be sure of quality by only testing the finished product. Instead, you need to build in quality – as well as efficiency and safety – through each step of the manufacturing process. This is what the Three Stages of Process Validation aims to achieve.
The Three Stages of Process Validation
The definition of Process Validation from the FDA is as follows:
“The collection and evaluation of data, from the process design stage through commercial production, which establishes scientific evidence that a process is capable of consistently delivering quality products.”
The Three Stages of Process Validation are:
- Stage 1 – Process Design
- Stage 2 – Process Validation or Process Qualification
- Stage 3 – Continued Process Validation
Let’s look at each in more detail.
Stage 1 – Process Design
This is the research and development phase and involves defining a process for manufacturing the product. It usually includes the following:
- Creation of a Quality Target Product Profile (QTPP)
- Identifying Critical Quality Attributes (CQAs)
- Defining Critical Process Parameters (CPPs)
- Conducting risk assessments
From a regulatory point of view, an essential component of this stage is meticulous and comprehensive record keeping.
That said, the collection and evaluation of data as part of this Process Validation stage also has business benefits too. This is because you can use the data to optimise your production process, create efficiencies, and troubleshoot problems.
Stage 2 – Process Validation or Process Qualification
This stage evaluates/qualifies the process designed earlier to ensure it can reproduce consistent and reliable levels of quality.
It involves collecting and evaluating data on all aspects and stages of the manufacturing process. This includes:
- The building and facilities, i.e. ensuring they adhere to local regulations as well as pharmaceutical manufacturing regulations
- The transportation of raw materials
- Storage of raw materials
- The knowledge, training, and working practices of production line employees
- Every step of the process to turn raw materials into the finished product. This includes having pre-defined sampling points at various stages of the process.
- Finished product packaging, storage, and distribution
Another useful component of this stage of Process Validation is to develop contingency plans for situations where things go wrong.
Stage 3 – Continued Process Verification
Continued Process Verification involves ongoing validation during production of the commercial product to ensure the process designed and qualified in the previous stages continues to deliver consistent quality.
One of the main aims of this stage is to detect and resolve process drift.
The stage involves product sampling, analysis, and verification at various points in the manufacturing process, and requires the involvement of employees with quality control training.
Again, comprehensive record-keeping is required at this stage, including logging anomalies and issues with product quality.
Final Thoughts
The Three Stages of Process Validation are a regulatory requirement for pharmaceutical manufacturing, but they do not have to be exclusive to that sector. In fact, the stages can be useful to any production process that produces high-quality products where consistent reliability is essential.
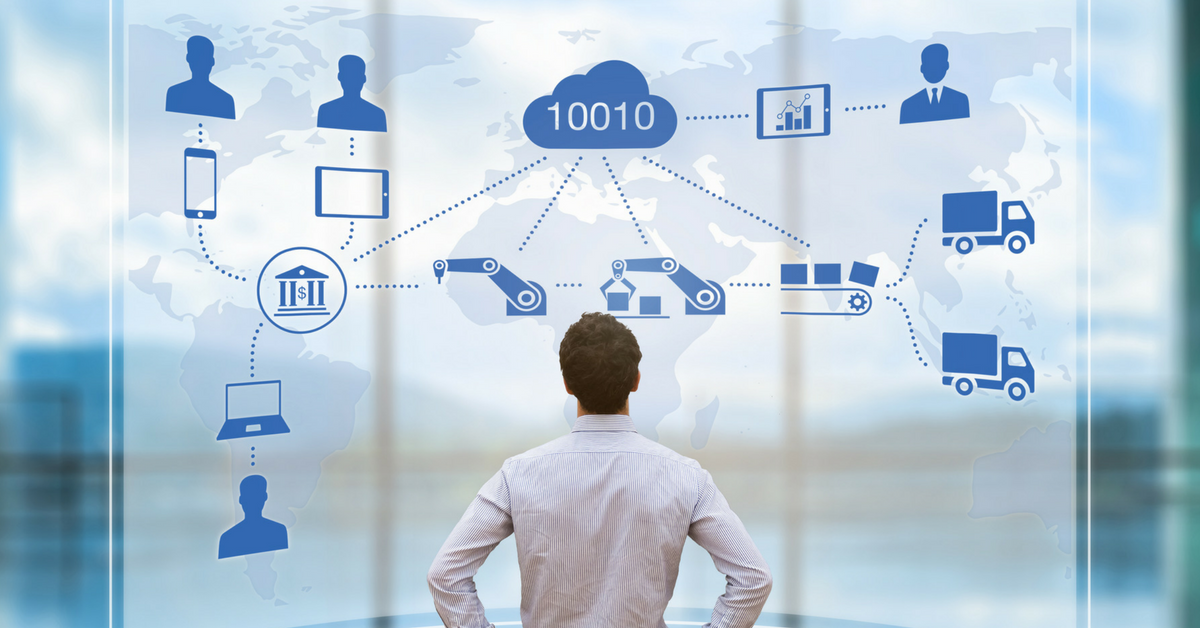
Industrial Automation Control Systems and How They Improve Businesses
Industrial automation control systems are becoming increasingly crucial to manufacturing in a range of sectors. They are often viewed as technical solutions, however, they come under the remit of the senior engineering team at the coalface.
