Blog
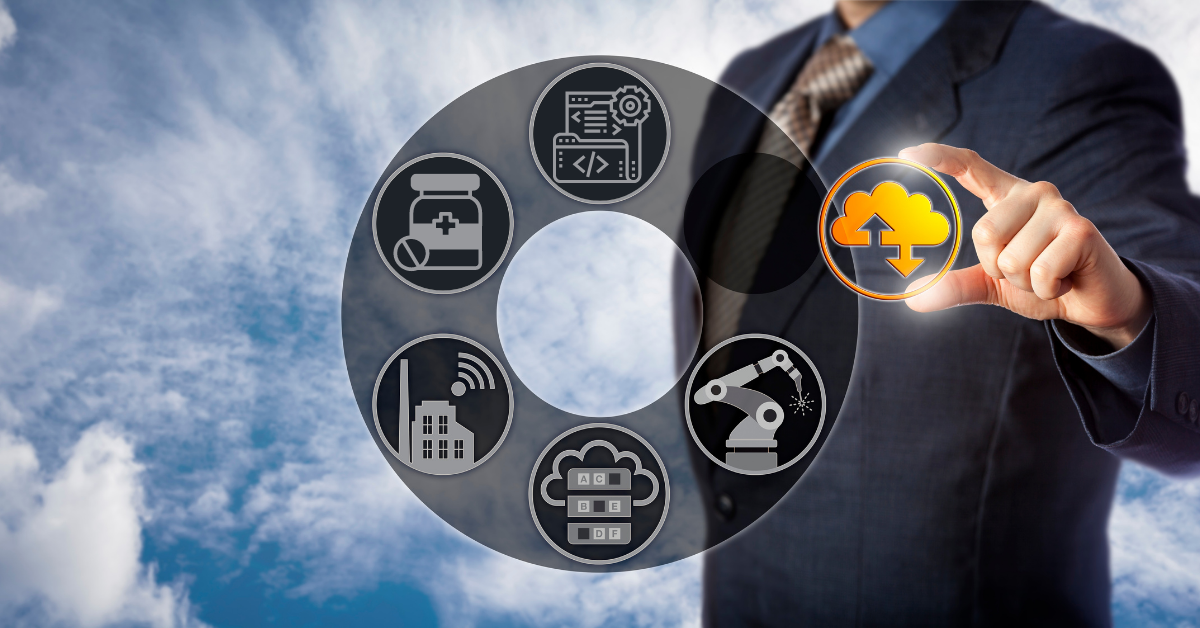
Build Once, Deploy Multiple Times in Seconds – Cloud-Based Solutions for Pharma & MedTech Manufacturers
For pharmaceutical and medical device manufacturers, repeatability is a primary goal when developing new manufacturing software solutions. The concept is simple – you select a facility or production line for the initial project, creating a software solution to deliver on your manufacturing and business objectives. Once you have that operational and delivering results, you can then look at deploying the solution in additional facilities and production lines.
While the concept is straightforward, achieving this repeatability is close to impossible using traditional on-premises architectures, as the copy of the solution never fully works on subsequent deployments. Even when developers give as much consideration as possible to repeatability, problems still arise. Those problems mean that, in subsequent deployments, code changes must be made, and fixes implemented.
This is because there are always unique features in every subsequent deployment of on-site manufacturing software solutions that aim to be repeatable. Those unique features can exist in a range of areas, including data capture and extraction, as well as the hardware and networking that exists in the facility. Server builds, function delivery, and equipment communication protocols can also have unique elements that prevent fully repeatable deployments. The hardware resources on-site can also present challenges, as can the ability of the system to handle the processes required to copy and redeploy the application.
At SL Controls, we have first-hand experience of these challenges as customers regularly ask us to deploy tried and tested manufacturing software solutions on different lines or facilities. Developing an answer to this repeatability challenge became a key priority.
Building Solutions in the Cloud
Developing cloud-based solutions is the key to overcoming the challenges of achieving full repeatability of manufacturing software solutions for companies in the pharma and MedTech industries. This is because the developer must create a solution that uses remote resources and that also fits within the architecture of the cloud.
So, for example, when a solution is developed to deliver data between a production line and the cloud, that solution must be tailored to the cloud. This makes the solution repeatable on any similar production line or facility, as it uses the architecture of the cloud rather than any on-premises architecture.
Not only are cloud-based manufacturing software solutions fully repeatable, but they can be copied and redeployed in seconds.
Benefits of the Cloud-Based, Build Once, Deploy in Seconds Model
- Reduce resources required for subsequent deployments – with the traditional approach using on-premises architecture, subsequent deployments of manufacturing software solutions usually require highly skilled developers to implement. With repeatable cloud-based solutions, the process of copying and redeploying is automated.
- Save time and money – the provisioning of the software solution on additional production lines or facilities takes seconds rather than days, weeks, or months. Plus, there is no requirement for further coding or development, increasing the savings further.
- Improves agility – having the ability to deploy essential manufacturing software solutions in new environments will make your business more agile and better equipped to react and adapt as required.
- Ensures greater consistency of deployment – the automated nature of redeployments ensures consistency, prevents configuration drift (where the software solution is changed with each deployment resulting in a situation where there are multiple versions in operation), and eliminates the potential for human error.
New technologies, systems, processes, and practices are making it possible for pharmaceutical and medical device manufacturers to transform their operations, enhance competitiveness, and improve profitability. Successfully, efficiently, and cost-effectively deploying manufacturing software solutions multiple times is one of the challenges to overcome. Cloud architectures provide the answer. To find out more, contact us at SL Controls today.
