Blog
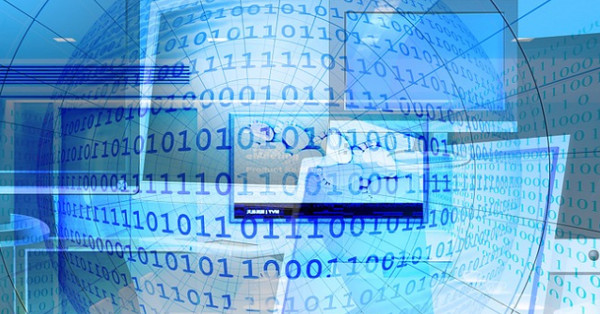
Harmonising Data from Different Manufacturing Control Systems
Data is central to almost all significant improvements your production line and overall operation will experience over the coming years. Industry 4.0, enhancing OEE, automating additional processes, integrating machines and platforms – all this and more relies on data.
In simple terms, this means a machine putting out data and another machine or system acting on that data to populate a report, track products, send a notification, trigger another stage in the production process, trigger a business process such as system optimisation or ordering new materials, and more.
The Challenge
There is a major barrier that is and will prevent you from achieving the improvements and benefits that new technologies and processes present: there is no consistency in data standards.
Various control vendors, OEMs, and automation technologies all produce data of some sort, but they do so according to their own standards. This means, in the vast majority of cases, solutions from different vendors do not talk to each other out of the box.
In many respects, this silo mentality of vendors is understandable. They believe they have the best solution for your production line and they want you to purchase all available products from them. Even if they don’t provide a particular machine or technology you need, they are still reluctant to work to a standardised data format because of the engineering hours involved and because it may mean compromising on the functionality, performance, and uniqueness of their products.
Busting this down to the reality of your plant, however, means you can have two machines, both from different vendors, both dependent on the other, and both producing data. Neither machine, however, recognises the data of the other.
The results for your business in this scenario are all negative: inefficiencies, increased risk, production delays, compliance issues, increased production costs, and more.
The Process
The solution to this challenge is obvious – develop a standard that works regardless of the platform. In other words, using a standard that makes it possible for your system to understand and, crucially, interpret and use data, regardless of how the machine creating the data was programmed.
Of course, this is easier said than done. The biggest consideration is developing a standard that performs equally and consistently across all vendors and platforms. There are three elements to this:
- Requires exposure to – and experience of – a wide range of different control systems, platforms, and technologies.
- You also need a deep understanding of the programming of the machine or platform. In other words, how the machine analyses itself, how it processes performance data, and how the data it produces is summarised, published, data-logged, and reported.
- Finally, you need a process that enables ongoing development of the standard to keep it up-to-date as vendors launch new platforms and technologies.
The Solution
Taking a vendor-neutral approach to developing a standard for data is the only workable option. This is exactly what we did at SL Controls, following the process detailed above.
In other words, we work with a broad range of clients so have extensive experience of a variety of vendor technologies, and we understand the programming of those technologies. In addition, we regard keeping the standard up-to-date with new developments in the industry as being a core business focus.
The benefits of a data standard like this to your operation are substantial. These include:
- You will gain a deeper understanding of your production line which will enable you to take performance improving decisions.
- Overall OEE will improve.
- Your production line will become more efficient.
- Opens the door to further integration, automation, and implementation of other Smart Factory technologies.
To say all this is possible with data is far too simplistic for a modern production facility. The benefits above are only possible when data is usable. This can only happen when you have a workable data standard, such as we offer at SL Controls.
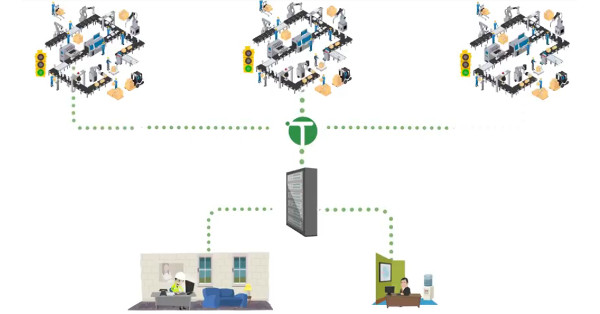
Video – Making Data Work in Your Business Across Multiple Manufacturing Facilities
Data has never been more important than it is today. It is how you use that data, however, that will determine the success of your production lines in the future.
It is crucial to have integrated systems so that data from one machine or process can be read and used by other machines. This should happen within a production line, across multiple production lines, and across multiple production facilities, regardless of geographical area.
