Blog
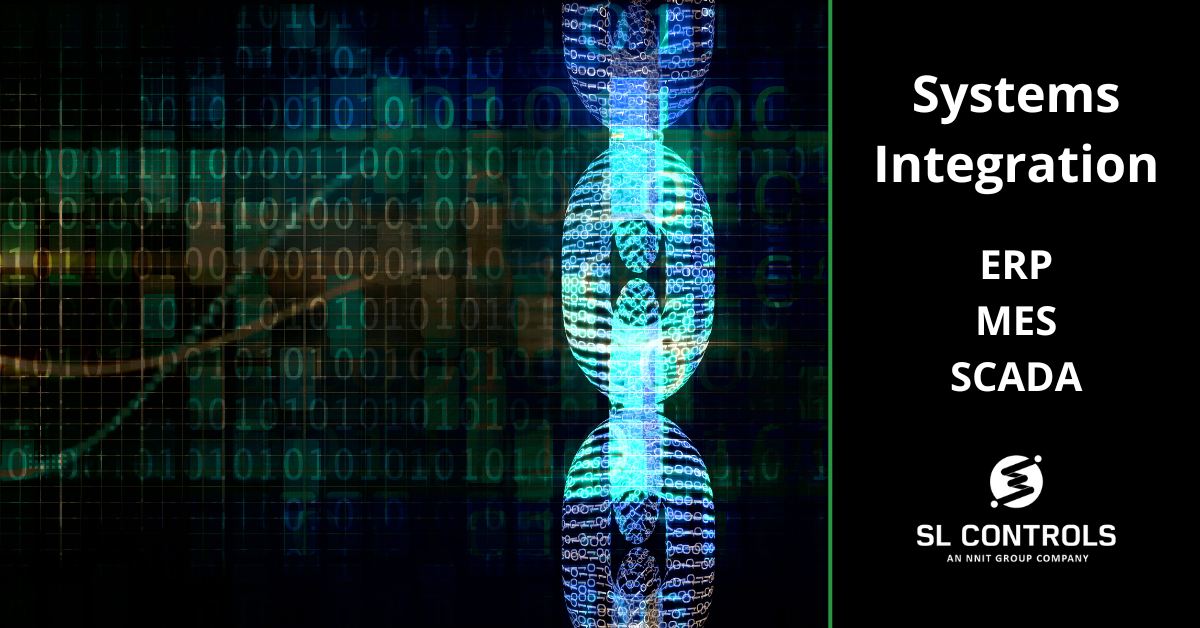
The Importance of Systems Integration to Optimize Your SCADA, MES, and ERP Systems
Systems integration is an essential part of any modernization and improvement project in manufacturing organizations. Systems integration is also the cornerstone of Industry 4.0, and it is central to the development of the smart factory of the future. What does systems integration mean in practice for manufacturers in the life sciences sector? One of the primary objectives is to optimize SCADA, MES, and ERP systems.
This could apply to existing systems as well as during the implementation of new platforms. For example, you might already have SCADA (supervisory control and data acquisition) and ERP (enterprise resource planning) systems and are now exploring the benefits and ROI of an MES (manufacturing execution system) platform. In this situation, systems integration is essential for the successful implementation of your new MES.
Of course, SCADA, MES, and ERP systems are not the only platforms that are important to your operations. Other equipment, applications, and platforms could also benefit from being part of your systems integration plans. Examples include LIMS (laboratory information management systems), QMS (quality management systems), and PLM (product lifecycle management) platforms.
That said, SCADA, MES, and ERP are arguably the three most important levels of integration to achieve because of where they sit in a manufacturing organization’s technology stack. In simple terms:
- ERP – office and business operations
- SCADA – the automation of processes on the production line
- MES – the link between the two
Making Use of Data and Getting the Most Out of Your Systems
To understand the importance of systems integration for MES, SCADA, and ERP platforms, let’s first look at what each platform is responsible for. There are some overlaps depending on the system and vendor that you choose, but the following descriptions apply in most situations.
What is an ERP Platform?
ERP platforms facilitate, manage, and automate a wide range of the administrative and operational functions of your business. This includes everything from finance and purchasing to sales, customer service, and logistics.
What is SCADA?
SCADA systems control and monitor the equipment on your production line, usually through PLCs (programmable logic controllers). They collect data, monitor alarms, and enable real-time monitoring of your production lines and equipment.
What is an MES Platform?
MES platforms manage the processes involved in turning raw materials into new medical devices or pharmaceutical products. MES platforms can also optimize OEE, and they have features that can include scheduling, performance analysis, raw material tracking, quality management through statistical process control, and production optimization.
Connecting the Three Layers
SCADA, MES, and ERP systems all produce and monitor data, and they all automate and optimize processes. Without effective integration, however, they will operate in isolation, so they will never achieve full optimization. This is only possible when they are connected and working together, with data flowing seamlessly between the platforms.
By integrating your SCADA, MES, and ERP, you will have a single source of truth covering your entire operation – at office level, on the factory floor, and everything in between.
The Benefits of Integrating SCADA, MES, and ERP
- Reduces production line downtime and improves OEE
- Improved batch control processes
- Streamlined processes from the factory floor to office-based functions
- Improved supply chain resilience and efficiency
- Reduced waste, including waste from raw materials, overproduction, transport costs, and energy use
- Move to data-driven decision-making (both manual and automated data-driven decision-making) with the availability of real-time data streams covering production, quality, supply chain, finance, planning, procurement, maintenance, and more
- Eliminate mistakes that come from manual data handling
- Enhanced oversight at all levels, including operator, engineering, management, and C-suite
- Improved customer, user, and patient experience
- Enhanced competitiveness
- Reduced costs through efficiency savings, productivity improvements, and greater levels of automation in workflows, processes, and data handling
- Improved alignment between the different functions in your business, including those where there is currently minimal alignment
- Improved compliance processes
What About the Challenges of Systems Integration?
There are challenges to overcome with systems integration projects that involve SCADA, MES, and ERP platforms. The main challenges concern the disconnect between OT (operational technology) and IT (information technology). Both OT and IT produce, store, and use data in different ways, and they use different languages, hence the disconnect.
OT is the system used on the factory floor, while IT is for business and administrative operations. SCADA and MES typically come under the OT umbrella, while ERP is an IT system.
Therefore, solutions need to be developed to facilitate the integration of these platforms and ensure a seamless transfer of data.
Getting the Support that You Need
At SL Controls, we have extensive expertise in systems integration projects, from overcoming the challenges described above to ensuring your SCADA, MES, and ERP platforms are fully optimized. Our expertise will also ensure you get maximum returns from the investments you have made in these systems. Get in touch today to find out more and discuss your requirements.
