Blog
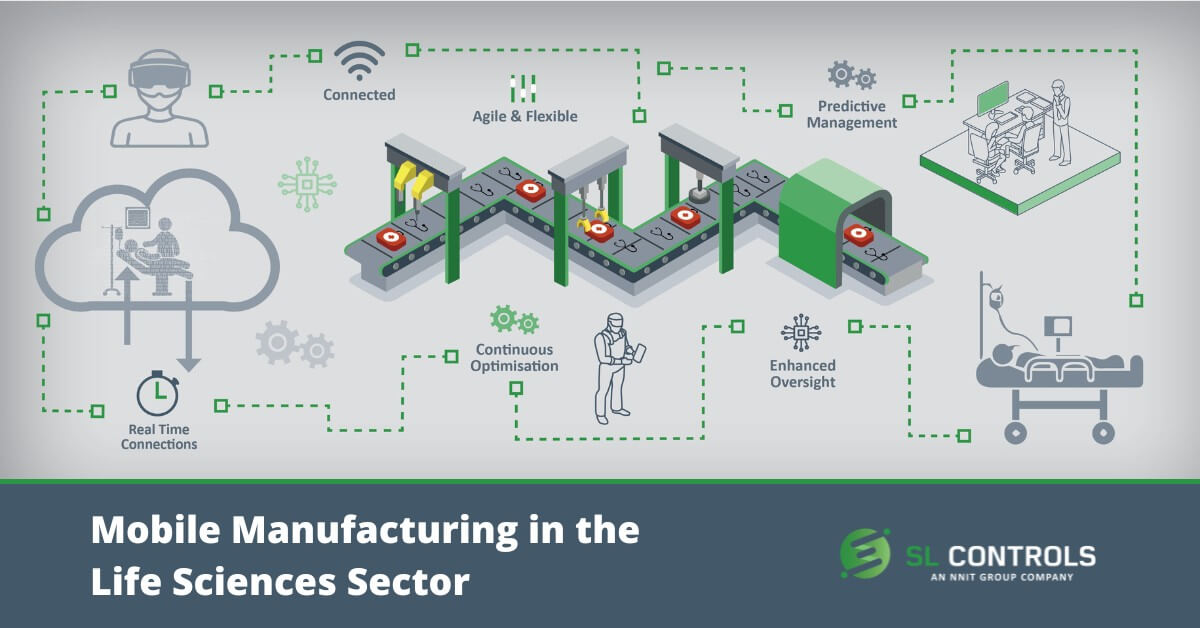
Mobile Manufacturing in the Life Sciences Sector – Opportunities, Risks, & Challenges
Manufacturing in the life sciences sector is dominated by large-volume, high-speed production facilities where business models are based on economies of scale. This approach has served the sector and society very well over the past decades, especially in the developed world. Now, however, there is increasing interest, research, and innovation in a different form of production – mobile manufacturing.
Mobile manufacturing is a type of decentralised production, where manufacturing takes place closer to the point of need. It offers many potential advantages to life sciences companies as well as to patients, but there are also risks and challenges. We’ll look at all of these points in this blog.
However, it’s helpful at the outset to highlight one of the main factors driving innovation in this area – personalised medicines, treatments, and devices.
There is still a need in the healthcare sector for mass-produced pharmaceutical and medical device products, so high-speed, high-volume production facilities are here to stay. However, there is also a growing need for alternative manufacturing approaches, such as batch size of one manufacturing, to make personalised and other low-volume novel products both commercially and practically viable.
What is Mobile Manufacturing in the Life Sciences Sector?
Mobile manufacturing solutions can take different forms, but they are often described as a factory-in-a-box. They often utilise continuous manufacturing processes that improve process control, enhance quality, maximise automation, improve flexibility, and increase efficiency. Mobile manufacturing solutions also often feature 3D printing and other additive manufacturing techniques.
Some of the most common characteristics of mobile manufacturing solutions include:
- Flexibility – flexibility of location as well as, often, flexibility in capacity and product, where the mobile manufacturing facility can produce different products in large or small quantities.
- Location – can be fully autonomous or installed in an existing facility, such as a hospital.
- Replicated – the unit can be replicated for multiple installations in different locations.
- Redeployment – the unit can be redeployed in a different location.
The Advantages of Mobile Manufacturing for the Life Sciences Sector
Societal and Healthcare Benefits
One of the main societal and healthcare benefits of mobile manufacturing is its potential to reduce the unequal access to medicines and treatments between developed and developing countries.
As mentioned previously, mobile manufacturing solutions also create viable production solutions for personalised medicines, including products that are difficult to manufacture using the high-volume, high-speed manufacturing model. Cell and gene therapies are a good example. The rapid manufacturing turnaround required by many cell and gene therapy products makes it highly beneficial to move production as close to the patient as possible.
Another societal and healthcare benefit of mobile manufacturing is that it enables a rapid response to patient demand, where products can be made available to patients faster than traditional manufacturing approaches.
Commercial Advantages of Mobile Manufacturing
The commercial advantages of mobile manufacturing include:
- More effective and efficient method of producing low-volume therapies and treatments.
- Potential cost-savings compared to the traditional approach of large-scale manufacturing facilities often located at a considerable distance from the point of care. This includes an enhanced ability to right-size the manufacturing process according to the product.
- Reduced capital investment risks as mobile manufacturing facilities can be built according to market demand, deferring large-scale capital expenditure until there is greater certainty of market success.
- Reduced risk of supply chain disruption where problems at one facility can have a wide impact on overall production.
Sustainability of Mobile Manufacturing
The sustainability benefits of mobile manufacturing include reductions in transportation costs to move medicines and other treatments from manufacturing facilities to the point of care. Smaller buildings/facilities also require fewer resources to build, run, and maintain, while right-sizing manufacturing based on the product can reduce the environmental impact of production.
The Commercial Factors Driving Innovation in Mobile Manufacturing
- Market size – smaller markets are more suited to mobile manufacturing and other decentralised manufacturing strategies.
- Scale of processes – small footprint processes are more suited to mobile manufacturing.
- Product maturity – where mobile manufacturing can be a more viable option for new product introductions.
- Speed to market – facility build times are faster and capital expenditure is lower with mobile manufacturing.
Practical Example of Mobile Manufacturing
This example comes from BioNTech, the German biotechnology company. In 2022, it introduced in Africa its new turnkey container-based mRNA manufacturing facilities for the production of vaccines. This mobile manufacturing solution enables the production of mRNA vaccines in bulk with fill-and-finish completed by local partners. The solution is capable of producing 50 million doses of the Pfizer-BioNTech Covid-19 vaccine a year.
Mobile Manufacturing Risks and Challenges
There are a number of risks with mobile manufacturing that must be understood and mitigated, as well as several challenges.
Cybersecurity
Mobile manufacturing facilities significantly increase the size and complexity of an organisation’s attack footprint. Therefore, the development of strong cybersecurity measures and protocols must be given the same level of priority as developing the technologies that make mobile manufacturing practically and economically viable.
Physical Security
There are also physical security risks that need to be understood and mitigated, as the physical attack surface will also increase as companies develop and deploy mobile manufacturing solutions. The risks from a physical attack on a mobile manufacturing facility include everything from intellectual property theft to data privacy breaches to manipulating the manufacturing process in a way that causes harm to patients.
Regulatory and GMP Compliance Challenges
Regulations governing the life sciences sector are weighted towards traditional centralised manufacturing facilities, where volume and scale are typically the priorities. Regulations, standards, and guidance will have to continue to evolve to accommodate and make viable mobile manufacturing solutions. This includes guidance on quality, inspection, and oversight.
An example of the regulatory challenges that exist includes how to ensure the ongoing compliance status of a mobile manufacturing facility when it is relocated or replicated. Another example is how an organisation’s Quality Management System can be applied to mobile manufacturing facilities.
It’s important to note that this is not a completely new area for regulators. For example, in the US, the system for people to donate blood is decentralised, with mobile blood banks inspected by the FDA every two years to ensure compliance with 21 CFR Part 606. Similar provisions exist in the EU that enable mobile blood donation facilities.
The Covid-19 pandemic also gave regulators and life science sector companies experience in completing virtual compliance inspections. Our team at SL Controls developed a virtual inspection solution that solved an immediate need during the pandemic but also has potential applications in ensuring the ongoing compliance of mobile manufacturing facilities.
Rapid Deployment and Redeployment
A key feature of successful mobile manufacturing facilities is likely to be rapid deployment and redeployment capabilities. Engineering, validation, transportation, installation, and commissioning solutions will need to be developed and refined to meet this requirement.