This is a complex challenge to address, particularly if you have machines and systems from different vendors.
TOTALdata is the solution. Check out the video for an introduction to how TOTALdata works:
Speak to a member of our team today about improving how your production line uses data. Email [email protected] and we will get back to you.
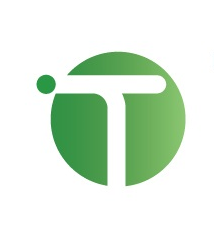
Delivering OEE Improvements of Up To 20% – The TOTALline Journey
You can improve OEE in your production line by up to 20 percent by introducing a new product from SL Controls, TOTALline. You can do this at a cost that is up to 50 percent cheaper than comparable solutions with similar features.
In addition, TOTALline improves decision making as well as delivering business efficiency savings. If you want to find out more about the product and its features, you can read the TOTALline pages of our website. This blog focuses on why and how we developed TOTALline, so you can get a better understanding of how it can benefit your business.
The Challenge
Every business is different, and every production line is different – different products, processes, machines, servers, software applications, and more. The goals of most businesses are similar, however. This includes operating more efficiently, improving OEE, reducing the resources required to operate the line, improving access to data, generating actionable reports from that data, and more.
Businesses face challenges in achieving these goals, however, not least of which is cost. There are also integration issues to consider particularly when you have machines, platforms, and software applications from different vendors. There are customisation issues too, i.e. there are products available that:
- Have some features you need;
- Lack other features you also need; but, instead,
- Have features you don’t need.
This leads to inefficiencies in implementation, confusion, and waste as you are paying for features you’ll not use. There’s also frustration as features you need are lacking.
This was the starting point for the development of our TOTALline suite of products – lines and plants have varied starting points, but everyone wants to achieve similar goals at minimal cost.
Of course, we could come into your business like other automation and controls solution providers to develop a system that works specifically for your business. This solves the customisation and integration challenges, but it’s an expensive option. We knew there was a better way.
So, the modularised TOTALline range of products was born – a multi-functional product that is easily tailored to specific needs.
It’s Not What TOTALline Does – It’s How It Does It
We have implemented individual and fully customised solutions for many customers that deliver the same results that TOTALline can achieve. In other words, it’s not what TOTALline does that makes it so innovative in the industry – it’s how it does it.
In addition, it’s the “how” that will deliver substantial benefits for your business.
SL Controls was able to achieve this because of our broad experience in implementing automation and controls solutions. We are unlike other vendors in this respect who may understand part of your line or a specific machine very well. We have the benefit, however, of having a complete overview of the process, enabling us to deliver integration, control, data logging, and data visualisation solutions covering your entire production line.
What TOTALline Does
By way of a very brief summary, TOTALline consists of a range of modules that:
- Automates and improves batch control changeover processes
- Enhances batch data integrity and improves traceability
- Enables machines to self-report
- Collects and logs machine, device, and line data centrally to provide actionable and meaningful reports
Benefits of TOTALline
The modular nature of the product brings a range of benefits to your business:
- You can customise the solution using the modules you need, leaving the ones you don’t
- Considerably less expensive than developing a solution from scratch
- As the core architecture of the modules is already in place, the system can be rapidly customised and deployed
- Easy to scale when you need additional features or if the needs of your business change
- Vendor-neutral so it will work whatever machines, systems, servers, platforms, or software you currently use
- Highly flexible so suits production lines in a range of industries including pharmaceutical and medical device manufacturing
The OEE improvements you make by implementing a customised TOTALline solution will depend on your business, but we regularly see improvements in the 10-20 percent range.
In terms of cost, if you compare the product with a full-scale line batch and data solution, TOTALline is up to 50 percent cheaper. In other words, it’s a product that can make a significant impact on your business for the better while delivering impressive ROI.
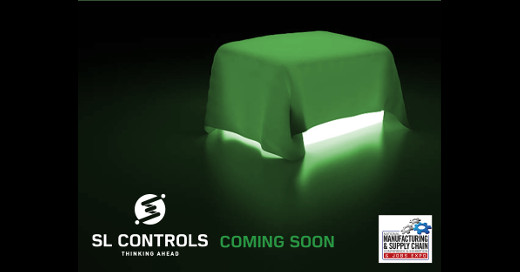
The National Manufacturing Exhibition – Addressing Industry Challenges
Integration, automation, and making better use of data – these are items on the agenda of most manufacturing facilities in Ireland. They apply in all industries, but they are particularly important in the pharmaceutical, medical device, and food and beverage industries, not least because of compliance and regulatory pressures.