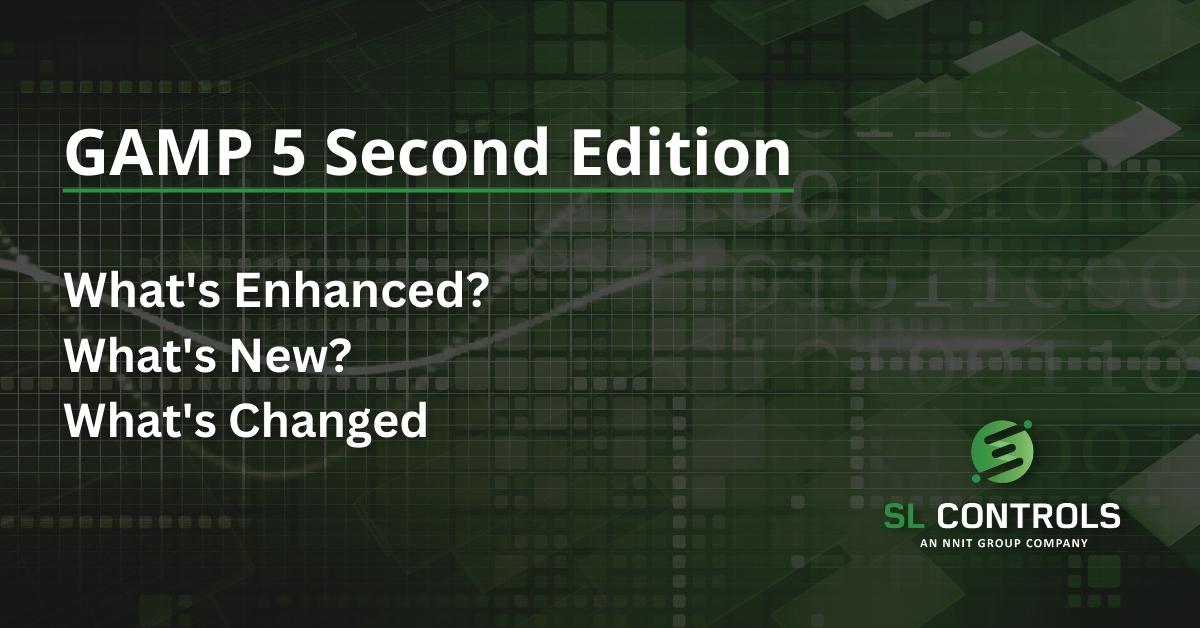
A New Look – GAMP 5 Second Edition
GAMP 5 is one of the most important validation and computer system assurance guides for the life sciences industry. This year saw the release of GAMP 5 Second Edition. So, what’s new and what’s changed?
The original GAMP 5 was published in 2008, and it went on to become the globally accepted guide for the commissioning, operation, and retirement of computerized systems. Nevertheless, technology has moved on since its release, advancing in areas such as cloud computing, big data, artificial intelligence, and agile software development.
It was time for a refresh, and the Second Edition of GAMP 5 was released in July 2022. Here are some of the notable changes.
Non-Linear Approach to Validation
GAMP 5 Second Edition has removed the assumption of a universal linear approach to software development and, with it, the V-model terminology.
The updated edition instead supports iterative and incremental models, such as agile methodologies for software development and validation. Agile methodologies allow for the continuous delivery of working software developed in iterations.
This change shifts the focus away from the delivery of fixed and prescriptive documents. The focus is now on risk-based records of information that take into consideration modern software lifecycle methodologies.
The linear approach is still applicable for systems that are well established and where requirements are fully known. Commercial off-the-shelf applications are a good example. However, for systems that are higher in complexity and novelty, iterative and incremental models may be more appropriate.
The new Appendix D8 has been included in the GAMP 5 Second Edition to specifically address Agile Software development.
Critical Thinking
There has been great emphasis recently that validation should be increasingly based on product, data, and process knowledge. Critical thinking has become a hot topic, and it is a key pillar of the FDA’s new Computer Software Assurance draft guidelines, released in September 2022.
GAMP 5 Second Edition and the FDA’s draft guidelines have recognized that the use of rigid tables, overly prescriptive templates, and tick-the-box methods have become commonplace for many companies. This trend impedes critical thinking and can, regrettably, inhibit innovation and the adoption of new technologies.
By facilitating critical thinking, teams can move away from one-size-fits-all, document-heavy validation approaches. Teams can instead apply informed decision-making and good judgment on where and how to scale quality and compliance activities.
Critical thinking gets its own appendix in GAMP 5 Second Edition. This appendix provides many examples of where critical thinking can be applied throughout the system life cycle.
The Use of Software Tools
The replacement of paper with automated processes is transforming the manufacturing and quality landscape. To make this transition, life sciences companies are increasingly using software tools, so much so that a new Software Tools appendix has been added to GAMP 5 Second Edition. Topics such as selection, risk assessment, and life cycle management are all covered in this appendix.
GAMP guidance and the FDA CDRH Case for Quality program strongly encourage the use of software life cycle management tools and automation, which can bring great quality benefits, and have low GxP risk.
– GAMP 5 Second Edition Appendix D9
Software tools generally do not directly support GxP critical processes, plus they can be used anywhere in the business. GAMP 5 Second Edition also points out that software tools are especially prevalent in IT Infrastructure processes.
An important takeaway is that software tools are classed as GAMP Software Category 1 in the second edition of GAMP 5. This is the lowest risk category, meaning that software tools do not require computerized system validation. There should instead be a risk-based approach with the software managed through the application of good IT practices, such as ITIL.
GAMP 5 Second Edition now acknowledges that:
Much information will never exist on paper, or even in the form of a document.
The guidance also states in Appendix M9:
There is no need to create documents simply for the sake of having a document in case of regulatory inspection. If it is not useful for managing the application in a state of control and it is not needed.
Data retained in native software tools offer more robust search capabilities compared to paper records.
Enable Innovation
One of the main challenges within a highly regulated industry is to continually ensure patient safety and product quality while allowing enough space for innovation growth.
A dogmatic focus on regulatory compliance has caused companies to apply unnecessarily rigid and prescriptive approaches that are disproportionate to the infrastructure of a system and its associated risks.
Recognizing that traditional linear or waterfall methodologies cannot be a one-size-fits-all approach for every case allows lifecycle activities to be scaled according to risk, complexity, and novelty. Hence, there is a welcomed introduction of agile approaches in both GAMP 5 Second Edition and the FDA’s Draft Guidance for Computer Software Assurance for Production and Quality System Software.
Additionally, GAMP 5 Second Edition has introduced additional appendices to address new software technologies, such as the blockchain (distributed ledger systems), artificial intelligence, and machine learning. This is to keep pace with the rapidly changing technology landscape that is currently unfolding within the life sciences sector.
Final Thoughts
GAMP 5 Second Edition is an important and welcome update for the sector. It is an evolutionary change that complements the still relevant key principles of GAMP 5, while also underlining important points within the guidance and introducing new topics that reflect current technology.
Technologies evolve at a rapid pace. The publication of GAMP 5 Second Edition will enable greater innovation and more cost-effective assurance of computer systems.
As a company that is involved in both the development and validation of software systems for life sciences companies, we are excited at SL Controls to embrace the changes outlined in the new GAMP 5 edition.
GAMP 5 Second Edition is a tool that can make achieving compliance easier, but for it to do so, it must keep up with the rapidly changing technology landscape. Perhaps 14 years was too long to wait for this new edition. That said, good things come to those who wait – and this new edition is certainly a good thing!
