Blog

What is Serialisation?
Serialisation is an important topic in manufacturing, especially in industries like pharmaceutical manufacturing. What is serialisation, though, and why is it important?
Serialisation involves adding unique serial numbers to products during the manufacturing process. Those serial numbers must be globally recognised so the product can be tracked and traced and/or identified anywhere in the world. Part of the process of serialisation involves applying the unique serial number to the packaging of the product in the form of a 2D or 3D barcode.
Different Types of Serialisation
There are different types or levels of serialisation, depending on the product. Broadly speaking, they fall into three categories:
- Product type serialisation – this applies to goods that have a long shelf life so don’t require the identification of individual units.
- Batch serialisation – this is for products where it is important to identify the product type as well as the manufacturing batch. This applies to perishable consumer goods as well as regulated products. Pharmaceuticals are an example of the latter.
- Unit serialisation – this is where it is important to identify the individual product unit as well as its manufacturing batch and other information.
The unit or batch element of a unique serial number separates products into different manufacturing runs or individual product units. The primary purpose of doing this is to prevent fraud, especially in the pharmaceutical industry. After all, chemically synthesizing drugs to create fraudulent versions is increasingly common. Counterfeit drugs are difficult to track, however, not least because the different elements (the drug itself, the packaging, etc) may be manufactured in different countries.
Serialisation helps to combat counterfeit pharmaceutical products as well as products in other industries.
The Technology
In the past, unit serialisation only existed on high-priced items. Cars are a good example. Modern regulations require a more widespread implementation of serialisation, particularly in industries like pharmaceuticals. New technologies make this not only possible but also affordable.
By the end of 2018, serialisation regulations will cover 75 percent of the prescription medications produced around the world.
While the technology is available, serialisation requires substantial integration of systems in production facilities, particularly in relation to unit and batch serialisation. This integration includes software systems at all levels, printer technologies, tagging technologies, production machines, and readers. Regulations also require the proper storage, management, and reporting of serialisation data.
As a result, serialisation in the pharmaceutical industry is not simply about adding a unique serial number to the products you manufacture. It does involve this, but it also involves generating data that identifies individual products. It also involves storing and managing that data, making it easy to access, often many years after the product leaves the manufacturing line.
Benefits of Serialisation
As mentioned above, one of the primary objectives of serialisation is to prevent fraud. This offers benefits to everyone in society:
- Protects patients from potentially dangerous counterfeit medication
- Protects the business interests of those in the pharmaceutical industry
- Mitigates lost tax revenues for governments
Preventing fraud is not the only advantage of serialisation, however. Here are some other important benefits:
- Enables you to match an individual product to the batch in which it was produced to help you understand issues, improve the service you offer customers, and enhance business performance
- Enables the tracking of products through the entire distribution process, from the manufacturing line to a pharmacist dispensing the medication to an individual
- Helps with the investigation of problems as an individual product can be traced back to its batch on the production line
- Assists in product recall situations
- Enables additional control over products and batches such as, for example, associating an expiry date to the unique serial number of a batch
Serialisation is now a fact of doing business for many industries, including pharmaceutical manufacturing. Ensuring your systems and processes are sufficiently capable is, therefore, essential.
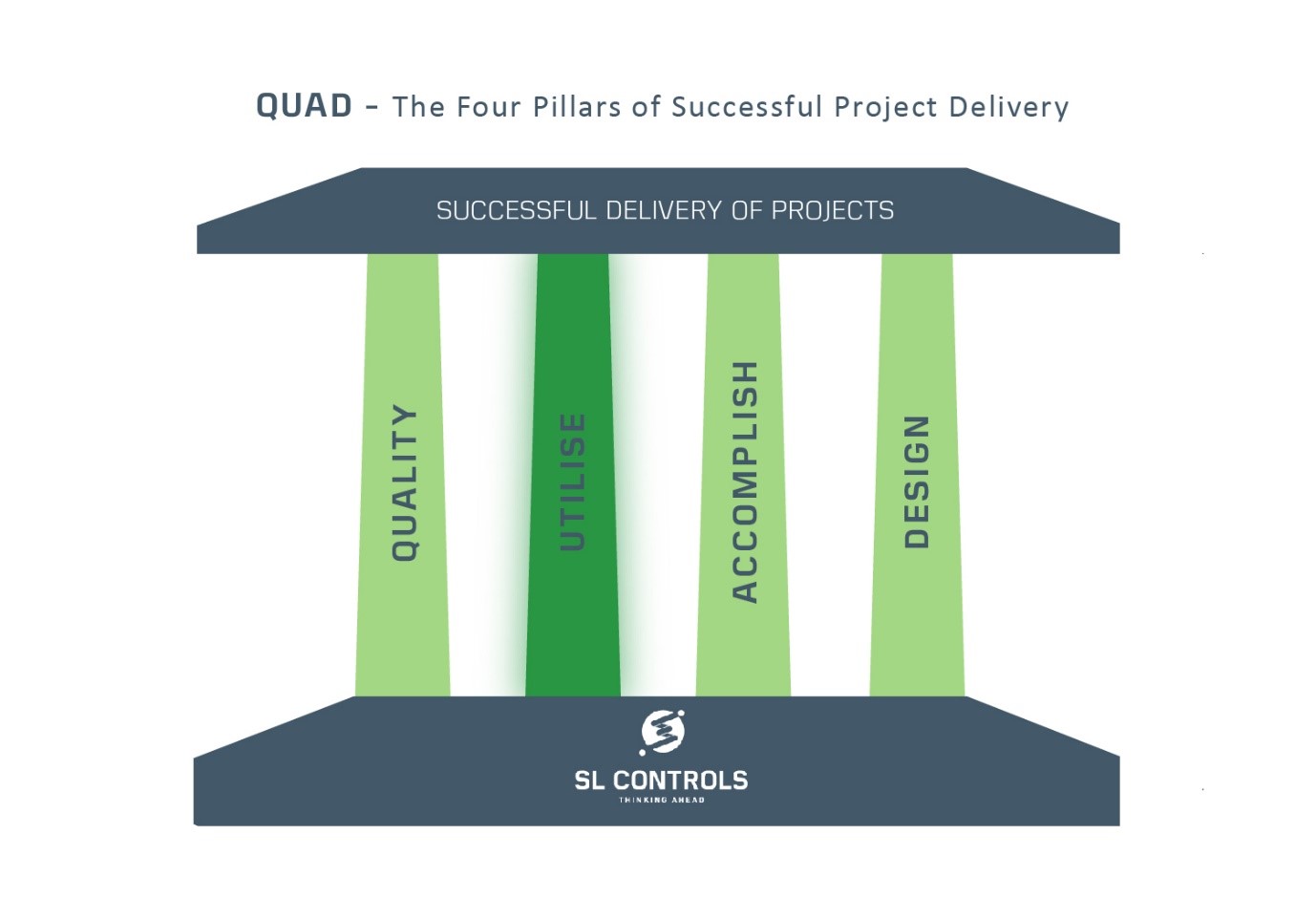
Utilise – Enabling a Successful Project
SL Controls uses an approach it calls QUAD for the successful delivery of projects. This approach applies specifically in our field of controls and automation, but it can be applied to other software projects as well. QUAD stands for Quality, Utilise, Accomplish, and Design. Each of these elements is a pillar on which you should build a successful project.
In the previous blog in this series, we explored the Quality pillar. This blog will look at the Utilise pillar – Enabling a Successful Project.
