Blog
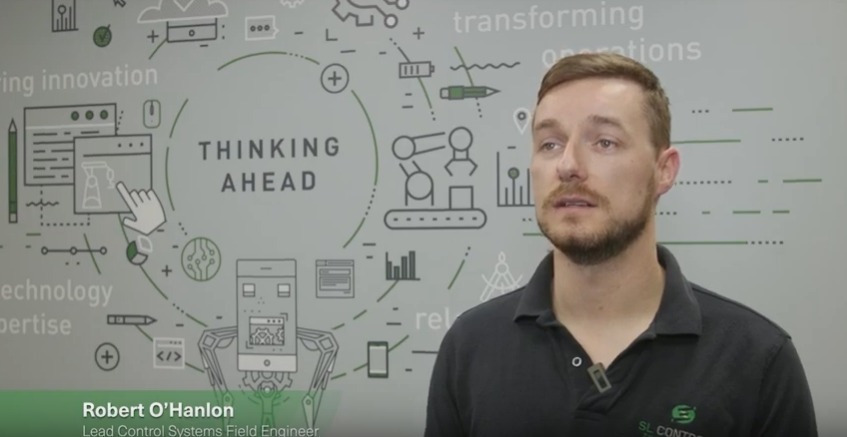
Video – Employee Stories: Robert O’Hanlon
Robert O’Hanlon is the Lead Control Systems Field Engineer at SL Controls. Find out what it’s like being a field engineer as well as what it’s like working for SL Controls.
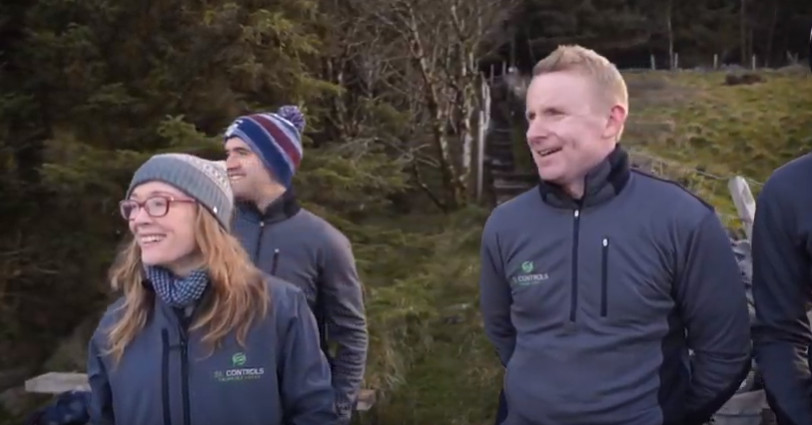
Atlantic MedTech Cluster Video Profiling SL Controls
SL Controls is a member of the Atlantic MedTech Cluster, a group that promotes the MedTech industry in the Northwest of Ireland. This video was made by the Cluster to promote SL Controls and what we do.
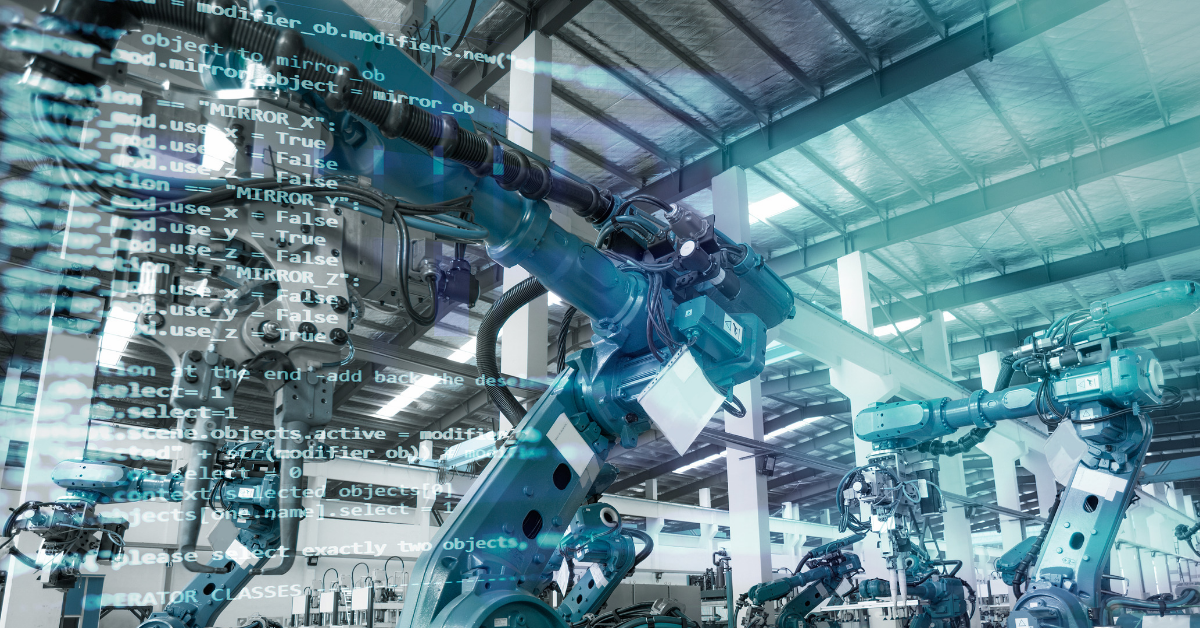
The Business Opportunities of Digitalisation and Digital Transformation in Manufacturing
Digitalisation (digitalization) is a process that results in the digital transformation of a business. It involves moving passed digitisation (digitization) – way beyond digitisation, in fact. With digitALISAtion, you don’t simply move from using paper-based systems to digital systems. Instead, you transform your business, blending the physical world with the digital world so they effectively work as one.
The result is a digital business, i.e. a pharmaceutical or medical device manufacturer that is a fully digital business.
A range of technologies is involved in the digital transformation of a manufacturing business. This includes:
- Robots
- Cobots
- Software that automates manufacturing processes
- Software that automates other business processes and that integrates those processes with the manufacturing process
- Sensors and semiconductors that are connected to the internet
- Artificial intelligence
- Machine learning
- Data analytics
- Cloud technology
- Collaborative working technologies
- Virtual, augmented, and mixed reality
- And more
What are the business opportunities of digitally transforming your business, though? Here are some of the most important.
Improved Productivity
Factory automation technologies improve output rates and reduce error rates. Digitalisation can also improve most – if not all – manufacturing processes. Batch changeovers are a significant example where digitalising the process can cut changeover times from 10, 20, 30 minutes (or more) to a couple of minutes (or less).
Additionally, sensors and machine learning technologies can improve OEE and reduce breakdowns, leading to further improvements in productivity. A good example of this is systems receiving real-time data from sensors that they can then use to predict failures before those failures occur.
More Efficient Use of Resources
