News
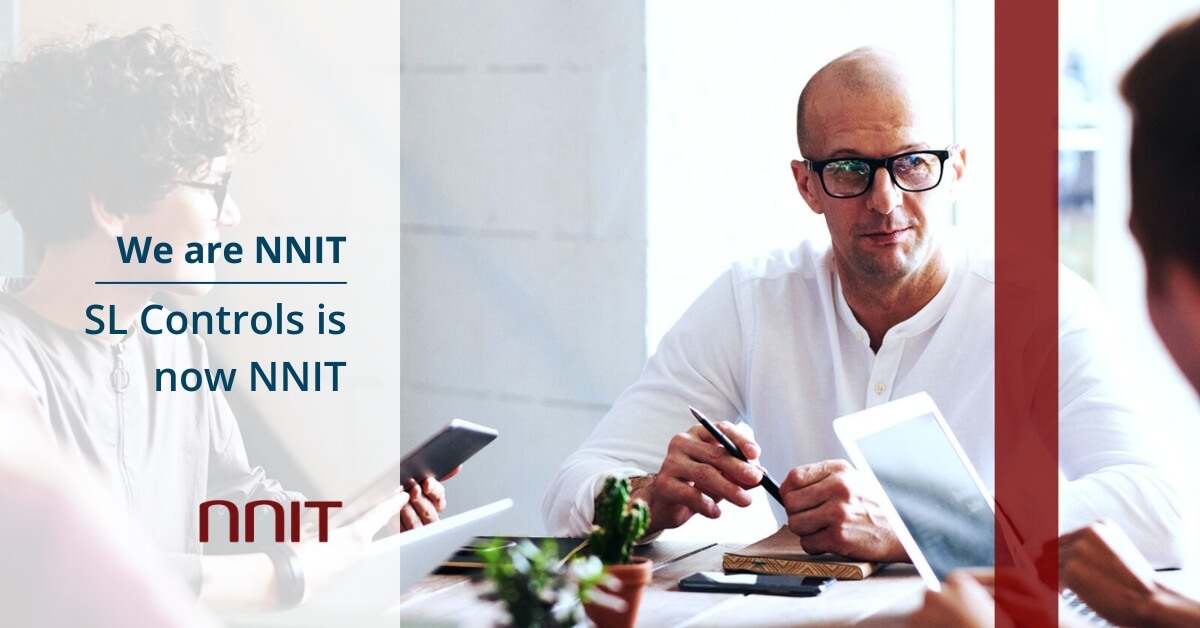
SL Controls Rebranding as NNIT as Part of Merging Initiative
Following our announcement earlier this month, the process of merging SL Controls with parent company NNIT is progressing well. Part of that merging process includes rebranding SL Controls as NNIT.
NNIT acquired SL Controls in 2021, immediately strengthening the service offering and value proposition offered to clients. Integration between teams in both organisations has been an ongoing process with fantastic work on all sides behind the scenes. That work includes communication with customers, suppliers, partners, and other stakeholders.
Over the coming weeks and months, the slcontrols.com website and other brand assets, both online and offline, will be fully integrated with NNIT.
Deirdre Loughlin at SL Controls, said: “Merging SL Controls with NNIT is a significant undertaking that will deliver considerable benefits to our customers and the wider life sciences sector. One of the most visual representations of that merger is switching off the SL Controls website and LinkedIn pages.
“You will now be able to find us on the Smart Factory section of the NNIT website.
“A great way to stay informed of our progress and to learn more about the end-to-end life sciences solutions that we offer is to follow us on the NNIT LinkedIn page.
“SL Controls is now NNIT, and we are excited for the future.”