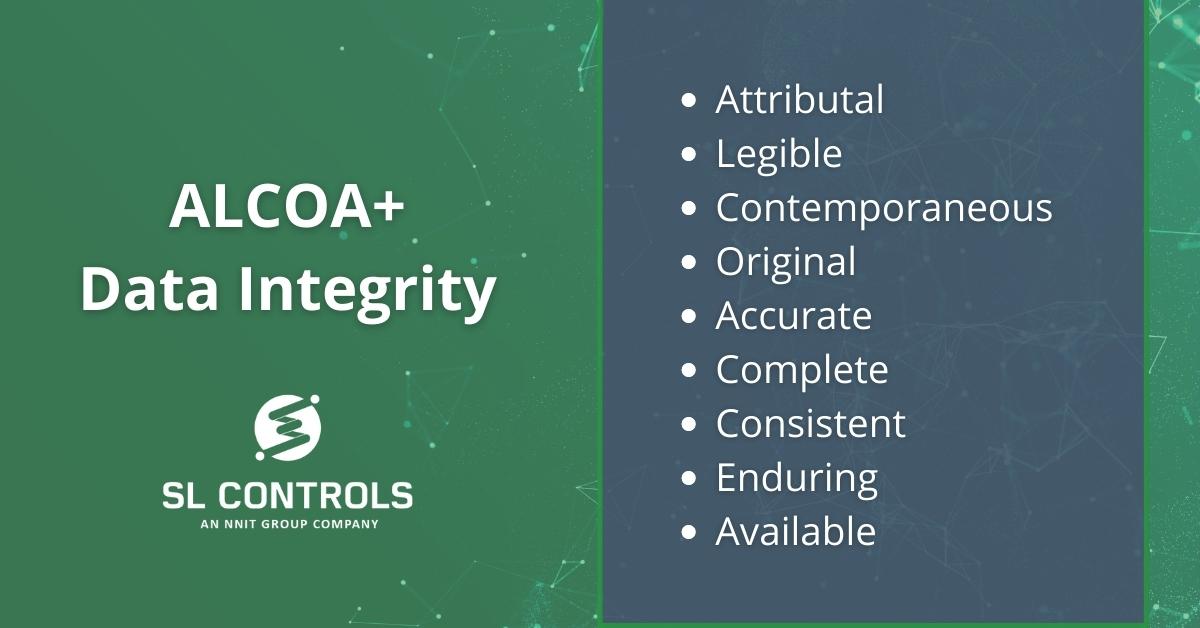
What is ALCOA+ and Why Is It Important to Validation and Data Integrity
ALCOA+ is a set of principles that ensures data integrity in the life sciences sector. It was introduced by, and is still used by, the FDA – the US Food and Drug Administration. It has relevance in a range of areas, particularly in relation to pharmaceutical research, manufacturing, testing, and the supply chain.
As well as being crucial for compliance reasons, ALCOA+ principles are becoming increasingly important to GMP (Good Manufacturing Practices). Their relevance is also growing as manufacturers in the life sciences sector continue to implement Industry 4.0 solutions and processes.
The Importance of Data Integrity
Data has always been important in pharmaceutical manufacturing and research. However, a range of different factors means the importance of data is growing exponentially. Key to this is the move away from paper-based records to digital data collection, storage, and processing.
Advances in technology, increasing levels of automation, the globalization of the life sciences sector, and the use of contract manufacturers mean it is also now more important than ever to ensure data integrity through the entire product lifecycle.
Other drivers for the growing importance of data include:
- The importance of ensuring the quality and safety of medicines
- Enhanced regulatory requirements in relation to data, traceability, and audit trails
- The evolving expectations of consumers and end users
- The increasingly competitive nature of the pharmaceutical industry
- The fact that almost all Industry 4.0 technologies and systems rely on deeper levels of equipment integration and a vastly increased volume of digital data transfer
You can’t just have data, though, as data integrity is as important as the data itself. When you have data integrity, you have data you can use and rely on. That’s where ALCOA+ comes in.
Data Integrity and GMP Records
The ALCOA principles that ensure data integrity apply to the following types of GMP records:
- Electronically recorded – data recorded using equipment from simple machines through to complex and highly configurable computerized systems
- Paper-based – a manual recording on paper of an observation or activity
- Hybrid – where both paper-based and electronic records constitute the original record
- Other – this includes photography, images, chromatography plates, and more
ALCOA and ALCOA+ Principles
ALCOA is an acronym for the original five principles of data integrity. Those principles are:
- Attributable
- Legible
- Contemporaneous
- Original
- Accurate
These original ALCOA principles have since been updated to ALCOA+. The original principles remain with four additions:
- Complete
- Consistent
- Enduring
- Available
Let’s look at each of the principles in more detail.
Attributable
To ensure collected, generated, or updated data is attributable, the following must be recorded:
- The identity of the person, system, sensor, equipment, or device that collected, generated, or updated the data
- The source of the data
- The date and time
The above applies whether the data is collected, generated, or updated automatically or manually.
Ensuring data is attributable is not a technical issue, as all modern (and many old) systems and software applications have the above capabilities. The main challenges come with procedures and policies.
An example is password integrity, where one password is used by multiple workers. When this occurs, data that is collected, generated, or updated is not attributable.
Legible
Ensuring data is legible is about more than being able to clearly read the data, although that is important in situations where manual record-keeping takes place. Being able to make out words and figures is much less of a problem with electronic data, though.
That said, legibility still has relevance when data is digitally created, generated, or updated, as it is essential that data can be read and understood years and even decades after it’s recorded. This point is as relevant to digitally recorded data as it is to data recorded in notebooks.
So, it’s important to avoid using clichés and unusual phraseology as this may be difficult to decipher in the future without getting clarification from the originator of the data, a person who may no longer be available.
Using consistent, straightforward language throughout an entire organization, regardless of locality, is the best approach.
One final point to consider in terms of the legibility of data is that data collected, generated, or updated must be permanent.
Contemporaneous
It’s essential that individuals or systems record data whenever an activity or action takes place. With electronic data, timestamping is usually normal practice, although there are some points that should be considered. This includes ensuring data operations are not held in a queue that could delay timestamping, while also ensuring system clocks are accurate and time zones are recorded.
In general, though, contemporaneous data recording is another point that has more relevance to manual record-keeping. The main aim is to avoid the practice of creating or updating data at some point in the future. When data is recorded after an event or action, mistakes can happen, i.e., elements can be forgotten, parts can be left out, and information can be recorded inaccurately.
Original
Records should be original rather than copies or transcriptions. Again, this applies mostly to manual record-keeping. For example, you should not write information on a scrap of paper with the intention of completing the main record later, as this can result in errors.
Instead, the original recording of the data should be the main record, whether that record is on paper or on a digital system. With digitally recorded data, it is also important there are technical and procedural processes in place to ensure an original recording of data cannot be changed.
Any analysis, reports, or calculations based on data collected, generated, or updated should be traceable back to the original source.
Furthermore, copies of an original record should be formally verified as being a true copy, and they should be distinguishable from the original. The original version of the data should also be preserved, even when copies exist.
Accurate
All records should reflect the reality of what happened and should be error-free. Also, there should be no editing of the original information that results in that information being lost.
If changes are necessary, those changes must be documented in a way that makes it possible to refer back to the original information. Nothing should be removed, blocked out, or deleted.
When recording data electronically, the system must have built-in accuracy checks and verification controls. Measurement equipment should be regularly calibrated as part of this process.
Complete
All recorded data should have an audit trail to show nothing has been deleted or lost. This doesn’t just cover the original data recording, but also metadata, retest data, analysis data, etc. There should also be audit trails covering any changes made to the data.
Consistent
This primarily means ensuring data is chronological, i.e., has a date and time stamp that is in the expected sequence. Changes made to an original data recording should be timestamped.
Enduring
While durability is a factor in many of the above data integrity principles, ALCOA+ places specific emphasis on ensuring data is available long after it is recorded – decades in some situations.
For digitally recorded data, specific steps should be taken to ensure data is enduring, including putting in place robust and tested data backup systems as well as disaster recovery plans and uninterruptable power supplies. Cybersecurity is also an important consideration.
Available
Data must not only exist, but it must also be accessible. So, data storage systems should be searchable, with data properly indexed and labeled. The most efficient way of achieving this is normally by recording data electronically.
By being available, the data must be readable at any time during the retention period. This could be for a range of purposes, including audits, reviews, and inspections.
