Blog
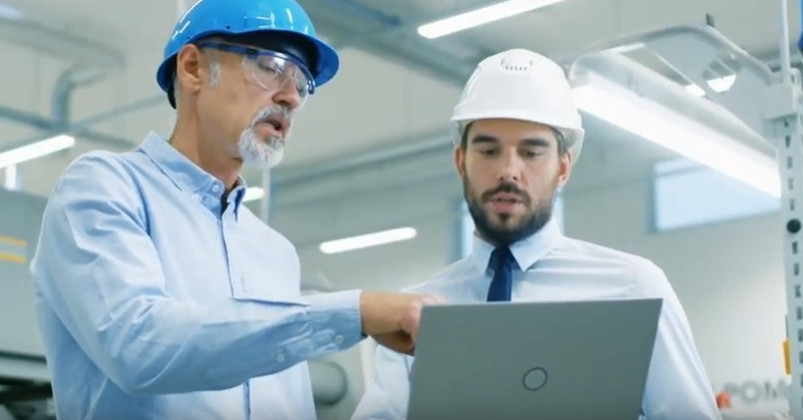
VIDEO: Find Out More About SL Controls Validation Services
Validation is essential in high-volume, highly regulated manufacturing environments such as manufacturers of pharmaceuticals and medical devices. At SL Controls, we provide a full range of Validation Services. Check out our new video to find out more about our capabilities and experience as well as how we work when delivering Validation Services.
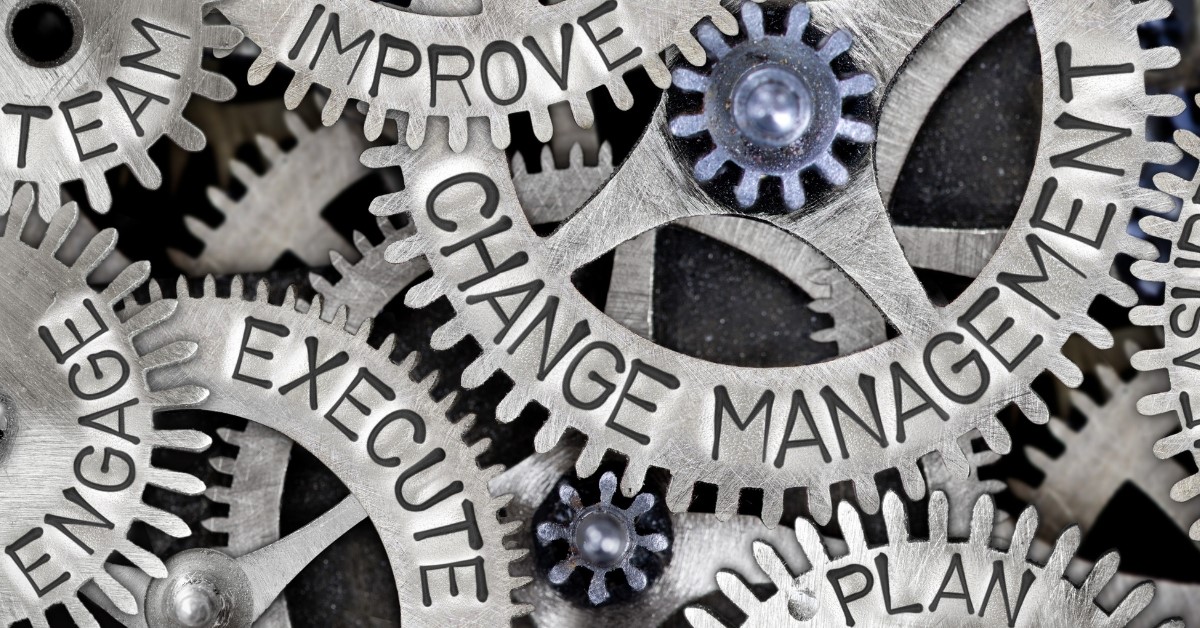
The Importance of Change Management in Validated Systems
Implementing change in a validated system is a crucial time for ensuring it remains controlled. As a result, it is essential that change management is carefully planned and implemented.
This is particularly important for compliance reasons, not least because a carefully planned and documented change management process demonstrates to regulators that validated systems remain in a controlled and validated state after the changes take effect.
Categorising the Planned Change
Not all changes in validated systems are the same. For example, changes can be minor, or they can be complex and far-reaching.
In manufacturing environments, you can normally categorise the changes being requested in three ways. By doing this, you can assess the resources you will need to successfully implement the change and ensure your processes and systems remain validated.
The three main categories of change in a change management process are:
- Minor – minor changes require minimal testing to ensure re-validation. You can normally limit this testing to the specific element that is the main subject of the change.
- Major – major changes require more wide-ranging re-validation efforts. This often means testing and re-validating areas that are both directly and indirectly impacted by the change.
- Critical – critical changes typically involve re-validating the whole system. These are the most resource intensive and high-risk change management processes.
Do You Always Need to Re-Validate When a Change is Made?
Typically, yes, particularly in manufacturing environments that are heavily regulated such as in pharmaceuticals manufacturing and medical device manufacturing.
The question is more about the scale of the re-validation effort that is required. In other words, is the change small and likely to have a minor impact? If so, minimal testing is required. For more substantial changes, however, further re-validation work up to full re-validation may be required.