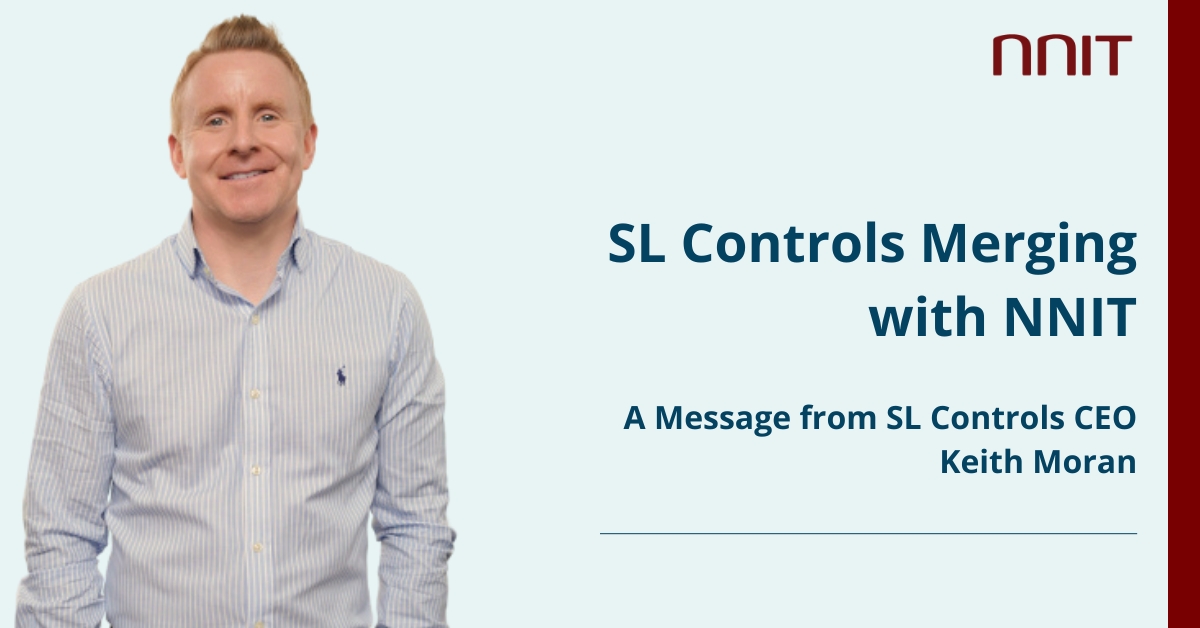
SL Controls Merging with NNIT – a Message from CEO Keith Moran
Following a huge amount of work by our fantastic team over many months, we are ready to announce that SL Controls is fully merging with our parent company, NNIT. This process will be completed in January 2025 and represents a very exciting time for the newly integrated SL Controls and NNIT team.
What does this mean in practice? The now former SL Controls employees will all become part of the Smart Factory and Supply Chain business unit within NNIT. All staff will remain in place to continue delivering Smart Factory solutions to our customers in the global life sciences sector. I will personally head up NNIT’s Smart Factory and Supply Chain solutions.
This merger will enhance the services we deliver to our existing clients while giving us even greater access to large-scale Smart Factory projects across Europe and around the world.
Natural Evolution
SL Controls was launched over 20 years ago and was acquired by NNIT in 2021. Merging fully into NNIT is the next step in our evolution. I am incredibly proud of our 150-strong team, and I am enthusiastic about the career opportunities offered by this integration.
I am also excited about the continuing impact we can have in the life sciences sector helping pharmaceutical and medical device manufacturing operations modernise and improve. Our whole ethos as a company from the beginning has been to support and facilitate the digital transformation of production lines. We will now more than ever be better equipped to help our current and future customers meet the challenges of today and prepare for the future.
Positive Change
The former SL Controls team is now part of the NNIT Group, headquartered in Denmark but with locations around the world including, of course, Ireland. NNIT delivers best-in-class digital solutions, specialising in serving the life sciences sector.
As part of the full integration of SL Controls with NNIT, there will be several visible changes. We have already communicated with customers to confirm the continuation of service delivery and to answer any questions. From a branding perspective, we will begin operating under the NNIT logo and brand and the SL Controls website and social media channels will be switched off.
You can visit the new Smart Factory section of the NNIT website to learn more about our enhanced service offering. I would also like to encourage you to follow us on NNIT’s social media channels, particularly LinkedIn.
Hard Work and Dedication
In closing, I want to thank the integration teams that have worked diligently over the last number of months to ensure the merger is smooth and successful. There is still work to do, but it has been fantastic to see the (now former) SL Controls teams and NNIT teams come together across a range of different disciplines to achieve a united goal.
I along with other leaders in NNIT have always believed there would be a strong cultural alignment between SL Controls and NNIT. To see that cultural alignment in action gives me even greater confidence in the future we are embarking on together.
I have always said during my time leading SL Controls that success is only possible because of the skills and dedication of our people. That will continue to be the case as we head into 2025 and beyond as NNIT.