The Utilise Pillar Explained
This part of delivering a successful project involves ensuring you have the right team in place. The team makes the delivery of the project possible which is why we call this pillar the enabler. In addition, getting the right resources and having them available at the right time is what makes the project successful.
There are four main elements to making this happen:
- Resource Acquisition
- Resource Retention
- Resource Upskilling
- Resource Allocation
Below we’ll explore best practices for each of these elements.
Resource Acquisition
The starting point is to acquire the right resources required for the project. This involves having a comprehensive HR strategy in the company and usually means having ongoing recruitment initiatives. After all, if you’re trying to recruit resources as a project is about to start, it’s probably too late. You need the team already in place which requires continuous recruitment drives.
This can take many forms: job boards, social media campaigns, recruitment agencies, and more. It’s also a good approach to have a strong connection with local colleges. At SL Controls, for example, we have a close relationship with the University of Limerick, the Limerick Institute of Technology, and other colleges close to our offices around the country. We regularly do presentations to students and employee graduates from these colleges.
The other crucial element you need in place to have a proper resource acquisition strategy is the package you offer. This includes salary as well as other benefits. When you structure this right, you can attract the best talent in the market. Using SL Controls as an example again, applicants often choose roles with us over multinationals because of the packages we offer.
Resource Retention
It’s as important to have a comprehensive resource retention strategy as it is to have an acquisition strategy. After all, it’s much more expensive to recruit and train someone new than it is to keep the people you have.
Again, this involves salary, but staff usually have varied reasons for wanting to work at particular companies. Getting the right work-life balance is often very high on the priority list.
There are varied strategies you can use to give employees a good work-life balance. One of the things we’ve done at SL Controls is to operate from regional offices. This means employees can live and work where the projects are rather than travelling long-distances. It also gives our team opportunities for career expansion without having to relocate.
We also have other initiatives such as Live Well at SL and Think Well at SL which promote physical and mental health and wellbeing. Plus, we offer defined career paths so staff know exactly what they need to do to progress their careers within the company.
Initiatives like these and others help improve staff retention rates.
The nature of the projects you offer employees is also important, i.e. ambitious engineers are more likely to stay with you if they get the opportunity to work on varied projects. At SL Controls, for example, we are vendor neutral. As a result, our engineers are constantly learning, extending their experience and staying at the top of the technology knowledge tree.
Resource Upskilling
For projects to be successful, you need to make sure your team has the necessary skills. This can be an ongoing process where you encourage people to pursue additional academic qualifications. It can also include identifying specific training courses that members of the team can complete to get the skills they need for the project.
Knowledge transfer initiatives are also important in engineering and programming teams. This solves the problem of one person having lots of knowledge of a particular area while other members of the team don’t. This situation pigeonholes the employee with the knowledge plus it creates difficulties if that person decides to leave.
With knowledge transfer initiatives, each person has a responsibility for passing on the knowledge they have to other members of the team. At SL Controls, we have a process for achieving this where the person with the knowledge prepares material for the rest of the team. This could be a presentation, training course, or article.
We find this delivers additional benefits – improving the soft skills of the team, i.e. doing a knowledge transfer presentation helps to improve presentation and training skills.
Resource Allocation
Finally, you need to use the right resources for specific tasks with the objective of getting the job done. This involves setting up the full team from the outset, scheduling the resources properly, and ensuring the resources are used effectively and efficiently. The latter involves spreading the load to avoid situations where an individual is solely responsible for a particular aspect of the project whether that is design, validation, technical, or anything else.