Change Management Steps to Ensure Systems Remain Controlled and Validated
Step 1 – Assess the Change Request
This includes assessing whether the change request is clear and whether the requirements and objectives of the change are well-defined. It’s also important to assess whether the change request is justified, i.e. is it worth doing given the impact it could have on the already validated system.
Step 2 – Assess the Impact
You then need to assess the impact the change is likely to have on the controlled system. Often this involves conducting a risk assessment. A risk assessment will help to identify the parts of the system that require re-validation and new testing.
Step 3 – Document the Expected Outcomes
The risk assessment and analysis of the impact of the change will produce a set of expected outcomes. You should document these outcomes as part of the change management process.
Step 4 – Implement the Change in a Safe Environment
This could be a sandbox environment on a computer system, for example. If the change is being made to a manufacturing process, machine, or piece of equipment, the safe environment could be a digital twin. The safe environment could also be on a physical machine or manufacturing process while production is shut down.
Step 5 – Testing
Test the changes you have made and their impact on the system in the safe environment. This testing should be measured against the expected outcomes documented earlier. The results of the tests should be also be documented.
Step 6 – Implement the Changes in the Live Environment
Once you are happy with the results of testing in the safe environment, you can move to implementation in the live environment.
Step 7 – Testing and Re-Validation
Further testing and re-validation should take place with full records kept of all tests and test results.
Step 8 – Update Validation Documentation
The change you have implemented is likely to have made the existing validation documents out-of-date. You need to update these documents with the new information, specifications, processes, etc.
Step 9 – Train Users
Finally, it may be important to re-train users on how the changes implemented will affect them.
The Change Management Process
Ensuring your systems are validated during periods of change, however minor the change, requires careful planning and proper change management. This ensures ongoing regulatory compliance and makes the overall process more efficient.

How You Can Increase Profits by Moving from Planned to Predictive Maintenance
Unplanned downtime caused by equipment or machine breakdown costs money and eats into your profits. Modern technology provides a solution that offers significant improvements compared to other methods that are used to maintain machines and prevent unplanned downtime. That solution is predictive maintenance.
In other words, using real-time data to predict in advance when a machine is likely to breakdown as well as identifying the cause of that failure. Maintenance can then be scheduled before this event occurs.
This is different from the planned maintenance model, a model which is widely used but which has several flaws.
The Problem with Planned Maintenance
Most manufacturing facilities use planned equipment and machine maintenance models. In other words, they work from a pre-determined schedule to organise maintenance work on machines, often based on the number of hours the machine has been in operation.
This model is outdated, however. Of course, planning maintenance is better than leaving maintenance until something breaks. Planned maintenance is far from perfect, however.
Typically, planned maintenance schedules often come from OEMs who base maintenance schedules on best practices, generalisations, and, when they have it, aggregated data.
Planned maintenance schedules cannot take into account the specific circumstances of your manufacturing facility, however. After all, a machine on your production line will operate under a completely unique set of parameters compared to any other machine of the same make and model in any other manufacturing facility. This creates the potential for unplanned downtime.
This is the problem that predictive maintenance can solve.
You Should No Longer Accept Unplanned Downtime
Unplanned downtime is something that manufacturing facilities have always sought to combat. After all, unplanned downtime, however minor, means lost productivity which, ultimately, hits the bottom line.
In previous decades, however, when planned maintenance schedules were the best option for preventing breakdowns, unplanned downtime was unavoidable – a necessary evil, so-to-speak.
This is not the case today, not least because technologies exist that make it possible to eliminate unplanned downtime caused by equipment failure.
Unplanned downtime is also unacceptable in modern manufacturing environments because of the highly competitive nature of many industries and the pressures that exist on profit margins.
Eliminating Unplanned Downtime with Predictive Maintenance
Predictive maintenance is the next step forward from planned maintenance schedules. At its most basic, predictive maintenance involves using sensor technologies to capture real-time data from machines. You then use software algorithms and reports to identify anything that indicates the potential for a breakdown.
Crucially, you will have this information while the machine is still operational. You can then arrange for maintenance work during a period of planned downtime.
It’s also possible to take predictive maintenance even further with digital twin technologies, for example, or machine learning.
With a digital twin of your machine or production line, you can test different scenarios in the virtual world using real-time data to predict performance and maintenance issues under different conditions.
With machine learning, you can build self-improvement into the predictive maintenance algorithm to further automate and enhance the process while driving even greater efficiencies in the machine maintenance process.
Benefits of Predictive Maintenance
- Eliminate unplanned downtime due to machine or equipment breakdown
- Reduces waste, such as the wasted materials that a breakdown can sometimes create
- Reduces the cost of repairs as breakdowns can often have a knock-on effect on a machine, creating problems other than the original failure
- Extends the useful life of the machine, reducing long-term capital expenditure
- All the above combined leads to improved productivity and increased profits
As with most technologies that come under the Industry 4.0 umbrella, you should take a structured and staged approach to moving to a predictive maintenance model. The technology exists today, though, so you should take your first steps now.