Keith Moran
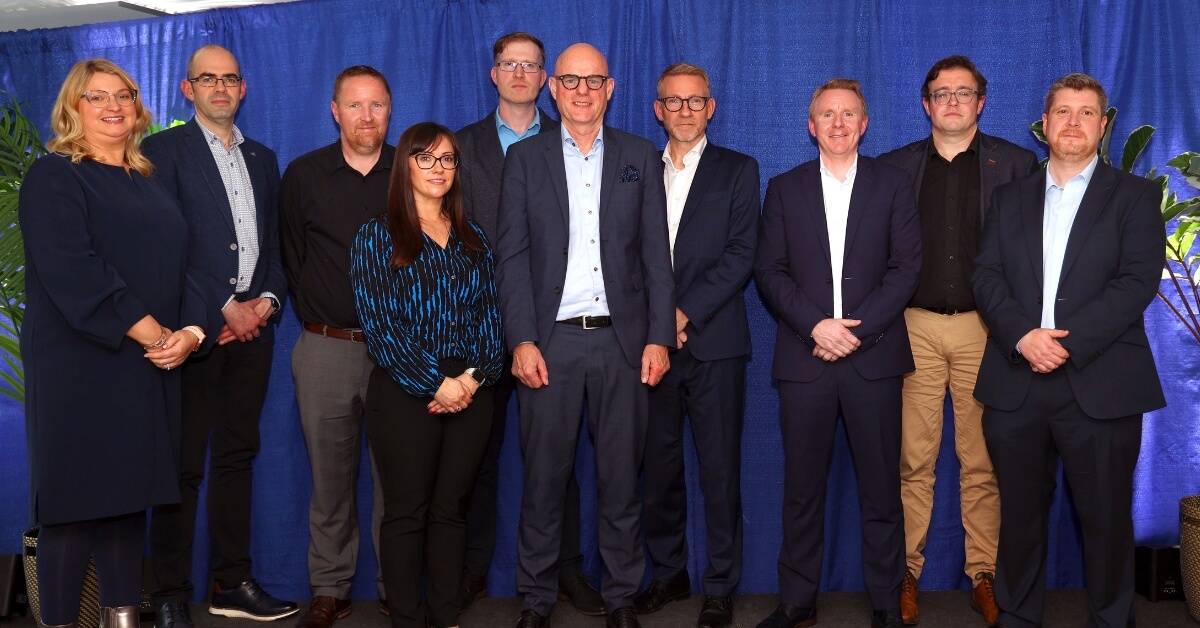
Press Release: SL Controls to merge with multinational NNIT
- SL Controls is set to fully integrate with NNIT by January 2025
- Ireland to become global ‘smart factory’ base for NNIT
SL Controls is to merge with multinational NNIT as Ireland takes on the role of the global ‘smart factory’ base for NNIT.
Former SL Controls CEO Keith Moran will head up NNIT’s Smart Factory and Supply Chain solutions, while the former senior leadership team from SL Controls will be assuming responsibility for NNIT’s Smart Factory operations.
All former staff and management from SL Controls in both Ireland (Sligo, Dublin, Limerick, and Galway) and the U.S. (Florida) will remain in place.
The Irish specialist technology integration firm was acquired by the NNIT Group – one of the world’s leading suppliers of business and IT solutions to life sciences — in 2021.
Publicly listed NNIT is specialised in life sciences internationally and the private and public sectors in Denmark. It has 1,700 employees in Europe, Asia, and the US.
In January 2025, SL Controls will merge into NNIT and fully integrate with the NNIT Group.
The former SL Controls operations will be part of NNIT’s Smart Factory solutions, with 150 employees in Ireland and across NNIT’s other locations worldwide.
The smart factory is part of the future of manufacturing. It integrates systems, equipment, and devices so they can generate data to improve production processes.
NNIT will be working with the life sciences sector internationally to modernise manufacturing processes based on smart factory principles and ensuring clients have constant access to accurate and reliable manufacturing data from every corner of their factories.
Headquartered in Copenhagen, Denmark, the NNIT Group also has locations in Germany, Switzerland, Poland, Czech Republic, UK, China, Philippines, Singapore, and the US. The company focuses on high complexity industries and advises on and builds sustainable digital solutions that work for patients, citizens, employees, end users and clients. Its expertise in digital transformation for the life sciences industry helps its clients across key parts of the life sciences value chain, turning fragmented and isolated manufacturing and supply chain processes into a well-integrated digital landscape where data flows freely from one end to the other, enabling data-driven decisions manufacturing.
Celebrating 30 years in business this year, NNIT consists of a group company NNIT A/S and subsidiaries – SL Controls, Excellis Health Solutions and SCALES Group.
Keith Moran, SL Controls, CEO, says:
“We are very excited about the international role we will be playing in the NNIT Group and how this change will further enhance our service offering to meet our current clients’ global requirements while also giving us access to larger-scale global projects across the European market.
“SL Controls will be NNIT by January 2025, and we will be fully integrated into the NNIT Group. This ongoing evolution of the company brings with it many benefits and opportunities for clients as we widen our network.
“It is an excellent progression for the company and for all the people working in it. We are delighted to be fully integrating with a company that shares our vision of excellence in service delivery in the life sciences industry.