Benefits
Following this resource utilisation strategy brings several benefits to your project:
- Reduces lead times – as teams are already in place
- Reduces the costs associated with losing resources – as recruiting new talent is time-consuming and expensive
- Ensures there is no disruption to projects because of lost resources – because it takes time to replace a resource
- Resource continuity – clients can see the same resource on their projects
- Retains knowledge in the business – through the knowledge transfer initiatives
- Makes the project as efficient as possible from start to finish – ensuring it is delivered on-time and on-schedule
The Other Pillars of the QUAD Structure
We describe the QUAD structure using pillars because each element is equally important to the successful delivery of a project. In the next article, we will look at the Accomplish pillar.
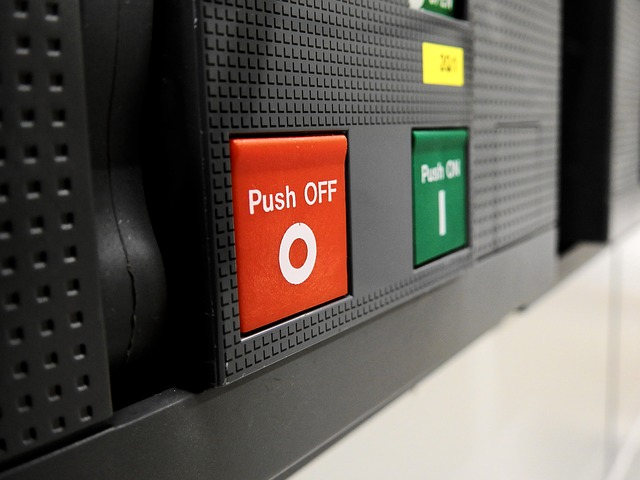
The Importance of a Controlled Christmas Shutdown
It’s Christmas and everyone is looking forward to the time off. All that’s left to do is to switch off all the equipment on the line, turn the lights off, and head home. How you do this, however, will have a major impact on what happens when you start up again in January.
If you don’t shut down your line and all the supporting systems above it properly and in sequence before the break for Christmas, the first shift back in January will face significant issues. In fact, you could lose 20 to 40 percent of your first shift in January because of start-up problems. These are easily avoidable with some forward thinking.
Generating Christmas Errors
Properly shutting down your production line, particularly automated systems, before you break for Christmas involves taking into consideration level two and level three systems as well as level one systems.
These higher-level systems are invisible when you have your hand on the machine isolator. These systems are usually hosted outside the manufacturing space and are involved with processing batch data, equipment access control, machine parameters, machine utilisation data, process data, etc. Even though they are outside the manufacturing space, it is essential you consider them in relation to their status of operation when they don’t have a connected machine controller for the holidays.
An example is the data connection between a batch control system in the MES layer and the equipment, the system that monitors the batch integrity of your line. By not taking this data connection into account, the system remains in an unknown state over the Christmas period. In other words, it won’t be able to confirm the status of the production equipment, so will still expect the same data. This can generate ever growing connection and error logs.
These are errors and connection issues that you will need to resolve before you can get production back up and running again. This takes time and needs to be done before you get the system back to a position where you are ready to download, line clear, and process the next batch number. That means lost productivity and, potentially, additional expense.
Controlling the Christmas Shutdown
The solution is to plan the Christmas shutdown looking at all layers of the organisation. This involves understanding how different pieces of equipment and systems interact. In other words, what happens to A and B when I switch off C?
Once you understand how everything interacts, you can produce a shutdown sequence to follow on the last day of operation before the break. Following this to the letter will turn off the equipment and higher level systems in a way that doesn’t generate errors or unnecessary notifications.
You should also produce a January start-up sequence to switch on all systems and equipment again in the right order, i.e. to ensure there are no problems starting a particular piece of equipment or software system before another one.
Preparation is Better than Resolving After the Fact
It is possible to resolve issues that occur because of incorrect shutdown or start-up sequencing. In fact, we help clients with these problems every year. That said, it’s not the best option as it’s cheaper and more productive to plan the shutdown and start-up sequence in advance.
When our team prepares a controlled Christmas shutdown and start-up plan, we do the following:
- Evaluate the system and identify all the interacting systems at the different levels.
- Develop an architectural model to determine the correct shutdown and start-up sequences
- Recommend the shutdown and start-up sequences to ensure the restart in January happens as quickly and smoothly as possible.
In addition, we often provide remote support through monitoring software where our engineers check all levels of automation, from machines to servers, during the shutdown and start-up processes. For some clients, we also provide engineers on-site.
Whatever way you choose to develop a Christmas shutdown and start-up plan, make sure you do it sooner rather than later. Integrated and automated systems provide benefits when they are operational but headaches when they are not stopped and started in the right sequence. A small amount of planning now avoids these problems.
To find out more about how SL Controls can help with your Christmas shutdown or start-up planning, please email us at [email protected].
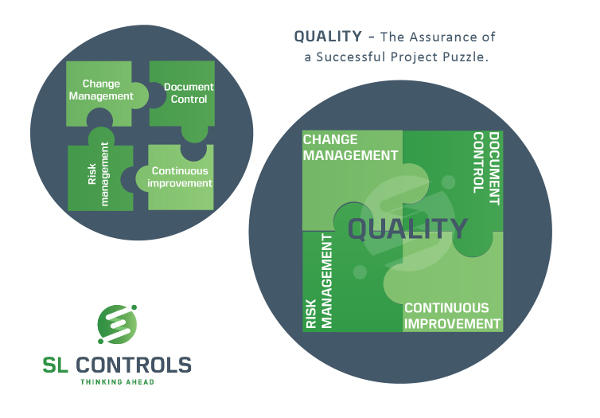
Quality – The Assurance of a Successful Project
In the previous blog in this series, we outlined the four pillars of successful project delivery – QUAD. These pillars ensure major software projects, such as system automation and system control projects, meet expectations, complete on schedule and stay within budget. To recap, the four pillars are:
- Quality – the assurance of a successful project
- Utilise – enabling a successful project
- Accomplish – executing a successful project
- Design – the pre-requisite of successful projects
This blog focuses on one of those pillars: Quality, the assurance of a successful project.