Taking it a stage further, most manufacturing operations know these three areas – integration, automation, and making better use of data – are priorities. However, significant challenges exist in their implementation.
The Challenges
There are no consistent data standards across vendors and platforms, for example. This means you can get data from an individual machine, but this doesn’t tell you much about your overall production line or allow you to compare or share data between machines/lines.
When your systems can’t use data across machines, integration of those machines, data-driven comparisons, and functionality becomes impossible.
As a result of this lack of integration, you can’t automate processes.
This leaves you with unnecessary and inefficient manual processes that are riskier to your business and considerably costlier than the automated alternatives. Plus, your machines may produce data, but you won’t be able to use that data to drive process improvement and comparison in a consistent manner within the organisation.
The Solution
SL Controls has developed a solution that addresses these challenges. It is a new product that we are launching at the National Manufacturing Exhibition next week.
It is a product rather than a service, so we can implement it in your production line quickly. However, as it is a product, you benefit from economies of scale which means costs are low. In fact, the cost of implementing our new product is about half the cost of developing a bespoke solution offering the same benefits.
While it is a product, it is modularised and configurable. In other words, we can completely customise it for your facility, ensuring it delivers according to your specific business objectives. This means you choose the modules you want and leave out those you don’t want.
We’ll then configure the models you select to integrate them into your existing systems.
Get the Benefits of a Modern Production Facility
The benefits of implementing this new SL Controls product are considerable. You can read about these benefits on our launch announcement page. On that page, you can also find out more details about the National Manufacturing Exhibition and the official product launch, where everything will be unveiled.
There is a form on that page as well where you can book a timeslot to speak to a member of our team. We’d love to show you how the new product works and how you can improve OEE in your production line by up to 20 percent. We look forward to seeing you.
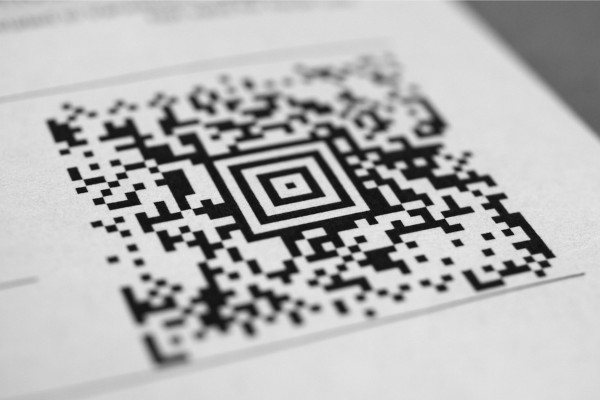
Serialisation in the Pharmaceutical Industry – What You Need to Know
Serialisation in the pharmaceutical industry is one of the best tools society has to combat counterfeit medicines. What are the facts relating to this issue, though, and what do you need to know now about serialisation?
Counterfeit medicines are a risk to public health. They are often not effective so don’t benefit patients. If that is not dangerous enough, counterfeit drugs can also actively harm patients, even causing death.
Counterfeit drugs also damage the pharmaceutical industry. They directly cause lost revenues plus they can have knock-on effects including unwarranted reputational damage, loss of patient confidence, and more.
Tackling Counterfeit Medicines
The solution is easy to state: rid the world of the scourge of counterfeit medicines. Anyone involved in the pharmaceutical industry, from manufacturers through to regulators, knows that this is exponentially easier said than done.
It isn’t even effective to turn up at a counterfeit manufacturing facility to close it down. This is because the medicines are almost always manufactured in stages at different locations. In addition, it is not unusual for these locations to be in different countries.
Counterfeit manufacturing facilities are typically also individually small. They produce at scale because they have multiple small facilities. In other words, when you shut down one, many, many more continue to operate unaffected.
Tackling the distribution side of the counterfeit drug distribution problem is equally challenging, not least because many fake medicines are sold on the internet. In fact, according to estimates from the World Health Organization, as many as 50 percent of drugs sold on the internet are counterfeit. In addition, around 90 percent of the drugs sold do not originate in the country the selling website claims they do.
While authorities are getting better at policing the web, there is a long way to go.
The Serialisation Solution
This is where serialisation comes in. It cannot, on its own, stamp out counterfeit medicines but it can make a major contribution to the effort.
Serialisation involves tracing each individual product via a unique serial number from the manufacturer right through to the end user – the patient. The serial number gives information such as the origin of the product, the production batch, the expiry date, and more.