“It also gives our team wider career options both in Ireland and across Europe and will give them access to work on major global projects. There is great cultural alignment between SL Controls and NNIT as we both focus on our people – success is only possible because of the skills and dedication of our team.”
Ricco Larsen, Senior Vice President, Region Europe, NNIT, says:
“We are thrilled to be joining forces with the SL Controls team, bringing deep expertise within the Smart Factory solutions area to our Manufacturing & Supply Chain domain.
Together, we will be even stronger with a second-to-none united offering portfolio to the life sciences market. This will bring many exciting opportunities for clients and employees alike, and we are very excited about our joint future.”
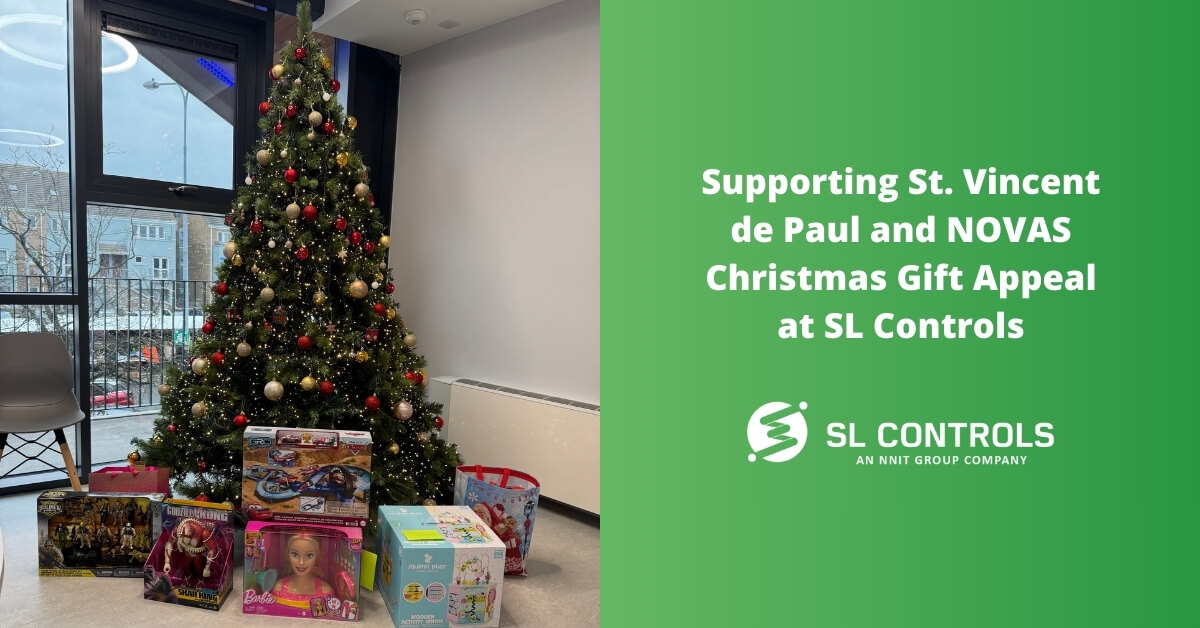
Supporting St. Vincent de Paul and NOVAS Christmas Gift Appeal
We are proud at SL Controls to support the St. Vincent de Paul Christmas gift appeal in Sligo again this year. A number of colleagues took part to ensure struggling families have presents this Christmas.
Norma Mulligan, People & Culture Executive at SL Controls said: “The work St. Vincent de Paul does is amazing at this time of year. It is heartbreaking to think of the families across Ireland struggling to put food on the table and keep their homes warm while also trying to ensure Christmas is magical for their children. It’s such a small gesture in the great scheme of things – buying and donating a toy to St. Vincent de Paul – but the impact of that gesture can be huge.
“We let the team know we would be participating in the gift appeal again this year and the response from employees was fantastic. We have now handed over the gifts to the St. Vincent de Paul branch in Sligo.
“Employees in our Limerick and Galway locations have supported the NOVAS Christmas Appeal this year and gave a digital gift so that toys could be bought for the children supported by NOVAS. Our thanks to everyone on the SL Controls team who got involved.”