Explaining the Quality Pillar
Quality strategies and actions taken throughout the entire project are crucial to its success. This begins at the requirements stage and continues through design, coding, testing, implementation and maintenance.
Also, at SL Controls, quality strategies and actions mean delivering projects in accordance with our ISO accredited QMS system.
From a client perspective, this results in expectations being met including functionality, performance, budget, and timeframe expectations.
Practical Steps
The practical quality steps required to deliver a successful project can be split into four broad areas:
- Change management
- Risk management
- Document control
- Continuous improvement
Let’s look at each element in more detail.
Change Management
Every software project you initiate will involve change control and management. As a result, change control and management should be an umbrella over every project.
Change management begins by identifying the impact on controlled items such as documentation, application software, operating software, firmware, hardware and configuration data associated with the project. This is one of the first things that should be done. Once you identify the impact to the controlled items, you can then make decisions on what you need to do from a quality perspective. This can include risk assessments, design, testing, deciding on the suite of documentation you will require, etc.
The change control process then tracks all this through to the completion of the project – right through to sign-off of all elements.
Risk Management
All Automation systems and control projects should take a risk-based approach. In fact, all software projects should have a risk-based approach. This means carrying out risk assessments on any and all aspects of the project.
Risk management on a project begins with an initial risk assessment. The purpose of this risk assessment is to determine the overall impact that the software may have on patient safety, product quality and data integrity. This risk assessment is typically followed by a functional risk assessment which involves calling out each function and then assessing the risk. It also includes safety risk assessments which involve employee, contractor, and, often, patient/customer safety. It is also important to do project and logistical risk assessments looking at time overruns, budget overruns, and other operational issues.
With each risk assessment, it is important to clearly identify the risk, understand how to mitigate the risk, and decide on the level of testing required.
Document Control
This part of the quality process covers document control and source code control, particularly version control of all code. For example, taking the existing code from a machine and then capturing, documenting, and controlling all updates to that code throughout the project. The same applies to other documents created during the project including design documents, test plans and more.
Good document control speeds up the error correction process and ensures full traceability. Full version management should continue until live implementation of the code and completion of the project.
Continuous Improvement
This is a central part of the SL Controls’ ethos and is crucial to successful project delivery. It is also part of our QMS systems. Improvements to our QMS are typically driven through outputs from other critical internal processes such as customer complaints, internal and external audits, customer feedback and non-conformances.
Typically, improvements are handled within the critical processes where they are raised, however, improvements that require medium to longer term fixes are generally transferred to our CAPA process. Under the CAPA process, a full investigation of the issue is carried out before identifying and implementing a long-term corrective action to ensure the same issue doesn’t happen again on this or any future project.
Benefits of Focusing on Quality
There are several benefits to adopting an approach that puts quality at the core of successful project delivery, rather than considering it as an add-on:
- Delivers expectations – the project will be completed successfully and will meet your objectives.
- Ensures constant improvement – the formal process of continuous improvement ensures you benefit from the collective learning of SL Controls’ engineers on multiple projects.
- On-time and on-budget – effective quality strategies and actions ensure delivery on these important goals.
- Saves you time – you will spend less management time dealing with issues in a project when it has a major focus on quality. In addition, you will avoid potential lost revenues through product recalls and associated reputational damage, equipment downtime, and more.
- Increased confidence in the solution – a focus on quality throughout the project ensures it runs smoothly and delivers what you expect, increasing your confidence in the solution.
The Q Pillar of the QUAD Structure
The QUAD approach to successful project delivery includes the principle that each of the four pillars is equally important. This demonstrates the importance of quality in all systems automation and control projects.
In upcoming articles, we will explore the remaining three pillars – utilise, accomplish, and design.
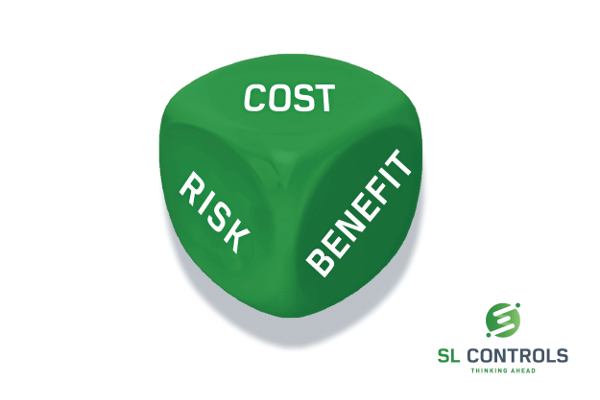
How to Justify Early Extra Investment to Reduce Late Budget Overruns
Software projects that result in late budget overruns are never welcome. As a result, most companies take steps to keep tight control on costs, particularly in the early stages of a project. Therefore, the last thing they want to see is a big invoice during the initial scoping and design stages, i.e. before coding even begins, let alone testing.
Providing extra investment in a project’s early stages, however, is the best way to reduce late budget overruns. Specifically, early investment in the requirements and design stages helps to identify potential defects and remove them from the system as early as possible.
This approach is exponentially cheaper than finding and fixing bugs at a later stage in the project.
The Cost of Software Defects
Well-known research backs up this approach, particularly research by Barry Boehm of the University of Southern California and Victor R. Basili of the University of Maryland. Their research confirms what we have seen at SL Controls in numerous projects.