Implementing serialisation in the pharmaceutical industry involves acquiring unique serial numbers for your products, assigning them to each batch you produce, printing the serial number on the product’s label in the form of a barcode, and then managing the data so you can trace the product via the serial number. You might need to do this months or even years after the product leaves your production line.
What You Need to Consider
Cost
You will need to allocate a budget for upgrading your system to both apply serial numbers to your products during manufacturing and also to manage the data this produces. This includes software development costs to add functionality and integrate systems, as well as potential hardware upgrade costs.
Resources
You will also need to allocate resources to fully implement serialisation in your production line. As there are no standardised global rules that cover the whole pharmaceutical industry, this includes getting a full understanding of the implications of serialisation depending on the global markets you serve and the type of products you produce. You will also need resources to properly plan the implementation of serialisation, and there will be an element of staff training involved.
Getting the right partner
Crucial to all successful serialisation implementations is ensuring you work with the right partner. This means selecting a software provider who is vendor neutral so can work with all your platforms and equipment. You should also select a provider with integration, serialisation, and pharmaceutical industry experience.
Automation
Implementing serialisation will slow down production, particularly in the packaging phase. After all, you will need to add serial numbers to each package. This means individual product packages, case packages, and pallet packages. Adding additional automation to your line can offset this and, in some cases, make your line more efficient than before.
Data management
Your facility will need systems that enable the efficient storage of data that serialisation produces, as well as giving users quick and easy access to that data. You need hardware for this but, crucially, you also need effective data management and reporting software. In almost all cases, this will mean a bespoke solution integrated with your existing system.
Data exchange
For serialisation efforts to be effective, it is not good enough for you to have data internally. You also need systems in place that facilitate the secure sharing of data with your supply chain and others.
Changing regulatory environment
Countries around the world have different serialisation regulations in place and different deadlines for their implementation. This is challenging in itself but there is also the fact that these regulations are not fixed. Instead, you should view them as evolving. This means any serialisation solution you implement should be flexible and scalable. Your compliance team must also be nimble to ensure you are on top of all current regulations as well as any upcoming changes.
Serialisation is a reality for the pharmaceutical industry. While there are cost, production, and resource issues involved, it will bring multiple benefits.
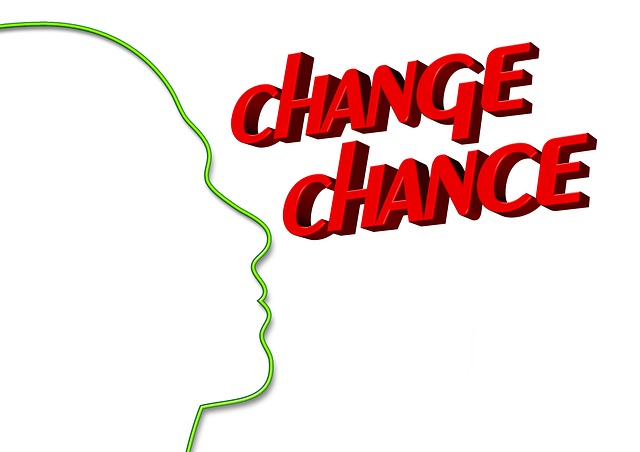
The Boomtime for Construction Site Sparks Becoming Automation Engineers
Do you remember the dark days at the start of the financial crises in 2007 and 2008? It’s hard to believe it was more than 10 years ago when UK customers of the Northern Rock bank could not access their money because of a bank run. Then there was the “St Patrick’s Day Massacre” on 17 March 2008 when Anglo Irish lost almost a third of its value in a single day.
These events and others were key moments in the Irish and worldwide financial crisis. At the time, it was hard to see light at the end of the tunnel.
The banking sector, the construction industry, and the wider Irish economy were in destructive turmoil. That said, these events were also the precursor for what would become a boom time for a particular group of people – ambitious construction industry sparks.
Facing the Challenge Head-On
The years of the financial crisis from 2008 to about 2014 were not easy for anyone in the construction industry. For many electricians, the only viable choice was to return to college to upskill in an electric-related discipline.
Luckily there were some incentives that made this easier. This was important as many electricians had come from well-paying jobs and careers. In other words, they had mortgages or rent to pay, families to feed, car payments to make, and more.
The incentives included grants that made it possible to just about survive, particularly given the fact the social welfare alternative was no more attractive.
Crucially, qualified electricians were able to skip the first year of a three-year degree. This meant they could qualify quicker which would get them back working again faster.
What to Study?