Skills Availability
Mass manufacturing strategies have financial advantages, but skills availability is another important consideration, especially in the life sciences sector. The availability of skills means a large percentage of production in the sector takes place within established ecosystems.
Ireland is a good example, as it has a strong life sciences sector ecosystem that includes high levels of employee skills as well as established companies that provide support services to pharmaceutical and medical device manufacturers.
With mobile manufacturing, factory-in-a-box solutions can be installed in locations with minimal skills availability. Organisations will need to develop plans to overcome this challenge by, for example, maximising automation. Training strategies might also be part of the solution.
The Potential of Mobile Manufacturing
Mobile manufacturing is not the only way to achieve decentralised production. Furthermore, decentralised production is not going to be the best strategy in all situations. What is becoming clear, however, is that innovation in the development of medicines and other treatments is placing an increased requirement for new manufacturing solutions. Mobile manufacturing is likely to have an important role to play in bringing elements of healthcare to more people faster, more efficiently, and more economically than before.
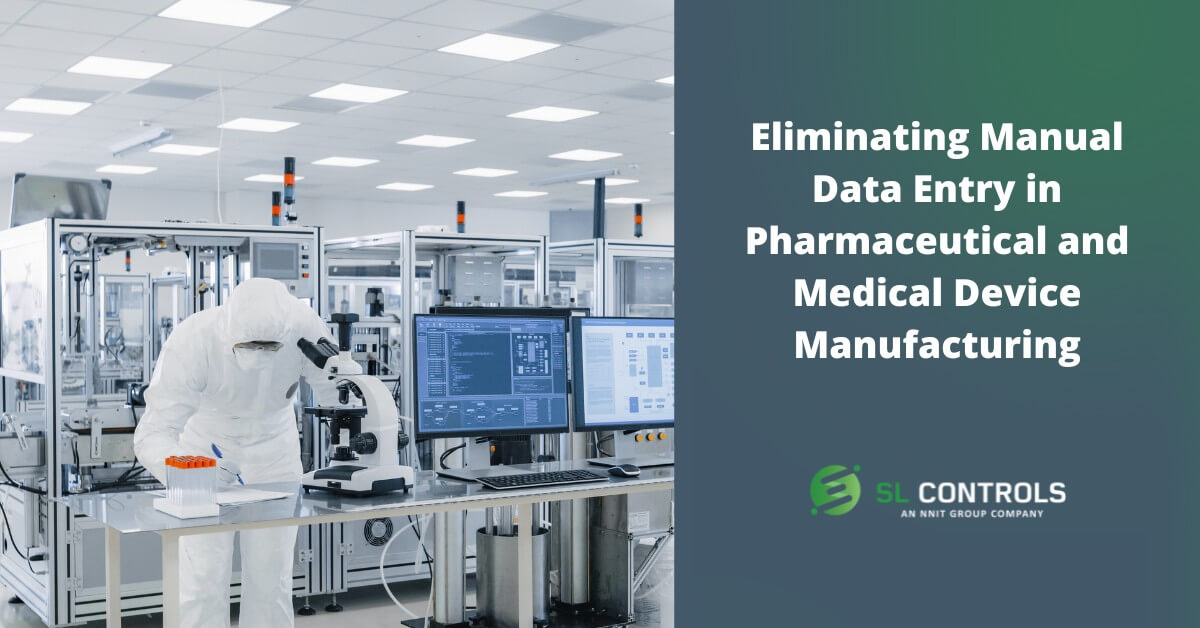
Eliminating Manual Data Entry – An Essential Requirement for Pharma and MedTech Manufacturers
Digitalising pharmaceutical and medical device manufacturing facilities is a high priority for companies in the life sciences sector. Achieving this priority involves developing fully integrated production lines while maintaining (and improving) compliance with GxP regulations. Eliminating manual data entry is an essential requirement to reach this level of digitalisation.
The rewards of creating the fully digitalised factory of the future are great – enhanced productivity, less reliance on increasingly difficult-to-find labour, and improved competitiveness, resilience, and profitability, to name a few.
However, the digitalised life sciences sector factory of the future requires full equipment and systems integration built on a foundation of integrated data.
Why Integrated Data is Essential
Manual data entry processes restrict pharma and MedTech manufacturing facilities from realising the full potential of advanced technologies such as digital twins and artificial intelligence (AI), i.e., technologies that rely on accurate, well-structured, real-time data.
Furthermore, the science behind innovations in the pharmaceutical and medical device industries is moving at pace, and production processes need to keep up. Personalised medicines such as cell and gene therapies are a good example, as the process of manufacturing personalised medicines is far too complex to manage with manual data entry.
Why Manual Data Entry is Not Suitable for the Digitalised Factory of the Future
Manually Entered Data is Inconsistent and Unstructured
A single piece of data can be recorded in a range of different ways. Dates and times are good examples, as there are many different ways of recording a date or time. This results in inconsistencies, and it is difficult to do anything with inconsistent or unstructured data beyond its raw existence.
Manually Entered Data is Prone to Human Error
Errors in manual data entry can occur for a range of different reasons. Staff might not be properly trained, for example, or mistakes can happen because of work pressures or workload spikes. Simple typos are another problem, and ambiguous or unclear data can cause issues.
Mistakes can also occur if record keeping is not contemporaneous, i.e., where systems are not updated at the time of recording the data. Any time lag between recording the data and entering it into the system increases the risk of error.
Manually Entered Data is Subject to Bias and Can Be Contested
Operator biases, either conscious or unconscious, can corrupt data that is recorded manually. This reality combined with the inevitability of human error means all manually entered data can be contested.
Manually Entered Data Creates Bottlenecks and Restricts Productivity
Manually entering data takes time, so it can create bottlenecks on production lines as well as in quality control processes. The potential for productivity improvements is also limited when operators have to spend time manually entering data.
Manually Entering Data is Labour Intensive
Manually entering data requires resources, plus it is not a task that can be considered value-adding.
Manually Entered Data Limits Real-Time Insights
When manual data entry processes are used, it is not possible to rely on the completeness or accuracy of real-time data.
Integrated Versus Automated Data
While the elimination of manual data entry is essential for pharma and MedTech manufacturers, it is also important to highlight the difference between automated data entry and integrated data.
With automated solutions, data is collected by devices and sensors in real time. This is significantly better than manual data entry, but it is an approach that is fragmented if the various systems and equipment, including legacy systems, are not integrated.
Therefore, integrated data goes further than automated data entry as it eliminates this fragmentation.
The Transition from Manual Data to Integrated data
The transition from manual data to integrated data involves integrating equipment and systems across the organisation and beyond. This includes operational technology on the production line as well as IT systems across other departments and business units. It often also involves integration across the supply chain.
It is important that manual data entry is eliminated entirely as any manually entered data that is merged with integrated data will corrupt the wider data stream.
However, the move to fully integrated data cannot typically occur overnight. A staged process is more realistic, but controls and processes can be put in place to minimise manual data entry risks. For example, instead of an operator typing an entry into a field, they should select a pre-defined option in a drop-down.
Advances in technologies and the capabilities of modern MES platforms are presenting significant opportunities for manufacturers in the life sciences sector – opportunities to modernise, improve, and innovate. The elimination of manual data entry and replacing it with integrated data is central to success.