In particular, the Boehm and Basili research describes how the cost of fixing a defect is up to 100 times more expensive at the end of a project (the maintenance phase) compared to fixing a defect at the start (the requirements phase). In addition, the cost of fixing a defect increases through each stage of the project. The cost increases considerably after the main coding stage.
Source: B. Boehm and V. Basili, Software Defect Reduction Top 10 List, IEEE Computer, IEEE Computer Society, Vol. 34, No. 1, January 2001, pp. 135-137
The general principles related to the cost of defects are as follows:
- The longer a defect remains in a project, the more damage it does as it will have a broader impact than a defect introduced at a late stage
- The longer a defect remains in a project, the costlier it is to fix
- Spending more time and resources in the requirements and design stages of a project will identify defects early and, importantly, will help to prevent defects from entering the project further down the line
- All defects identified late will be costlier to fix
In addition:
- Software projects spend up to 50 percent of their resources on avoidable rework
- 20 percent of defects account for 80 percent of avoidable rework
The solution is to find and address defects in the requirements and design stages. After all, it will always be cheaper and more efficient to avoid putting defects into the code in the first place than it is to find and remove them at a later date.
The SL Controls Experience
We have referenced below one example of a project we were involved in where several decisions were made in the early stages that led to significant difficulties at the latter stages of the project. At their core was a failure to take a controls and data-focused approach with clearly defined Critical to Quality (CTQ) parameters.
This led to a situation where several requirements of the project were not met. Crucially, these defects were not discovered until the Site Acceptance Testing (SAT) stage of the project. It should be noted there was no Functional Acceptance Testing (FAT) at the OEM site for scheduling reasons which resulted in the defects being uncovered later in the testing phase.
The late discovery of the defects resulted in the project going over budget and over schedule.
Of course, the situation could have been worse if production went live with critical software defects. The budget overruns were, however, significant.
We ran calculations showing this budget overrun could have been almost completely eliminated if the defects were found and corrected at the requirements and design stages of the project. It is likely the project would also have completed on schedule which would have saved the company even more.
Focus on the Early Stages
In summary, the best way to avoid budget overruns in software projects is to focus on identifying risks and defining CTQs in the requirements and design stages. This preventative approach is considerably less expensive than a corrective one that relies on the coding and testing stages to identify and remove defects.
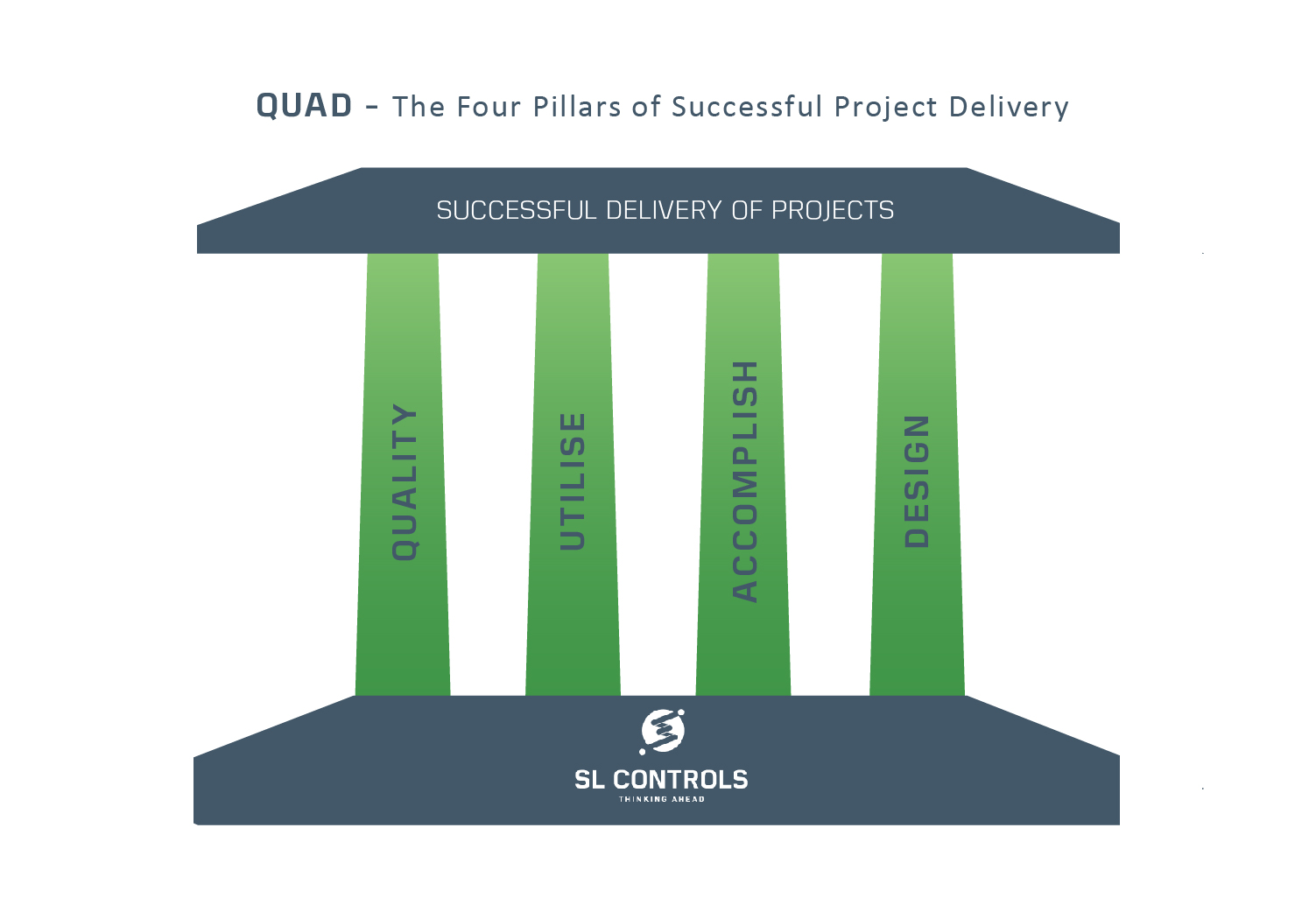
The Four Pillars of Successful Project Delivery – QUAD
Successful projects don’t happen by chance. They need careful planning, proactive management, proven quality control measures, effective design, proper resourcing, and more. At SL Controls, we use an approach to deliver projects that we call QUAD. It is implemented on all systems integration projects. It involves building each project on four essential pillars of success:
- Q – Quality
- U – Utilise
- A – Accomplish
- D – Design
The pillared structure of the approach is key to its success. It is not linear where one element follows another. Instead, each of the four pillars is equally important and is crucial at all stages of project delivery.