The Data Integrity Lifecycle
ALCOA+ principles apply throughout the entire data lifecycle:
- Creation – from sensors, systems, operators, etc
- Processing – during analysis, calculations, and comparisons
- Use – reviews, reporting, and analysis
- Retention and retrieval – storage of data as well as retrieval for auditing and other purposes
- Destruction – the destruction of data at the end of the retention period
The Importance of Data Integrity in the Life Sciences Sector
Data integrity is essential to all validation processes in pharmaceutical and medical device manufacturing facilities. Understanding and following the ALCOA+ principles will help you ensure data integrity, especially when selecting data solutions and implementing data recording and documentation protocols.
With data integrity now so intertwined with product quality, patient safety, and regulatory compliance, following the ALCOA+ principles should be a high priority for all life sciences sector manufacturers.
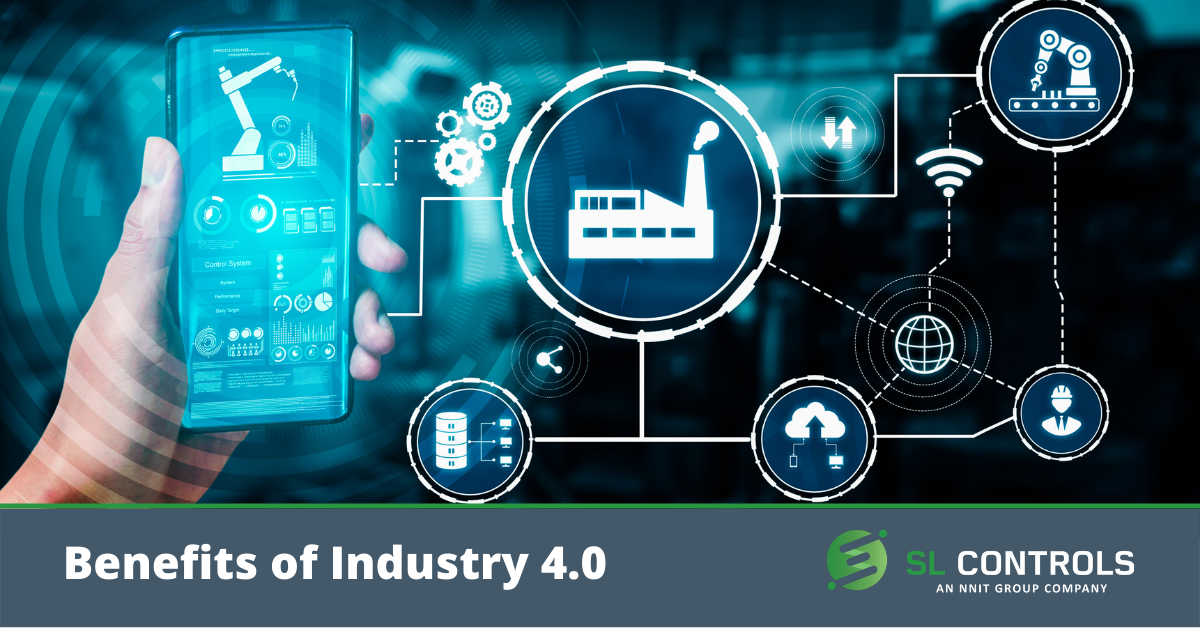
Benefits of Industry 4.0
The benefits of Industry 4.0 technologies, processes, and systems include improved productivity and efficiency, better flexibility and agility, and increased profitability. Industry 4.0 also improves the customer experience, including through more personalized and intelligent products.
Understanding and then contextualizing these benefits is important, particularly in highly regulated industries like medical device, pharmaceutical, and biopharmaceutical manufacturing. Any investment you make in technology, improved manufacturing processes, or enhanced systems must also take into account compliance, quality, and patient safety.
It is essential that you get a return on investment too.
So, what are the benefits that Industry 4.0 technologies, processes, and systems can bring to your production lines and business? We have split them into four categories with a specific focus on high-speed, highly regulated production facilities in the life sciences sector:
- Manufacturing benefits of Industry 4.0
- Quality and compliance benefits of Industry 4.0
- Customer and patient benefits of Industry 4.0
- Operational Benefits of Industry 4.0
Manufacturing Benefits of Industry 4.0
Improved Productivity and Less Machine Downtime
In simple terms, Industry 4.0 technologies enable you to do more with less. In other words, increasing throughput while allocating your resources more cost-effectively and efficiently.
Your production lines will also experience less downtime because of deeper levels of integration, enhanced machine monitoring, and automated/semi-automated decision-making. OEE (Overall Equipment Effectiveness) will improve, too, as your facility moves closer to becoming an Industry 4.0 Smart Factory.
Improved Efficiency
Multiple areas of your production line will become more efficient as a result of Industry 4.0-related technologies. Some of these efficiencies are mentioned above – less machine downtime as well as the ability to make more products and make them faster.
Other examples of improved efficiency include faster batch changeovers, automatic track and trace processes, and automated reporting. NPIs (New Product Introductions) also become more efficient as does business decision-making.
Optimised Supply Chain Management and Security
With Industry 4.0 technologies, processes, and systems, you will have better visibility across your entire supply chain. Your supply chain will also become better connected, enabling real-time monitoring with enhanced communication and collaboration.
This can, for example, make it possible to identify bottlenecks and other supply chain problems before they have an impact on production line output. Having this advanced knowledge means you can take mitigation steps.
Your supply chain will also become more resilient and agile, improving your ability to respond to changing market conditions and customer demands.
Optimized Product, Production Line, and Factory Lifecycles with Digital Twins
Digital twin technologies capture data in the physical world to create a digital replica that updates in real time. That replica could be a twin of a product, a production line in your facility, or your entire factory.
Having this digital twin allows you to optimize performance and efficiency and test different scenarios without impacting real-world output. You will also be able to identify areas of innovation and improvement.
Empowered People
With Industry 4.0 technologies, your people will have access to better data to give them enhanced oversight as well as the ability to take data-driven decisions.
Furthermore, you can eliminate the need for your people to work on repetitive tasks. With automation technologies and advanced workflows taking on repetitive tasks, your team can concentrate their efforts on value-adding tasks.
Increased Knowledge Sharing and Collaborative Working
Traditional manufacturing plants operate in silos. Individual facilities are silos as are individual machines within a facility. This results in minimal collaboration or knowledge sharing.
Industry 4.0 technologies allow your production lines, business processes, and departments to communicate regardless of location, time zone, platform, or any other factor. This enables, for example, knowledge learned by a sensor on a machine in one plant to be disseminated throughout your organization.
Best of all, it is possible to do this automatically, i.e., machine-to-machine and system-to-system, without any human intervention. In other words, data from one sensor can instantly make an improvement across multiple production lines located anywhere in the world.
Flexibility and Agility
The benefits of Industry 4.0 also include enhanced flexibility and agility. For example, it is easier to scale production up or down in a Smart Factory. It is also easier to introduce new products to the production line as well as creating opportunities for one-off manufacturing runs, high-mix manufacturing, and more.
Quality and Compliance Benefits of Industry 4.0
Makes Compliance Easier
Complying with regulations doesn’t have to be a manual process in industries like pharmaceutical and medical device manufacturing. Instead, Industry 4.0 technologies make it possible to automate compliance, including track and trace, quality inspections, serialization, data logging, and more.
Improved Product Quality
Industry 4.0 solutions can move quality functions from inspection rooms to the production line. This can mean real-time, in-line inspection with increased automation. The result is an inspection process that evolves from a go/no-go approach to one that is continuously measuring and analyzing to improve processes and identify quality issues so they can be corrected before they get to a failure stage.
An increase in automation will also reduce human error in the quality function and automate the collection, transmission, and storage of data.