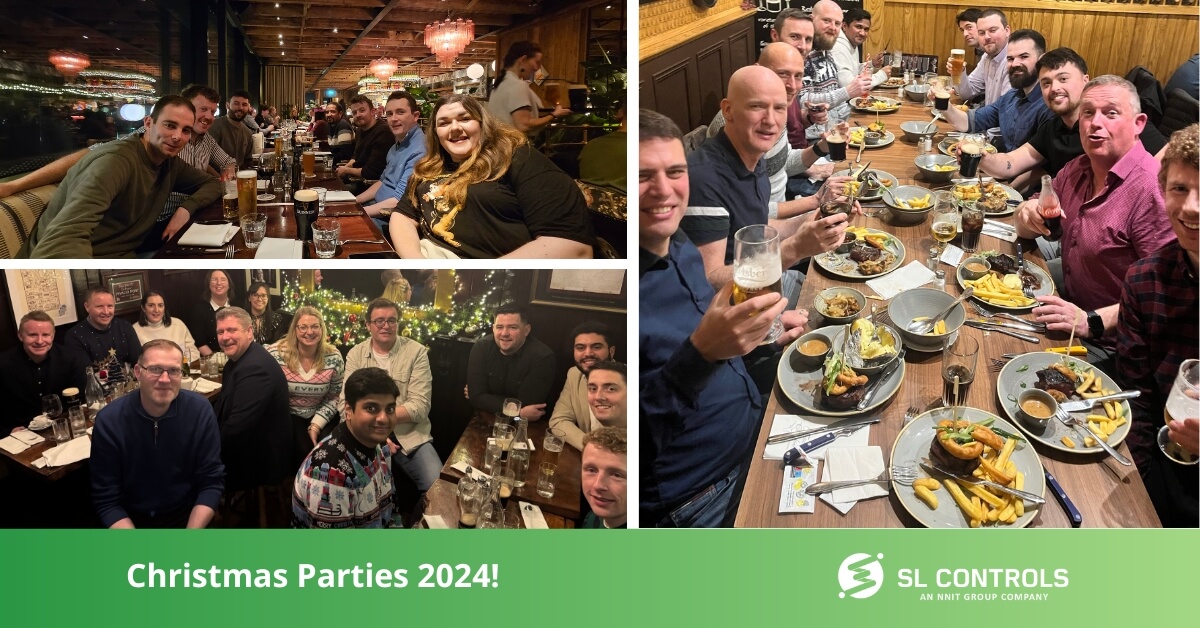
SL Controls Christmas Party Pictures 2024
SL Controls teams at our regional office locations came together on Friday for Christmas parties. As we have done in previous years, the venues chosen were close to our office locations to minimise travel, so there were three parties in total, in Sligo, Limerick, and Galway.
Norma Mulligan, People & Culture Executive at SL Controls said: “We have office locations around Ireland and in the US, but we are a remote team at SL Controls. While some employees do go into the office more than others, it is much more likely that staff will be working from home or from a client facility. This makes get-togethers like our annual Christmas parties so important.
“Christmas parties are a chance to relax with colleagues, many of whom you might not have talked to in person since our summer company outing. It is also always good to socialise with the people you work with in a non-work setting.
“We have an initiative at SL Controls of celebrating wins together, and there is no better way of doing that at this time of the year than at the Christmas party.”
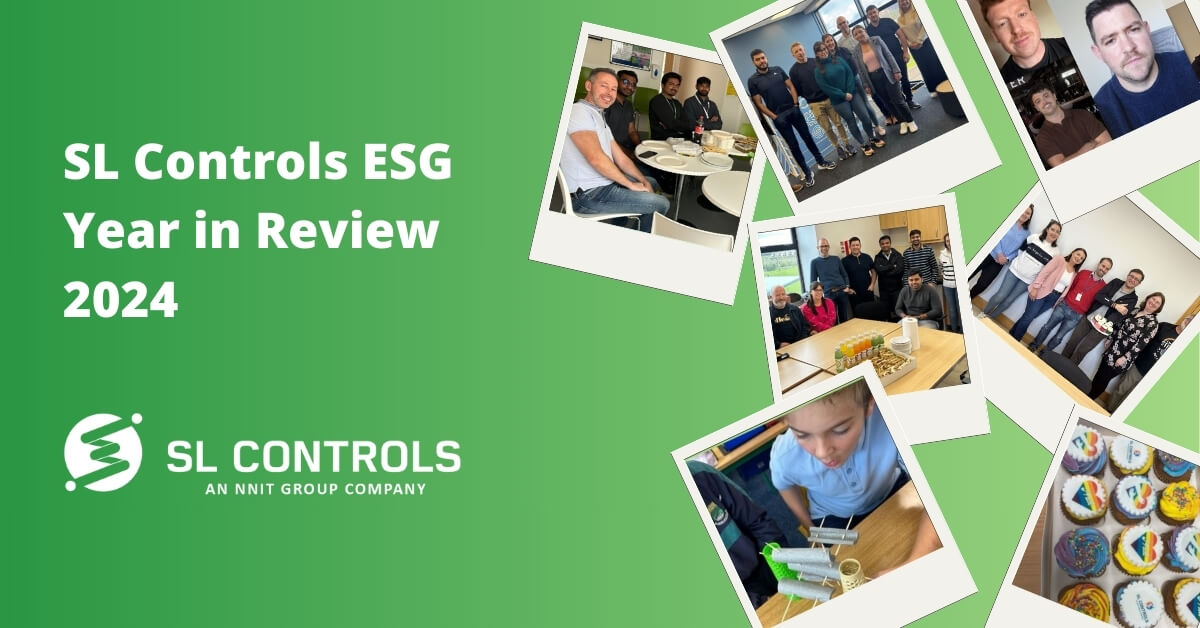
SL Controls ESG Year in Review 2024
2024 has been busy commercially and operationally for SL Controls, and it has also been busy for our ESG (environmental, social, and governance) leaders and facilitators. Throughout the year they organised a range of initiatives and activities focused on our five sustainable development goals:
- Good health and wellbeing
- Quality education
- Gender equality
- Decent work and economic growth
- Responsible consumption and production
Raising Funds for the Irish Cancer Society
At the start of the year, we asked employees to vote for the SL Controls’ charity of the year. The team selected the Irish Cancer Society. We have organised a range of fundraising initiatives throughout 2024, including staff participating in Movember recently.