Without a focus on each of the four pillars, one or more might crumble or buckle putting the whole structure – or project – at risk.
What is QUAD?
To make QUAD work when delivering a project, it is essential to have good communication with all individuals and teams involved, both internal and external. Effective collaboration is essential.
The QUAD project delivery structure includes the following elements:
- Quality – the assurance of a successful project. This element is delivered in accordance with our Quality Management System (QMS) where we implement a peer reviewed risk-based approach. This is supported by critical internal processes such as change management, document control, training, and risk management. These supporting processes are paramount to ensuring our projects are delivered to the highest possible standards.
- Utilise – this is the enabling element of a successful project. Much of this part of the delivery involves the utilisation of the existing team through upskilling and, where necessary, recruiting new members. In addition, staff retention initiatives are incredibly important to maintain resource continuity.
- Accomplish – this is the execution pillar where the focus is on engineering the project to a successful conclusion. As this is the doing element of the project, Safety is the single most important component. Therefore, it involves the execution of Safety Risk Assessments, Safe Plans of Action, and Method Statements. This pillar is also closely integrated with the design pillar and there is a constant feedback loop.
- Design – this is a pre-requisite of all successful projects. As a result, the bulk of the heavy lifting with this pillar happens in the early stages from the initial scoping work to completing the design. Sticking with the QUAD philosophy, however, the design phase is never truly complete and remains an important pillar of the project for the duration.
As you can see, some of the elements above have a company level perspective as much as a project level perspective. Talent retention is the most obvious example, along with internal team collaboration. In other words, for QUAD to be truly effective, the approach must be accepted and championed by all departments and at all organisational levels.
When this happens, the elements come together to ensure the successful delivery of projects.
Benefits of the QUAD Approach
- Quality – delivers quality throughout all stages of the project to both internal and external standards.
- Flexible and agile – with QUAD, it is possible to quickly and efficiently adapt to changes in a project’s scope. Being flexible and agile also allows you to scale up a project with minimal disruption or complication. This particularly applies when implementing a project by phases or when you start with a pilot.
- On-time delivery – QUAD makes it possible to meet deadlines.
- Deliver on budget – completing projects on budget is another crucial objective of using the QUAD delivery approach.
- Ensure resources are in place when they are needed – many projects stand and fall on the availability of resources. QUAD’s robust, integrated, and dependent structure mitigates this risk.
- Delivers on expectations – as well as delivering projects on time and on budget, QUAD also delivers on other expectations. This includes achieving the project’s expected outcomes and delivering ROI.
Successful Project Delivery
The above is a brief overview of how QUAD helps deliver successful projects. In the coming weeks, we will look at each of the four pillars in more detail, including the challenges faced in each and the strategies used to ensure success.
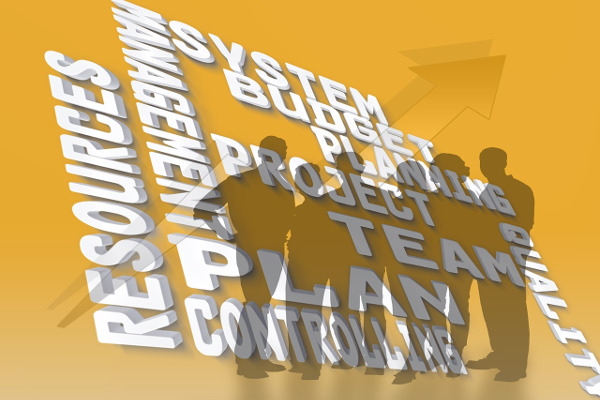
Staying Competitive – 4 Things You Need to Consider in Your 2018 Budget
It’s that time of year again – planning, prioritising, and setting budgets for your plant for the coming year. What are you going to budget for in 2018?
You will, of course, have similar priorities that you always have in your yearly plans and budgets – productivity gains, efficiency savings, capital equipment investment, staffing and recruitment, staff training and upskilling, etc. You may also be allocating additional budget to some current hot topics. Cybersecurity is a good example.
You’re probably coming close to finalising the 2018 budget but before you sign it off completely, here are some things you should consider.
What Should Also Be on Your Agenda in 2018
While all the above are important, there are other things you should consider including in the 2018 plan for your plant. This includes new and developing technologies that will provide a foundation you can build on to help you remain competitive in what is a constantly evolving and often challenging market.
If you haven’t considered the following four topic areas, you should look at them before finalising your budgets and plans for 2018:
- Factory 4.0
- Compliance and serialisation
- Computer systems validation
- Data analytics
Let’s look at each in more detail.
Factory 4.0 – the Birth of a Revolution
Factory 4.0 (or industry 4.0) is gaining a reputation as being a buzzword. It is more than a concept for the future, though. In fact, it’s a commercial reality now so it’s probably not something you can leave until future years.