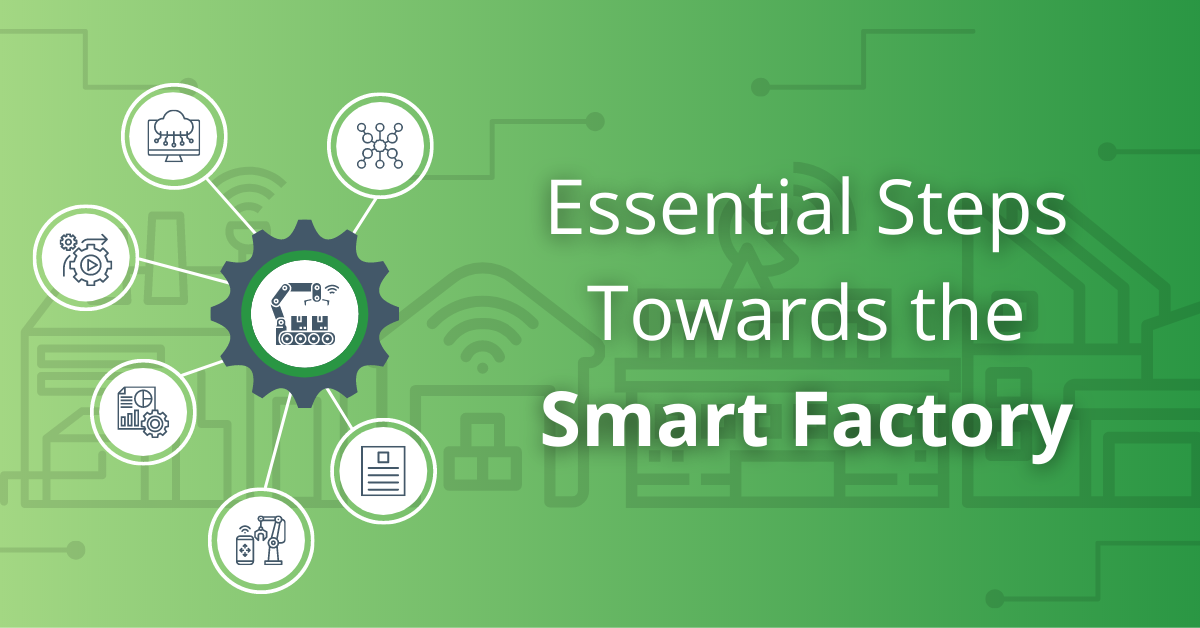
The Essential Steps in Your Smart Factory Evolution
Moving your business closer to becoming a Smart Factory is widely regarded as essential to continuing competitiveness and profitability. Driving efficiency savings, making productivity gains, dealing with skills shortages – these are just some of the challenges that manufacturers face, all of which can be considerably mitigated with Smart Factory solutions.
How do you get to the Smart Factory, though? What should you do next, how far should you go now, and what are the priorities? How do you transform your manufacturing operations into a future factory?
The answers to these and similar questions are not easy as there is no one-size-fits-all solution. Instead, the many different variables that exist mean the solution is different for every production environment.
Those variables include the production inefficiencies that currently exist, issues with productivity, and the specifics of the product/s being manufactured, as well as the wider business processes for procurement, distribution into the supply chain, sales, and more.
Initial Stages
We’ll look at the essential technical steps that are required to move your manufacturing facility closer to being a Smart Factory, but there are some initial stages that you need to go through before any technical work should begin.
Identifying Priorities and Goals
Wherever you are on your Smart Factory journey, it is essential to identify your current priorities and goals. Those priorities and goals could be something specific, such as introducing a new product to your production line or increasing capacity without the need to hire additional staff. These are ideal opportunities to introduce new technologies that will help with your smart factory evolution.
You might also have more generalised priorities and goals where the aim is to improve efficiency, productivity, decision-making, and/or reliability on your existing production lines. This could be, for example, increasing levels of automation to alleviate recruitment or staff retention pressures, or it could be optimising OEE to maximise profitability.
Smart Manufacturing Audit
Another initial stage you should go through is to audit your current Smart Factory status. This audit should include all aspects of your operation, such as the equipment on your production lines, the current level of systems integration, how you use data, your IT infrastructure and the level of integration with OT (operational technology), cloud vs. on-premises systems, and connectivity.
As well as giving you an overview of your current status, an audit will also tell you what can be achieved by implementing new Industry 4.0 technologies and processes. You can then use this information to identify the opportunities that best match your priorities and goals, and that will deliver the best return on investment.
Technical Steps Towards the Smart Factory
The steps typically involved to move your facility from where it is now to a Smart Factory include:
- Enabling communication and the collection of data – this is known as Equipment Systems Integration
- Data visualisation – to make it possible for you to access and process the data collected
- Automated decision-making – where many manual and time-consuming decisions are automated
- Machine learning – where the systems in your facility automatically improve by learning from real-time data and the outputs from previous decisions
Step 1 – Equipment Systems Integration
The ultimate objective of equipment systems integration projects is to connect all potential sources of data to a common system. This includes the production line as a whole as well as individual machines and equipment.
It can also include data not directly connected to manufacturing the product, both within your organisation and outside it.
Within your organisation, this includes data from other units and departments in the business, from finance to HR to purchasing to sales and marketing. This process is known as vertical integration, where the focus is on integrating the OT (operational technology) and IT (information technology) aspects of your business.
Outside your organisation, the main focus should be on your supply chain. This is known as horizontal integration. It involves integrating with third parties in your supply chain both upstream and downstream to achieve real-time visualisation and communication, and to maximise efficiency.