Workplace Wellbeing
We marked Workplace Wellbeing Week in April with a series of initiatives, including providing a healthy lunch for staff who came into the office on our April anchor day.
Cultural Diversity
To celebrate World Day for Cultural Diversity in May, we asked the SL Controls team to share details about their country and culture. We created a video highlighting the responses which you can view here.
Pride Month
We celebrated Pride Month throughout the month of June, including during a staff anchor day when employees who typically work from home came into the office.
Fitness Month
June was Fitness Month at SL Controls, with participating employees splitting up into teams to compete in a summer activity challenge. The Le(g)s Misérables team walked, cycled, ran, and swam further than anyone else.
Diversity, Equity, and Inclusion
We marked National Diversity and Inclusion Day in July by launching unconscious bias training for all employees and reinforcing our commitment to making positive changes.
Women’s Group
Our Women’s Group continued to meet throughout the year with a number of virtual get-togethers. Our industry continues to be male-dominated, so the discussions enable our female employees to connect with each other, build relationships, and discuss a range of topics.
Book Club
We launched a book club in 2024 for employees. Get-togethers started virtually but we have also had in-person meetings to discuss the books we are reading. It has proven to be a popular initiative that we are looking forward to continuing in 2025.
Mental Wellbeing Champions
Our Mental Wellbeing Champions ran a number of initiatives throughout the year, including Lunch and Learn sessions about workplace mental health. They also promoted good mental health at work with a pizza lunch as part of World Mental Health Day in October.
Inspiring the Next Generation of Engineers
We continued our relationship with STEAM during 2024, with two 10-week programmes where SL Controls engineers went into primary schools to teach the children about the core principles of engineering. The schools were in County Tipperary and County Sligo in Ireland.
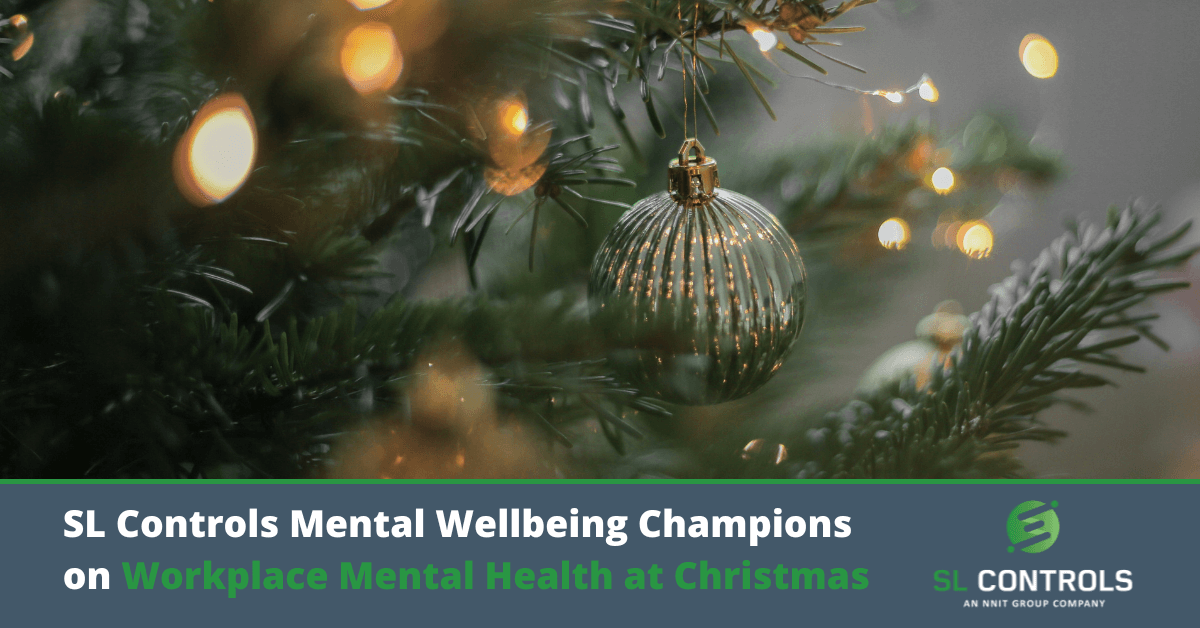
SL Controls Mental Wellbeing Champions on Workplace Mental Health at Christmas
Christmas is a unique time of the year in the workplace as much as in the shops and in our homes. While it is often a time of celebration and happiness, it can also be a time of stress and challenge. That’s why the Mental Wellbeing Champions at SL Controls are emphasizing the need to mind your mental health this Christmas.