The decision to go back to college was not the only decision electricians had to make – they also had to decide what electric-related discipline to study. There were three main choices:
- Renewable energy – this was the hot topic at the time, and many predicted it would be the boom industry of the near future. As a result, electricians were promised plentiful, sustainable jobs that would pay good money.
- Electronics – a solid discipline that has always attracted attention.
- Automation – an emerging discipline that not many people knew very much about.
Those who chose automation, however, were not disappointed.
Returning to Study – More Than a Change of Scenery
It’s not difficult to imagine what a jolt it must have been for many electricians to step back into the classroom. Broadly, those electricians fell into the following categories:
- Those who left school early to get a trade and mostly worked in the domestic installation sector
- Those who did some study at an early age but never thought they would go back to it
- Ambitious and highly-skilled electricians who were always open to upskilling and changing careers
- Manufacturing workers, particularly those who were part-time, who wanted to upskill and, in many cases, get away from shift work
In all the above categories, the electricians involved had little or no mathematical or programming skills.
They acquired them though, they got their qualifications, and they became hireable engineers.
Embarking on New Careers
Electricians who went back to college to upskill as automation engineers have generally done well in their new careers. Their previous experience means they understand how machines work, plus they had exposure to PLCs during their apprenticeships.
In addition, working on building sites gave them a work ethic that included doggedness, drive, and a can-do attitude. All these characteristics are attractive to employers and end clients alike.
SL Controls recognised this new resource at an early stage and has, to date, hired about 10 engineers who were formerly electricians.
Is the Boom Coming to an End?
All booms must end, and it appears this one might be becoming a memory.
Over the past five years, the building industry has not offered as many apprenticeships so there are fewer electricians in the construction industry. In addition, that industry continues to recover so there is work for those electricians who are entering.
So, the resource of former electricians moving to the automation industry might be drying up.
One thing does remain, though – the electrical apprenticeship model means those that did become engineers are now proving themselves to be effective mentors for today’s crop of junior engineers.
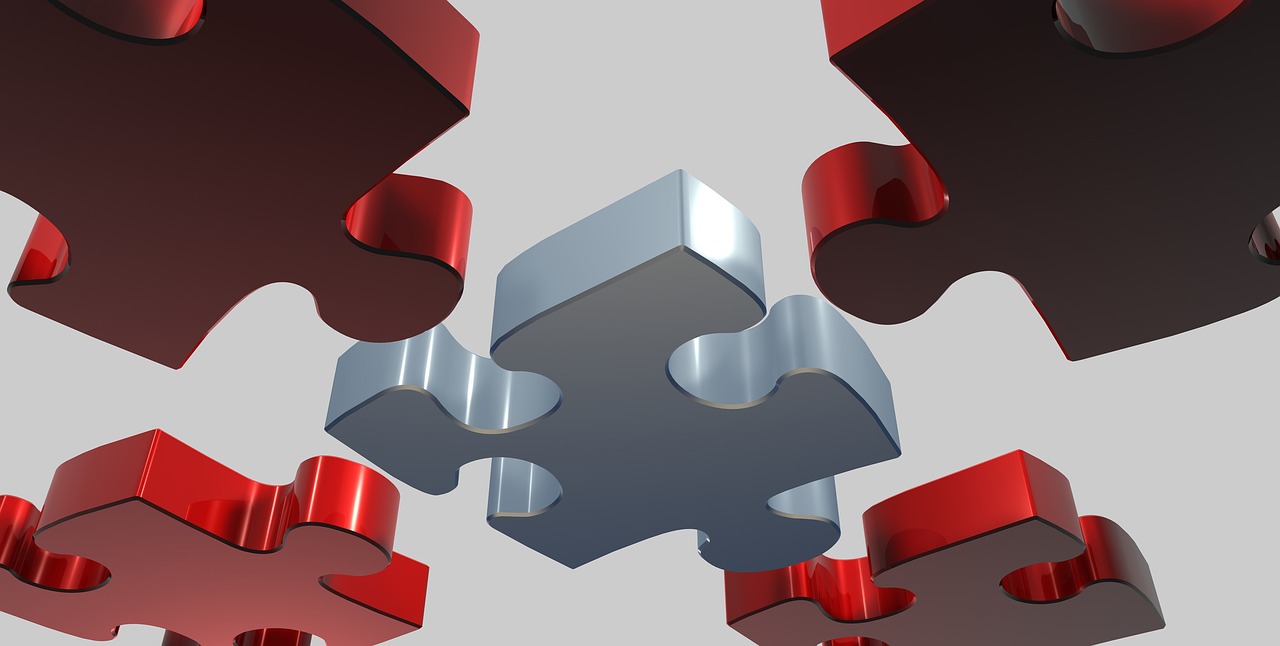
Importance of Being Vendor Neutral
You don’t have to look very far on the SL Controls’ website or any other material we produce to see we are vendor neutral. What does being vendor neutral mean, however? More importantly, what benefits does vendor neutrality bring to your business?