The fact is, though, industrial automation control systems impact the wider enterprise, which means they can significantly improve your business. These improvements centre around enhanced productivity both on the plant floor and in other areas of the organisation.
This, in turn, makes you more competitive and flexible in fast-moving markets, as well as increasing profitability and ensuring your business is prepared for the future.
Before going into how industrial automation control systems improve the wider enterprise, let’s first explain what they are.
What Are Industrial Automation Control Systems?
Industrial automation control systems involve the integration of devices, machines, and equipment within the manufacturing plant.
As mentioned above, however, they can also go further than this by integrating the system on the plant floor with the rest of the organisation. This includes compliance processes, supply chains, sales operations, R&D, and more.
Industrial automation control system solutions require secure infrastructures to enable communications and data transfers as well as smart devices for the collection of data. Usually, you achieve this through sensors on machines and equipment.
Industrial automation control systems also require hardware, software, and communication solutions that turn the data collected by the sensors into information that results in an automatic action.
That could be actions within the production line, such as moving from one batch to another. It can also go further than this, however, such as automatically controlling the level of production based on real-time and automatically collected data from sales and distribution channels.
Improving Productivity
As mentioned, most of the business benefits of industrial automation control systems revolve around improved productivity. In other words, optimising the manufacturing facility as well as helping to optimise the business overall
Examples include speeding up production time which lets you then optimise distribution channels and processes that can then also feed into sales and customer service operations.
Here are some of the productivity improvements that industrial automation control systems bring to your business:
- As the automation control system takes care of repetitive tasks, you can optimise the use of resources in your production lines. Those repetitive tasks cover everything from batch changeovers to recording batch information to scheduling routine machine maintenance and more.
- Automation control systems also increase flexibility and scalability. For example, introducing new products to the production line is a smoother and faster process. It is also much easier to scale production up or down as the needs of the business dictate.
- You will see improved accuracy of data collection leading to significant improvements in batch and individual product traceability. This saves you money as you need to allocate fewer resources to this process, plus it improves standards of customer service. It improves compliance in regulated industries
- Industrial automation and control systems also improve accuracy in your factory operations overall. This is because a programmed controller, such as a PLC (Programmable Logic Controller) will perform a task to the same standard and within the same parameters every time.
- Your production facility will experience reduced downtime as automatic processes can predict failures, schedule the most efficient times for maintenance, and more.
- Finally, automation control systems result in fewer production errors saving time and money while also improving customer satisfaction.
A lot of the focus of industrial automation control systems is on the technical and plant-floor improvements they offer. The real benefits, however, exist in the business overall.