Shauna Ryan, Director of People & Culture, said: “I think the first point is to acknowledge the importance of minding your mental health at Christmas. After a busy and successful year at SL Controls, we are coming up to a natural pause with the Christmas break, but that in itself can bring added pressures.
“Our personal lives can also become incredibly busy and, for many, stressful in the lead-up to Christmas. There’s so much to do and so much to remember while dealing with more traffic on the roads, longer queues at the checkouts, and weather that leaves a lot to be desired.
“And then there is the fact that some people struggle with the holiday period itself, despite the slower pace and less to do.
“In the life sciences sector where we operate, there are additional pressures too, as stopping production lines is not always possible for extended periods of time. This means work responsibilities can continue through the Christmas break.
“So, minding your mental health at Christmas is incredibly important.”
Norma Mulligan, People & Culture Executive, said: “There are three main messages we have for colleagues, particularly at this time of year. The first is to talk to someone if you are struggling – or for any reason, really. The second is to be mindful of your colleagues and check in with anyone you think might need a bit of support.
“The final message is to be aware of the support that is available through the mental wellbeing resources we provide at SL Controls and through services and resources like Healthy Ireland @ Work. After all, it’s important for us all to mind our mental health at Christmas.”

Growing a Mo for Men’s Health at SL Controls in Movember
November is a time for getting out the hats and gloves, taking down the Halloween decorations, and getting ready for the run-in to Christmas. For some of the men on the SL Controls team, it is also a time for growing a Mo – a moustache – as part of Movember.
Movember is a campaign that takes place every November around the world to raise awareness about men’s health. People get involved in lots of different ways but one of the most popular is growing a Mo.
SL Controls Senior Systems Engineer Conor Davey said: “For some, the moustache is a fantastic fashion statement but in November, it is also a way to highlight your support for men’s health and the importance of raising awareness around men’s health issues.
“It’s almost cliche now, but it’s probably still true that men are generally not as proactive about talking about their health, identifying symptoms, or getting potential symptoms checked out. The annual Movember campaign is helping change this.”
As it is International Men’s Day today, we are highlighting, celebrating, and supporting the SL Controls employees taking part in Movember this year. They include Conor as well as Liam McManus, Sam Costelloe, Frank Quinn, and Shane McLaughlin.
Conor said: “The SL Controls charity for 2024 is the Irish Cancer Society which ties in well with the Movember campaign. We have set up a Just Giving page if you want to support the guys growing a Mo and donate to the Irish Cancer Society.”