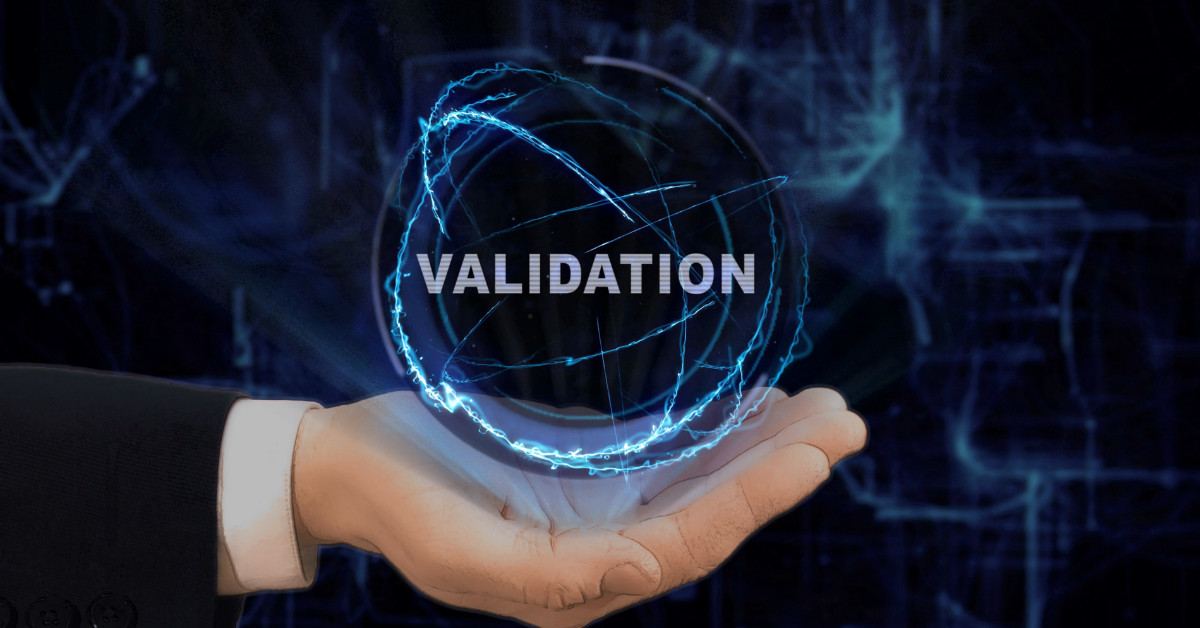
Lean Validation: Why It’s Important and How to Achieve It
Validation impacts many critical aspects of your business from productivity to compliance to patient safety to product quality. It’s not enough, however, to have an effective validation process. To remain competitive and prepare your business for the future, you need an optimised validation process. This means lean validation.
A lean validation approach delivers everything you need from a validation process, but it achieves it as efficiently as possible.
This will save you money over the medium-to-long-term, although lean validation is about much more than this. It’s also about improving and enhancing your manufacturing, quality control, compliance, and product development processes overall.
The Problem with Validation
Validation is about ensuring your facility manufactures products of consistent quality while also providing documented evidence of this quality. It is also about ensuring systems (processes, equipment, machines) perform as per specification at each stage of the manufacturing process. Providing documentary evidence to prove this is also important.
The validation process is essential for product quality, compliance, and patient safety reasons, among others.
However, validation can be a long, drawn out, time-consuming, and inefficient process. This particularly applies when validation processes and systems are paper-based.
That said, validation can also be inefficient when all or part of the process is digitised, including when elements of validation are automated.
When validation is not efficient, your costs increase. It can also take longer to get products to market and it can reduce your competitiveness. It can also cause compliance issues in your business.
The solution is lean validation.
Lean validation makes the process of validating your manufacturing processes as efficient as possible, saving you time and money.
What is Lean Validation?
Lean validation is about eliminating waste at all stages of the validation process. This makes the validation effort more efficient while also achieving your goals as a manufacturer in a highly regulated industry. Those goals include:
- Establishing effective and efficient data collection and document control systems
- Optimising quality and patient safety
- Reducing risk in the manufacturing process
- Ensuring your processes and products comply with regulations
- Ensuring you have documentary evidence that you are in compliance with all regulations
- Reducing waste throughout the manufacturing process
- Exceeding GAMP 5 standards
How to Achieve Lean Validation
Lean validation doesn’t happen by accident. Instead, it requires participation from everyone involved as well as ongoing effort. This includes:
- A strategic, high-level approach to validation where the goal is not just successful validation, but successful validation achieved as efficiently as possible
- Buy-in from all those involved and accepting that, just because things have always been done this way, doesn’t mean they should be done like that in the future.
- A focus on value throughout the validation process, i.e. questioning each step, process, action, or decision and asking if it adds value to the validation effort. The aim is to reduce or eliminate anything that doesn’t add value to the validation process. Examples of this include tests that don’t add value and testing duplication.
Lean Validation in Practice
While each validation project is different, there are a number of best practices that are essential in most lean validation processes. Some examples include:
- Class-based design or class-based programming – using this object-oriented programming approach to software development eliminates duplication, speeds up testing, and reduces the time it takes to develop code
- Equivalency – identifying where equivalence occurs in processes, machines, and equipment to reduce duplication of effort
- Build in quality – building in quality from the beginning will help reduce waste by, for example, creating repeatable validation processes
- Automate – automating as much of the validation process as possible particularly data creation, storage, removal, and retrieval
- Digitise processes – a good example is approval processes as they often present bottlenecks in validation. Digitising approvals will deliver efficiency savings.
- Paperless systems – the use of validated paperless systems to reduce the potential for document loss and/or rework
Adapting and customising any validation process to ensure it meets the needs of your business is essential. However, a lean validation approach should always be central to the effort.