Where do you start, however? It’s such a huge topic and there is no way you can achieve major change over 2018, right? Of course, but you should start now or you risk falling behind.
A good approach is to conduct a scoping exercise in 2018 regarding factory 4.0. This should look at what the technology and processes will mean for your business while also assessing your existing position in relation to modernising your facilities. Examples include:
- Do you need to buy new equipment?
- What additional expertise and third-party assistance will you need?
- What new software will you need?
- Will your existing systems integrate?
- And more
Once the scoping exercise and assessment are complete, you can measure the expected ROI of factory 4.0 in your plant and start planning for implementation.
Compliance and Serialisation
Depending on your industry and region, serialisation deadlines may affect your business in 2018. You should be some way along the road of getting ready by now. If you are not, however, you will need to allocate more of your 2018 budget to catch up and ensure you meet the deadlines.
Computer Systems Validation
As you know, process validation is always a major priority. Machines are getting smarter, though, and the world is becoming more software driven. In addition, the world’s regulators are starting to shift their attentions more and more towards software validation.
If you haven’t already started investing more of your budget on software validation than you have in the past, it will be beneficial to start in 2018. This will keep you ahead of the curve, it will improve your operations today, and it will ensure you are more equipped for the future.
Data Analytics
Data analytics will improve your business as your team will have more accurate information and less paperwork to deal with. This means they can focus on the data so they can plan more efficiently and identify areas for improvement. In addition, more accurate data will give a better insight into your operations.
Where do you start, though, and what exactly is possible? How can machine A effectively talk to machine B and how can systems built on completely different platforms interact seamlessly, i.e. in a way that benefits your business and doesn’t just cause you more headaches? What will be the real impact on operations, intended and unintended?
These are all valid concerns but the problem with data analytics is not the technology as it exists and is effective. The problem is having the expertise to roll it out.
Therefore, this is what you should look at in 2018. Add to your budget in 2018 a plan to bring in the expertise. Again, this is often best achieved through a third-party specialist. Also, you should look at implementing data analytics on a stage-by-stage basis so you can measure success, analyse the benefits, and ensure the full roll out goes smoothly.
Usually, the best way to start is with a pilot, ideally focusing on a problem area or problem machine in your facility. You can use this pilot to measure ROI and then plan to roll out implementation to your full plant in late 2018 and into 2019.
Moving Your Plant Forward in 2018
Each of the four priorities above is likely to be a part of your thinking when planning and budgeting for many years to come. The time to start is now.
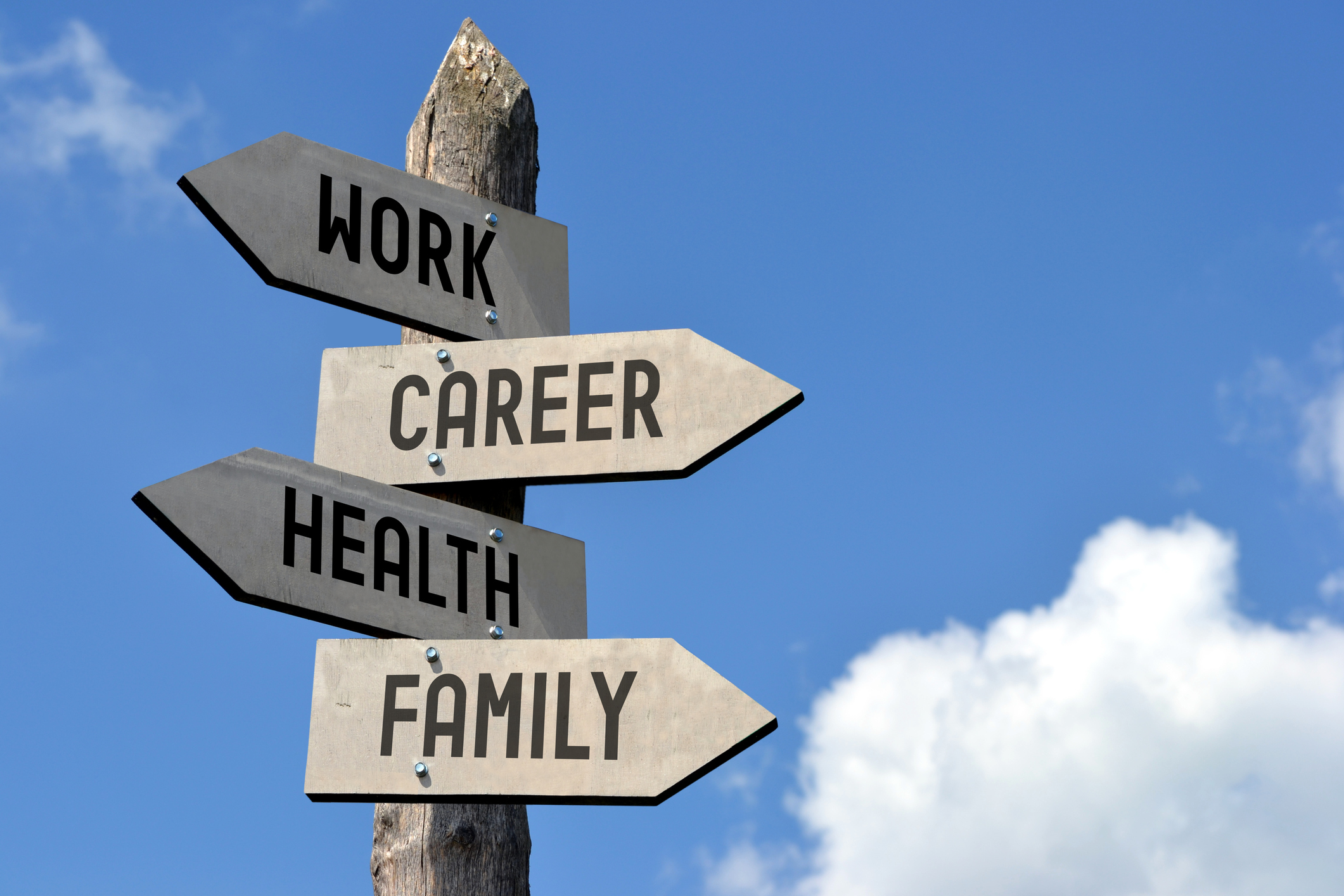
Blog: Valuing and Retaining Contingent Workers
Successfully Managing a Consistent Supply of Contingent Workers
There are a huge number of challenges associated with the successful management of non-permanent contingent workers. The high turnover rate of contingent workers has long been a thorny issue. At SL Controls, we have found a perfect balance and an excellent solution to retaining a contented workforce and, ultimately, satisfied clients.