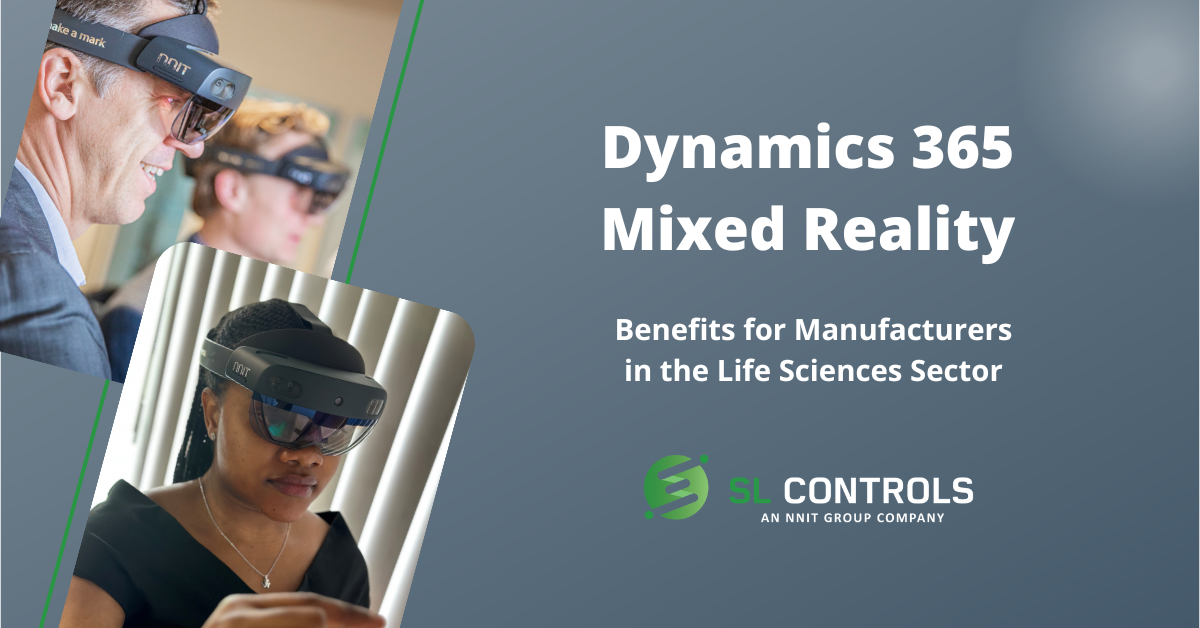
The Benefits of Dynamics 365 Mixed Reality for Manufacturers in the Life Sciences Sector
Cutting-edge technologies are helping manufacturers in the life sciences sector improve productivity while also addressing challenges – challenges that include skills availability, product quality consistency, production oversight, and OEE (a measure of equipment and overall production line performance). Examples of these cutting-edge solutions include Manufacturing Execution Systems, process automation solutions, and equipment systems integration solutions. Another example that doesn’t get as much attention is mixed reality.
Mixed reality technologies have a low capital investment requirement that can produce impressive results. Before looking at how mixed reality can benefit manufacturers in the life sciences sector, let’s first define what mixed reality is and the main technologies that are available.
What is Mixed Reality?
Mixed reality (MR) is the lesser-known sibling of virtual reality (VR) and augmented reality (AR). You typically use a headset with all three technologies. VR involves entering a completely virtual environment. AR, on the other hand, keeps you in the real world and overlays it with digital content. What about MR?
MR takes AR a stage further, creating a range of opportunities for life sciences manufacturers. Not only does it overlay digital content onto the real world, but it lets that digital content interact with physical objects. Users can also interact with the digital content, including moving and manipulating digital objects and holograms.
What is Microsoft HoloLens?
Microsoft HoloLens is a leading mixed reality technology that offers a range of features that bring benefits to life sciences manufacturers. For example, it recognises hand gestures to make digital objects act like physical objects. It also has built-in voice support and highly precise spatial mapping capabilities.
Plus, as HoloLens is a Microsoft product, it also seamlessly integrates with other Microsoft tools and technologies, including Power Apps, Dynamic 365 Guides, and Microsoft Teams.
Applications for Mixed Reality Technologies in Medical Device and Pharmaceutical Manufacturing
Quality vs Compliance Training
The root cause of many customer complaints and CAPAs (corrective and preventive actions) in life science manufacturing is often misdiagnosed as human error, and the corrective action is typically a retraining procedure. In many cases, however, the real root cause is inadequate competence levels. Up until recently, we did not have platforms to properly measure and monitor competence. Microsoft HoloLens, together with Microsoft Community training, creates an immersive and highly interactive training experience, making it an ideal solution for improving and monitoring the competence of resources.
These technologies are key enablers of a paradigm shift that allows the industry to move the needle away from being overly focused on compliance and back towards quality, restoring the equilibrium between these two important concepts.
Furthermore, SOP training created on Microsoft HoloLens devices ensures all staff receive the same quality of training, plus it is straightforward to keep the training up to date if the SOP changes. The technology also enables Just-in-Time Competence.
Our Parent company, NNIT, has been working with this cutting-edge technology. The NNIT Mixed reality team, headed by Kasper Kronmann Nielsen, has created a whitepaper on the Microsoft learning platform. It explains how to achieve the Dynamics 365 Guides mixed reality for regulated industries.
Remote Support
Traditionally, getting support for manufacturing equipment involved a specialist engineer travelling to your facility. At best, this could take hours and considerably longer if the engineer wasn’t in your region, country, or even continent. Remote support solutions eliminate unnecessary delays, but the quality of support can be fragmented and inconsistent. This is because of the challenge of replicating the experience of a specialist engineer actually being on-site.
Until the introduction of Microsoft HoloLens, that is. By utilising the HoloLens, a specialist engineer can see through the eyes of a technician on-site to deliver accurate instructions to resolve the problem. The engineer can even demonstrate how to carry out a task using a digital object that the on-site technician can replicate in the real world using the physical object. The process can also be recorded on the device as a knowledge asset and for training. The application that enables this functionality is called the Dynamics 365 remote assist.
Benefits of Mixed Reality Technologies for Medical Device and Pharmaceutical Manufacturers
The main benefits of mixed reality technologies for SOP training in the life sciences sector include:
- Employees enjoy immersive training experiences with realistic simulations.
- The training platform is highly interactive, so employees learn by doing. Evaluations can also be created to verify and validate that users understand the training and can improve their competency.
- The training can be completed in any location, improving the efficiency of the training process, and reducing costs.
- The training is completed in a safe and controlled way, so will not impact live production lines or processes.
For remote support applications, Microsoft HoloLens offers a range of benefits:
- Real-time support with specialist engineers that involve no unnecessary waiting or travelling.
- Reduced downtime because of the elimination of unnecessary waiting time for specialist engineers to support an equipment event.
- Support is received hands-free unlike, for example, using a phone to engage with a remote support engineer, where one hand is occupied holding the phone. The hands-free nature of mixed reality technologies means technicians receiving the support can use their hands to complete tasks and follow instructions.
- Improved quality of support as the specialist engineer can see and experience exactly what is happening with the machine or equipment.
- Reduced costs as you eliminate call-outs and related fees.
Summary
Microsoft HoloLens brings the holograms you see in science fiction movies to real life with practical applications in pharmaceutical and medical device manufacturing facilities. Whether you use this technology for remote support, training, or both, the benefits are impressive, and you can expect a rapid return on investment.
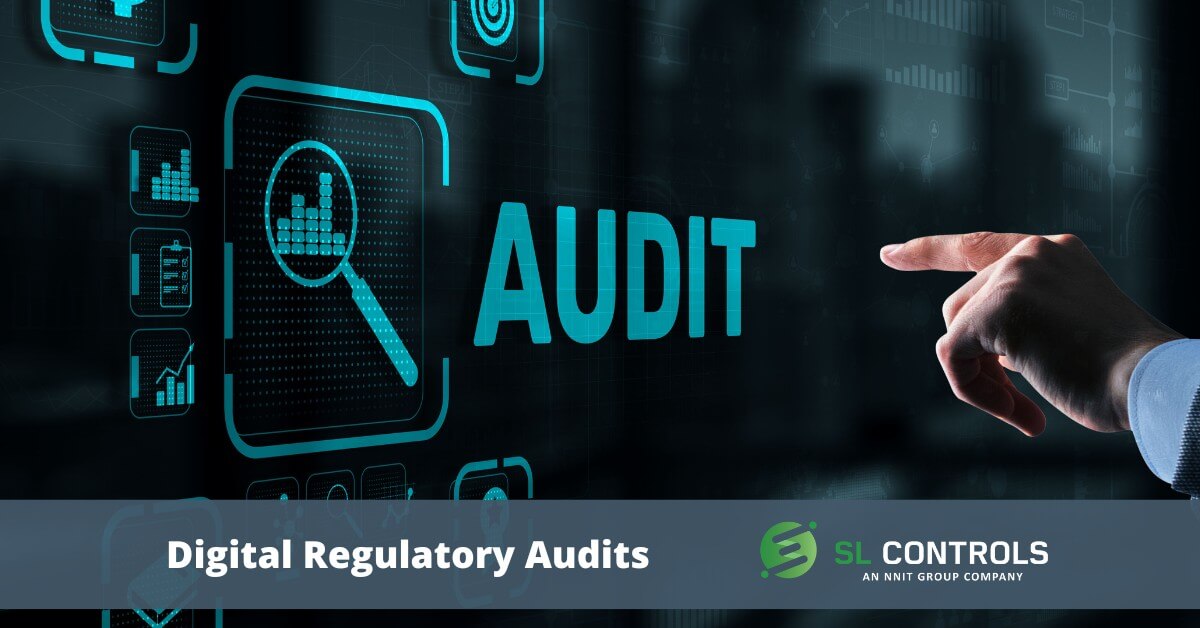
Digital Regulatory Audits – the Fully Compliant, Less Costly, and More Efficient Solution
Like other companies, manufacturers in the life sciences sector faced a number of challenges during the Covid-19 pandemic. One specific and unique challenge was how to conduct a regulatory audit when people couldn’t travel and there were restrictions on who could meet, where, and when. At SL Controls, we developed and successfully implemented a digital audit solution to overcome this challenge.