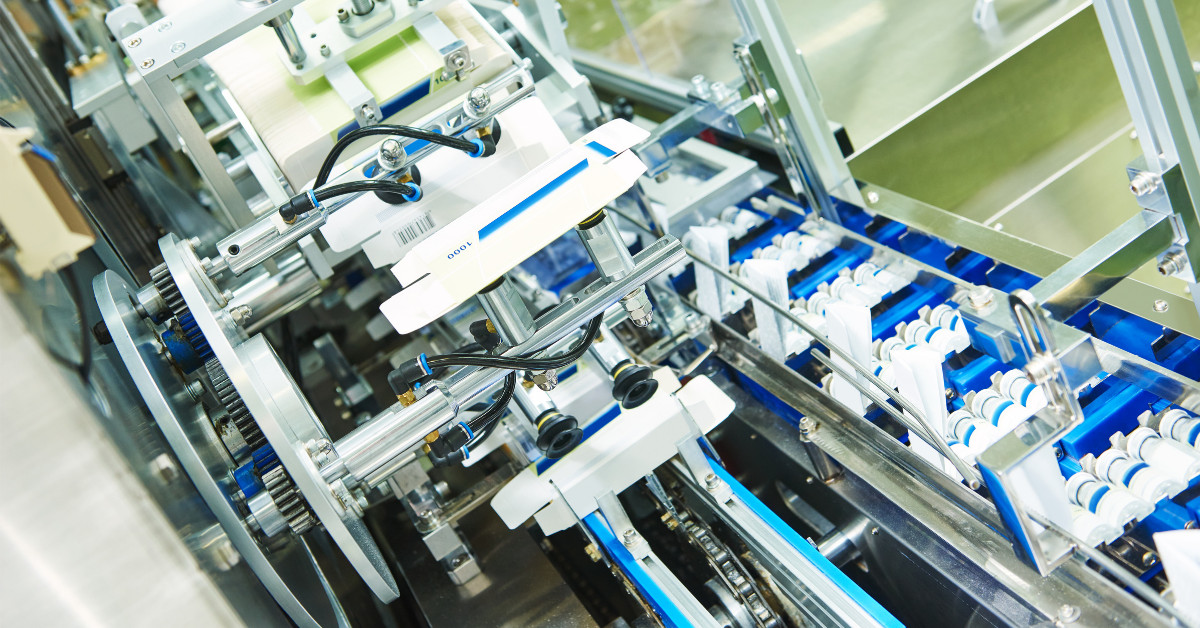
An Introduction to Equipment Systems Engineering
At SL Controls, we work on projects that involve improving OEE and overall productivity in manufacturing businesses. We do this by integrating platforms, equipment, machines, and systems to streamline the production process, enhance automation, improve the use of data, give greater management oversight, make production lines more efficient, and more.
As our clients are primarily pharmaceutical and medical device manufacturers, compliance and quality are also critical components of the services we offer.
Evolving Skillset Requirements
We can deliver our range of services because of the unique set of skills of those on our team.
However, over the years we have seen those skills evolving. As a result, our requirements in the recruitment marketplace have also evolved.
The reasons for this are varied but they include the development of new technologies, increasing demands from the customers of our clients (i.e. the end users/patients of the medical device or pharmaceutical products that our clients manufacture), and the changing regulatory landscape.
The types of engineer we currently employ include:
- Control Systems Engineers
- Automation Engineers
- Validation Engineers
- Software Engineers
As a company, however, we at SL Controls have always looked to the future, anticipating market requirements and the issues we might face to deliver on those requirements.
We also have a significant interest and passion for the engineering sector in Ireland in general. Plus, we are in an ideal position to provide expert analysis of the factors that will influence the industry in the future.
This means we can clearly see the importance of getting more young people engaged with STEM topics and courses. We also need more young people to pursue a career in engineering, particularly young women as they are currently significantly under-represented in our sector.
That said, we believe there is something additional happening. This is the fact engineers working in our industry in the future will need a broader range of skills compared to the traditional disciplines that exist today.
This is demonstrated by the skillset evolution mentioned above that we’ve seen in our own company.
This broader range of skills is encompassed in the role of the Equipment Systems Engineer.
What is an Equipment Systems Engineer?
In our industry, we can already see that putting engineers into discipline silos is no longer effective.
To deliver engineering services to the pharmaceutical and medical devices industries we serve, we need engineers with the following range of engineering knowledge, experience, and skills:
- Control Systems
- Mechanical
- Electrical
- Validation
- Software
Engineers must also have knowledge of Information Technology and Information Systems, including communication, cloud, and networking technologies. They must also have programming skills.
The above is a good summary of the job description of an Equipment Systems Engineer.
The Equipment Systems Engineer
The role of Equipment Systems Engineer is new, but it’s one we are championing here at SL Controls.
I, alongside SL Controls Co-Founder and Chief Technical Officer Shane Loughlin, have established E-Cubers, a not-for-profit industry-backed initiative that brings together all stakeholders, including those in education, to promote Equipment Systems Engineering to young people.
E-Cubers is also about creating and establishing more opportunities for students and engineers to acquire the skills they need to one day become an Equipment Systems Engineer.
Find out more about E-Cubers and the work we are doing by visiting the E-Cubers website.