Customer and Patient Benefits of Industry 4.0
Better Customer Experience
Industry 4.0 also presents opportunities to improve the service you offer to customers and enhance the customer experience. For example, with automated track and trace capabilities, you can quickly resolve problems. In addition, you will have fewer issues with product availability, product quality will improve, and you can offer customers more choice (see the point about increased profitability below).
Personalized Products
Given the benefits they offer to patients, the medical device and pharmaceutical industries are moving closer to personalized products. For production facilities, this means mass customization and increasingly smaller batch sizes down to as low as batch sizes of one.
With Industry 4.0 solutions, it is possible for manufacturers in the life sciences sector to personalize products within a high-speed mass production environment.
Intelligent Products, Particularly in the Medical Device Industry
Products across all industries are becoming more intelligent, including medical device products. Technologies like sensors, 5G, and the industrial internet of things (IIoT) make it possible to develop connected products that can share a wide range of information. This includes:
- Patient health data to enhance monitoring, treatment, and diagnosis
- Usage data to monitor the performance of the device
- Product data to help R&D teams develop improvements to existing products as well as new products
Intelligent products that are made possible with Industry 4.0 technologies can also perform multiple functions, including monitoring multiple health data points.
Operational Benefits of Industry 4.0
Reduces Costs
Becoming a Smart Factory does not happen overnight, and it won’t happen on its own. To achieve it, you need to invest, so there are upfront costs. However, the cost of manufacturing at your facilities will fall as a result of Industry 4.0 technologies.
Primary drivers for these reduced costs include:
- Better use of resources
- Faster manufacturing
- Less machine and production line downtime
- Fewer quality issues with products
- Less resource, material, and product waste
- Lower maintenance costs
- Lower overall operating costs
- Creation of innovation opportunities
Industry 4.0 technologies also give you a greater knowledge of the manufacturing process, supply chains, distribution chains, business performance, and even the products you manufacture. This creates opportunities to innovate, whether that is changing a business process, developing a new product, optimizing a supply chain, improving OEE, and more.
Enhanced Potential for Innovation
The enhanced potential for innovation delivered by Industry 4.0 is a result of many of the points already highlighted:
- Digital twin technologies
- Knowledge sharing
- In-line real-time inspection processes
- Product personalization and technologies that enable intelligent products
- Increased automation of repetitive workflows that enable staff to focus on value-adding tasks
Improved Decision-Making
Data is a key element of Industry 4.0 and smart manufacturing processes as machines and systems need to become more integrated so that data can be captured and used. This makes it possible to move to true data-driven decision-making in medical device and pharmaceutical manufacturing facilities. There is also the potential for machines to make decisions based on data, enhancing automation even further.
There is a range of benefits when you move to data-driven decision-making, including improving forecasting accuracy.
Higher Revenues
Many of the above points can result in higher revenues for your production facility. For example, by fully automating your production line and implementing other Industry 4.0 technologies, you could add a new shift with minimal staffing costs to meet an uptick in demand or compete for a new contract.
Increased Profitability
Increased profitability comes as a result of many of the points above, including higher revenues with reduced costs.
Furthermore, Industry 4.0 technologies enable you to produce higher quality, higher margin, and/or more innovative products. For example, Industry 4.0 technologies make it possible to offer customers personalized products while still using mass production methods to make those products.
Summary
The benefits of Industry 4.0 span manufacturing, business operations, compliance, quality, and the customer experience. As a result, the technologies and solutions that come under the Industry 4.0 umbrella are transforming manufacturing industries across the world.
While industries in the life sciences sector are generally behind other industries in terms of Industry 4.0 evolution, there are significant gains that can be achieved through careful planning.
Additionally, regulators are adapting to the realities of digital transformation and Industry 4.0, enhancing the potential even further. Other drivers are also accelerating the push towards Industry 4.0 solutions, including challenges in recruitment and the need to increase resiliency. With the benefits outlined above, it is also possible to get a healthy return on investment.
Staying competitive in a digitally transformed world is about continuous improvement with an Industry 4.0 focus.
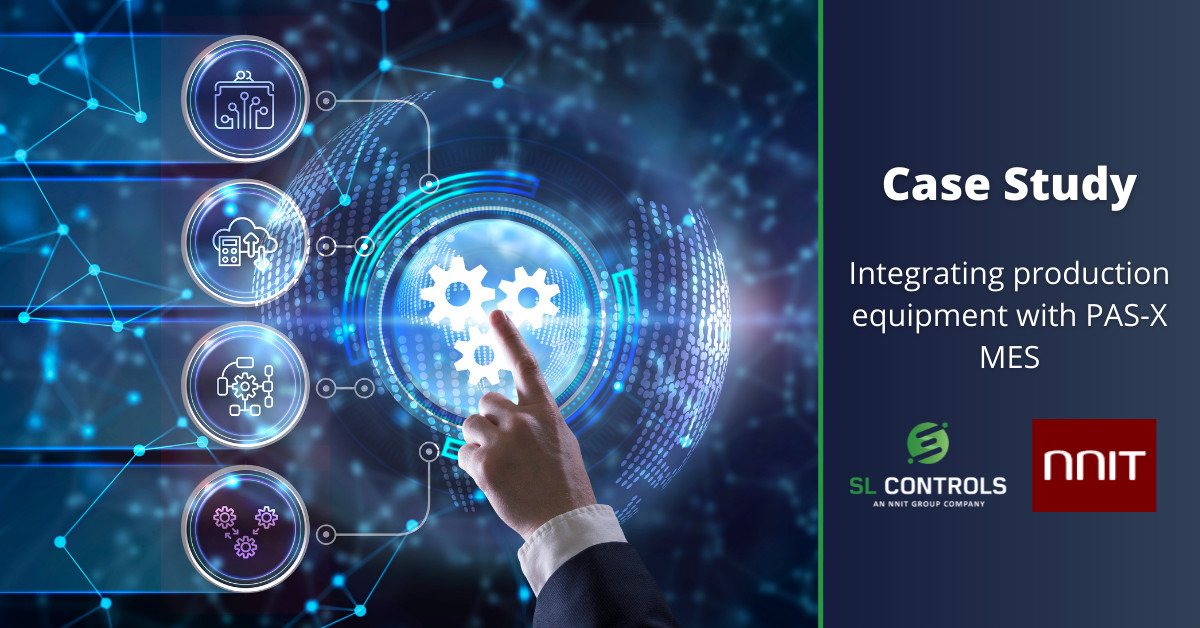
Case Study: Successfully Integrating Production Equipment with New PAS-X MES Implementation
The Project
The project outlined in this case study involved integrating the PAS-X MES platform into a customer’s production line. The customer is in the life sciences sector.
SL Controls’ parent company, NNIT, was the lead on the project. NNIT provided full support for the integration process, including scoping, design, deployment, and validation.
The first phase of the project involved defining the processes that would benefit most from storing electronic batch records. It was also important to define Master Batch Record (MBR) process flows and ensure MBR compliance with CFR Part 11.
An issue was identified at this point in the project, as the process would require the manual entering of data into the PAS-X MES. This had a number of negative implications, including the resources that would be required, the limitations it would put on the system, and the increased risk of human error that manual data entry brings.
To move the project forward and find an alternative solution to manual data entry, it was necessary to identify the production equipment that could be connected to the PAS-X MES platform. This would also involve determining the type of connection that would be needed and the required network infrastructure design.
This is where SL Controls got involved in the project, as we have significant expertise in equipment systems integration.
Objectives
There are five Operational Technology (OT) infrastructure levels in life sciences sector production facilities.
At SL Controls, our main expertise is in levels 0 to 2, i.e., designing and developing SCADA systems, developing data historians, batch performance tracking, integration of manufacturing equipment, etc.