We worked together with a multinational customer in the life sciences sector to develop our digital audit solution. While the solution made it possible for our client to overcome an immediate challenge, it has retained its benefits beyond the pandemic as well as having wider use cases for medical device and pharmaceutical manufacturers.
Transforming Regulatory Audits in the Life Sciences Sector
Regulatory audits in the life sciences sector are essential for product quality and patient safety. However, they are also resource-heavy, often involving upwards of 60 people. Some of those people may only be needed for a small part of the audit, but they are still needed. Traditionally, that has meant getting everyone together in the same location, from validation staff to subject matter experts to external auditors.
SL Controls co-founder and Chief Digital Architect, Shane Loughlin said: “When we were approached by our client about developing a digital audit solution, we decided to take a step back to look at what an audit process is and what it involves. When we did this, we could see that audits are, at their core, collaboration events.
“So, in developing this digital audit solution, what we were actually creating was a digital collaboration platform. It needed tweaks, adjustments, and specific features to ensure it met the standards and requirements of regulators and our customers. But it was a digital collaboration platform, nonetheless.
“We are excited by this concept as the solution has much wider use cases beyond enabling regulatory audits in pandemic situations. It has the potential to become the standard approach for regulatory audits in the life sciences sector, and it can be tailored as a digital collaboration tool for other applications.”
The Importance of Compliance When Collaborating Digitally
There are lots of digital collaboration platforms available. The difference between standard digital collaboration platforms and the solution we have developed is compliance, i.e., our solution meets the compliance requirements of auditors in Europe, the US, and elsewhere around the world.
SL Controls Compliance Director, Dermot McMorrow, said: “The big difference with our solution is that it is fully compliant on the IT security side of things. As a team, we had been thinking about this for some time before Covid-19 as we knew this was the way things were going. The pandemic acted as a catalyst, so we are now way beyond the proof-of-concept stage.
“The solution has been developed, tested, proven to be effective, and then used in multiple audits of companies in the life sciences sector.
“The results have been impressive, too. Both companies and auditors found the process at least as smooth and seamless as the traditional in-person approach, with most saying it was an improvement. There have also been considerable efficiency and cost savings, primarily through improved communication and control, and the elimination of travel.”
Secure, Compliant, and Effective Digital Collaboration in the Life Sciences Sector
In developing the new digital audit and collaboration solution, we looked for ways to automate and streamline as many of the processes as possible. Systems Engineer Blessing Nwachukwu worked on the project.
“We worked closely with our client on the development of our new digital audit solution. Automating processes was a crucial consideration, as was making the solution as seamless as possible. We also had to ensure the process was integrated into the Microsoft platform to create an effortless experience for the users. The solution can connect people from any location to participate in an audit, making it fully remote-enabled.
“Our initial thought was to host the platform on an external domain, but that created connection and accessibility difficulties. We moved instead to hosting the platform on the customer’s domain using Microsoft Teams and its suite of apps.
“After conducting tests and mock audits, we supported our customer on their first live audit. It was an HPRA audit, so the auditors were in Ireland, but everything was done remotely. The audit went smoothly, and it was successful. This led to more audits and, so far, we have successfully supported our customers in 16 different regulatory audits using our digital solution. Each one resulted in positive feedback.
“This solution and the technologies that make it possible represent an important milestone in the modernisation of the compliance processes that are so essential in the life sciences sector. At SL Controls, we are continuing to refine and expand the solution, and we are enthusiastic about its potential.”
If you would like to find out more about our digital audit solution for the life sciences sector, please get in touch with us today.
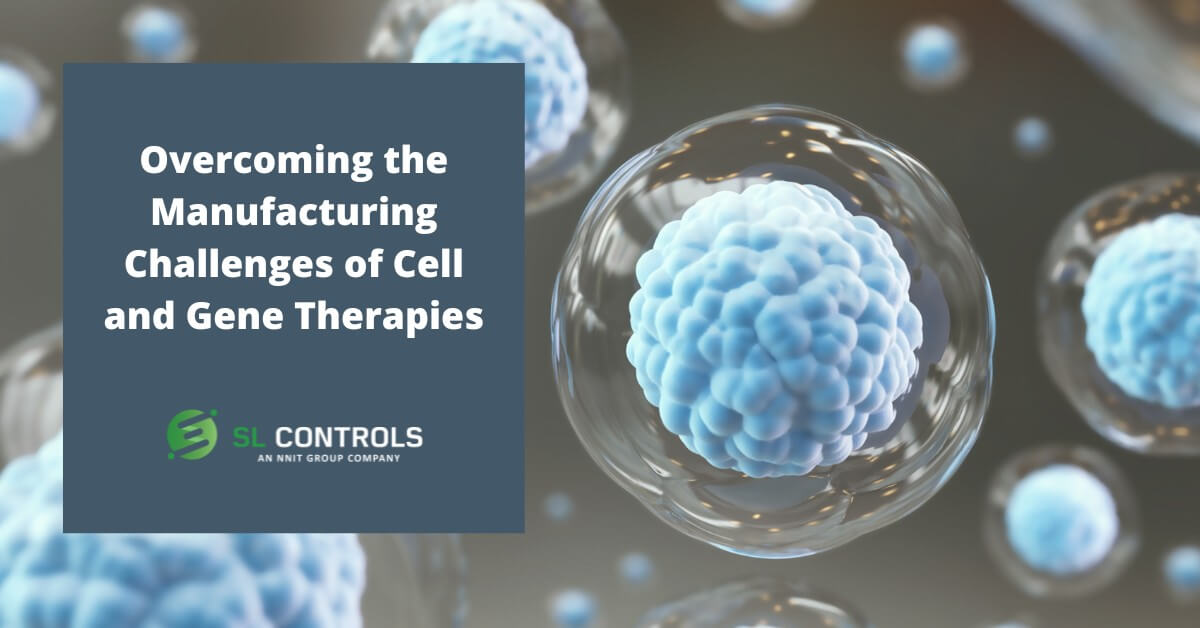
Overcoming the Manufacturing Challenges of Cell and Gene Therapies
Considerable progress has been made in the development of cell and gene therapies (CGTs) over recent years. Many new CGT products have already been approved by regulators in the US, EU, and other parts of the world, and many more are in development. The most exciting part is the improvements in patient outcomes that CGTs can potentially achieve. This applies to a range of conditions, including rare and difficult-to-treat conditions such as cancer.
Furthermore, there is an expectation for many CGTs in development that they will be curative, so will replace the lifelong treatment of chronic diseases. In some cases, there is the possibility to achieve this with a single treatment.
While the potential of CGTs is game-changing, there are significant challenges and barriers to overcome – challenges and barriers that are limiting the development and widespread use of CGTs. Examples of those challenges include:
- Clinical trial challenges, including finding enough trial participants, particularly when therapies are being developed for rare conditions.
- Complex regulatory processes that are still evolving.
- Commercialisation, value realisation, and profitability challenges.
Manufacturing is another major challenge limiting the deployment of CGT therapies. It is those manufacturing challenges that we will explore in this blog.
The Challenges of Manufacturing CGTs
Manufacturing CGTs is considerably more complex than manufacturing most other pharmaceutical products.
Specialist facilities are needed, and they are in short supply.
Specialist skills are also needed, and they are in even shorter supply.
While all CGTs present complex manufacturing challenges, including allogeneic (i.e., off-the-shelf) therapies, autologous cell therapies are among the most complex.
With autologous (personalised) therapies, cells are taken from a patient, often in a hospital setting. They are then sent to specialist manufacturing facilities where the therapy is manufactured and sent back to the hospital to be administered to the patient. The challenges of this process are numerous, but the main issues include:
- Time – many autologous cell therapies are highly time-sensitive, i.e., the therapy needs to be administered to the patient as soon as possible after the cells are extracted. This can be for many reasons, including the fact that some patients are in the late stages of disease, so simply won’t survive to receive the treatment if the manufacturing process takes too long.
- Distance – the specialist facilities needed to manufacture CGTs can be located far away from the patient’s clinical setting. This is already a problem in places like the US and Europe, but it is even more of a challenge when other regions of the world are considered.
- Raw materials – many of the raw materials required to produce CGTs are non-conventional, including cells taken directly from patients. This presents supply challenges.
- Quality control – strict quality control procedures need to be followed throughout to prevent contamination, for example, or to maintain the right temperature and environmental conditions at all stages of the process.