What Does Being Vendor-Neutral Mean?
Vendor neutrality is both a business approach and an approach to designing software, including automation and controls solutions. Therefore, becoming vendor neutral is a deliberate and important business decision. It’s not something that happens by default.
From a business perspective, it means not going into partnership with one or more vendors. Of course, there are advantages to having partnerships, but the benefits of remaining independent are much more compelling.
Primarily, without the restriction of partnerships, it’s possible to offer a broader and more comprehensive range of solutions.
From a design point of view, vendor neutrality means using standardised methods and design principles that are non-proprietary. This enables us to work on all systems, platforms, and equipment.
Benefits to You of Having a Vendor Neutral Software Provider
How do you benefit from using a vendor-neutral software provider? Here are the main advantages:
1. Complete focus on your success
Partnerships with vendors usually have a financial element. This can influence decisions by software providers and the approach they take to delivering your solution. Being vendor-neutral results in a solution that is genuinely aimed at achieving your goals rather than doing something that is also beneficial to the provider-vendor relationship.
2. Enhanced capabilities
A vendor-neutral software provider can deliver regardless of the machines, systems, or platforms you currently use. This means you won’t have to purchase new equipment to make everything work. You won’t be asked to compromise on features and/or functionality either.
3. You’ll get a holistic solution
Following on from the last point: when a software provider is vendor-specific, the solution may not be complete. This is often because of the limitations of a particular vendor. This situation doesn’t arise when you work with a vendor-neutral provider, resulting in a more holistic solution.
4. The team will have greater experience
A team that takes a vendor-neutral approach to software development for the manufacturing industry will have much greater experience of machines, systems, and platforms. They will also have more experience achieving results even when the tools they must work with don’t fit neatly into a pre-defined, vendor-specific box.
5. You’ll have more choice regarding your equipment and machines
Using a vendor-neutral software provider means you can continue using vendors you are familiar with and trust. You can also choose to move to other vendors too – there are no restrictions.
6. You’ll get ongoing budget and efficiency savings
You’ll get these savings in many ways. For example, the solution will deliver maximum efficiency savings because it is holistic. Also, you will save when upgrading, expanding, or replacing your machines or equipment because you won’t be tied to a particular vendor.
Being vendor neutral is critically important to SL Controls and helps us optimise OEE, achieve systems integration, and more for our clients. The benefits of using a vendor-neutral software provider are significant for you too. To find out more, contact us today.
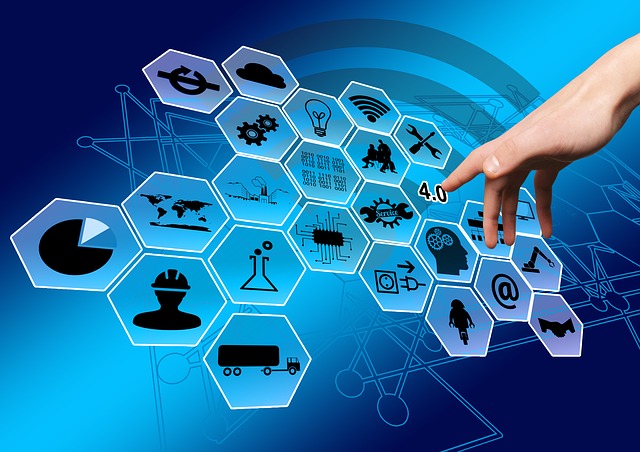
Industry 4.0 – A Realistic Pathway to the Smart Factory
Industry 4.0 is the undeniable buzzword in manufacturing at the moment. After all, it is easy to understand the potential benefits and get excited by the prospect of the smart factory. Making your plant part of the fourth industrial revolution, however, is much easier said than done.
It is such a massive topic, in fact, that it’s difficult to know where to start. The whole concept is both overwhelming and daunting.
In addition, while the theory of Industry 4.0 is great, you’re not involved in theory. Instead, you’re in the real-world of maximising OEE, tight manufacturing deadlines, increasingly high customer expectations, creating supply chain efficiencies, reducing costs, complying with regulations… the list goes on.