As both an employer and a supplier of choice for highly skilled engineering staff, we at SL Controls tasked ourselves with seeking an innovative solution to help alleviate the high turnover of contingent workers and ensure a consistently high level of service to our clients. We are pleased to share our hard earned expertise and knowledge.
Implementing a Contingent Workforce Solution
In 2011, SL Controls began supplying contingent workers to a leading healthcare company in the mid-west region of Ireland. Our client needed support for their core permanent workforce. They also needed the flexibility to augment their internal software controls and software validation departments as demand dictated.
Our contingent workforce solution offered them:
- Enhanced flexibility to increase resources during peak project workloads
- Access to a unique and specialised set of skillsets which they did not have requirements for on a permanent basis
The initial deployment of software controls and the accompanying validation engineers was centrally managed from SL Controls’ head office. The identified skillsets required by the client were carefully matched to our existing engineering staff.
The early months of providing this service proved to be very successful with the client acknowledging the valuable contributions and making additional requests for other specialist engineering skillsets in the IT server compliance and MES integration domains. However, over the medium to long-term, some issues emerged.
The Challenge of Retaining High-Quality Staff – Eliminating the High Attrition Rate of Contingent Workers
The consistency of the service underwent a robust test and was not sustainable over the medium to long term. Isolation, both geographically and from the core employer, was identified as an issue.
For example, one of the SL Controls engineers working on the client site in the mid-west had to travel four hours from Donegal on a Sunday evening to work onsite at the client’s premises from Monday through until Friday. The continuous travel combined with being away from family during the working week meant the proper work/life balance could not be achieved. This ultimately resulted in the employee relocating to our head office in Sligo.
This scenario is typical and continues to be experienced by other suppliers of contingent workers to the pharmaceutical and medical devices sectors. Action needed to be taken to ensure that SL Controls employees working onsite for the client had the proper work/life balance while also feeling connected to the local SL Controls office.
The Impact on Clients
The client is also directly impacted when contingent workers are displaced. Clients typically invest upwards of six months in an engineer who then becomes knowledgeable and familiarised with their systems and processes. This time investment is something that cannot be recouped.
The idea of, once again, commencing the search for a replacement engineer is daunting. The loss of skillsets gained through the process of learning and understanding key technologies and tools as part of their daily project duties weighs heavily in terms of time costs.
There are no winners in this type of scenario as the employee seeks to strike the correct work/life balance and the client is left with the situation of having to reinvest in another engineer who may similarly fall victim to the same mitigating circumstances.
The Solution – SL Controls Invests in a Region and Its People
SL Controls invested in becoming a supplier of a highly skilled contingent workforce to address the issues. Having analysed the set of contributing factors, SL Controls took action in 2013 to help construct and underpin a more robust process. Employing locally would be a priority.
Our approach included:
- Establishing a local projects office to service the entire mid-west region. The National Technology Park in Limerick was deemed most suitable.
- Identifying and hiring local software controls and validation engineering talent in the mid-west region.
This approach brought several benefits:
- As permanent staff of SL Controls, this highly skilled workforce experiences better job satisfaction
- As the staff are more satisfied, they are more committed to the company and its ethos
- Employing locally invests in the region and the community
- Employees feel they are an integral part of the company
- Employees feel they have identified career paths
This pride and ownership helps to remove the temptation for employees to engage with head hunters.
The Result – Improved Service Delivery Levels
The ability to hire locally has proven very successful. It has resulted in staff retention rates in excess of 95%.
In keeping with the traditional company values, SL Controls continues to hire only permanent staff, providing a greater degree of certainty for the employee and also for the client. All SL Controls’ employees are provided with a structured career path which allows them to develop and progress in their chosen engineering disciplines. This is further underpinned by the company’s core values of fairness, camaraderie, respect, communication, innovation and balanced lives.
The benefits, as seen and acknowledged by our clients, is first and foremost in the continuity of service which they have witnessed since 2013. We have provided them with a platform where they can rely and call upon the same group of engineers to work with and alongside their own permanent staff.
As the relationship develops over time, the knowledge and experience gained by SL Controls engineers on client systems and processes have opened up opportunities for clients to engage the SL Controls’ local projects office to undertake specific turnkey software and validation projects.
The model of establishing an office and hiring local permanent staff has since been rolled out to the Dublin and Galway regions, with the same degree of success. The low staff turnover, high-quality of work, and the timely and successful completion of projects by SL Controls’ highly skilled staff are a testament to the commitment made in valuing our workforce.
« Previous 1 … 16 17 18