- Logistics – even the smallest logistical hiccup can have serious consequences. In fact, the logistical precision required to produce autologous cell therapies is practically impossible to achieve consistently and at scale using traditional manufacturing approaches. Chain of identity and chain of custody processes are also complex to create and manage.
The CAR T Example
CAR T is a cell therapy where chimeric antigen receptors (CAR) enable T cells to identify and kill target cells in the body. There are multiple CAR T products currently approved for use in the US and other jurisdictions. There is also increasing evidence of the effectiveness of CAR T therapies in inducing remission in patients with cancer and autoimmune diseases.
Despite its effectiveness and potential, the rollout of CAR T therapies has been severely limited. There are a number of reasons for this limited rollout, including the challenges faced by other CGT products. There are also CAR T-specific challenges, such as patients developing toxicities and minimal clinical response rates against solid tumours.
As with other CGTs, another major challenge to achieving widespread rollout of CAR T is the complexity and cost of manufacturing.
CAR T therapies are autologous therapies. As they are unique to each patient, they need to be manufactured in what is essentially a batch size of one. Time is also a critical factor with CAR T therapies, as CAR T therapies are most effective when administered as soon as possible after the T cells are harvested from the patient. Ideally, this should be days at most.
Personalised cell therapies currently take about 2-3 weeks to produce, but that is a best-case scenario. The reality is that even a 2-3-week production timescale is rare because of the availability of suitable manufacturing capacity and resources, and the complex logistics that are involved.
That is before you even factor in financial and scalability considerations, both of which are essential to make CAR T therapies widely available and affordable for hospitals and patients, as well as profitable for pharmaceutical companies.
Overcoming the Manufacturing Challenges of CGTs
Allogeneic therapies are more compatible with traditional centralised manufacturing approaches. However, innovative solutions will need to be developed to overcome the challenges of manufacturing autologous therapies. Many allogenic therapies will also benefit from these new manufacturing solutions.
There are six main areas that need to be addressed to overcome the manufacturing challenges of CGTs.
Product Development Cycle
It is essential that manufacturing is considered early in a CGT product’s development cycle.
Expanding Capacity
Additional CGT manufacturing capacity is required, although how that is developed and structured is likely to require a novel approach – see the last point below.
Increasing Skills Availability
The industry needs to increase the availability of skills to ensure manufacturers can recruit and retain the people they need. The fact there is a skills shortage at the moment is understandable as CGTs are an emerging part of the life sciences sector. However, CGTs are expected to continue growing rapidly, so it makes sense to address the skills shortage urgently.
Automate Manufacturing Processes
Automation will play a crucial role in making CGT manufacturing viable both from a practical and financial perspective.
Supply Chain Optimisation
CGT manufacturing supply chains need to be optimised to ensure a consistent supply of materials, including materials such as viral vectors and plasmids.
Bring Manufacturing Closer to the Point of Care
This solution to CGT manufacturing challenges will be the most disruptive, but it also has the potential to be the most transformative. By bringing manufacturing closer to the point of care through innovations like mobile manufacturing facilities or manufacturing-in-a-box concepts, the production of CGTs becomes much more viable:
- The time it takes to manufacture CGTs will be considerably reduced.
- The number of steps will be minimised.
- Human involvement in the manufacturing process will be minimised, particularly when combined with automation technologies.
- The logistical challenges that currently exist can be minimised and potentially eliminated.
The Starbucks Model
There will need to be detailed collaboration between hospitals and manufacturers, but taking a Starbucks approach is likely to be the best route to ensuring the widespread adoption of CGTs, particularly autologous therapies.
The highly skilled team at Starbucks’ Seattle headquarters can probably make a delicious cup of coffee. However, that is no good if you are in Boston, Dublin, Rio de Janeiro, Nairobi, Hanoi, or Auckland. By the time it reaches you, what’s left in the cup will be cold and horrible. What you need is a Starbucks close to the point of need with well-trained baristas using specialist equipment and carefully sourced ingredients.
As mentioned previously, the Starbucks approach is a disruptive model for an industry that has achieved significant success using high-speed, high-volume manufacturing. However, to keep up with the scientific advances being made in CGT development, manufacturers need to embrace this new level of innovation and disruption.
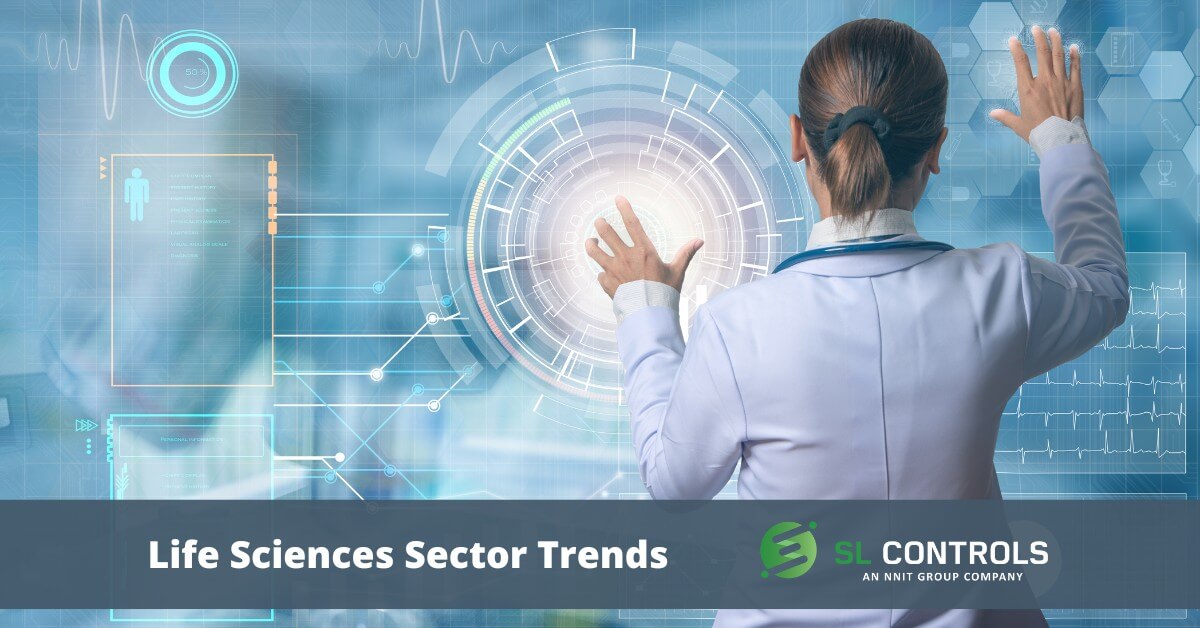
9 Game-Changing Trends in the Life Sciences Sector
The life sciences sector continues to grow as new therapies, drugs, and products are developed. New manufacturing and business technologies are also driving change in the sector, as are ever-evolving regulations and best practice guidelines. So, where is the sector heading?
Here are nine game-changing trends in the life sciences sector to be aware of:
- Cell and gene therapies
- Mobile manufacturing
- Externalisation
- Additive manufacturing
- Decentralised trials
- Digital twins
- Growing importance of big data and analytics
- Move away from paper documentation and manual record-keeping
- Validation for the 21st century
Let’s look at each in more detail.
Growth in Cell & Gene Therapies
The life sciences industry is increasingly focusing on treating the patient rather than the condition or illness. Cell and gene therapies (CGT) have this patient focus, with significant growth expected in CGT use over the coming years.
New CGT innovations are being developed, but these types of treatment are expensive. They are also often challenging to manufacture, as CGTs are typically customised for each patient so need to be produced in small batches. Also, production processes often need to take place much closer to the patient than is currently the case with the sector’s mass manufacturing infrastructure. This leads us to the next key trend in the life sciences sector.
Mobile Manufacturing
Companies in the life sciences sector are digitalising workflows and processes to transform business models and develop smart manufacturing operations. The next big change on the horizon is mobile manufacturing, creating an alternative to large-scale manufacturing facilities and large-batch production runs.
Mobile manufacturing solutions won’t be required for all products, but the example of CGT therapies highlights the growing need for the sector to develop new and innovative methods of production that bring manufacturing closer to the point of care. These solutions need to be scalable, practical, compliant, and cost-effective, but progress is already being made.
Mobile manufacturing will also help to improve access to critical medicines and healthcare products, reducing the geographical and societal inequalities that currently exist around the world.
Externalisation
Contract Development and Manufacturing Organisations (CDMOs) and Contract Manufacturing Organisations (CMOs) have been an important part of the life sciences sector for many years now. Their importance is now growing as small, medium-sized, and large life sciences sector companies continue to turn to CDMOs and CMOs, primarily for capacity, expertise, and timing reasons.