Where, then, do you start with Industry 4.0?
The Problem with the Smart Factory
Most articles about Industry 4.0 and the smart factory add a concise definition of what the author thinks it is. Here is the reality, though – nobody really knows what the smart factory looks like.
Of course, there are technologies and concepts that are a part of Industry 4.0 that we can talk about. In brief, this includes connecting and integrating all aspects of the manufacturing process including machines, IT, systems, platforms, human operators, business processes, the supply chain, and the wider enterprise.
Crucially, it’s not just about connecting these elements but also automating decision-making across the whole company and manufacturing process.
So, the smart factory is more about becoming autonomous than it is about more traditional automation. It also involves technology that enables machines, systems, and processes to learn, change, and self-optimise.
Back to the point above, though, i.e. nobody really knows what the smart factory looks like. This is because technology is advancing incredibly rapidly. In fact, in five or 10 years’ time, there will be technology available to make your factory smarter that has not yet been conceived.
In other words, the smart factory is not an end result. Instead, it’s an evolution with no conceivable end date.
Also, there is no fixed Industry 4.0 pathway. The pathway is, instead, completely flexible and can – and should – be adapted to the needs of your business.
The Realistic Industry 4.0 Pathway
Understanding there is no fixed pathway and that developing the smart factory is an ongoing evolutionary process actually makes starting the journey much easier. In fact, the answer is quite simple: you should have big goals for your plants, but you should start small.
This could involve starting on a single production line, or even a single asset, and maximising its performance. This could mean automating batch control, for example, or improving the way you generate, collect, centrally store, present, analyse, and then use data to make real-world decisions.
By starting small like this, it’s easy to manage, there are fewer risks, and it’s cost-effective while still letting you test and prove concepts. You’ll also get to see how the benefits of Industry 4.0 will impact your operations and facilities, plus you’ll get to see the challenges too. These include:
- The impact on operational processes
- Governance issues
- Compliance
- The impact on people including the reallocation of resources
- Cybersecurity
When you start small, you can then gradually scale to other lines, the whole factory, multiple factories, and into the supply chain and wider business processes.
By doing so, you won’t create a smart factory within a predefined period of time, but you will be part of the fourth industrial revolution. Your factory will also become smarter and your overall business will improve.
With no clear reason to delay, the time to start on your Industry 4.0 and smart factory journey is now. Visit our Factory Automation pages for more information.
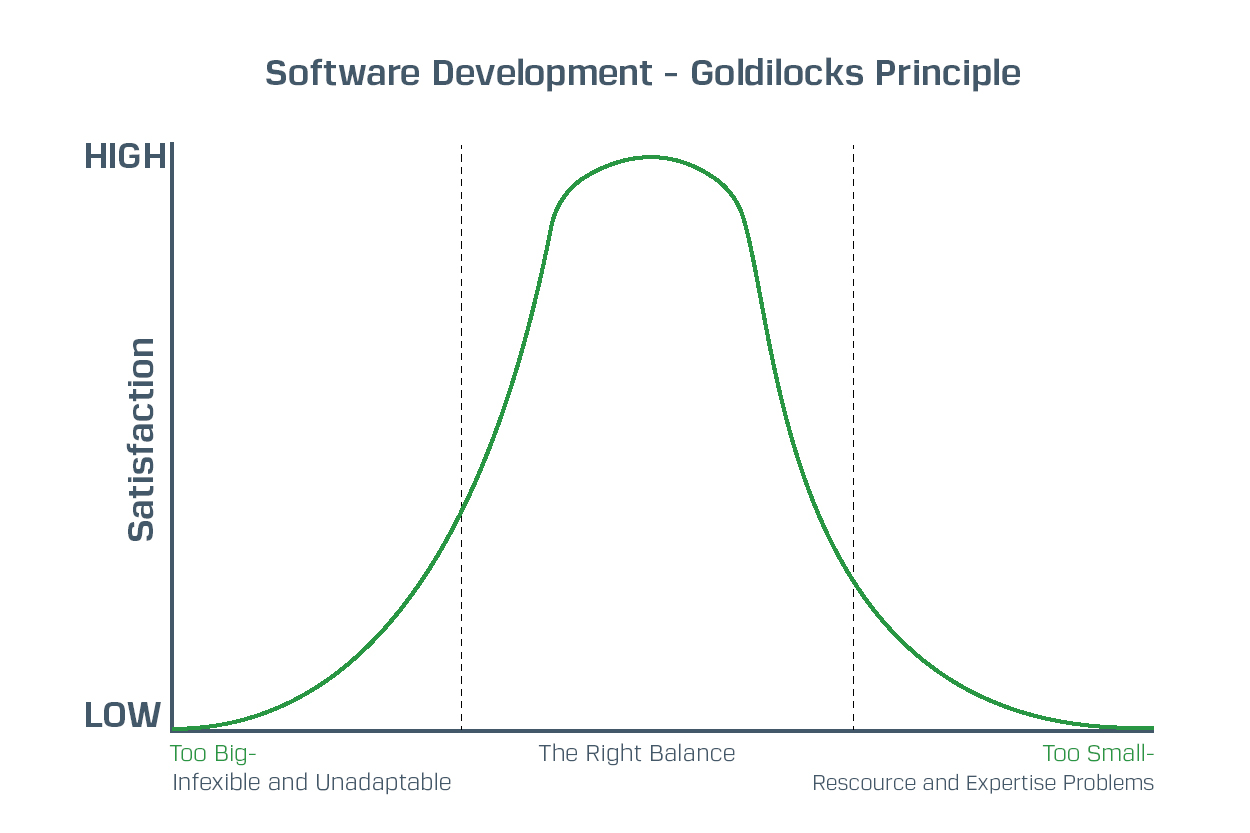
Why the Regulated Sector Needs Bespoke Software Solution Providers That Are Not Too Big or Too Small
If you’re in a regulated sector like pharmaceutical or medical device manufacturing, what type of software provider is right for your needs? Firstly, you need a provider that delivers bespoke solutions with complete flexibility. Secondly, you need a provider that has access to the right expertise and adequate resources.
This means you need a provider who is large enough to scale but small enough to adapt. In other words, a provider large enough to have sufficient resources to handle big projects while also being small enough to remain agile and flexible in delivering your specific requirements.