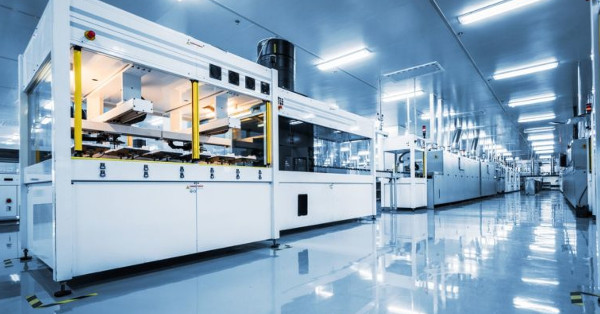
OEE, TEEP, and OOE – What is the Difference?
OEE, TEEP, and OOE are terms often used in the manufacturing industry. What do they mean, however, how do you calculate them, and why are they important?
OEE, TEEP, and OOE are different methods of defining the availability of your production line. In other words, they measure the difference between how much good products you could theoretically make in a perfect world compared to how much you actually make. This difference shows where you can make improvements to increase capacity without investing in new machines or production facilities.
Three main factors influence OEE, TEEP, and OOE:
- Availability
- Quality
- Performance
OEE – Overall Equipment Effectiveness
You calculate OEE based on the time you have a machine scheduled to run. OEE is the performance of that machine compared to its maximum capacity, i.e. what the machine could do if everything worked absolutely perfectly.
You measure OEE by looking at:
- Availability – the time you have the machine scheduled to run minus planned and unplanned stops
- Performance – when the machine doesn’t run at its full capacity for whatever reason
- Quality – the impact of defective products and reduced yield as a result of defective products
Here’s the calculation for working out OEE:
OEE = Performance x Quality x (Actual Production Time / Scheduled Time)
Note: Actual Production Time / Scheduled Time = Availability
TEEP – Total Effective Equipment Performance
TEEP takes into account all the factors that influence OEE, plus it includes periods of time when your production line or machine is not scheduled to run. This is sometimes referred to as schedule losses and includes periods of time when your production line is not open or operational. Overnight hours and weekends are the most common example.
So, 100 percent TEEP would mean a machine running 24/7 while producing perfect products as fast as it can with no stops.
Here’s the calculation for TEEP:
TEEP = Performance x Quality x (Actual Production Time / All Time)
Note: Actual Production Time / All Time = Availability
OOE – Overall Operations Effectiveness
OOE is a lesser used method of measuring production line availability. It is a slight variation on OEE as it makes a distinction between the time your plant is operating and the time a machine is scheduled to run.
So, for example, when you use the OOE metric, planned machine maintenance time is included in the OOE calculation but not in the OEE calculation. This is because, during planned maintenance, the machine is not scheduled to run. Other factors also impact OOE, such as shift changeover times.
In other words, OOE measures availability from the minute a shift starts until the minute it ends. In most production facilities, it is not possible to start and finish production exactly between these times as there will be inevitable waiting/changeover periods. So, where OOE is used as a manufacturing metric, it falls between TEEP and OEE:
- TEEP – total time
- OOE – operating time
- OEE – scheduled time
Here’s the calculation:
OOE = Performance x Quality x (Actual Production Time / Operating Time)
Note: Actual Production Time / Operating Time = Availability
Improves Decision Making
In summary, OEE, TEEP, and OOE are all used to improve the decision-making process. This applies when you are increasing manufacturing capacity as well as when improving productivity and/or building flexibility and scalability into your operations.
So, for example, before investing in new machines, you can look at improving OEE to ensure you are getting the most out of your machines during the times they are scheduled to be operational. Once this gets close to maximum, you can then start looking at TEEP to decide whether an additional shift or other solution can give you the capacity expansion you need.
In all situations, OEE, TEEP, and, where it is used, OOE, ensure you have the information you need when making critical business decisions.