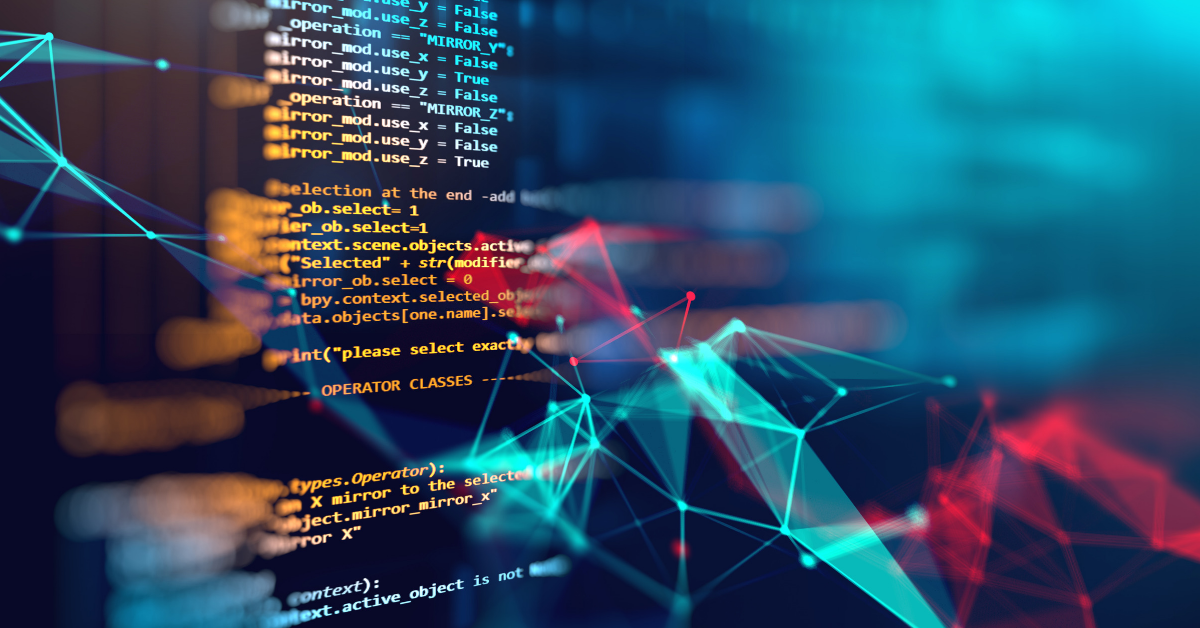
What Is Vendor Neutral and Why It’s Important to Your Manufacturing Facility?
In manufacturing environments, vendor neutrality typically refers to software platforms and solutions that can operate regardless of machine or equipment vendors. The aim of this type of software is usually to improve performance as well as deepening levels of integration on the production line to enhance efficiency and productivity.
Even for software platforms and solutions that are not about integration, vendor neutrality is important as, without it, applications for the software become much more restrictive.
With vendor neutral software development, however, solutions can be applied to whatever machines or equipment you have in your production environment.
Vendor neutrality also makes it much easier to integrate not just machines, but units in the business other than production lines. For example, integrating production lines with the platforms and systems that manage your supply/distribution chain.
Your Options
When deciding on a solution to enhance and upgrade your production capabilities, you have the choice to go with either a vendor-specific solution or one from a neutral third-party that doesn’t favour any particular vendor.
In many cases, both will deliver on your expectations, although you may have to make additional investments if you go for a vendor-specific solution to ensure all the machines, equipment, and systems in your factory are compatible with it.
In the longer term, however, the inherent restrictions of vendor-specific solutions can cause you problems.
Taking a Longer-Term View
Having vendor neutral software systems and solutions in place is important in your manufacturing facility because you will have much more flexibility to make changes, scale, or upgrade in the future.
This is why SL Controls adopts the vendor neutral approach to developing software. We develop software for manufacturers in the pharmaceutical and medical device industries. As with many other industries, pharma and MedTech advances at a significant rate. There is also a continual push for efficiency savings and productivity gains.
As a result, the companies we serve regularly introduce new products, refine their manufacturing processes to make them more efficient, or make changes to their production facility to ensure it continues to adhere to regulations in Europe, the USA, or in other jurisdictions.
In other words, there is constant flux in the field of play of manufacturing businesses, particularly those like pharmaceutical and medical device manufacturing.
Flexibility and the ability to quickly adapt are, therefore, key to success.
Return on Investment
While vendor neutral software platforms and systems will not make your manufacturing facility more flexible and adaptable on their own, they play an important role.
Crucially, vendor neutral systems make it possible for you to take decisions based entirely on the needs of your business. This is a significantly better position than being forced to take decisions on the purchase and/or use of equipment based on vendor, platform, or system compatibility.
So, while you do have the option of using vendor-specific software solutions, using a vendor neutral software developer will deliver a greater return on investment over the short and long-term, as well as helping you achieve your objectives.