Once systems are integrated and connected to a common system, you can start making changes that will deliver real and tangible benefits for the company. This includes automating additional processes where it wasn’t possible to do so before because the equipment and platforms couldn’t connect or communicate with each other.
Your system will also be able to collect and store data, setting you up to move to the next step.
Step 2 – Data Visualisation
Once you have gone through an equipment systems integration process, your production facility will have the capability to collect data from a vast range of sources.
This is only one step in the journey, however. The real work begins when you start putting the data you collect to good use. In other words, the data your system collects must have value.
After all, data in itself won’t improve your business. You’ll derive value from how you use that data.
Implementing data visualisation solutions is a key part of this process.
Data visualisation makes it possible for decision-makers to make sense of the data collected. Those decision-makers can then act on what the data tells them. This applies to everyone, from operatives to engineers to engineering managers to CEOs.
Again, however, this is only a step on the Smart Factory journey as the next point, automated decision-making, will improve productivity even further.
Step 3 – Automated Decision-Making Based on Data
Automated decision-making is where you move from a position where people analyse and use data to one where the system makes decisions itself. This can be rules-based decision-making, where you have if-this-then-that scenarios, or it can be data-driven decision-making.
Automating decision-making offers a range of benefits:
- Decisions can be taken immediately any time of the day or night as there is no need to wait for a decision-maker to be available
- Improved productivity and enhanced OEE as a result of eliminating decision-making delays
- Eliminating the risk of human error in decision-making
One of the most straightforward examples of automated decision-making is equipment maintenance schedules.
Instead of a manager scheduling maintenance according to a timetable created by the manufacturer of the equipment, sensors collect data with that data then used to determine the best time to schedule maintenance. As a result, maintenance scheduling decisions can be based on specific business objectives, such as conducting the maintenance before a failure occurs or completing the maintenance when it will have the least impact on output.
Step 4 – Machine Learning
Following on from the above, the next step is to enable your Smart Factory to learn from the decisions it takes and the information it receives.
So, in the equipment maintenance example above, the system will learn as the machine operates in the live production environment, tailoring the maintenance scheduling decisions it takes accordingly.
Another technology that becomes important in this part of the Smart Factory journey is statistical modelling and digital twins. These technologies allow you to run data-driven simulations to improve processes, plan for production line changes (such as new product introductions), and more.
Furthermore, machine learning opportunities exist with data from all sources, not just the manufacturing element of the business. For example, a Smart Factory with machine learning capabilities can also improve areas like product development and sales forecasting as it gets better at predicting customer trends and other external factors.
Moving Forward
The above is a general guide to the steps typically required on a Smart Factory development journey. What should you do now, however?
At SL Controls, we can help you answer this question through services like digital maturity assessments, Smart Factory road-mapping, automation strategy development, and creating a business case. Find out more today.
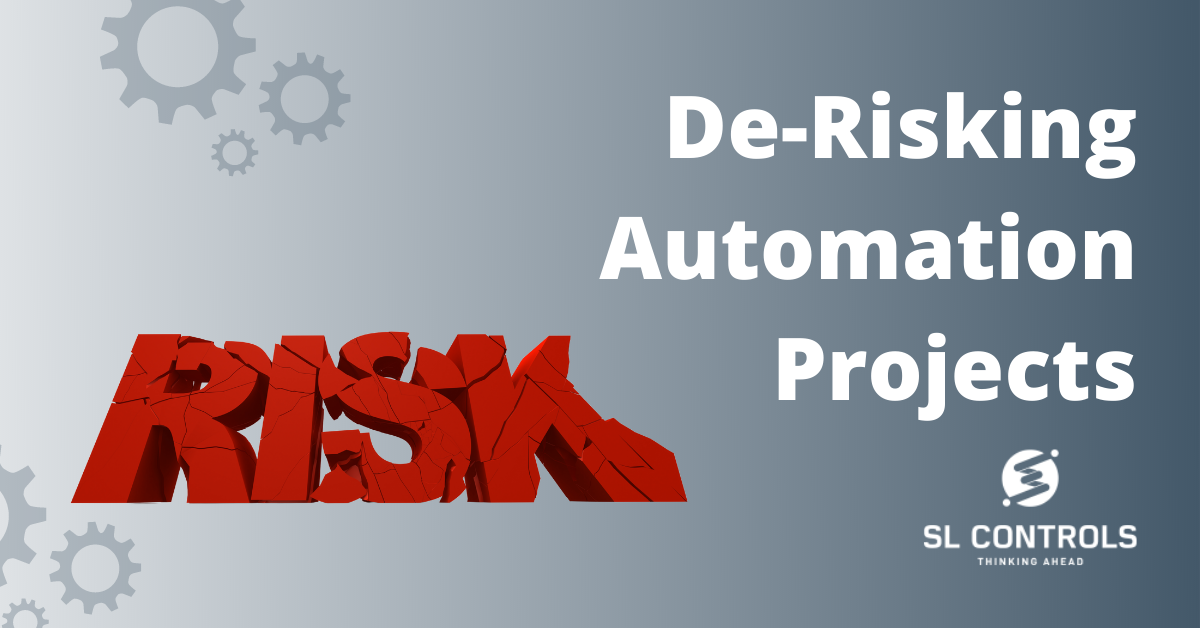
8 Essential Elements For De-Risking An Automation Project
Risks can enter an automation project at just about any stage. Those risks can result in serious consequences from budget and schedule overruns to unplanned downtime, disrupted supply chains, and more.