The digitalisation of a manufacturing business involves using machines and software to perform functions that are currently performed by people. This allows companies to redeploy and reallocate their resources in a more effective way.
For example, if a machine or system fails in a traditional manufacturing environment, the manufacturer may need to call an engineer for support. That engineer may then need to travel to the manufacturing facility to complete the repair.
Not only does digitalisation make it possible for this process to be done remotely: digital twin technologies take it much further. Digital twin technologies allow support engineers to keep a virtual twin of the equipment or machine, updated with real-time data. The engineer will, therefore, know there is a problem at the same time as the manufacturer.
In addition, a digital twin with artificial intelligence capabilities could predict the failure and either automatically schedule maintenance or send process updates, both of which can potentially prevent the failure from occurring.
More Effectively Working with Suppliers, Regulators, and Others
By digitally transforming a business, it’s possible to build digital bridges with companies and organisations in distribution and supply chains. Automating these processes reduces errors as well as decision-making times. This offers a range of benefits including the more efficient management of raw material stock levels or finished product output.
Improving Communication and Oversight
Digitalisation makes communications more efficient while also adding transparency to communications. Collaborative software and cloud technologies are good, practical examples of this.
Digitalisation also means there is no longer a need to be in a physical location to have full management overview of what is going on. Among other things, systems can send reports with real-time data, while it is also possible to remotely operate processes, functions, and systems.
Product Customisation
Product customisation is a manufacturing trend that is going to become bigger and more important to a wider range of companies. However, in a traditional manufacturing setup, even one with extensive robotic automation, it’s not possible.
With digitalisation technologies, though, manufacturing businesses can move to small batch and mixed manufacturing, opening the door to product customisation.
The benefits of this are substantial including increased revenues, extending the reach of your brand, and building better relationships with customers.