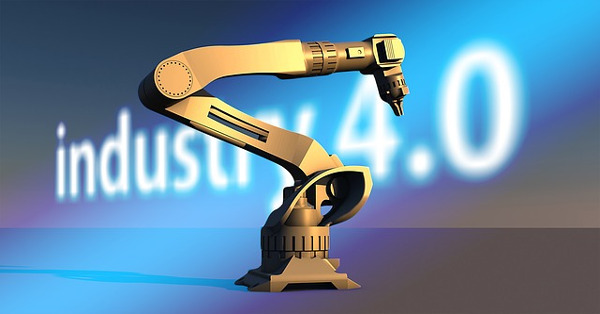
Demystifying Industry 4.0
Remaining competitive and profitable requires constant improvements in productivity, customer service, quality, regulatory compliance, and flexibility. Industry 4.0 promises to deliver these improvements.
Often, however, there is too much hype and/or misunderstanding surrounding Industry 4.0. It’s time for some clarity.
The Industrial Revolutions
Let’s start at the beginning: Industry 4.0 is another way of describing the Fourth Industrial Revolution:
- First Industrial Revolution – introduction of mechanical production, typically powered by steam engines
- Second Industrial Revolution – introduction of technology powered by new sources of energy, particularly electricity but also oil and gas
- Third Industrial Revolution – introduction of digital technologies including everything from the early mainframe computers of the 1950s to more modern automation technologies and internet-based communication and monitoring solutions
- Fourth Industrial Revolution – Industry 4.0
Before going into a more detailed look at Industry 4.0, it is important to understand the first three industrial “revolutions” are more accurately described (in terms of time) as evolutions. They did, of course, revolutionise manufacturing and industry, but each era lasted decades and built on the one before it.
The Third Industrial Revolution, for example, began in the 1950s. Only now, 65+ years later, are we transitioning to the Fourth Industrial Revolution.
Therefore, we can safely say Industry 4.0 will be evolutionary, so will happen over many years rather than a short period of time.
It will revolutionise manufacturing and industry, though, changing the world just as much (if not more) than the three Industrial Revolutions that have gone before it.
What We Can Expect from Industry 4.0
From a technology perspective, Industry 4.0 will bring deeper machine and process integration to your production lines. It also involves enhanced data collection which will lead to improved decision-making. Much of this decision-making will be automated. In fact, automation is a crucial part of Industry 4.0. Other technologies that will be important too include robotics, machine learning, and AI.
This doesn’t fully describe what we should expect from Industry 4.0, however, as the technologies above are about the practical side of manufacturing.
The impact of Industry 4.0 will go much further than this to change and improve your overall business. We can use a simple example of a technology that exists today. In the past, managing and improving the performance of production lines was a post-event task, i.e. you checked data after the batch or shift to get an understanding of results.
With Industry 4.0 technologies, however, you can establish a baseline for performance, with deviations from that baseline being monitored and identified in real-time. Obviously, this means you can address performance issues immediately, mitigating their impact.
Let’s take this a stage further: Industry 4.0 technologies will make it possible to have an AI system in place that monitors the performance baseline of your production line, taking automatic corrective action when required.
This means, however, taking a completely different approach to managing performance than the system most manufacturing facilities currently use.
So, Industry 4.0 is About Digitalisation and Organisational Change
Another example of the impact of Industry 4.0 on your wider business is meeting customer demand. Currently, this involves manual decision making (i.e. human decision making) on everything from analysing sales data to purchasing raw materials to authorising overtime so you can increase manufacturing capacity.
With Industry 4.0 technologies, this could all be integrated, with every point on the supply chain feeding data back to your production line. This then facilitates automated decision making as well as the automatic implementation of those decisions to meet expected demand, whether that demand means scaling up or scaling down production.
This then has knock-on effects. For example, a system like this could identify downturns in demand where it would schedule machine maintenance work, preventing future breakdowns as well as minimising the need for planned downtime when demand is high.