We also have extensive expertise in the integration of manufacturing equipment with MES systems, as represented in the Plant Level. It was this expertise that was required, so SL Controls engineers joined the wider NNIT team.
Our expertise fitted in perfectly, as this stage of the project involved the integration of production equipment with the PAS-X MES platform.
What We Did
Our engineers worked with the customer’s automation engineers, as well as equipment vendors and our colleagues at NNIT, to identify the best methods for connecting the production equipment to the PAS-X MES.
We also proposed changes to the existing OT/IT infrastructure to facilitate data collection and batch information download from the new MES. We supported the customer’s IT and OT engineers in the implementation of these changes.
Our robust solution enabled data handling from the equipment on the production line to the PAS-X MES and vice versa.
Results
- With our solution, the PAS-X MES could be implemented with the risk of data errors significantly reduced as manual data entry was eliminated from the process.
- The solution is also robust enough to cope with the demands of a high-speed, high-volume, highly regulated production environment.
- The solution is compliant, too, as it satisfies the regulatory requirements of electronic batch records.
- We also provided a full end-to-end solution for the customer, utilizing the expertise in both SL Controls and NNIT.
Sven Savic, SL Controls Systems Architect, said: “The acquisition of SL Controls by NNIT means the two companies now offer complementary skills that enhance the end-to-end level of service that we can offer. This unique and highly effective approach to project delivery was demonstrated in the successful delivery of this PAS-X MES implementation project.”
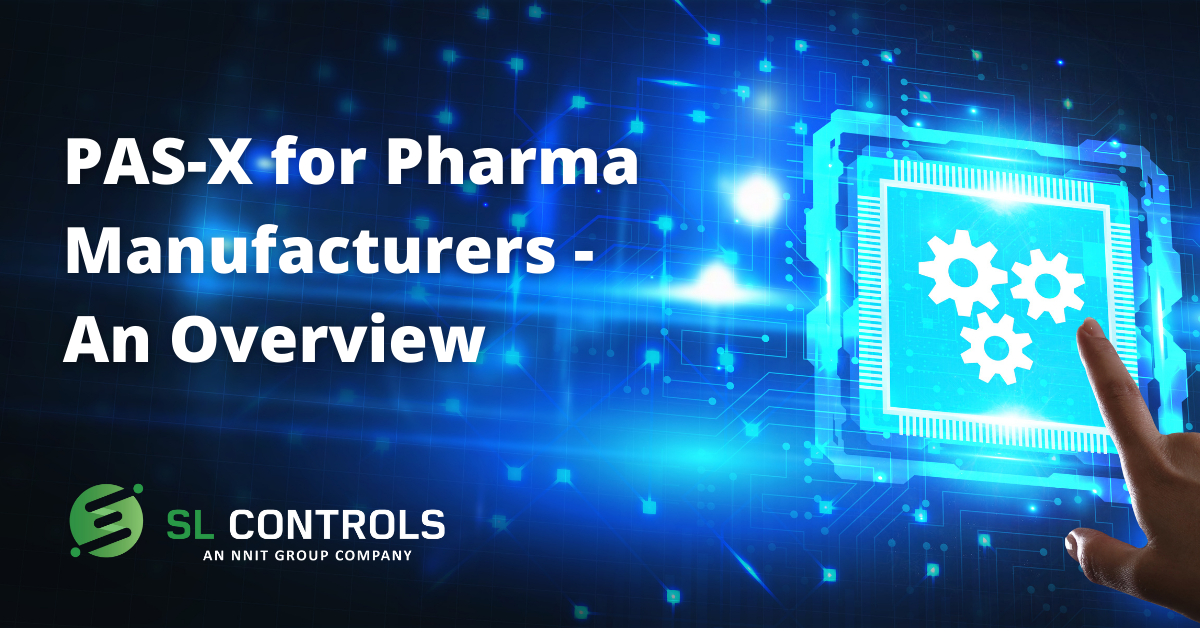
What Is PAS-X and Is It the Best MES Solution for Your Pharma Manufacturing Facility?
MES (manufacturing execution system) platforms are becoming increasingly indispensable tools in manufacturing facilities, including in the life sciences sector. There are many MES options available (including PAS-X), so it’s important to get the right advice and support to ensure the implementation of a solution that works for your organization today and into the future.
In this blog, we are going to look at PAS-X, including what it is and why it could be the ideal MES solution for your pharmaceutical manufacturing facility.
First, though, a recap on the more generalized benefits of MES platforms. When properly specified, configured, integrated, and optimized, an MES platform will improve your production processes, increase automation by digitizing manual workflows, and enable real-time monitoring and line management capabilities.
The benefits that result from these functions and capabilities include everything from improved allocation of resources to shorter production cycles to reduced time to market.
What is PAS-X?
PAS-X is an MES platform developed by German software developer Körber that controls, synchronizes, and monitors production processes. It can be integrated and connected to all equipment, systems, and lines in modern manufacturing facilities. It can also be integrated with ERP platforms as well as more specialized systems, such as LIMS systems.
Crucially, PAS-X is suitable for all segments of the pharmaceutical industry, including pharmaceuticals, vaccines, and biotech. It is also suitable for all product types, including liquids and solids.
Why Choose PAS-X?
The main point to consider is the fact that PAS-X was designed specifically for the pharmaceutical manufacturing industry. It is also used by more than 50 percent of the 30 leading pharmaceutical and biopharmaceutical companies in the world. This point alone is not absolute, so it doesn’t mean PAS-X is the right option in all pharmaceutical facilities. However, it is tried, tested, and trusted in the pharma industry.
What about other factors to consider when looking at PAS-X? Here are the main points:
- PAS-X helps you achieve paperless manufacturing with the automation of manual and repetitive processes that are common in the pharmaceutical industry, particularly in relation to record-keeping.
- It meets the requirements of the FDA, European regulators, and regulators in other parts of the world. This includes the FDA’s 21 CFR Part II.
- It facilitates real-time monitoring, including remotely, of all data that your facility produces during production and packaging processes.
- PAS-X provides access to usable production data for everything from operational decision-making to quality control to process optimization
- Helps you digitalize production and documentation processes in your pharmaceutical manufacturing facilities, including compliant electronic batch records (EBRs).
- Enhances quality assurance efficiency by enabling review-by-exception, whereby an automated process checks batch reports. Only when a deviation is identified is the batch sent to the quality assurance team for further quality processing. This functionality, alongside the EBR capabilities of PAS-X, accelerates batch release processes.
- Enables fully digitized traceability of all batches and production processes.
- Helps to standardize processes across your production line.
- PAS-X has a modular structure so you can implement the elements that you need, adding new modules at later dates according to business requirements.
- It comes out of the box with pre-configured templates, accelerating implementation.
SL Controls – Your PAS-X Solutions Partner
At SL Controls, we have wide-ranging experience in PAS-X implementation, optimization, and scaling projects, with specific expertise in integrating production line equipment with the PAS-X platform.
Our team can help with all stages of the project, including everything from creating a business case and defining the project scope to development, commissioning, and testing. In most situations, we’ll work with the preconfigured templates that come with PAS-X to customize your implementation while minimizing timescales and project costs.
To find out more about PAS-X, to discuss a project you are planning, or to find out how we can help you overcome current challenges, please get in touch.