Enhancing the Customer Experience
Opportunities like product customisation enhance the customer experience but there are other ways digitalisation can make this happen too. For example, integrating sales, marketing, and customer service systems with manufacturing systems brings customers closer to the business overall.
In addition, some of the technologies mentioned above can also make after sales support more effective. Putting sensors in products for maintenance and product support purposes is a good example. Another is running a digital twin of a product that is on-site with a customer to ensure optimal performance and reduce failure rates.
Product Development
With digitalisation, manufacturers can take customer feedback a stage further with sensors that provide real-time data. This provides invaluable information for engineers and those responsible for product development, i.e. they will know how customers and end users actually use products rather than making assumptions.
Improved Safety
There are many examples of this:
- Robots, cobots, drones, virtual reality, and other technologies make it possible to use a machine in, or send a machine into, a hazardous environment rather than a person
- E-learning technology can improve health and safety training across an entire organisation
- Machine learning can inform health and safety procedures based on facts, reducing accident rates
- And more
The Future is Now
It is not possible to achieve full digital transformation immediately… or even within a few years. These technologies are, however, being implemented in production facilities around the world right now. To remain competitive and take full advantage of the opportunities above, the time to advance the digitalisation of your business is now.
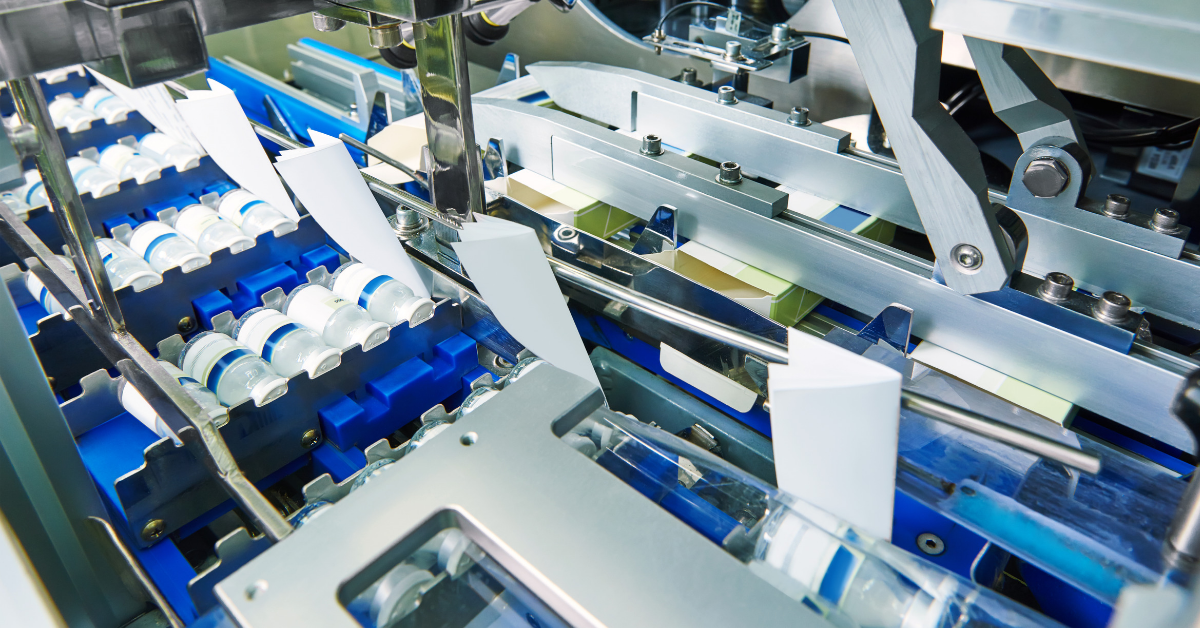
7 Industry 4.0 Trends that Will Influence Manufacturing in 2019
Manufacturing technologies are advancing at a faster rate than ever before. In such a fast-paced and busy environment, it can be hard to cut through the information and noise to get to what really matters and what will really make a difference.
In other words, the things that will improve your competitiveness in the marketplace and your bottom line.
Industry 4.0-related technologies are driving much of the changes that are currently taking place in manufacturing. This applies in all sectors, but it is particularly important in high-specification and highly regulated industries like pharmaceutical manufacturing and medical device manufacturing.
If you’re in one of these or a related industry, here are seven Industry 4.0 trends that will influence manufacturing in 2019.