Planning for the Future
As you can see, the potential of Industry 4.0 is fascinating and exciting, plus it will dramatically improve the productivity and efficiency of manufacturing facilities.
However, we must not think of Industry 4.0 as a technology issue. It should instead involve a wider business digitalisation strategy that is led, planned, and implemented by top management. You can then achieve significant and durable benefits.
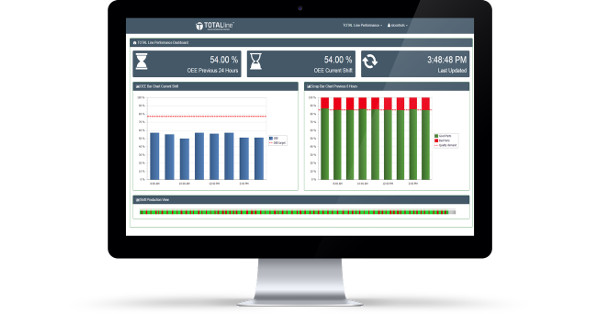
OEE and Why It’s Important
OEE is one of the most important performance measurements in modern manufacturing facilities. By optimising OEE, you can increase capacity, reduce costs, improve quality, and/or increase efficiencies in your production lines.
Now, here is the really interesting part – it’s possible to achieve significant performance gains in your manufacturing facility by optimising OEE. Before getting into that, though, here is a more detailed explanation of OEE and its benefits.
Overall Equipment Effectiveness
OEE stands for Overall Equipment Effectiveness. It is a method of analysing the performance of a machine or piece of equipment compared to its theoretical maximum capacity. OEE applies only to periods when the machine or piece of equipment is scheduled to run, though, i.e. you don’t include overnight downtime if the machine is not scheduled to run overnight.
OEE includes three main factors:
- Availability
- Performance
- Quality
So, a production line which has an OEE of 100 percent will manufacture only good products with no defects (quality), production will run as fast as it can (performance), and there will be no stop time, even for short periods (availability).
Issues that Impact OEE
- Availability – planned stops in production for setups and adjustments such as planned maintenance, cleaning, and quality inspections. In addition, unplanned stops in production, typically because of breakdowns, also negatively impacts OEE. Short stops and short periods of idle time are important too. These stops can occur for a range of different reasons including blocked sensors, misfeeds, and jams.
- Performance – this applies when production doesn’t run at its full capacity. This could be because of worn out equipment, poorly maintained equipment, environmental factors, or operator issues. Examples of the latter include operator errors, inexperience, or availability.
- Quality – defective products as well as the reduced yield that occurs as a consequence of defective products. Examples include operator error, wrong settings, and inefficient batch changeover processes.
Why Is OEE Important?
You may have significant capacity potential in your factory that OEE optimisation can release. This will increase production and/or make your operation more efficient and cost-effective.
In addition, taking steps to improve OEE is almost always more cost-effective than the alternatives. This particularly applies in the long-term but often also applies in the short and medium-term too. The alternatives include adding a new shift, increasing overtime, purchasing new equipment, outsourcing production, or opening a new facility.
Currently, an OEE score of 85 percent is considered exceptional. The reality is that many manufacturing facilities fall well below this rate, making significant improvements possible.
Benefits of OEE in Manufacturing
- Ensures you use existing equipment to its fullest capacity, reducing the need for investment in other areas
- Gives you a better oversight of the production process, so you understand where the real problems exist and how to prioritise them.
- Delivers significant return on investment whether you are increasing capacity, driving efficiencies, launching new products, and more.
- Helps you maintain competitiveness in the market, particularly in competitive industries like pharmaceutical and medical device manufacturing.
- Improved process quality which will save you time and money as well as helping maintain your reputation in the market while also avoiding the risks and consequences of product recalls.
- Reduces machine maintenance and repair costs as you can put proper plans and schedules in place.