Therefore, it’s important to de-risk your automation project at every possible stage. This ensures errors are reduced to a minimum, as well as ensuring the project delivers on expectations.
We have a project delivery process at SL Controls that helps to reduce risks in all project phases. There are also factors relating to your organisation and operations that need to be considered. We’ll start with those.
Minimising Risks In Automation Projects – What You Can Do
There are five crucial areas you should look at to minimise risks in your automation project:
- Set clear goals – you should have a clear understanding of why you are embarking on the automation project and what you want to achieve. What are the objectives, what has to happen to meet those objectives, and how will you measure success?
- Senior leadership buy-in – getting senior leadership buy-in at the earliest possible stage will make the process smoother, as well as reducing risks.
- Resistance to change – are there people in the organisation who will resist the change that automation will bring? This situation is not unusual. The key is to ensure you have a well-thought-through plan of how you will deal with this resistance. Examples of things you can do include communicating effectively, addressing fears head-on, and offering training.
- Resources and expertise – what resources and expertise will you need for the successful delivery of the automation project? If you are not completely sure of the expertise that will be required, how will you get that information? What level of resources do you have in-house? What are the key skills and capabilities you will need from a third-party provider?
- Stakeholder communication – communication is a potential risk factor in automation projects as communication failures can lead to errors, delays, overruns, and other problems. Therefore, you need to develop an effective communication strategy that includes all stakeholders.
De-Risking Your Automation Project At Every Stage Of Delivery
At SL Controls, our project delivery processes focus on de-risking at every stage, from the pre-automation phase through to final commissioning and testing.
Central to this are eight essential elements to de-risking all automation projects.
1. Proof Of Principle
Proof of Principle (POP) involves proving the feasibility of achieving the desired outcomes for the project based on things like the technologies currently available, budget constraints, timelines, etc.
By going through the POP process, we can avoid pursuing goals or targets that are not feasible or achievable and, instead, make changes to achieve the desired outcome. This prevents wasted expenditure.
2. Design For Manufacturing
Design for manufacturing (DFM) is most commonly used when designing new products. It involves ensuring the design of a product makes it easy to manufacture within the cost target.
In relation to automation projects, we adapt DFM principles to ensure we don’t just create a fancy automation solution. Instead, our goal is to develop an automation solution that is reliable, and that improves several key metrics, i.e., OEE, output rate, quality, productivity, etc.
3. User Requirements Definition
A User Requirements Definition is a document we create that specifies what you, as our client, expect the automation project to deliver. It’s not a technical document but should include, among other things:
- Required functions and features of the solution
- Workflow of the solution
- Integration requirements
- Data requirements
- Regulatory requirements
- Life cycle requirements
In terms of the de-risking process, creating and agreeing on a User Requirements Definition is part of the project’s feasibility analysis. It also ensures everyone is on the same page.
4. Design Review Management
The design review is an essential part of de-risking automation projects. In regulated sectors, it’s also a compulsory part of the process and must be properly documented.
A design review tests and evaluates the design of the automation solution against the User Requirements Definition.
5. Factory Acceptance Testing
The goal of Factory Acceptance Testing (FAT) is to ensure the equipment, platforms, and components of the automation solution can deliver on requirements. It is a process that can highlight issues and errors, so it plays a key role in de-risking automation projects.
6. Logistics Management
Logistics management is often taken for granted in automation projects, despite the fact there are so many things that can go wrong, many of which can have significant consequences. A good example is a piece of equipment getting dropped and damaged. This could set a project back for weeks or months.
To mitigate these risks, we insist on using qualified and approved freight forwarders who take essential steps to ensure the smooth teardown, crating, and transportation of equipment and machinery. This includes:
- Mapping every aspect of the route
- Planning the equipment required
- Deciding on the crate specification
- Selecting appropriate bracing to secure equipment
- And more
7. Site Acceptance Testing
While the aim of a de-risking strategy is to eliminate risks at the earliest possible stages of an automation project, the Site Acceptance Testing stage is still important. It’s also an essential GMP requirement.
8. Final Commissioning
De-risking in the final commissioning phase includes IQ (installation qualification), OQ (operational qualification), and PQ (performance qualification).
De-Risking Strategy
By emphasizing de-risking in the earliest stages and then focusing on the elimination of risks through each subsequent stage, we ensure the successful and smooth delivery of automation projects, maximising your ROI.