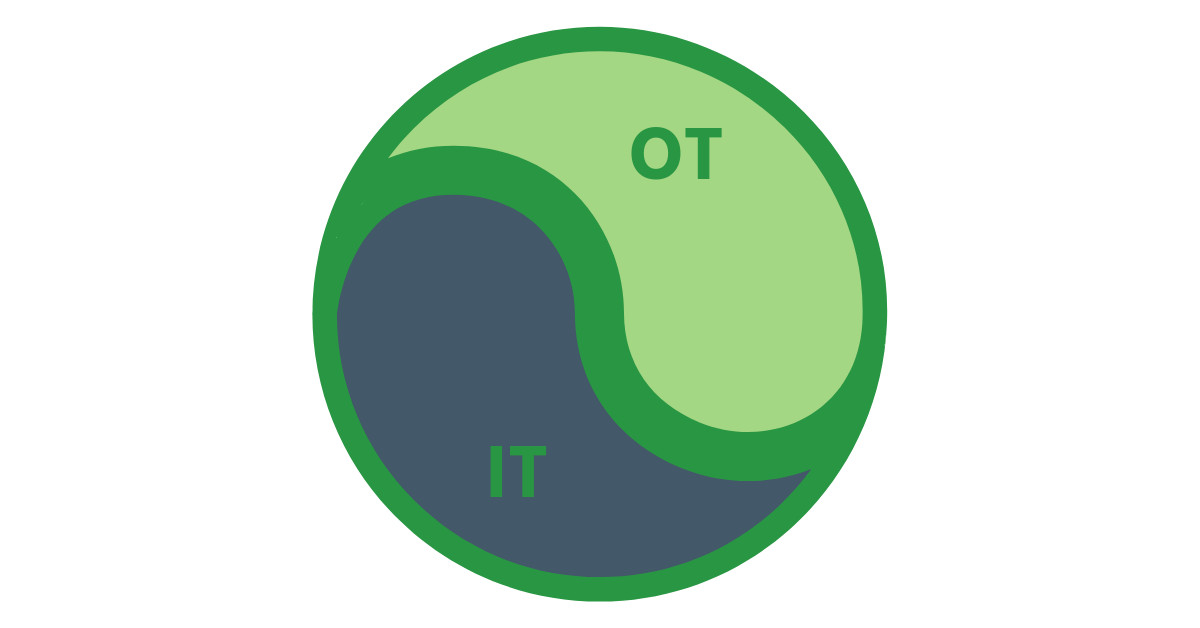
The Convergence of IT and OT – Giving You a Competitive Edge
One of the most important changes occurring in manufacturing at the moment is the convergence of IT and OT. This needs to be not only on your radar, but part of your current plans for improving your business today and helping you stay competitive in the future.
In most manufacturing businesses, there are two types of technology infrastructure. The first is technology that comes under the heading IT – Information Technology. The second type of technology in modern manufacturing businesses is OT – Operational Technology.
New solutions, new approaches to the use of technology in manufacturing environments, and innovative ways of thinking now make it possible for IT and OT to converge.
The benefits of IT and OT convergence are varied, but they combine to give you a competitive edge by making your business more productive, efficient, flexible, agile, and profitable.
IT Defined
IT supports the business functions of manufacturing businesses. Those functions include:
- Sales and customer relationship management
- Customer service, including end-user customer service
- Accounting
- Purchasing
- Human resources
In terms of the technology involved, IT covers all computer, server, networking, and storage devices that create, secure, process, and transmit data to support the above business units and functions.
OT Defined
OT covers technology used in the production process to control and monitor machines and equipment. Examples include:
- SCADA systems
- PLCs
- Sensors
- Meters
- Remote terminal units
The Traditional State of IT and OT
Networking and internet connectivity are often not a part of OT. Sometimes this is because vendors of machines or equipment don’t include networking functionality, or else it’s included but not utilised.
In other situations, production line machines and equipment are deliberately air-gapped for security reasons, although this is an outdated and often ineffective approach to security.
Whatever the reason for the lack of integration between IT and OT, it typically leads to machines in production environments using closed protocols that are often proprietary to vendors.
All this combined means IT and OT often exist in their own silos, with little or no interconnectivity.
However, integration across platforms, systems, and machines is now possible with modern technology.
This is the convergence of IT and OT.
Technologies Making IT/OT Convergence Possible
- Sensors
- Controls, automation, and validation software programmes
- Robotics technologies, including cobots
- Cloud technologies
- SSL encryption and other security technologies
- Improved broadband and mobile internet speeds
- Wireless technologies that are capable of operating in a production environment
- Data analytics and the use of data dashboards
- Digital twin technologies
- Big data technologies
- Machine learning and AI
The above technologies all come under the umbrella of Industry 4.0.
Benefits of IT and OT Convergence
- Efficiency savings – both in manufacturing and in wider business operations
- Productivity – through predictive maintenance capabilities, faster batch changeovers, real-time decision making, automated decision making, and improved OEE
- Better business oversight – as engineers and senior management get access to more information and higher quality data
- Improved product quality – through technologies like digital twins in addition to the improved linkage between customers using products in the real-world and the processes of product development, manufacturing, and quality control
- Enhanced customer service – customer service staff can provide faster resolutions to problems in addition to the fact that manufacturing lines experience fewer production delays. The convergence of IT and OT also enables the mass customisation and/or personalisation of products, while linking production and business processes makes it possible to better manage market demand.
Challenges of IT and OT Convergence
Of course, converging IT and OT in your manufacturing facility is not a simple process, and it’s unlikely to be a revolutionary event. There will also be challenges including:
- Compatibility issues with new and legacy systems
- Integrating systems from different vendors with different platforms
- Security issues
- Buy-in across the organisation
- The upfront investment required
With the right expertise, it is possible to overcome the above challenges to build the systems and infrastructure that will evolve your entire operation, converging IT and OT.
Opportunities Presented by IT and OT Convergence
Some of the opportunities of converging IT and OT have been highlighted above, with most of them coming under the heading of digital transformation.