1. Factory Automation
The are many reasons for companies moving towards Factory Automation technologies. This includes making production lines more efficient, making more effective use of resources, and improving productivity.
Recruitment challenges are also a factor, with manufacturers looking to technology as a solution.
Remaining competitive in fast-changing marketplaces is also a driving factor for increasing numbers of companies adopting Factory Automation solutions.
There are challenges, not least the challenge of integrating legacy systems and platforms with new equipment and technologies. These challenges are not insurmountable, however, so Factory Automation will be a feature in manufacturing not just in 2019, but for many years to come.
2. Virtual, Augmented, and Mixed Reality
Virtual, augmented, and mixed reality can be applied in manufacturing facilities in several ways. This includes product design, production line development, driving OEE improvements, technical and engineering support, training, team collaboration, inventory management, and more.
These technologies help businesses work more effectively while also making them more efficient. An example of their application includes using augmented and virtual reality to design a new production line or product, perfecting it in the virtual world before real-world prototyping or production begins.
Another is an engineer providing remote engineering support on a specialist machine on your production line using mixed reality. In this situation, your facility and engineer can be located on the other side of the world to the technical support engineer.
3. Digital Twin Technologies
Digital Twins are an emerging technology that will become an increasingly important tool in manufacturing facilities. A Digital Twin is an exact virtual replica, updated in real-time, of a physical object, process, or product.
The applications for this technology in manufacturing are far-reaching. One example is having a Digital Twin of a piece of equipment – or your entire production line – where engineers can run simulations and where machine learning technologies can predict breakdowns, plan maintenance schedules, improve OEE, and more.
4. Increasing Convergence of IT and OT
In the past, IT and OT were typically separate in manufacturing businesses:
- IT – supporting management, sales, accounting, purchasing etc
- OT – monitoring and controlling equipment, tools, and other assets on the factory floor
In fact, not only was OT traditionally separate from IT, individual systems and equipment within the OT infrastructure also existed in their own silos.
The move to intelligent manufacturing technologies and big data now makes it possible to integrate machines, platforms, and systems across all units of the business. This drives efficiencies, enhances business oversight, improves product quality, makes customer service more effective, and increases productivity.
There are challenges, of course, including dealing with compatibility issues and ensuring systems are secure. Overcoming these challenges is possible, though, presenting considerable opportunities for manufacturers.
5. Further Move Towards Digitalisation
Digitalisation is sometimes referred to as digital transformation. It involves using digital technologies to adapt or transform your business into a digital business.
In manufacturing, this means incorporating many of the points above so that systems and equipment are integrated throughout every process, chain, unit, department, and facility in your business.
6. Increasing Use of Cobots
Some research predicts the cobot market will grow from USD $710 million in 2018 to USD $12.3 billion by 2025. One of the reasons for this is the fact today’s cobots are more affordable as well as being safer, more adaptable, and more compact.
Cobots create opportunities for manufacturers to improve their production lines, increasing productivity while keeping employees safe.
7. Small Batch and Mixed Manufacturing
Many of the technologies mentioned in the points above, as well as other technologies and processes, mean it is now possible for increasing numbers of companies to consider small batch and mixed manufacturing.
This creates opportunities for your production facility, letting you compete for a wider range of contracts.
There are other benefits too, including the possibility of offering customers individual product customisation options. This not only increases value, but also creates new business opportunities.
Final Thoughts
While the above is a whirlwind overview of some very advanced and technically complex technologies, it does show the opportunities that exist in 2019 and beyond for manufacturing companies with a forward-thinking and innovative outlook.
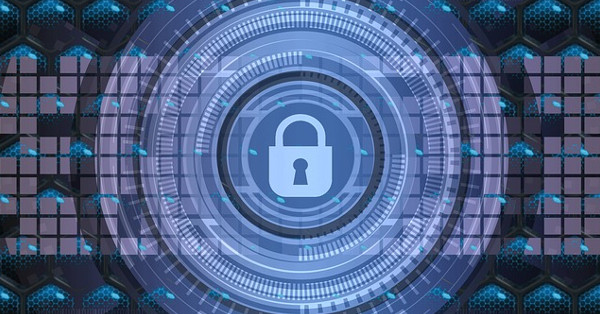
Security Challenges of Industrial Automation Control Systems
Cybersecurity, system security, and information security are challenges faced by all industries and sectors. For the manufacturing sector, these challenges are particularly acute, especially in relation to industrial automation control systems.