- Improves the scalability of your production line.
How to Make Performance Gains Using OEE
The first step is to put in place real-time, condition-based monitoring of equipment in your production line. This means gathering, storing, and analysing data to identify the most important areas for OEE improvement.
With this information, you can then allocate a budget to improve OEE and achieve your overall objective which, in most cases, involves providing better value, service, and products to your customers.
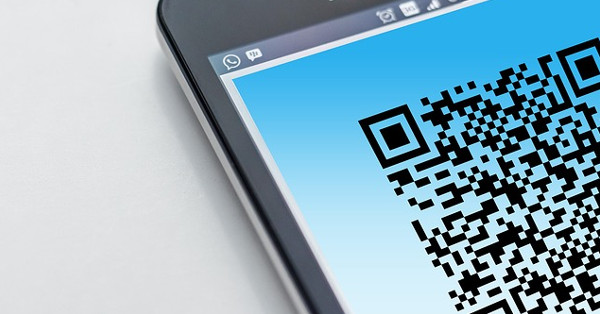
Key Serialisation Terms You Need to Know
Serialisation is about securing the supply chain, primarily in the pharmaceutical industry. At a very basic level, it involves applying a serial number and other features to a product, so it can be checked and cross-referenced as it moves through the supply chain to the patient/end user. As you might expect, however, serialisation involves much more than this.
New regulations and technologies have created a raft of new terms, abbreviations, and jargon. While this may not be completely familiar to you yet, regulations governing the traceability of pharmaceuticals will cover 75 percent of the world’s prescription drug supply by 2019. Serialisation phrases and terms, therefore, will come more and more into common usage.
Here are the main serialisation terms you need to know.
Key Serialisation Terms
- Authentication – authentication involves checking that a product comes from the manufacturer and is not counterfeit or marked as stolen. Verifying the serial number of the product is part of this process, but it is not enough to provide full authentication. Instead, other measures to check the product are also used, such as holograms, UV print, or micro-printing.
- Decommissioning – a process to mark a unique identifier as invalid or to highlight a product that still exists but should not be dispensed. In effect, the drug becomes inactive in the system. The Falsified Medicines Directive in the EU requires the decommissioning of products in a number of circumstances including when the product is exported to a region not covered by the FMD or if the product is going to be destroyed.
- FMD – the Falsified Medicines Directive. These are new regulations that apply to all EU member states as well as the UK which has stated it will comply with the FMD once it leaves the European Union under Brexit.
- Pedigree – a complete and certified record of the distribution of a pharmaceutical product as it goes through the supply chain. In other words, a record that details who owns the product at each stage of the process as it moves, for example, from manufacturer to wholesaler to pharmacy.
- Smallest Saleable Unit – the product that eventually is dispensed or sold to the patient/customer.
- Track and Trace – a key phrase used to describe the ability to understand a pharmaceutical product’s progress through the supply chain. “Track” is about locating where a product currently is in the supply chain. This could be by referring back to the last known scan of the product’s serial number, or it could be real-time tracking if the product has a tracking device installed. “Trace”, on the other hand, involves keeping a complete record of the path a product took as it went through the supply chain. This record may be checked months or even years later.
- UID – stands for Unique Identifier. It refers to a unique string of letters, numbers, and characters that make up the serial number of a product.
- Verification – systems and processes that verify a product is genuine. This could be simply checking the serial number matches the record supplied by the manufacturer. It also involves other methods of authentication, such as checking if that serial number is in the right location.
If you need help getting your business ready for the FMD or with anything else to do with serialisation and track and trace, please get in touch with a member of our team at SL Controls today.