This means going beyond digitising selected processes in your business to digitalising the entire business.
This is what will give you a competitive edge.
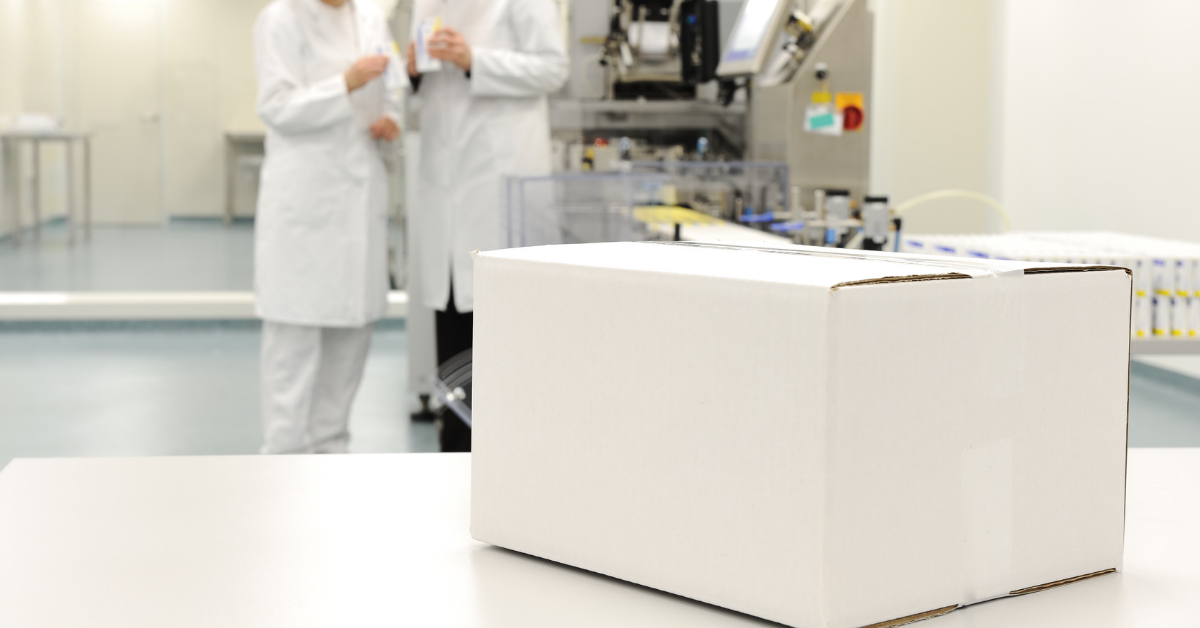
What is Aggregation in Serialisation and Why Is It Important?
As a pharmaceutical or medical device manufacturer, serialisation has probably been a key focus for your business for some time now. What about aggregation in serialisation, though? What are the legal requirements? What are the business benefits of aggregation, and will it deliver a return on investment?
What is Aggregation?
Aggregation can be a part of the serialisation solution on your production lines. Serialisation involves adding a unique identifier to each product at individual pack level, i.e. at the level patients or customers receive the product.
However, those individual pack-level products do not get from the production line to the patient/customer through the distribution chain as an individual pack-level product. Instead, multiple individual pack level products are packed in cases and then multiple cases are packed on pallets.
An aggregation solution adds codes to the outside of cases and pallets to identify the individual pack-level products inside. In other words, aggregation builds parent-child relationships from pallet to case to individual pack-level products.
This makes it possible to find out what is inside a case or pallet by scanning the code on the outside, i.e. you don’t need to open the case to get the serial number of each individual pack-level product.
Is Aggregation a Requirement Under the EU’s Falsified Medicines Directive?
Aggregation is not required under the EU’s Falsified Medicines Directive (FMD).
Instead, FMD focuses on the unique identifiers of products at individual pack-level:
- All products must have a unique identifier
- All unique identifiers must be uploaded to the European Medicines Verification System
- Products must be verified using their unique identifiers at various points in the distribution chain
Technically and legally, you can achieve this without aggregation.
If It’s Not a Legal Requirement, Why Implement Aggregation?
Even though aggregation is not required under FMD, many manufacturers are choosing to implement serialisation solutions that include it. This is primarily because aggregation helps make the distribution chain as well as stock level management more efficient.
This particularly applies if you use third-party logistics providers, but aggregation can offer benefits even if you don’t.
For example, without an aggregation solution, it would be difficult to find out the quantity of stock from a batch that is at different points in the distribution chain, i.e. the quantity of products from the batch at the packaging location, the quantity still at the third-party logistics provider’s warehouse, and the quantity that has already entered the supply chain.
Without aggregation, the only way to identify individual products in cases and/or pallets in each of these three locations would be to open the cases/pallets. An aggregation solution, however, will give you this information with a quick and simple scan of the barcode on a case or pallet.
Should You Implement Aggregation in Your Business
Aggregation will benefit your business, but it is also of significant benefit to others in your distribution chain, including third-party logistics providers and distributors. In fact, while you will benefit, aggregation is arguably more beneficial to those others in your distribution chain.
You then need to consider the fact that aggregation adds complexity to your serialisation solution, which increases the cost.
This requires a cost-benefit analysis specific to the needs of your business. Even if you choose not to implement aggregation, however, the one thing you should not do is ignore it.