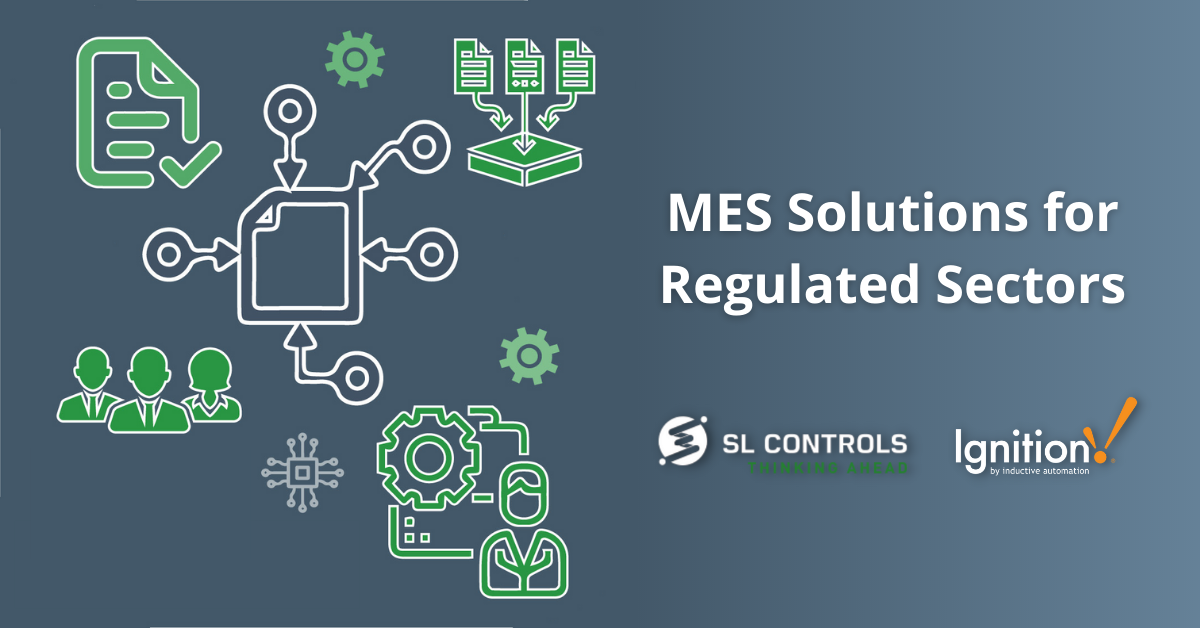
Utilizing the Power of Ignition in the Delivery of MES Solutions for the Regulated Sector
The regulated sector, including pharmaceutical and medical device manufacturers, is going through a period of transformational change. These changes are being driven by new product innovations, market pressures, the evolving regulatory landscape, and customer/end-user demands. MES solutions, powered by the platform Ignition, are enabling manufacturers to respond, including manufacturers in highly regulated industries.
SL Controls is a Gold Certified integration partner with Ignition. We have developed and deployed MES (Manufacturing Execution System) solutions for a range of clients, including pharmaceutical and medical device manufacturers.
Why MES Solutions are Important in the Pharma and MedTech Industries?
MES solutions optimize processes and line management, as well as providing you with optimization tools that improve OEE. MES solutions also improve product quality and deliver cost and efficiency savings through:
- Improved resource allocation
- Real-time management of operations
- Improved maintenance processes
- Enhanced inventory control
- Smoother process changeovers
- More effective interoperability with other manufacturing systems
- Minimized product recalls
- Reduced time to market
- Improved use of data
- Elimination of human error, particularly in data handling
- Shorter production cycles
Why Choose the Ignition Platform as the MES Solution for Your Facility?
At SL Controls, our experienced engineers and system architects have spent considerable engineering hours investigating, working with, and developing solutions for a vast range of MES platforms, including the largest and most well-known.
We understand the opportunities that these systems present to pharmaceutical and medical device manufacturers, but we are also acutely aware of the challenges, limitations, and frustrations.
Ignition stands out from other MES platforms. With the Ignition platform and our expertise in regulated industries, we have delivered significant improvements and return on investment for our clients through MES solution deployments.
Some of the key features of Ignition that make it stand out include:
- It is a server-based, single-platform solution that includes everything from machine control to scheduling to data management to reporting. As it is server-based, the platform is always up-to-date, and it is easy to distribute.
- Everything is included in Ignition, simplifying the development process and minimizing deployment timelines.
- It is easy to expand into other lines or facilities, or to scale according to business needs.
- It has a simple-to-use interface, and it is easy to operate, with a short and shallow learning curve.
- Ignition is more cost-effective than other platforms, and it operates a flexible licensing model that facilitates innovation and makes it easier and less costly to scale. Specifically, it operates a pricing model with unlimited licensing and unlimited free tags and runtime clients.
While it may not be as well-known as other MES platforms, Ignition is used by tens of thousands of facilities across a range of sectors in 75 countries.
Benefits of SL Controls’ Ignition-Based MES Solutions
- Manufacturing efficiency improvements
- Reduce downtime
- Minimize waste
- Capture, monitor, analyze, and control manufacturing data
- Optimize quality control processes and eliminate product defects
- Enhance high-level oversight of entire operations
- Integrate production (OT) with ERP and other business systems (IT)
- Reduce OT and IT costs
- Improve the utilization of assets and OEE through downtime tracking and visualizations that include OEE calculations
- Identify production trends and manage processes and inventory in real-time
- Track raw materials through to finished state with real-time oversight
- Suitable for applications that range from single lines to enterprise-wide
- Highly flexible and customizable. For example, if you have an existing SCADA system, you can choose to use Ignition for MES or you can use Ignition to expand your SCADA system into an MES. Modules can also be easily added and removed.
Your Ignition and MES Integration Partner
At SL Controls, we have engineers on our team that is fully trained on the Ignition platform. We also have direct experience developing and deploying MES solutions for clients in regulated sectors. In addition, we are continuing to expand this team of Ignition specialists as demand for MES solutions increases in the industries that we serve.
The adoption of MES solutions is a key priority for improvement-minded, forward-thinking pharmaceutical and medical device manufacturers. An SL Controls developed, deployed, and supported MES solution, powered by Ignition, will help your business achieve its modernization objectives.

What is Microsoft Cloud for Manufacturing and What Can You Expect?
Microsoft Cloud for Manufacturing is on its way. It was announced last year as one of several new industry clouds that Microsoft is developing, and it is currently in preview mode. What can manufacturers in the pharmaceutical, medical device, and technologies industries expect from this new Microsoft solution?
For us at SL Controls, Microsoft’s Azure cloud has been our platform of choice for some time now. We remain technology agnostic and have skills and capabilities across all leading cloud computing platforms, but we lean towards the Microsoft suite of services whenever it is appropriate to do so.
With this experience of delivering Industry 4.0 and digital transformation solutions using Azure and other Microsoft technologies, we have been watching the development of Microsoft Cloud for Manufacturing with interest since it was first announced.
What is Microsoft Cloud for Manufacturing?
Let’s start with what it is not – Microsoft Cloud for Manufacturing is not an alternative to the Azure platform, nor is it a unique instance of Azure. Like the other industry clouds in its suite of solutions, Microsoft Cloud for Manufacturing includes Azure and other Microsoft products, but they are extended and refined to have more relevancy for the manufacturing industry.
For example, Microsoft Cloud for Manufacturing will have APIs, workflows, templates, and standards designed specifically with manufacturers in mind. The aim is to make it quicker, easier, and more cost-effective for manufacturers to implement Industry 4.0-related solutions.
What You Can Do with Microsoft Cloud for Manufacturing?