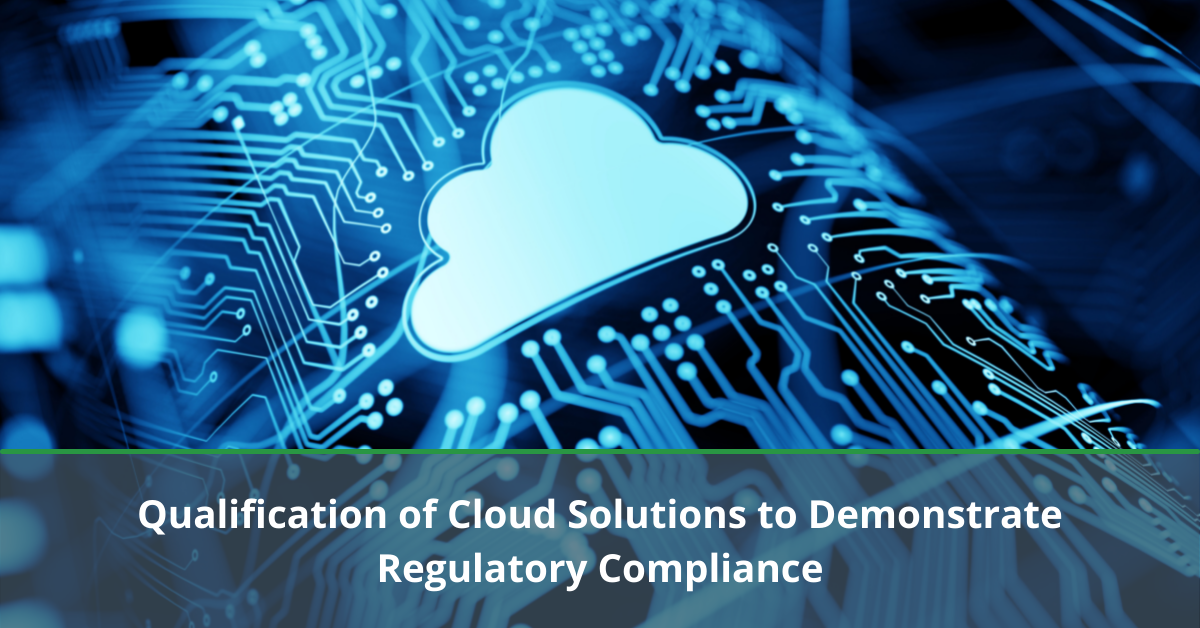
Qualification Of Cloud Infrastructure And SaaS To Demonstrate Regulatory Compliance
Cloud infrastructure solutions, as well as Software as a Service (SaaS), Infrastructure as a Service (IaaS), …
Qualification Of Cloud Infrastructure And SaaS To Demonstrate Regulatory ComplianceRead More »
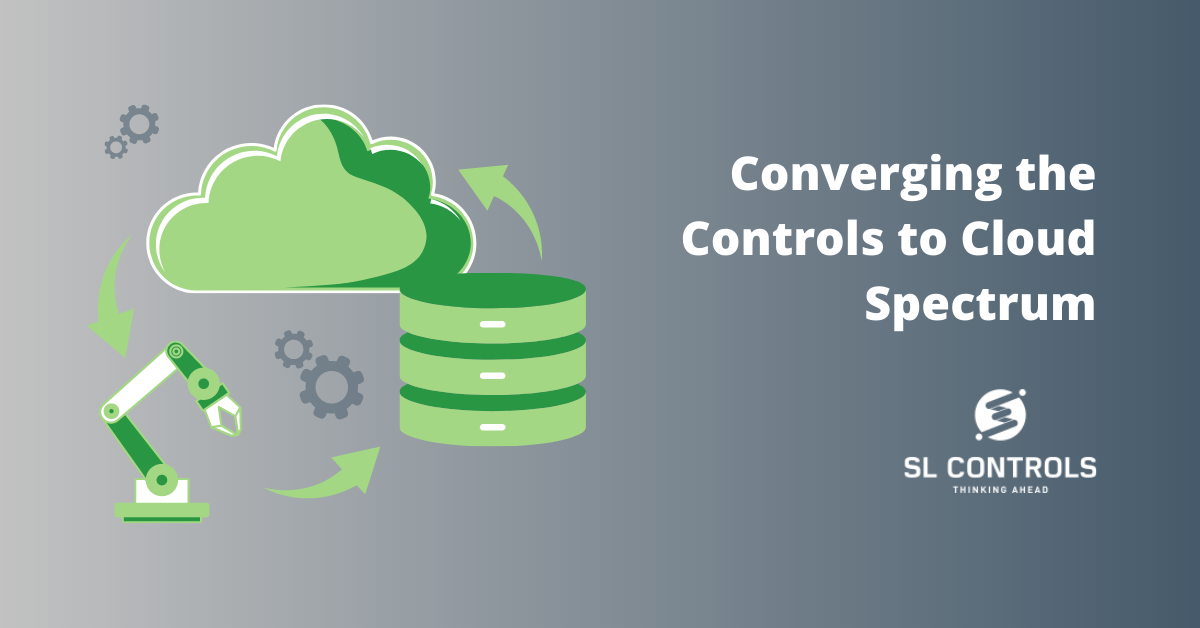
Bridging The Machine To Cloud Gap For Life Sciences And Technologies Manufacturers
Industry 4.0 as a concept provides manufacturers with impressive benefits and wide-ranging opportunities. …
Bridging The Machine To Cloud Gap For Life Sciences And Technologies ManufacturersRead More »
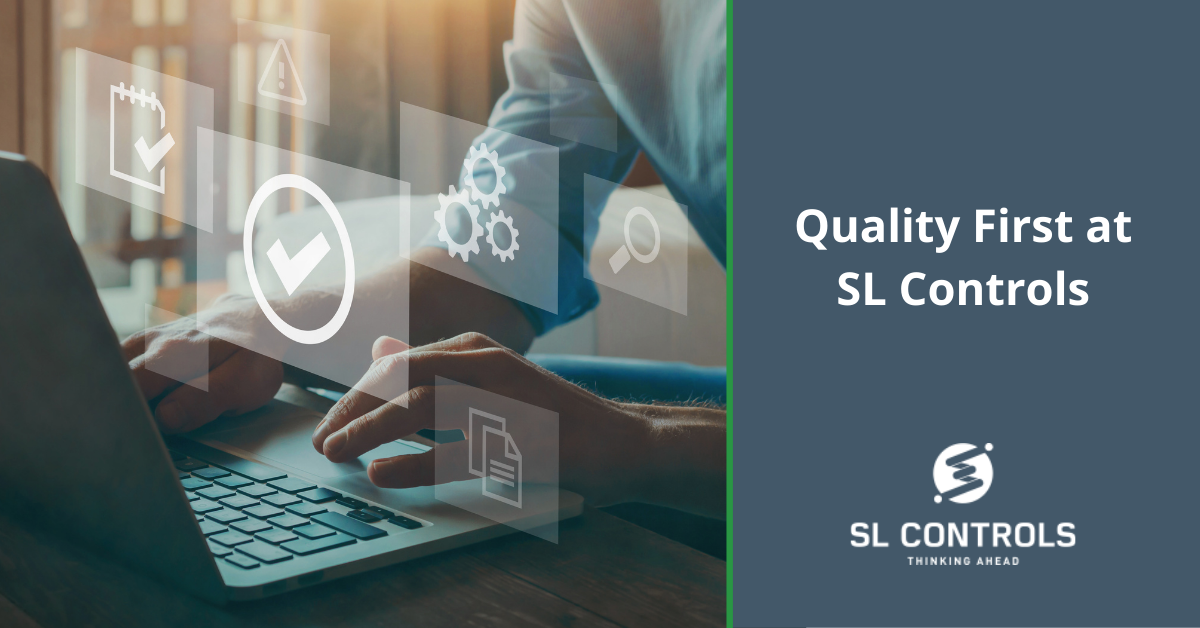
Putting Quality First At SL Controls
Like most businesses, there are several values and priorities that are important to us at SL Controls. …

Transitioning to Smart Manufacturing – A Practical and Cost-Effective Approach
The business case for implementing smart factory technologies is compelling, with tangible improvements in revenue, output, quality, and safety, alongside reduced costs. It is not surprising, therefore, that smart manufacturing technologies are becoming an increasingly important competition driver.
The technologies that are part of the Smart Factory include cloud computing, edge computing, vision systems, robotic process automation, predictive analytics, machine learning, artificial intelligence, big data, and industrial internet of things, as well as augmented, virtual, and mixed reality.
Each one individually has significant potential and creates opportunities for your business. When combined, the benefits increase considerably.
Implementing smart manufacturing solutions is not without risk, however, so where do you start? If you’ve already started, where do you go next? What are the practicalities of making the transition to smart manufacturing?
Important Practicalities to Consider
There are some important practical considerations to think about before embarking on major smart manufacturing projects. Many of these considerations relate to change management and include ensuring there is senior leadership buy-in, sufficient skills available for the initiative, and support for those involved.
Other considerations include the divide that sometimes exists in many manufacturing organisations between IT and OT. The success of smart manufacturing initiatives often hinges on these critical business functions working together.
Two other important considerations are worth mentioning:
- Integration – you will have different machines, equipment, devices, sensors, platforms, and systems that make up your manufacturing operations and supply chain management processes. The integration of these various technologies and machines is an important step.
- Connectivity – connectivity and the transfer of data are crucial to the implementation of smart manufacturing solutions, so it is essential to have a robust IT infrastructure to provide the required level of connectivity.
Finally, it is important to focus on business value when deciding on strategies and implementing smart manufacturing solutions. Without a proper focus on business value, improvements can be made in specific areas, but the benefits won’t extend much further. The best approach is to look at the overall objectives of the business to decide on the smart manufacturing technologies that offer the most value.