For example, large medical device companies regularly hand over elements of product development projects to a CDMO when they need specific expertise or because of insufficient internal capacity. Another example is startup companies that can bring their new product to market faster by partnering with a CMO compared to acquiring the skills, resources, technologies, and equipment that would be required to manufacture the product in-house.
Additive Manufacturing
3D printing technologies are already being used for prototyping in the product development process, as well as to produce prosthetics, implants, and other healthcare products. This trend is set to continue as the technologies available move beyond 3D printing to enable 4D printing.
4D printing creates 3D objects where the properties of the object can change over time in a way that is predictable. Stents are an example. Currently, stents are fixed objects with fixed properties. When 4D printing technologies become available, it will be possible to produce stents that have one shape while progressing through the body before automatically taking the required stent form when they reach the target treatment location.
Decentralised Trials
Clinical trials have traditionally been centralised largely because there was no other option. One of the main problems with this approach is achieving a sufficiently diverse range of participants. It is also expensive and time-consuming. New technologies, including wearable devices, now mean decentralised clinical trials are a viable option, increasing the diversity of participants.
One model is to involve local pharmacies in clinical trials, tapping into the data they have on potential participants.
Digital Twins
Digital twins are common in a range of situations, including production environments where digital twins can be created for individual machines or entire production lines. New technology advances are also pushing the concept of the digital twin into the field of healthcare, with many predicting there will be digital twins of people in the future.
These digital twins can be used to test drugs and medical devices, as well as to predict the outcome of various treatments. This can reduce animal testing, optimise clinical trial processes, and improve the diagnosis and treatment of patients.
Growing Importance of Big Data & Analytics
Reducing timescales while maintaining product quality, patient safety, and regulatory compliance has always been a priority for the life sciences sector. Despite this, the process to discover new drugs, develop new products, and obtain regulatory approval remains slow. The rapid development of Covid-19 vaccines showed us an alternative future, where timescales can be considerably shortened to the benefit of patients, healthcare professionals, governments, companies, and society as a whole.
Big data and analytics are crucial to shortening the lengthy timescales that exist in the life sciences sector. Here are some examples:
- Choosing clinical trial participants
- Real-time monitoring of critical quality attributes
- Accelerating drug discovery
- Improving production processes and supply chain management
- Demonstrating post-market drug safety and efficacy
Finally Moving Away from Paper Documentation and Manual Record-Keeping
The life sciences sector continues to digitalise and adopt new technologies and automation solutions. However, there are still large parts of the sector that are reliant on paper and/or manual record-keeping processes. This reliance on paper includes producing large amounts of documentation for compliance purposes.
The trend to move away from paper documentation and manual record-keeping will continue. It will also accelerate as modern technologies are adopted and processes are automated. The need for real-time data and the importance of data-driven decision-making are additional drivers for change. Furthermore, the evolving regulatory landscape is also encouraging a move away from paper, leading us to the next point.
Validation for the 21st Century
The traditional method for validating computer systems in the life sciences sector, Computer System Validation (CSV), involves manufacturers focusing heavily on the creation of documentation. The FDA has now released draft guidance on a new approach known as Computer Software Assurance (CSA).
With CSA, the FDA expects manufacturers to move away from focusing on the creation of documentation. It instead wants manufacturers to take a risk-based approach to validation with critical thinking at its core.
Staying Competitive While Pushing the Boundaries of Innovation
Some of the trends on this list are current realities, while others are emerging at the cutting edge of development. The trends also present both opportunities and challenges for companies in the life sciences sector. Understanding where the industry and technology are going can help you stay ahead of the curve.
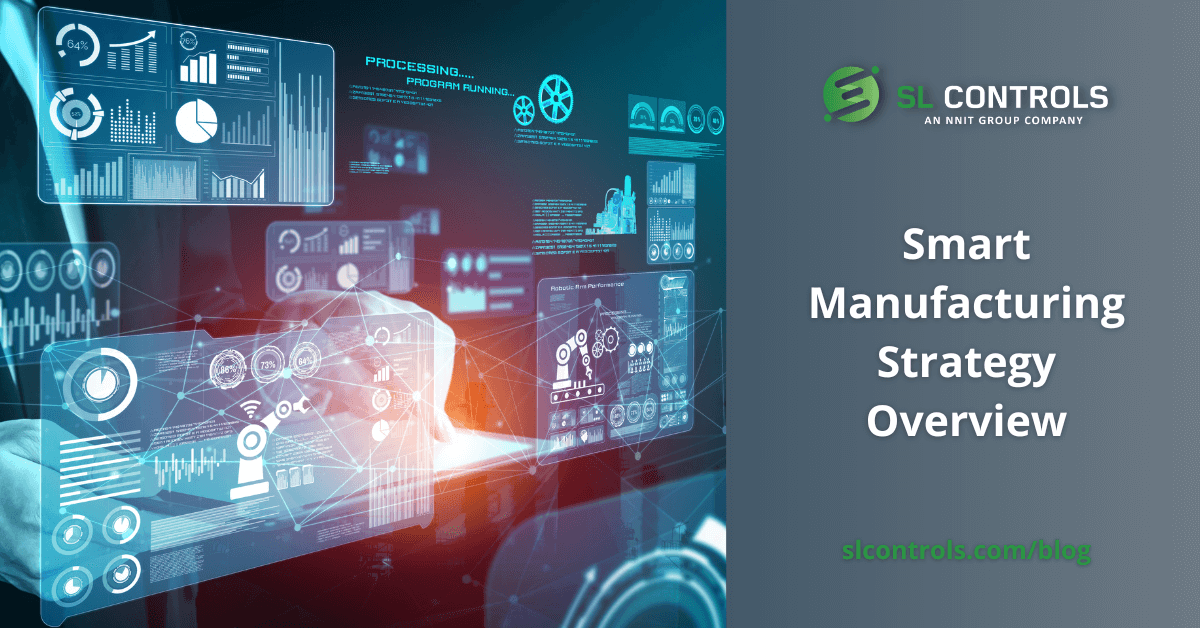
Smart Manufacturing Strategy Overview for the Life Sciences Sector
All sections of the life sciences sector understand the need to evolve operations using the cutting-edge technologies, processes, and best practices that come under the smart manufacturing umbrella. However, it’s important to take a structured approach, with a carefully developed and implemented smart manufacturing strategy.
In this blog, we’ll look at why it is important to develop an overarching smart manufacturing strategy, as well as providing an overview for creating one. The strategy overview that we present is relevant wherever you are on your smart manufacturing journey.
Change in the Life Sciences Sector and Why a Well-Structured Change Strategy is Important
The fact the life sciences sector is experiencing unprecedented change has been a common topic of discussion for some years now. The reality goes deeper than the concept of change, though, as change implies there will be an endpoint or conclusion.
However, the more likely scenario is that the life sciences sector has entered a period of ongoing change. New technologies are now developing at such a rapid pace that continuous evolution is now a reality and a necessity. Technologies like Microsoft’s HoloLens is a good example. It is now commonly used in many industrial applications, but nothing even close to it existed 10 years ago. Examples like this will become more commonplace over the coming years.
The ongoing changes that are taking place are not just the purview of technologies, either, as the life sciences sector is also experiencing changing customer expectations, markets, and products, all of which present opportunities. There are challenges too, of course, including skills, economic, business resilience, regulatory, and geopolitical challenges.
Smart manufacturing solutions help companies in the life sciences sector take advantage of the opportunities while addressing the challenges.
The Continuous State of Change – an Example
An example we can use to highlight the continuous state of change in the life sciences sector is the emerging trend of manufacturing operations needing to innovate at speed to keep up with cutting-edge product development breakthroughs.
A specific example is personalised pharmaceutical products that need to be produced as close to the patient as possible.
This means moving away from the mass production approach that has served the life sciences sector so well for decades (and other sectors for even longer). Instead of large manufacturing facilities producing and shipping products far and wide to reach the patients who need them, many personalised medicines will require batch-size-of-one manufacturing processes and, potentially, factory-in-a-box solutions where manufacturing capabilities, rather than the manufactured product, are brought to the patient.
Adopting a smart manufacturing approach is the only way to address the needs of today (productivity, competitiveness, quality, compliance, etc), as well as keeping up with the developments of the not-too-distant future (such as those in this example).
What is Smart Manufacturing?
It is helpful when developing a smart manufacturing strategy to look at what we mean by “smart manufacturing”. Some definitions include descriptions like the digitalisation of manufacturing processes. Automation is a key component, but it is only one element. Becoming a data-driven operation is also crucial.
However, it is often better to look at smart manufacturing through the lens of outcomes and objectives. Examples include:
- Improvements in key manufacturing metrics such as OEE and productivity.