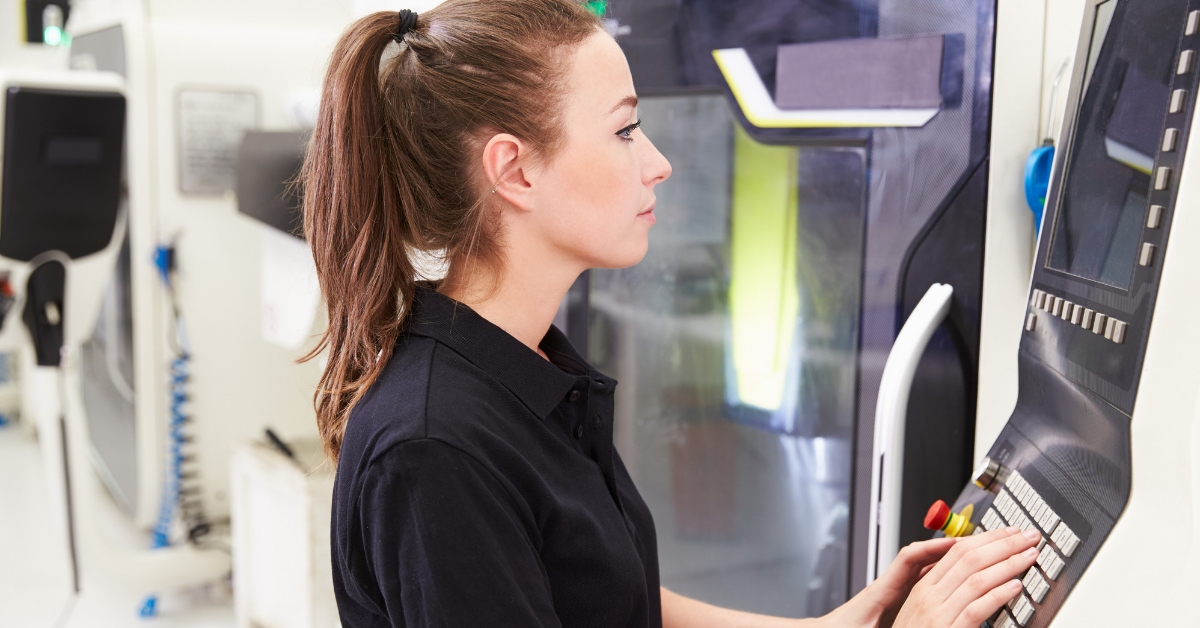
Why Ireland Needs More Women in Engineering
Ireland needs more engineers today, with most people predicting this demand will go on long into the future. Therefore, there is a skills shortage that must be overcome and women are likely to be a key part of the solution.
Just how bad is the skills shortage problem, though?
The Skills Shortage
Let’s look first at how industries that require engineers are growing. According to Engineers Ireland, companies in Ireland will recruit as many as 6,000 new engineers during 2019.
Let’s put this figure in context – there are only about 3,000 college graduates each year entering the workforce with engineering degrees and qualifications.
Understandably, companies need an immediate fix to this problem. Those fixes include upskilling and reskilling existing employees. Another solution is to recruit engineers from other countries or entice Irish expat engineers to return home.
The Gender Gap
According to an Engineers Ireland survey conducted last year, 12 percent of engineering professionals in the industry are female while females make up just 16 percent of engineering graduates. This gender gap is particularly acute in sectors like manufacturing.
Having this gender gap isn’t just bad because of the engineering skills shortage in Ireland – it’s also bad for companies. Research has found that companies that have a gender balance that reflects wider society are more productive and profitable. Therefore, it’s good for companies to recruit more female engineers.
What Can Be Done
We all need to promote engineering as a career for women. This includes explaining the reality of working as an engineer to young female students – from primary through to TY students.
At SL Controls, we work with companies in the pharmaceutical and medical device manufacturing sectors. As a result, our engineers help these companies develop and manufacture medicines and devices that save lives, more effectively treat medical conditions, and improve health outcomes for patients all over the world.
Like other engineering careers, the skills required to work on these projects are broad ranging. Technical skills are necessary in addition to a range of other skills including:
- Problem-solving abilities
- Creativity and the ability to think outside the box
- Communication and teamwork skills
- Leadership skills
- And more
This is the sort of information young people should be aware of in addition to understanding the career prospects and opportunities that exist when you become an engineer. When they have this information, they can make an informed decision about which area of study to pursue.
Good Work
There is a lot of work in this area that is already ongoing, i.e. promoting engineering as a career to young people generally and to girls and young people more specifically.
The STEPS programme is one example. It gets its funding from the Department of Education and Skills and the Science Foundation Ireland. It’s an outreach programme that encourages primary and secondary school children to consider a career in engineering.
The I WISH initiative is another example. It focuses on young female students and encourages them to consider engineering as their future career. It organises conferences, workshops, and campus weeks at colleges across the country.
Then there is E-Cubers, an initiative that SL Controls is heavily involved with. One of E-Cubers main aims is to promote a new and emerging engineering discipline to students at all levels of education, from primary school students to postgraduates. That discipline is Equipment Systems Engineer, a role which will become increasingly important in the coming years and decades.
This push to get more young people, particularly women, to study and pursue a career in engineering must continue. More needs to be done, though.
Ireland needs more engineers and women are underrepresented in the sector – it’s an opportunity too good to miss.
« Previous 1 … 11 12 13 14 15 … 18 Next »