Progressing Towards a Smart Manufacturing Approach
You need to move to the next stage of your smart manufacturing journey, but what should you do first? How do you ensure you don’t take missteps? How do you progress without diverting significant resources? Can you get a short-term and medium-term return on investment as well as a long-term return?
Let’s look at three key strategies:
- Trial projects
- Structured incremental implementation
- Simulation tools
A combination of the three, depending on the status of your existing operations, is often the best approach to keep costs under control, maximise return on investment, and ensure the transition is as smooth as possible, particularly in relation to product output and customer impact.
Trial Projects
Trial projects can be a useful approach in a wide range of situations, not just at the start of your Smart Manufacturing journey. With a trial project, you can ringfence costs and structure the work parameters as tightly as you want.
This will let you identify risks and areas for improvement, and it will demonstrate where you may encounter resistance, bottlenecks, or barriers when you start to scale up.
In addition, a trial project will give you a better indication of the real return on investment you can achieve from transitioning to Smart Manufacturing.
Structured Incremental Approach
Whether you go with the trial project option or not, adopting a structured, incremental approach is almost always the best option.
How far you go and how quickly depends on your current circumstances and immediate plans. For example, it might save you in the long run if you increase the scale of a project if it requires a considerable investment in new equipment.
It’s important you don’t go too far too fast, however. Upgrading all your legacy systems in a short period of time is rarely the best option, for example. Rather than a big bang investment, the more successful approach is usually a carefully planned evolution.
The most obvious reason for this is the fact it might not be practical, for financial or other business reasons, to upgrade all legacy systems in a short space of time. Furthermore, it might not even be necessary, i.e., you might not need to upgrade all your legacy systems to achieve your Smart Manufacturing goals.
Simulation Tools
It is also possible to explore and analyse the implementation of Smart Manufacturing processes and technologies in your facility using simulation tools. One of the most effective is using digital twins.
By creating digital twins of your current equipment and processes, you can model various options and scenarios to identify the best approach, helping you decide on the next Smart Factory steps to take.
Starting and Continuing the Transition
Smart Manufacturing may be a buzzword, but the technologies involved are driving transformational change in manufacturing companies in all sectors, including the life sciences sector. Companies that take a strategic approach and continuously improve their operations with new smart factory initiatives will be best placed to respond to the needs of the market today and in the future.