The threats to industrial automation control systems are varied:
- Targeted external attack to deliberately hinder production
- Targeted external attack to impact the state or quality of the product produced
- Indiscriminate external attack
- Ransomware attacks (extortion)
- Actions by disgruntled employees
As with information systems in other corporate environments, attackers can exploit technical vulnerabilities in systems. That said, most cybersecurity, system security, and information security attacks happen because of access to systems. This can be authorised and unauthorised access.
In the case of the latter, attackers usually gain unauthorised access to a system by exploiting an organisation’s non-technical security vulnerabilities. Tricking employees through social engineering techniques is one example.
Other Security Challenges
Industrial automation control systems also face other security challenges. This includes:
- Updating security – examples of this include applying security patches, updating software, and more. In general, updating the security infrastructure of an industrial automation control system is often crucial, but this must be done in a way that does not make the control system unstable.
- Updating system functionality – when not properly implemented, updating systems to add new functionality can introduce new security vulnerabilities, particularly when integrating with legacy devices and platforms.
Unique Security Challenges
Following on from the above, many of the challenges facing industrial automation control systems are unique. This includes the fact that the automation of industrial control systems means integrating systems and platforms developed by different vendors. These systems and platforms can be both proprietary and non-proprietary, with the latter presenting particular security challenges. An example is a device running on the Windows operating system.
Also, there is often a myriad of different devices involved, each one of which presents unique security challenges. This includes wireless transmitters, PLCs, remote terminal units, sensors, and more.
In addition, many of the above systems, platforms, and devices currently in use were developed five, 10, or more years ago. The internet, cloud technologies, and communication infrastructures were not as advanced back then. Therefore, the issue of cybersecurity as we know it today wasn’t as high on the priority list for vendors making these products.
You then need to add into the mix that many of the components and systems above have a long-life so could be in operation on production lines for some time to come.
Also, there is an increasing trend in the manufacturing environment to more closing integrate production networks with corporate networks like supply chain management, sales, business oversight etc.
This means the “airlock” between networks that existed in the past, and which offered a level of production line security, is now being eliminated.
Dealing with These Security Challenges
The first step in dealing with the security challenges of industrial automation control systems is to work with a solutions provider who understands the challenges and who prioritises security.
In practical terms, it is essential manufacturing operations take a holistic and multi-faceted approach to dealing with security challenges. This includes:
- Administrative controls – policies and procedures on cybersecurity, information security, and system security to cover everything from password integrity to major incident procedures to physically securing connected mobile devices.
- Staff training – this needs to be on technical policies and procedures as well as how to use the security systems in place. It is also important, however, that staff are aware of the interpersonal and social engineering risks that companies face, as well as how each individual in the company can decrease these risks.
- Physical controls – access controls, cabinet locks, etc.
- Technical controls – firewalls, intrusion prevention systems, anti-virus and anti-malware software, intrusion detection systems, backup procedures, disaster recovery solutions, etc.
- Upgrading legacy devices and systems – having a plan to upgrade and replace non-secure legacy systems, platforms, components, and devices will also make the industrial automation control system more secure.
Dealing with cybersecurity, data security, and systems security is the new reality of modern manufacturing environments. This is unlikely to change in the short-to-medium term in any significant way, and the threats we all face are more likely to increase rather than decrease.
Being aware of the risks, understanding that everyone is vulnerable, and being proactive in mitigating those risks, is the best solution.