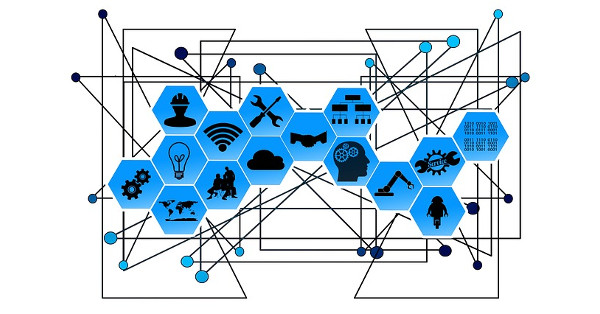
How Industry 4.0 Will Benefit the Pharmaceutical Industry
When thinking about the opportunities that Industry 4.0 presents, you get a sense of the excitement that great industrialists of the past must have felt with the introduction of steam power and electricity. These previous industrial revolutions changed the world for the better, and Industry 4.0 will do the same.
What about its impact on the pharmaceutical industry specifically, however? How can your plant benefit from the Smart Factory technologies available today, and those that will be available in the near future?
What Is Industry 4.0?
Industry 4.0 involves the convergence of people, data, and physical systems and the creation and implementation of autonomous computerised processes.
That’s quite a mouthful, so let’s take a run at it again.
Industry 4.0 is about automating and integrating all aspects of your business. This could be everything from the operation, reporting, and monitoring of a machine on your production line, to the ordering of raw materials from suppliers, to the traceability of products through your entire supply chain.
This is often called digitalisation or the digital transformation of your business.
So, what are the main benefits of Industry 4.0 to the pharmaceutical industry?
Increased Productivity
Improved productivity is one of the most important benefits that Industry 4.0 offers. From increased productivity, other benefits also flow.
Examples of increased productivity include:
- Automating processes so they can be completed faster and more accurately.
- Reducing downtime through automation and with the use of sensors and predictive systems that make machines self-aware. These technologies allow machines to auto-correct as well as predict failures, allowing for the better planning of maintenance to avoid unexpected downtime.
- Integrating the supply chain to make it more efficient.
- Making it possible to move away from batch manufacturing towards continuous manufacturing, a production method which involves much less downtime and improved productivity.
All the above leads to improved OEE in addition to productivity gains in other parts of your business.
Increased Quality
Automated processes and increased levels of automated and continuous monitoring of your production facility will lead to fewer errors and better-quality end products.
Industry 4.0 technologies also make it possible to improve the service you provide to customers. This could be by enhanced production planning, for example, achieved by connecting data from production, procurement, sales, and dispatch into one system.
Decreased Risk
This flows from the previous two points – greater accuracy in production will reduce the risk of poor quality products reaching end consumers.
Makes Regulatory Compliance Easier
Compliance with existing and new regulations coming into force in the EU and other locations around the world is easier using Industry 4.0 technologies. New track and trace systems and serialisation solutions currently being implemented to meet the Falsified Medicines Directive, for example, come under the Industry 4.0 umbrella.
Enhanced Business Oversight
Industry 4.0 technologies offer real-time reporting, the collection of greater amounts of data, better analysis of that data, and improved presentation of data in usable formats. This contextualised data leads to greater knowledge of both business and production processes which, in turn, leads to better decision making.
This offers a number of advantages. For example, contextualised data makes it easier to identify areas for improvement, enabling the better targeting of resources. Contextualised data also offers predictive analysis opportunities such as in product development or forecasting customer/patient demand, helping businesses plan for the future.
Creation of New Business Opportunities
Industry 4.0 will also create new business opportunities for companies in the pharmaceutical industry.
For example, Industry 4.0 technologies make it possible to integrate your supply chain end-to-end in a way that is seamless and highly efficient. This improves productivity, delivering immediate benefits for your business.
A more integrated and efficient supply chain is also easier to scale, however, presenting you with new opportunities for your business.
Increased Profit
When you package all the above together, the result is increased profitability in the business. Your business will also be more competitive and better-equipped to deal with the challenges and opportunities of the future.
Most pharmaceutical manufacturers have already started on the Industry 4.0 journey, taking the more realistic evolving approach rather than a revolutionary one. This still delivers benefits, and those benefits will only increase the further along the journey you go.