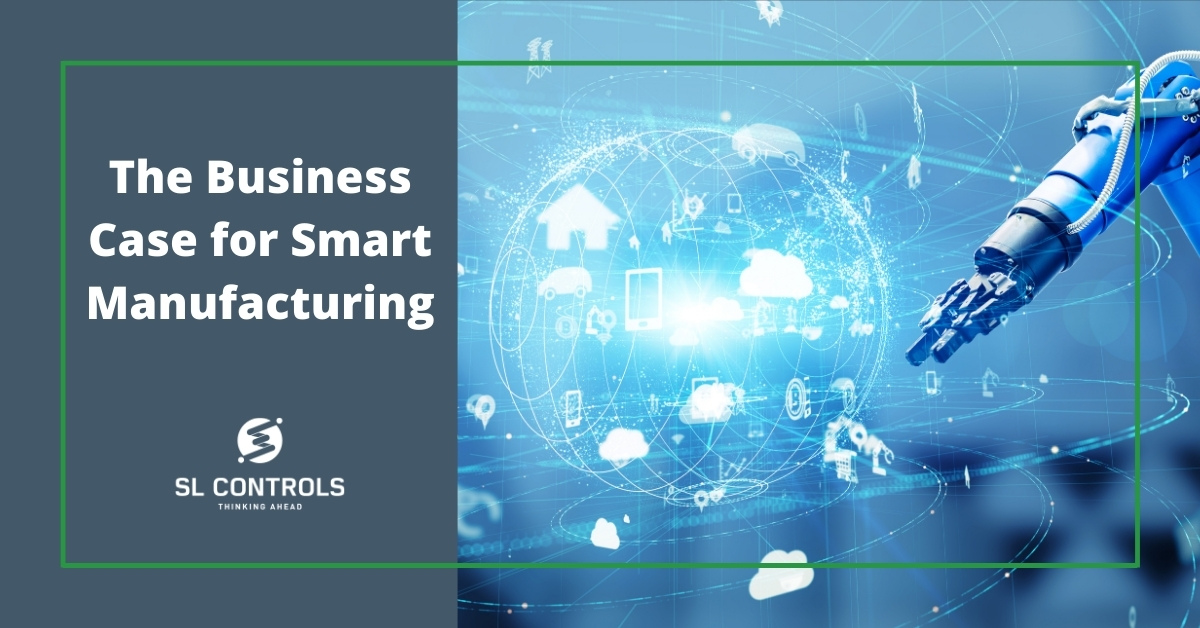
The Business Case for Smart Manufacturing
Advances in Smart Manufacturing technologies are changing the manufacturing sector forever. However, those technologies don’t change your core priorities and goals.
New technologies or not, you still need to deliver high-quality products that your customers need and want, plus you must maximise competitiveness, productivity, and profitability.
Marrying up a transition to Smart Manufacturing with your goals and priorities is not always easy.
We have looked at specific, practical, and cost-effective approaches to implementing Smart Manufacturing solutions and moving your production lines forward in other blog posts. A good starting point, though, is to consider the business case for doing so.
Of course, you will probably need to develop a specific business case for your facility. However, buying into the high-level pitch for Smart Manufacturing is an important first step.
Smart Manufacturing – The Business Case
As a component of Industry 4.0, Smart Manufacturing centres on digitalising manufacturing businesses and improving the ability of people and connected devices to work together.
The reality is the technologies that make smart manufacturing possible will have an impact on your business. This impact applies however quickly you proceed and how far down the Smart Manufacturing route you go in the near term.
Even if you do nothing regarding the implementation of Smart Manufacturing technologies in your facility over the next 12-24 months, by not moving forward, you risk falling behind or missing opportunities that could be beneficial to your business.
Why? Many of the challenges and opportunities that are becoming more important to the manufacturing sector are being driven by market trends, advances made by your competitors, regulatory requirements, and changing consumer behaviour and expectations.
Here are two examples by way of illustration:
Mass Customisation
Smart manufacturing technologies make it possible for manufacturers to move towards the mass customisation of products. This mass customisation trend will change the offering that is available to the consumers and users of the products you produce. In fact, marketplace expectations are already changing.
While industries like pharmaceutical and medical device manufacturing are not as far advanced as other industries, the direction of travel is firmly towards mass customisation. Manufacturing flexibility is increasingly important too.
New Product Introductions
The practical and regulatory requirements for introducing a new product on the market are as complex today as they have ever been. However, Smart Manufacturing technologies throw an important consideration into the mix.
Specifically, Smart Manufacturing technologies streamline and automate many NPI processes. Therefore, organisations that embrace Smart Manufacturing solutions will introduce new products faster while maintaining compliance and quality standards. This reduced NPI timescale greatly enhances competitiveness.
The Sooner the Better
The above are just two examples of the many ways that Smart Manufacturing can (and is) impacting your business. So, the summary is the sooner you get started with implementing Smart Manufacturing solutions, the better.
How you do that will depend on your business. The process requires a detailed assessment of the readiness of your organisation, as well as an analysis of where first to target Smart Manufacturing solutions with a focus on maximising improvements, delivering a healthy return on investment, and ensuring scalability for the future.
Benefits of Smart Manufacturing
- Improvements in OEE – overall equipment effectiveness.
- Increased efficiency, but not just in the operation of machines and equipment. Smart Manufacturing technologies also enable the more efficient use of resources, as well as delivering material efficiency benefits and helping make your operations more energy efficient.
- Reducing both planned and unplanned downtime through digital twin technologies, machine learning, and predictive analytics.