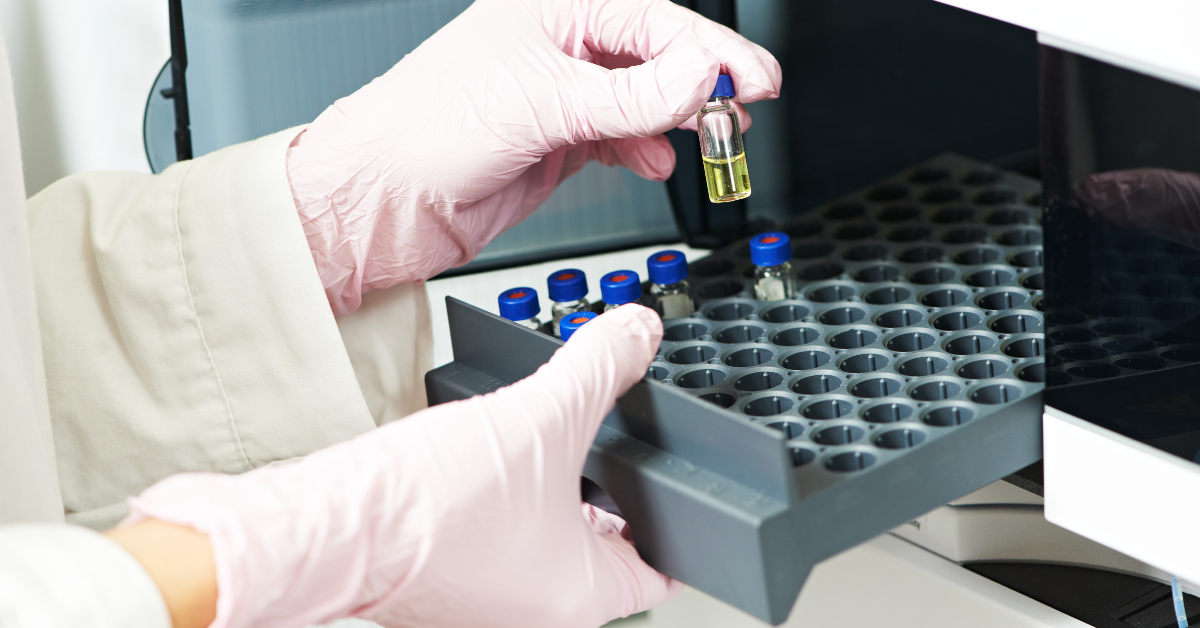
QBD, CQA, CPP, PAT – Understanding Process Validation Terminology
There are a lot of terms and abbreviations used when discussing process validation, with some more common than others. Understanding these terms and abbreviations is important given the crucial role process validation plays in relation to compliance, product quality, and production line productivity.
QBD – Quality by Design
In a QBD approach to manufacturing a pharmaceutical product, you consider the quality of the product at the earliest possible stage rather than simply testing the product for quality towards to the end.
In practice, this means identifying the sources of variability that could possibly affect a process. You then document these sources of variability as well as determining how you will manage them. This should be documented too.
This approach ensures the proper identification of the root causes of quality issues. The end result is a pharmaceutical product that meets predefined quality standards from the start.
QTPP – Quality Target Product Profile
QTPP is a summary of the quality characteristics of a pharmaceutical product. These quality characteristics are essential to ensure the finished product meets the required standard of quality.
The FDA (US Food and Drug Administration) says the QTPP should also consider the “safety and efficacy” of the product.
Things that are considered when creating a QTPP include the dosage strength, delivery system, dosage form, container system, and more. It should also include considerations such as purity, stability, and sterility.
CQA – Critical Quality Attributes
The FDA says CQAs apply to any “physical, chemical, biological, or microbiological property or characteristic” that must be within a limit or range to ensure the pharmaceutical product meets the required quality standard.
The identification of CQAs typically takes place during the first stage of process validation. This is the process design stage.
This is the ideal time to establish acceptable limits and ranges as well as establishing protocols for measurement, data collection, and data analysis.
CPP – Critical Process Parameters
A CPP is a variable that can impact the CQA (defined above). Therefore, CPPs must be monitored to enable early and accurate detection of deviations outside acceptable limits that will impact product quality.
Of course, not all process parameters are the same as some will have a greater impact on CQAs than others. As a result, it is important to prioritise CPPs over other process parameters as they will have the most impact. Of all process parameters, CPPs must be the most rigorously controlled.
Examples of CPPs include temperature, pH, cooling rate, rotation speed, etc.
Another term often used when determining CPPs and their impact on CQAs is CMA. This stands for Critical Material Attributes. A CMA relates to input materials and their chemical, physical, biological, or microbiological properties.
PAT – Process Analytical Technology
PAT refers to a method or system of testing. According to the FDA, it is essential for “designing, analyzing, and controlling manufacturing”. It involves taking measurements of the attributes described in the terms above, i.e. CQAs, CPPs, and CMAs.
Crucially, those measurements should be in real-time.
The aim of PAT testing is to ensure consistent product quality standards while also making the testing process more efficient. Productivity also improves because product quality becomes more consistent which minimises the volume of rejected products.