When you have these elements in place, your project will run more smoothly, and you will achieve your objectives more cost-effectively.
Not Too Big
When an organisation gets to a certain size, it loses its ability to quickly adapt, making it harder for larger solution providers to address your specific needs. This is because structures, products, services, and management decision-making processes become increasingly complex the larger a company gets.
Most large companies package their offering into major product or service solutions. These are often very comprehensive and, in their own right, powerful. This approach has three major and interconnected disadvantages, though:
- Off-the-shelf solutions are not always able to meet your technical or business requirements, however comprehensive they are. This applies, for example, when a function or feature is not already part of the company’s offering. You can even encounter these feature and functionality gaps when the product or service is customisable.
- The function or feature can be added to the product or service solution, but this typically happens as part of the provider’s regular update and release cycle. Usually, this cycle is one or two years long which is likely to be too infrequent to fit into the timeframe of your project.
- Even if a product or service solution includes all the features and functions you require, it probably also includes many you don’t. In other words, you’ll have to pay for unrequired features just to utilise the functionality you do need. As well as cost disadvantages, there can also be technical disadvantages in this situation.
Not Too Small
The biggest problem for small software solution providers is resource availability as small providers have access to limited resources. They might have the will and desire to customise a solution to meet your needs but soon run into trouble on the resources front. This can happen for several reasons including:
- Simply not having people with the right skills.
- Having people on the team with the right skills but getting into situations where those people are too stretched, usually because of multiple project responsibilities.
- Being too dependent on a small number of key people – often just one or two. Major issues then occur if one or more of those key people become unavailable, i.e. because they leave the company or fall sick, for example.
- Lacking a broader comprehensive experience of working with different customers that you would get from a larger design team.
Striking the Balance
You need to ensure the software solution providers you use get the right balance between:
- Remaining flexible and agile so they can deliver according to your specific requirements within the project cycle
- Having enough resources in place so they can deliver, even when things don’t go as planned
That means striking the right balance, i.e. being large enough to scale but small enough to adapt.
We can use SL Controls as an example as we are small enough to adapt. Our structure, however, means we have the capabilities required to deliver. For example, our product and software design teams are directly available to the project delivery teams. In addition, our design offering is a managed service that has the resources and structures in place to provide scalable solutions, particularly to the pharmaceutical and medical device manufacturing industries.
SL Controls also has a validation and quality department experienced in the development and testing of:
- GAMP Software Category 4 – Configured Software
- GAMP Software Category 5 – Bespoke Software
All the above means we have the right resources in place but also have a structure that is agile, facilitates fast decision-making, and is flexible according to your needs.
« Previous 1 … 15 16 17 18 Next »