The capabilities of the Microsoft Azure platform make it possible to implement a vast range of solutions needed by the life sciences and technologies industries. Microsoft is highlighting five main areas in this preview stage of Cloud for Manufacturing:
- Agile factory of the future – improving IT/OT security, operational visibility, and OEE, as well as utilizing machine learning to improve productivity, quality, safety, etc
- Supply chain resilience – optimizing the supply chain and improving supply chain planning and visibility
- Digital innovation – using digital twin technologies to improve everything from product development and product quality to machine downtime and output
- Workforce transformation – connecting workers and improving collaboration, particularly between those on the factory floor and those in the office, as well as improving training and skills development
- Customer engagement – improving customer service and the sales process, particularly in relation to demand management
These five areas are crucial, but our experience at SL Controls tells us the above list is only part of what is possible in the Industry 4.0 space with the Microsoft technologies that are set to be included in Cloud for Manufacturing.
Accelerating Change in Pharma and MedTech Manufacturing
With Microsoft Cloud for Manufacturing, manufacturers will continue to have access to proven, enterprise-ready equipment systems integration and automation platforms that will transform operations. At SL Controls, we have the skills and experience to customize Cloud for Manufacturing to deliver fast, tangible results for companies in highly regulated industries.
With our capabilities and the suite of Microsoft tools packaged under the Cloud for Manufacturing umbrella, your entire operation will become more agile, with end-to-end visibility, an empowered workforce, and enhanced sustainability. Data-driven decisions will become the norm, you will be more competitive, and you’ll become more resilient even in the most turbulent of markets.
Finally, while Microsoft Cloud for Manufacturing isn’t publicly available yet, the Microsoft products that will be a part of it are well-established. Examples include:
- Microsoft Azure
- Dynamics 365
- HoloLens 2
- Microsoft 365
- Microsoft Teams
- Microsoft Power Platform
- Microsoft AI
- Microsoft Cloud for Sustainability
At SL Controls, our architects and engineers can also integrate systems and platforms from other vendors.
We are looking forward to the public introduction of Microsoft Cloud for Manufacturing as we continue to use Azure and other Microsoft technologies to deliver advanced systems integration and smart manufacturing solutions for our clients.
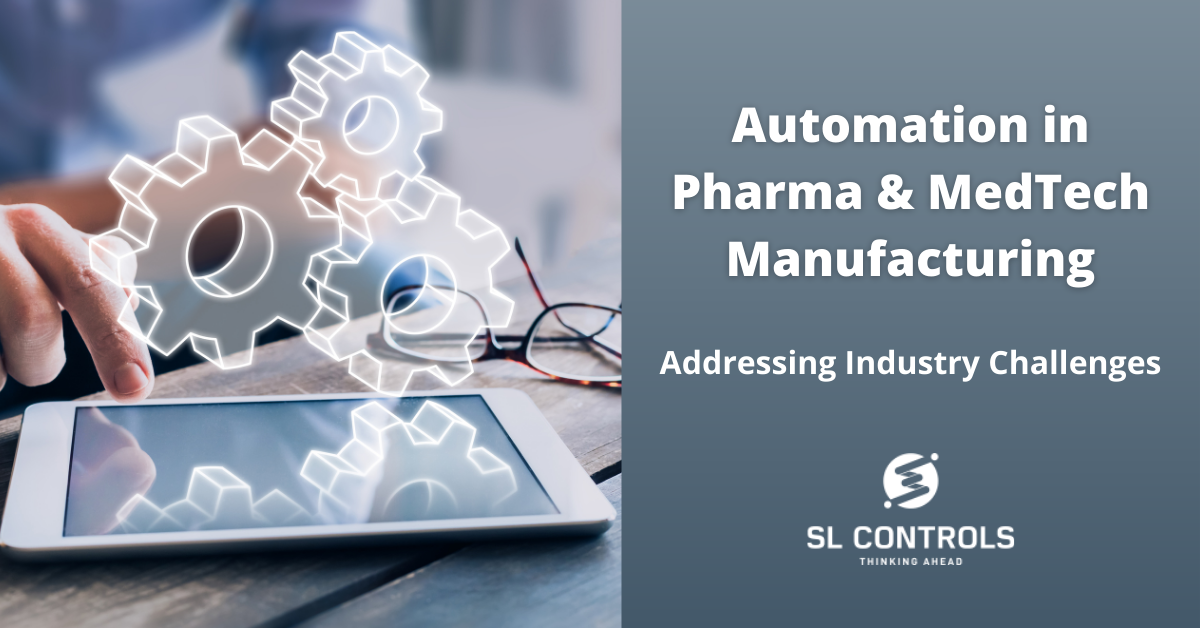
How Automation Can Address the Challenges in Pharmaceutical and Medical Device Manufacturing
There are a number of challenges facing the pharmaceutical and medical device manufacturing industries. Those challenges include labor shortages and developing supply chain resilience. There is also an increasing requirement to become more agile, where production facilities can react faster to changing demands and expectations.
Pharmaceutical and medical device companies also have to deal with changes in medical device regulations, such as the recently introduced EU MDR, while there are always pressures to improve productivity and profitability.
Automation technologies are a crucial part of the solutions to these challenges. This includes everything from robotic process automation (RPA) solutions to advanced equipment systems integration to the development of future-proof cloud-to-edge technology architectures.
It isn’t just about challenges, either, as there are also opportunities that become available to manufacturers through advanced automation solutions.
Below are some of the ways automation and other Industry 4.0 technologies are helping pharmaceutical and medical device manufacturers address current challenges and take advantage of the opportunities that exist
Improve Current Processes Without Increasing the Existing Footprint
Doing more with less is often the objective of pharmaceutical and medical device manufacturers. Automation and other Industry 4.0 solutions make this possible.
By integrating equipment and systems throughout all stages of the production process, making better use of data, and utilizing advanced, hybrid cloud technologies, it is possible to optimize existing manufacturing processes within existing footprints and with a reduced labor requirement.
Minimize New Product Introduction (NPI) Timescales
The experience of Covid-19 is likely to have changed the pharma and MedTech industries considerably and irrevocably. An example of a driver of these changes is also one of the biggest success stories of the pandemic – the introduction of vaccines. What we saw was the industry developing, testing, obtaining regulatory approval, and moving to at-scale manufacturing at a pace never seen before.
This experience demonstrated what is possible, and it presents potentially positive commercial opportunities for life sciences sector companies.
Not every new medical device product or drug will benefit from such rapid development and commercialization, but where they are applicable, automation technologies and solutions will play a key role.
Minimizing Engineering Time
Automation can reduce engineering time, enabling the rapid deployment of solutions and processes that deliver immediate production and business benefits.
An example is the use of cloud technologies to develop new software solutions for pharmaceutical and medical device manufacturers. When cloud platforms like Microsoft Azure are used, the solutions become repeatable on multiple deployments, automating the process of rolling out the solution to additional lines and facilities.
Digital Twin Technologies Enhancing Agility and Flexibility
Digital twin technologies are suitable for a range of applications in modern pharmaceutical and medical device manufacturing facilities. This includes the implementation of a preventative maintenance approach, where maintenance work is completed based on real-world requirements and predicted component failures rather than pre-determined timescales and unexpected downtime caused by actual failures.
Digital twin technologies can also be used to enhance agility and flexibility in production environments. For example, production processes, machines, and equipment can be replicated digitally in the cloud, so engineers can work on modified or expanded designs. Those designs can then be validated in the virtual simulation, enabling rapid deployment when the amended operations are required.
The Future of Automation
Automation has been important in manufacturing for many decades now, but we are entering a new era with the availability and capabilities of Industry 4.0 technologies. This includes everything from the Industrial Internet of Things (IIoT) to smart manufacturing methodologies to digital transformation strategies.
Automation isn’t the only solution to the challenges faced by manufacturers in regulated industries. However, it is the central component in many and a crucial consideration in most.
« Previous 1 2 3 4 5 6 … 18 Next »