- Improved resilience to deal with market challenges as well as enhanced agility to take advantage of commercial opportunities.
- Enhanced scaling capabilities while enabling production facilities to be more flexible, including in relation to producing different products on the same line.
- Creating connected operations, whether connected across different facilities, production lines within the same facility, or equipment on a single production line. It also involves connecting manufacturing operations with other business units and departments.
All the above objectives and outcomes can be achieved with a well-structured and implemented smart manufacturing strategy.
Smart Manufacturing Strategy Overview
Step 1 – Define Objectives and Vision
The first step is to look at your production operations, wider business strategy, and corporate objectives. This includes:
- Immediate business challenges and risks
- Medium and long-term business goals
- Manufacturing and operational priorities
Step 2 – Identify a Partner
Getting the right partner is essential to help with both the planning and implementation of your smart manufacturing strategy. The qualities you should look for in a smart manufacturing partner include:
- Expertise in the life sciences sector as well as specific pharmaceutical and/or medical device industry experience.
- Broad range of technology expertise.
- A proven track record of delivering smart manufacturing projects in the pharmaceutical and medical device industries.
- Established expertise in the essential aspects of smart manufacturing projects, including change management, project management, equipment systems integration, and ongoing support.
Step 3 – Assess Digital Maturity
The roadmap to smart manufacturing success will depend on your existing situation. Therefore, assessing your current levels of digital maturity is essential. Elements to analyse include:
- OT (operational technology) and IT infrastructure
- Current processes and workflows
- Existing resources and skills, as well as resource and skills challenges
- Technology platforms, applications, and systems
- Production line equipment
Step 4 – Identify Challenges
Identifying the specific challenges faced by your organisation is also essential, as it allows the project management and implementation team to put in place mitigation measures and/or solutions. Challenges can be caused by a range of factors:
- Organisational
- Cultural
- Resources and skills
- Technology
- Financial
Step 5 – Define the Implementation Roadmap
This is the point where you decide on the next phase of development before implementing the project. Common steps include:
- Identify suitable project/s.
- Make sure your plans are in alignment with business objectives and adjacent projects.
- Create a business case and get organisational buy-in.
- Develop and implement a project implementation strategy, including technical and functional plans.
Taking the Next Steps
Delaying the next phase of your smart manufacturing journey will only set you further behind. The best approach is to start implementing the above strategy now to ensure your manufacturing operations evolve in step with the ongoing changes in the industry.
You don’t need to have all the answers, and you don’t even know what projects to undertake next. Looking at your business objectives and engaging a suitable partner will give you the answers you need while also ensuring you are on the path to success.
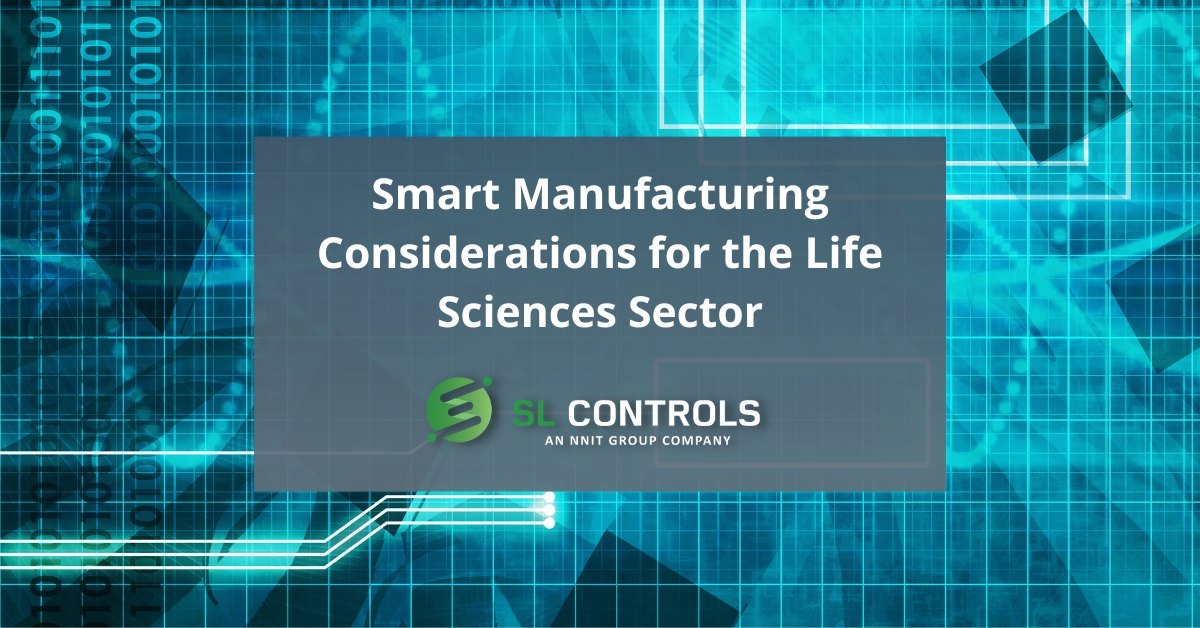
Smart Manufacturing Considerations for Pharma and MedTech Manufacturers
Most pharmaceutical and medical device manufacturers have implemented new technologies and processes over the past number of years that would come under the smart manufacturing umbrella. You are probably also now considering the next stage on your journey. What are the smart manufacturing solutions and opportunities that you should explore next?
There are a number of factors that are essential to consider when deciding on smart manufacturing projects and solutions. Crucially, those factors go way beyond the technical components, as it is important to also take into account business, resource, and process factors.
We’ll start with business and resource considerations before looking at processes and workflows. We’ll then finish off with the main technical considerations.
Smart Manufacturing Considerations – Business and Resources
Business Alignment
It is important to look at the short, medium, and long-term market and product strategies for your facility and throughout the organisation. What new markets do you plan to target? What new products do you expect to introduce? How do you see the industry evolving over the long term and how will your organisation remain competitive? What decisions are being taken in other parts of the business that will impact what happens on the factory floor?
When answering these questions, it is essential there is alignment between your smart manufacturing strategy and the strategies, plans, and objectives of the wider business. Furthermore, there should always be a business-led approach to technology implementations.
Wider Digital Transformation Initiatives in the Business
Efforts to improve your smart manufacturing capabilities should also be aligned with the wider digital transformation initiatives of the business.
For example, smart manufacturing and digital transformation technologies are creating new business models in the life sciences sector. Examples of these new business models include service rather than product-based business models and the expected growth of personalised medicines and treatments.
Buy-In from Senior Executives
Smart manufacturing technologies and solutions will play a major role in the digital transformation of pharmaceutical and medical device companies over the coming years and decades. This is in addition to the immediate positive impacts that advanced technologies and best practices can have on your business, from productivity improvements to increases in profitability.
Therefore, it is important senior executives are involved in the process and buy into the strategy.
Embracing New Approaches
Smart manufacturing solutions and other developments present opportunities for the life sciences sector to do things differently. Traditionally, however, the sector is slow to change, not least because of patient safety, quality, and regulatory concerns.
Change now needs to be accelerated in areas such as embracing data-driven and automated decision-making or moving to modern compliance frameworks. Just because things have been done a certain way in the past doesn’t mean they should continue like that in the future.
Other Business and Resource Considerations
The other main business and resource considerations for smart manufacturing strategies and projects include:
- Supply chain resilience – given the spotlight on supply chain resilience in the pharmaceutical and medical device industries, how can smart manufacturing solutions make an impact?
- Sustainability targets and objectives – it’s important to view smart manufacturing solutions and projects through the lens of sustainability, as there are often opportunities to make small changes that can have a positive impact.
- Regulatory compliance – there is a need for ongoing regulatory compliance, but there are also opportunities to improve compliance processes by making them more efficient, data-driven, and risk-based rather than procedural.
- Investment scale – how much are you willing to invest and when? What are your ROI expectations?
- Resource availability and multi-functional teams – what resources do you have available to work on smart manufacturing project implementations? Who will be part of the leadership group, and will the teams be multi-functional with members from different departments and business units?
- Third-party partners – you will also need to decide on a smart manufacturing solution and integration partner. The best approach is to select a partner that offers an end-to-end range of services and that has specific experience in the life sciences sector.
Smart Manufacturing Process and Workflow Considerations
Process and workflow factors also need careful consideration in smart manufacturing projects. Examples include:
- Get a full understanding of existing processes and workflows, including getting the viewpoints of those on the frontline. This is essential as the theory or perception of a process can be very different from the reality.
- Conduct a critical analysis of all processes and workflows once there is a good level of understanding. It is helpful to ask why you do things the way you do, and could certain workflows and processes be done better.