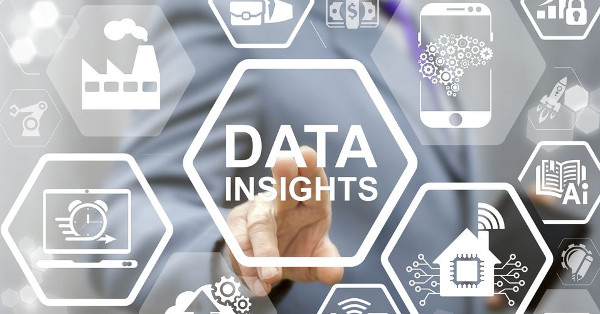
Benefits of Automating Regulatory Compliant Data Processes
The way your manufacturing facility processes data is becoming more and more important. This is true of manufacturers in all industries as consumer demands increase and competition becomes more advanced. Data processing is particularly important, however, in heavily regulated industries, such as the pharmaceutical and medical device industries.
In these industries, the benefits of automating regulatory compliant data processes are substantial. Here are 10 of the most important.
1. Improves Accuracy
Automating data processes produces higher quality and more consistent results. This ensures the information you give to regulators is as accurate as possible. In addition, data accuracy will also improve your overall production operation.
2. Simplifies Data Management
Automation greatly simplifies data processes in your manufacturing facility too. This applies to each stage including collecting, transmitting, storing, interpreting, reporting, retrieving, and more.
3. Improves Data Security
Automation can improve data security whether you have paper-based records or digital records, particularly if you currently hold those records on-site. By automating data processes, you can move the data you need both for regulatory and business purposes into the cloud. Enterprise-level security features can then be implemented to protect that data. This includes encryption technology, multi-generation (or unlimited generation) backup processes, and more.
4. Enhances Data Visibility
Automating data processes can also make better use of the data your equipment and systems collect. This enhanced visibility will make regulatory compliance a more efficient process. In addition, you will learn more about your overall business, helping you target areas for improvement, identify opportunities, and more.
5. Increases Productivity
Automating removes the need for the manual handling and processing of data. This gives you the opportunity to reallocate resources currently used for data processing to other areas of your business. In addition, an automated process is significantly faster than a manual one, letting you achieve more with the same resources and in the same amount of time.
6. Saves Time
Following on from the last point, the time savings that automation delivers will benefit your business overall, but it will also improve your compliance processes. For example, you will be able to send reports and respond to regulatory requests much faster when you have automated data processes. This is because you can run reports or retrieve information at the click of a button rather than manually going through records.
7. Reduces Costs
Reducing the resources required to process data, in addition to improving productivity and saving time, will reduce costs in your business. In fact, the initial capital cost of developing and implementing an automation solution will be quickly offset by the money you save as a result of the solution’s implementation.
8. Improves Adaptability
The regulatory landscape in Europe, the US, and in other parts of the world is evolving. Of course, this is nothing new, particularly in the pharmaceutical, biopharma, and medical device industries. Automating data processes, however, will make it much easier for your business to adapt to future changes in regulations.
9. Enhances Business Oversight
As you can see from most of the points above, there are overall business benefits of automating data processes as well as benefits to your regulatory compliance efforts. One of the most important benefits that data process automation delivers, however, is enhanced business oversight. In other words, all levels of your business will get a better understanding of processes and operations. This includes information relevant to senior management through to highly detailed data used by engineers responsible for the operation of specific machines.
10. Improves Decision Making
Following on from the last point, enhanced business oversight improves decision making. This is because you can make data-driven decisions, confident in the knowledge the data used is accurate, high-quality, and consistent.
In summary, automating regulatory compliant data processes will help you remain competitive while also ensuring your business doesn’t become overburdened with compliance issues.
« Previous 1 … 13 14 15 16 17 18 Next »