Not Just About Compliance
All the above abbreviations describe steps taken during process validation, all of which are essential in terms of regulatory compliance. However, going through these steps also delivers productivity and efficiency benefits to production lines.
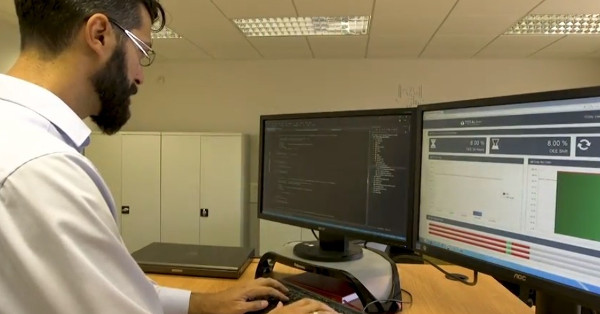
A New Approach to Delivering Bespoke Software Solutions to the Regulated Sector
Like all manufacturers, companies in regulated sectors must innovate and improve their manufacturing processes to remain competitive. Driving efficiencies and increasing productivity levels are ongoing objectives.
In addition to this drive to remain competitive, manufacturers in regulated industries must deal with the added burden of compliance. Also, requirements in many heavily regulated industries are changing as governments around the world, particularly in the USA and EU, raise standards.
Prime examples of this are the pharmaceutical and medical device manufacturing industries where new regulations aim to improve product quality and traceability. The latter has multiple aims including combating the trade in fake and stolen medicines as well as improving quality of service for patients and consumers.
The Traditional Approach to Delivering Bespoke Software Solutions
So, there is a need to improve and innovate production lines while also meeting new and existing regulatory requirements. In many cases, this involves the introduction of new software solutions. Examples include:
- Integrating machines and automating processes
- Collecting and making better use of data
- Adapting production lines in preparation for new business opportunities
- NPIs
- Updating validation procedures
- And more
In the past, the development, testing, and implementation of these software solutions followed a similar path. The core of this development path typically involved a software solution provider starting with a blank screen.
Of course, most software solution providers serving the manufacturing sector will have specific sections of tested and trusted code they can adapt and re-use on multiple projects. If the project is to deliver a bespoke software solution, however, providers will write most of the code from scratch.
There are lots of benefits to this approach, not least that you will end up with a highly customised software solution that meets your specific needs and objectives.
There are downsides as well, however:
- Project time – starting from scratch is the longest approach to developing a new software solution
- Project cost – as the project will take longer, costs will be higher too
- Longer testing and debugging time – as bugs always exist in new code, there is no way to be sure the software will be fully ready for all situations and outcomes, regardless of the extent and quality of testing it has gone through
We know all the above at SL Controls because we have extensive experience developing fully bespoke – and often highly specialised – software solutions for the manufacturing industry. Plus, we have specific experience developing those solutions for manufacturers in regulated industries.
Sometimes, this approach is unavoidable, i.e. starting from what is essentially a blank screen is the only way to deliver on the client’s requirements. However, this is not always the case.
Therefore, we knew there was an alternative approach to developing bespoke software solutions for manufacturers in regulated sectors that would be suitable for a wide range of situations.
So, we built it.
The SL Controls New and Unique Approach to Software Development
The new approach we developed at SL Controls has three main objectives:
- Deliver the same level of quality, versatility, flexibility, and scalability as a software solution written from scratch
- Meet the promise of being a bespoke software solution by being fully customisable
- Reduce project delivery times and costs
We achieved this by taking a modular approach to the most typical software requirements that manufacturing sectors require. This involved breaking those typical software solutions into commonly needed components.
We then fully developed and tested the code for those components and packaged them in a module. This gave us multiple modules that, when put together, created an end-to-end software solution.
Furthermore, we didn’t lock down each module in a take-it-or-leave-it-type situation. Instead, we built the modules so each one could be individually modified and customised.
TOTALline – Improving Manufacturing Processes in Regulated Sectors
The result of the efforts above is the TOTALline product range. With TOTALline, clients can:
- Select (and only pay for) the modules they need – there are 14 modules to choose from
- Get all or some of those modules customised to better meet their requirements
In other words, creating bespoke software solutions from scratch is no longer required in many situations. Examples include automating batch record-keeping and traceability, automating batch changeovers, integrating production line equipment, and data collection and reporting.
Where TOTALline is a suitable software solution, you will save considerable time and money, dramatically improving return on investment. Find out more today.