- What is the level of data integrity in the organisation and what steps should be taken to make improvements?
- What repetitive and time-consuming tasks can be automated?
- What tasks that are prone to human error can be automated or semi-automated?
- How can you improve processes and workflows to make production and the wider business more agile and adaptable?
- How can you enhance collaboration, especially cross-function collaboration?
- What is the change management strategy, and how will you communicate and solicit feedback from members of the team, particularly those directly impacted by the changes that smart manufacturing solutions will bring?
- What level of staff training will be required and how will that training be delivered?
- Where automated solutions replace manual processes, how will you reallocate resources?
Smart Manufacturing Technical Considerations
Finally, we come to the technical considerations that are important in smart manufacturing projects. The main examples include:
- The existing technology and equipment infrastructure and components.
- Equipment systems integration plans, i.e., what existing systems and equipment are staying so need to be integrated, and what is being added or replaced?
- Integration at all levels of the technology stack, including at the SCADA and PLC level on the factory floor as well as Manufacturing Execution (MES) and Enterprise Resource Planning (ERP) systems.
- The level of horizontal and vertical integration you want to achieve, i.e., integration between production operations and other parts of the business, as well as integration across the supply chain.
- How you currently use data and how that can be improved, enhanced, and optimised, from collection to transmission to storage, processing, and use.
- Strategies for legacy systems that are staying, especially in relation to the standardisation of processes, terms, data, etc.
- Your cloud strategy within the operational technology (OT) environment and how that is aligned and linked with the cloud strategy within the organisation’s IT infrastructure.
- Cybersecurity and the increased level of risk that comes with connecting more devices and expanding the potential attack surface of your organisation.
Getting the Right Expertise and Support
The lists and points above are not exhaustive, as there are typically other considerations that apply on a case-by-case basis. What they highlight is there are extensive considerations that have an influence on your direction of travel and potential for success when implementing a smart manufacturing project.
Therefore, it is important you get expert advice and support. To speak to one of our smart manufacturing specialists, please contact us at SL Controls today.
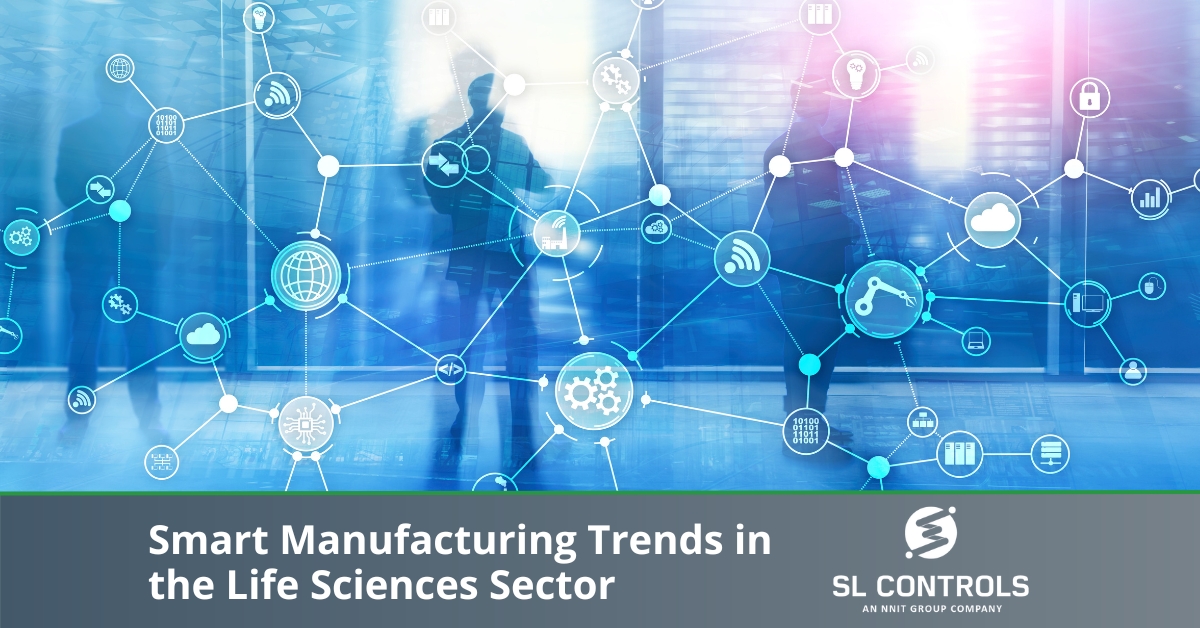
Smart Manufacturing Trends for 2023 in the Life Sciences Sector
Manufacturing in all sectors and industries is changing as smart manufacturing technologies, the industrial internet of things, and Industry 4.0 best practices continue to advance. What about the life sciences sector specifically? Here are the 2023 smart manufacturing trends that pharmaceutical and medical device manufacturers need to be aware of.
Integration of MES, SCADA, and ERP Systems
The integration of MES, SCADA, and ERP systems is essential for the digitalisation of manufacturing and other business processes in the life sciences industry. Achieving this integration will be a primary focus for manufacturers in the sector in the years ahead. The benefits of doing so range from product quality and patient safety to improved business performance, reduced risks, and enhanced data-driven decision-making.
Another trend that is a feature in the life sciences sector is the move away from clunky legacy MES platforms that required a lot of customisations. Pharmaceutical and medical device manufacturers are increasingly moving to more modern, adaptable, and flexible MES solutions that facilitate end-to-end connectivity.
Increasing Focus on Data Integrity
Data integrity is essential for the digitalisation and modernisation of manufacturing processes in the pharmaceutical and medical device industries. There are multiple steps that should be taken to ensure data integrity, but two primary focus areas for 2023 and beyond will be:
- Eliminating manual intervention in data collection, updating, and processing
- Bridging data gaps, both digital and paper-based
Accelerated Innovation with GAMP 5
The summer of 2022 saw the first major update of GAMP 5 since its introduction 14 years earlier. You can read more about what has changed in GAMP 5 Second Edition on our blog. One of the main outcomes, however, is an increased facilitation of innovation.
Many in the life sciences sector implemented the original version of GAMP 5 with approaches that were prescriptive and rigid. This hampered innovation.
With GAMP 5 Second Edition, there is a recognition of agile development methodologies and critical thinking, both of which encourage a move away from previous, prescriptive methods of validation. This will result in accelerated innovation in the sector over the coming years while still protecting patient safety and product quality.
Continued Development of Batch-Size-of-One Manufacturing Solutions
R&D efforts in the pharmaceutical and medical device industries are creating new, cutting-edge personalised medicine and healthcare solutions. This means there is now an increased onus on pharmaceutical and medical device companies to develop the manufacturing solutions that will enable the commercialisation of personalised drugs and medical devices.
One exciting area of this evolution of manufacturing in the life sciences sector is the concept of the factory-in-a-box, as well as microfactories. Both have significantly smaller footprints than traditional production facilities to maximise agility and flexibility, and to enable the moving of manufacturing operations closer to the patient.
ESG Considerations Driving Change
Environmental, Social, and Governance (ESG) factors have been high on the agenda of most leaders in the life sciences sector over the past 12 months. This trend is set to not only continue, but to accelerate over the coming year and beyond as pharmaceutical and medical device companies implement strategies and initiatives that deliver tangible results on their ESG commitments.
Continued Focus on Supply Chain Resilience and Capacity Building
One of the challenges faced by companies in the life sciences sector throughout 2022 was supply chain disruption. Capacity is also a common issue, with many in the sector operating with zero or close to zero spare capacity.
Both of these factors are increasing lead times for orders of many pharmaceutical and medical device products. Patients are also impacted, while life sciences sector companies are unable to take full advantage of the commercial opportunities that exist.
The sector has been adapting throughout 2022 to these challenges, and fantastic work has been done to maintain consistency and reliability in the delivery of orders. That said, supply chain and capacity challenges remain, and they are being exacerbated by current geopolitical uncertainties and turbulent economic conditions.
Therefore, we can expect a continued focus on supply chain resilience and capacity building as we move into 2023.
Innovation and Growth
Even with the challenges highlighted in the last section above, 2023 is set to be a year of innovation and progress for companies in the life sciences sector. New opportunities to streamline and improve manufacturing lines, increased levels of vertical and horizontal integration, and the ability to make better use of data, are all going to drive innovation and growth.
There are also going to be continued R&D breakthroughs in drugs and medical devices, creating new opportunities for manufacturers. The key message, therefore, is to not stand still with your smart manufacturing initiatives, projects, and strategies.
« Previous 1 2 3 4 5 … 18 Next »