Link to the SL Controls Just Giving page: https://www.justgiving.com/page/slcontrolsirishcancersociety
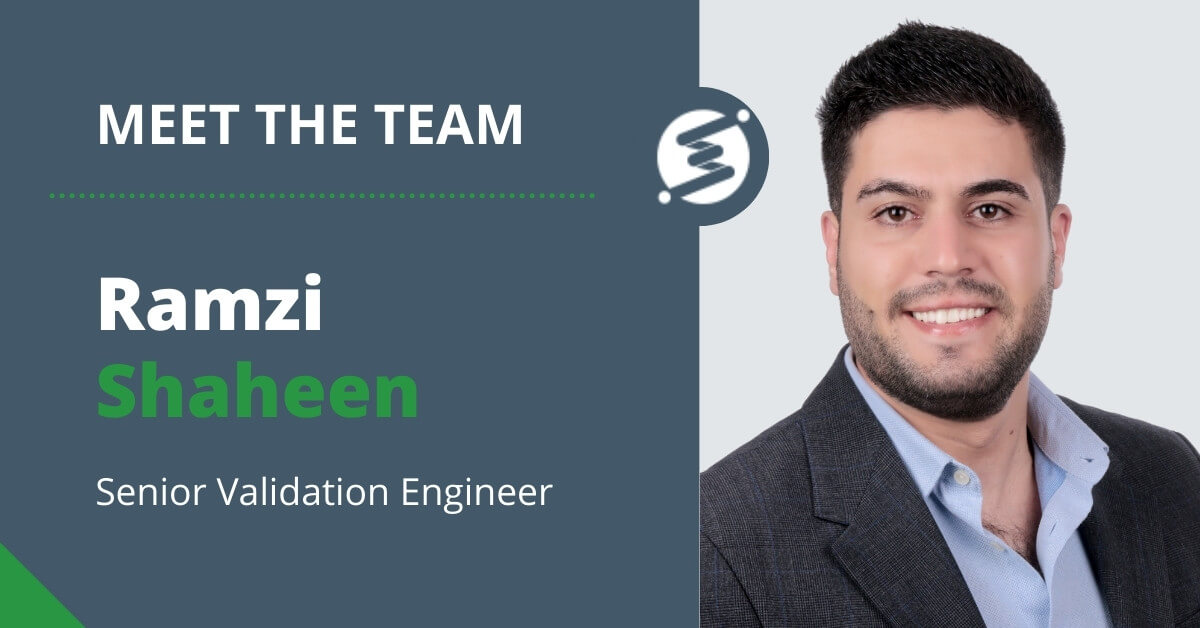
Meet the Team: Ramzi Shaheen
1. Describe your job as if you were explaining it to a five-year-old.
Imagine you have a really big, complicated system that helps people make important things, like medicine or toys. My job is to check and test the system and make sure it works and is safe, so it doesn’t break or make mistakes. I also help other people on my team understand how to take care of the system and make sure everything runs smoothly.
2. What types of projects are you working on at the moment?
I am currently working as a Senior Validation Engineer, while SL Controls is helping me transition into a project management role by gradually introducing management responsibilities within the projects I handle. One of my main projects involves the implementation of the PEMAC Assets platform, developed by PMI, for one of our major clients. This system is designed to optimise asset management, focusing on maintenance, calibration, and performance tracking.
While this project is technically an upgrade, we approach it as a new installation due to the significant changes involved. As part of my role, I lead the validation process, ensuring the system meets all regulatory and client standards.
In addition, I work closely with the project manager to assist in guiding the team through key phases, ensuring everything runs smoothly.
3. What is your proudest moment (work life or personal life)?
One of my proudest professional accomplishments in recent years was leading a significant process transformation for a global life sciences client of SL Controls. The client was facing challenges with project documentation and operational workflows. I spearheaded the implementation of a new business assessment framework to serve as the foundation for their operations.
4. What’s the best advice you could give to someone thinking of coming into this industry?
My advice to anyone considering a career in this industry is to look beyond the technical aspects and understand the larger impact of your work. While we may not be working directly in emergency rooms or on the front lines, we are supporting industries that save lives every day, whether through medical devices, pharmaceuticals, or advanced technologies that improve healthcare outcomes.
Also, invest in honing both your technical expertise and your communication skills. Stay curious, stay passionate, and always be willing to learn and adapt. This is an industry where innovation and continuous improvement define success.
5. Outside of work, what are you most passionate about?
Outside of work, I am deeply passionate about giving back to my community and helping others overcome challenges. Whether it’s through volunteering or offering mentorship, I find great fulfilment in supporting individuals who are facing difficulties, particularly in education. I also have a strong interest in initiatives that focus on humanitarian causes.
6. What’s the best thing about working for life sciences customers (pharma, MedTech, etc)?
In this field, precision, quality, and compliance are critical. The standards are high because the stakes are high, and that drives continuous improvement and innovation. I find great fulfillment in knowing that the systems we design, validate, and implement help healthcare professionals deliver critical care efficiently and safely.
7. What is the best thing about being on the SL Controls team?
One of the best things about being part of the SL Controls team is the strong sense of community and support. From the moment I joined, it felt less like a traditional company and more like being part of a close-knit family.
What truly stands out at SL Controls is the company’s commitment to its people. They’ve provided me with tools, guidance, and opportunities to advance my career while aligning with my passion for making a difference.
The company’s mission-driven ethos, combined with a forward-thinking approach to innovation, creates a space where I feel valued and motivated. I’m proud to be part of a team that not only focuses on delivering high-quality results but also genuinely cares about the impact we make on the world.