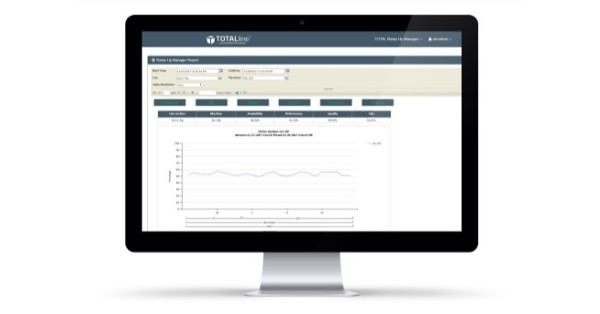
The Smart – and Cost-Effective – Way to Improve the Performance of Production Lines
Integrating equipment, machines, platforms, and sites to improve productivity is a key objective of most production lines. Automating processes to drive efficiencies is another crucial objective. How can you achieve these objectives with minimal risk and cost, however, while also ensuring full regulatory compliance?
The traditional way of automating processes and integrating the elements that make up your manufacturing capabilities is to get a software solution created from scratch.
There is another way.
This new and unique alternative delivers the same end result but at a lower cost and with a faster delivery time.
The TOTALline Solution
TOTALline is a software product made up of several fully customisable software modules that achieve the broad objectives outlined above.
For a quick introduction, watch this 60-second video where SL Controls’ Technical Director, Paul Clarke, succinctly summarises TOTALline.
What Does TOTALline Do?
We developed TOTALline at SL Controls to meet the specific needs of manufacturers in regulated sectors, particularly pharmaceutical and medical device manufacturing. In summary, TOTALline enables you to achieve data-driven savings in your manufacturing processes.
The software modules that make up TOTALline are off-the-shelf, giving you substantial cost and time savings. Our team then fully customises and integrates the modules to meet your requirements.
The benefits of TOTALline include:
- Improved efficiency by automating processes such as data collection, data analysis, and batch control
- Improved productivity through enhanced machine integration and the automation of processes
- Reduced risks through the accurate and automatic collection and reporting of data, including batch reports
- Improved OEE
- Improved decision-making as you will have better insight into the performance of your production lines
- Reduced costs compared to achieving the same objectives with a solution created from scratch
- Faster implementation time than achieving the same objectives with traditional alternatives
TOTALline Products
We have split TOTALline into three distinct product offerings to make it easier for you to find the best solution for your needs. Each one of those product offerings can then be fully optimised before being integrated into your production line by our highly skilled and experienced team.
TOTALbatch
With TOTALbatch, you can reduce batch changeover times to just a few minutes. You will also benefit from improved batch integrity and traceability.
Watch the video to find out more.
TOTALdata
Move away from manual record-keeping on your production lines forever with TOTALdata. TOTALdata is vendor neutral and will give you greater oversight of your operations, improving analysis and decision making.
Watch the video to find out more.
TOTALsolution
With TOTALsolution, you can select any modules from the full TOTALline product range, including those in TOTALbatch and TOTALdata.
Watch the video to find out more.
Taking the Next Steps
In a sentence, the TOTALline product range from SL Controls will improve the performance of your production line without the cost and time delays of developing a similar software solution from scratch.
To find out more about TOTALline and how it can help your manufacturing facilities, please contact a member of our team today.
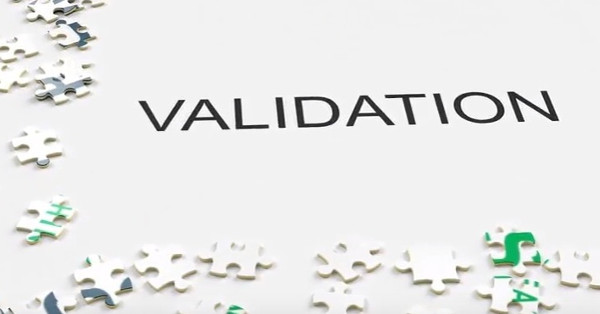
Video: Validation Services Explained
At SL Controls, our validation services include 21 CFR Part 11 compliant software, batch execution systems, source code reviews, process validation, software validation, and equipment validation. Watch our video to find out more.
https://www.youtube.com/watch?v=_wkDSrjyBQM
« Previous 1 … 12 13 14 15 16 … 18 Next »