- Improved quality control.
- Opening up the potential of new business opportunities with the introduction of new product lines, mass customisation strategies, and more.
- More effective and efficient regulatory compliance processes.
- Increased output that will improve revenues and profits while also delivering capital expenditure avoidance.
- Improved customer satisfaction by consistently and reliably delivering high-quality products, in addition to responding quickly to queries and complaints.
- Building a closer direct connection with your customers.
- Increasing the variety of products that you can produce on a single production line.
- Overall improvements in productivity.
- Enhanced insight at all levels of the business, from supply chain management to how customers use products to predicting future market demands.
Drivers for Transitioning to a Smart Factory
When making a business case for Smart Manufacturing, it also helps to understand the drivers of change. Some of the most important of these drivers include:
- Customer demand and expectations – these constantly evolve, with one major current trend being mass customisation. Market factors that increase or decrease demand unexpectedly and/or in short periods of time are also factors.
- Agility and flexibility – i.e., ensuring your business is in a position to take advantage of the new opportunities that Industry 4.0 and Smart Manufacturing technologies present.
- Productivity and improving OEE – the constant push to improve performance and efficiency, particularly in the face of increasing demands.
- Availability of skills and resources – many businesses in a range of industries struggle to recruit and retain the operatives and technicians they need, so they are looking to technology as the solution.
- Compliance – additional compliance requirements on manufacturers, particularly in highly regulated sectors like pharmaceuticals and medical device manufacturing, results in a push for innovative solutions. Some of this comes from regulators, but manufacturers striving to keep compliance costs under control are also a factor.
- Business opportunities – Smart Manufacturing technologies have the potential to transform businesses, creating opportunities in new markets, product development opportunities, business model innovation, and more.
- Sustainability – sustainability is increasingly important in all businesses. Smart Manufacturing technologies can increase energy efficiency and reduce waste across the entire product lifecycle.
Getting Started with Smart Manufacturing
The business case for Smart Manufacturing is strong, although the way it is presented and tailored will differ depending on your organisation. To move to the next stage, find out more about the practical and cost-effective ways to transition your current facility using Smart Manufacturing processes, methods, and technologies.
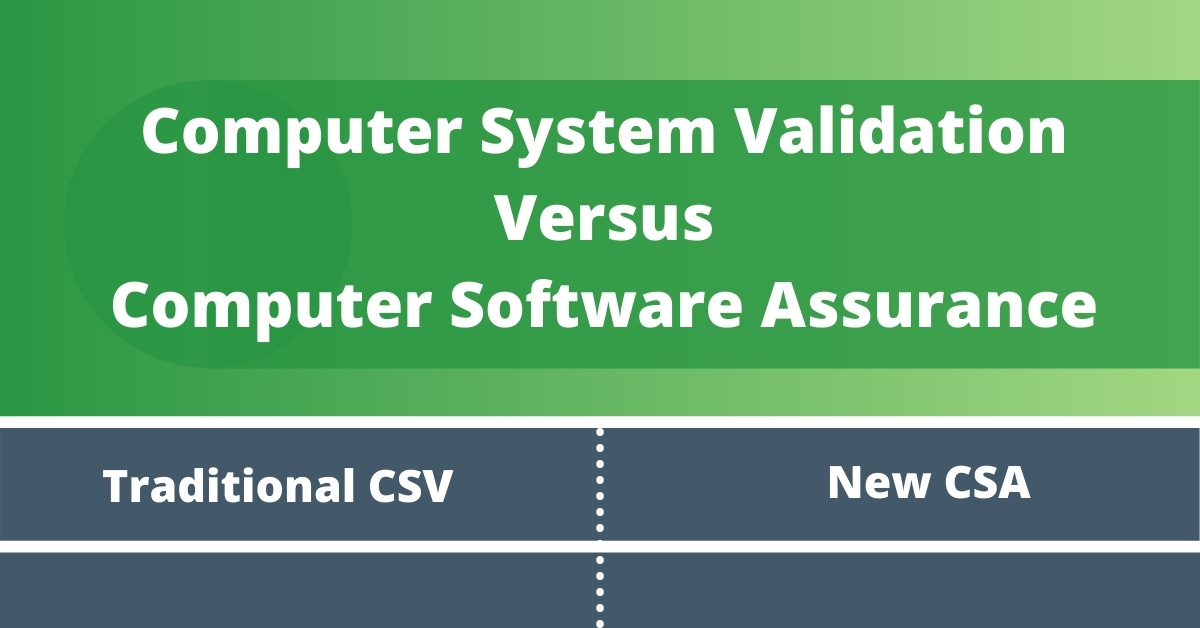
Infographic: Computer System Validation Vs. Computer Software Assurance
The FDA (US Food and Drug Administration) is due to release guidance on Computer Software Assurance. That guidance aims to put critical thinking at the centre of Computer System Validation (CSV) processes.
In our latest infographic, we highlight the main differences between traditional CSV and the new Computer Software Assurace (CSA) approach.
Traditional CSV
- Perceived as a barrier to automated solutions and innovation
- All software validated as if it’s product software
- The primary focus is securing evidence for auditors
- Duplication of vendor documentation and effort
- High occurrence of deviations due to tester error
New Computer Software Assurance
- A more flexible, less burdensome, and faster risk-based approach
- Various assurance approaches depending on the system/feature risk
- Apply critical thinking to ensure the software is safe and meet its intended use
- Reduced testing activities resulting from better supplier qualification and collaboration
- Reduced number of deviations due to tester error
« Previous 1 … 4 5 6 7 8 … 18 Next »